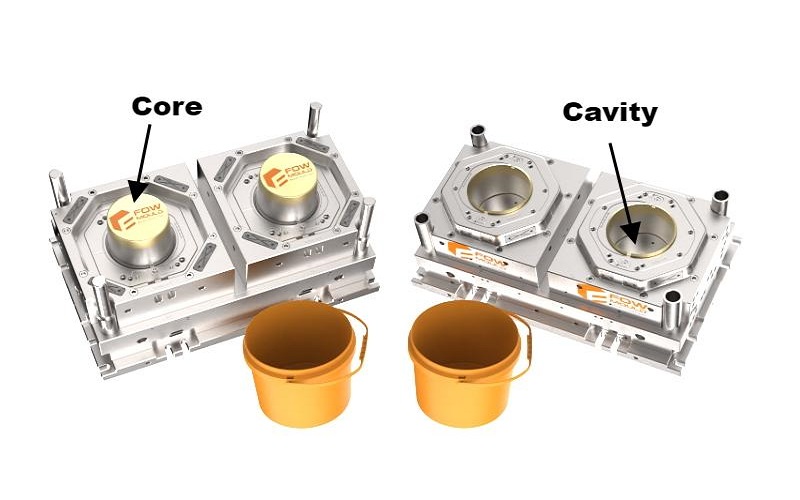
When it comes to the manufacturing business, you find that there are a lot of processes that take place daily. Familiarizing yourself with some of these processes is an excellent step. Especially as a business owner, doing this will ensure that you are well aware of what goes into the production of your products ranging from plastic molded chairs to auto plastic parts.
One of the processes you need to pay attention to is the injection molding process. A lot of people don’t understand what it is or what is involved. Here’s everything you should know about the process.
Source: www.creativemechanisms.com
The mold manufacturing process features the use of plastic material to achieve different shapes of products. It mainly involves using molten plastic material using heat. This molten material is then injected into a mold where it is shaped and cooled before being released.
The injection is mostly done using a cylinder to make the process easier. This process is ideal for large scale manufacturers who deal with plastic processing. It works great to produce complicated shapes and designs required for different uses.
Source: www.plasticstoday.com
The mold is a hollow metal object where molten material is introduced to ensure that it takes the right shape. It is used in the mold making technology. This device comes in handy in that you can create different shapes and mould designs if you need to. It allows for versatility, especially in the plastic industry.
Source: www.cadcrowd.com
The injection molding process includes a few steps that take place during manufacturing. These steps help achieve the result as desired with ease. These steps include:
The mold consists of two halves where the molten material is injected into. These two halves are designed to make the injection molding process easier. One of the two halves is designed to slide to allow for the release of the end product.
Before the injection of the molten material, this mold has to be clamped to ensure that it stays secure. This is done using a hydraulically powered unit. This allows it to move with ease when needed and stay secure during the whole process.
The time it takes to securely clamp the mold highly depends on the machine being used. Larger machines will need a longer time compared to smaller machines.
Source: youtube
Source: www.machinedesign.com
Given that the raw material in use is plastic, you find that most manufacturers prefer to work with plastic pellets. This is mainly because they are easier to use given that they’ll heat and melt faster.
The melting process is achieved when heat and pressure are applied simultaneously. Once this is done, the molten material is then introduced into a cylinder-shaped injecting tool. The cylinder is then used to introduce the molten material into the mold.
Given that the cylinder tool may have more of the molten material than can be introduced in the mold, it is designed to suck back the excess. This means that you won’t be wasting any material in this process.
This is the part of the process where the cylindrical injection tool has to stay attached to the mold for a while.
Doing this allows the mold to accumulate all the material it needs and release the rest back into the injection tool. This is an important part to ensure that you are using the right amount of molten material.
Source: www.powerjet-machinery.com
Source: www.pulsecooling.com
Once the molten plastic has been introduced into the mold, it begins the cooling process. This is an automatic process that happens once the material gets into contact with the mold surface.
As the plastic begins to cool, it will solidify and immediately take the shape of the mold you are using. During this process, you may expect some shrinkage which you can easily address by ensuring dwelling takes place.
The mold opens only after the injected material has fully cooled and solidified. This is determined by the cooling time on each material and machine you use. Once the material is fully cooled, the hydraulic clamp releases and allows the mold to open from one half.
Source: www.mhs-hotrunners.com
Source: www.mhs-hotrunners.com
After the mold has opened, the cooled material will be released. To do this, a lot of pressure is required. This is mainly because during the cooling process you find that the molten material takes the shape of the mold. This makes it harder for it to come out on its own.
To make the ejection process easier, you could consider using a release agent on the mold. This should be done before injecting the molten material into the mold. This will ensure that the ejection process is easier.
Source: techminy.com
When going through this process, you’ll need to use a quality molding machine that will get the job done. Most molding machines feature two units in them. They include:
This is the part of the machine that holds the mold together to ensure that the molten material is allowed to fully form. The mold comes in two halves attached to a base known as the platen.
One-half of the mold that is found on the front is attached to a fixed Platen that doesn’t move. This half is also designed to align with the nozzle of the cylindrical injection tool. This part of the mold is known as the mold cavity.
On the other hand, you find the rare part of the mold that is attached to a movable plate. This allows it to open and close as required during this process.
This mold is known as the mold core. The clamping tool features quality hydraulics that allows it to push the mold cor towards the mold cavity with ease.
Source: www.indiamart.com
Source: www.indiamart.com
As discussed earlier, manufacturers prefer to work with plastic pellets that have to be melted down to the molten state. This is achieved in the injection unit that also ensures the right amount of molten material is introduced into the mold.
This unit features the use of a hopper where the raw material is introduced. The hopper comes with an open bottom that then introduces the material into the barrel. Once there, the material is then heated and injected into the mold to facilitate the molding process.
Source: Pinterest
When working with the injection molding process, the most used material has to be virgin plastic pellets. These pellets provide an easier time when melting and introducing into a mold for cooling. However, there are times when reprocessed material can be used to achieve the same results. This applies to the use of finely ground sprues and runners.
These materials would otherwise not be used in the manufacturing process. With this, you have to be cautious to avoid interfering with the properties of your plastic.
Source: Pinterest
Like any other process, there have to be conditions that should be met to ensure that optimal results are achieved. With this in mind, the injection molding process also applies the same principles. From the temperature of the cylinder and mold to the speed of the injection. All these conditions will play a big part in the outcome of your end product. This is why professionals are required to operate this to determine the right combination that works best. Without this, you could end up with a product that doesn’t meet your expectations.
The injection molding process is quite easy to understand given that it doesn’t involve any complicated steps. It is a process that requires you to invest in the right machines and learn how to operate them for the best results.
Take your time to understand what it entails and how it can impact your business. This is an amazing process especially if you are in the plastic manufacturing industry. It will allow you to work with plastic and create amazing designs and shapes that would otherwise prove to be a difficult task. For more information, check out our website and you can find out some most-discussed injection moulding problems and solutions.
Please contact us using the form below or emailing (harry@fowmould.com)