Delrin is the brand name for an acetal homopolymer, first developed and brought to market by DuPont in 1956. It is highly regarded for its exceptional strength, wear resistance, and ease of machining. Delrin is found in a wide range of applications, from mechanical parts to everyday consumer products.
So, what exactly is Delrin? Why does it stand out among numerous materials? This article will delve into the characteristics of Delrin, its applications, and its significant role in the industry.
Basic Definition Of Delrin
Polyoxymethylene (POM), more commonly known as acetal or its branded name Delrin®, is a semi-crystalline engineering-grade thermoplastic widely used to create highly precise parts.
Its molecular structure consists of repeating oxymethylene units (-CH₂O-), which endow it with high crystallinity and outstanding physical characteristics.
As a high-performance thermoplastic material, Delrin offering low friction, high stiffness, and excellent mechanical properties.
The origin of Delrin can be traced back to the American company DuPont. In the 1950s, DuPont pioneered the development and commercialization of this material, introducing the homopolymer version of POM under the registered trademark “Delrin.”
Since then, Delrin has become synonymous with pom, although other brands of POM materials are available on the market today.
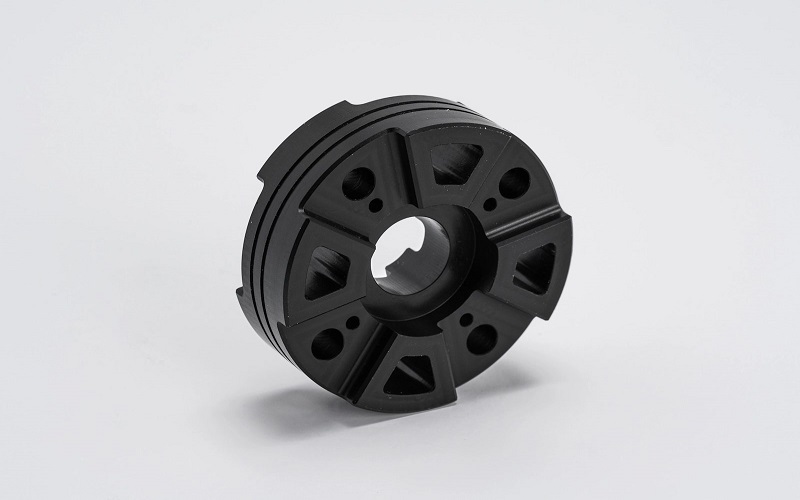
Delrin Material Properties
Whether it’s the smooth, glossy surface or performance under demanding conditions, Delrin’s plastic properties make it the preferred choice for precision parts and industrial applications.
The material properties include it having superior density, low moisture absorption, and it is chemically resistant to hydrocarbons, solvents, and neutral chemicals.
Physical Properties
High Crystallinity and Mechanical Strength: Delrin boasts a crystallinity of up to 70%,granting it excellent mechanical performance. Its tensile strength can reach up to 70 MPa, comparable to some metals, and it possesses outstanding rigidity and fatigue resistance, making it suitable for high-load components like gears and bearings.
Surface Characteristics:Delrin has a smooth and glossy surface, typically appearing in a pale yellow or white color. This feature not only enhances its aesthetic quality but also improves tensile strength and impact resistance, making it excel in applications where appearance and function are equally important.
Thermal Properties :Delrin exhibits impressive thermal resistance, including a high resistance to instantaneous temperature spikes and a wide operating temperature range of -40°C to 120°C, making it suitable for diverse environments.
Low Water Friction and Wear Resistance:Delrin exhibits an extremely low coefficient of friction and excellent self-lubricating properties, maintaining long-term performance in sliding parts without additional lubrication. Specific formulations (such as Delrin 500TL NC010, containing PTFE) further enhance its wear resistance, making it suitable for high-friction environments.
Low Moisture Absorption and Dimensional Stability
Delrin’s moisture absorption rate is only 0.2%-0.5%, allowing it to maintain high precision and shape stability under varying temperature and humidity conditions. Its low thermal expansion coefficient (approximately 10⁻⁵/°C) ensures dimensional reliability amidst temperature fluctuations.
Chemical Properties
Chemical resistance: Delrin exhibits good chemical resistance to oils and peroxides but is sensitive to strong acids and oxidants. After stabilization treatment, it can remain stable at 230°C.
Lubricity: Delrin 500TL NC010, which contains polytetrafluoroethylene (PTFE) lubricating components, offers low friction coefficient and excellent lubrication properties, making it suitable for high-friction and high-wear applications.
Thermal Oxidative Aging and Stability: Untreated Delrin may undergo thermal oxidative aging when exposed to high temperatures or prolonged oxygen exposure, leading to performance degradation. By adding antioxidants or heat stabilizers, its chemical stability can be significantly enhanced, maintaining reliable performance below 230°C.
Decomposition Characteristics: At extremely high temperatures, Delrin may decompose and release formaldehyde gas. This chemical property limits its applications in ultra-high temperature environments. Therefore, choosing the appropriate formulation and usage conditions is crucial.
Delrin Properties Table | |
---|---|
Properties | Value |
Density(g/cm³) | 1.41 |
Melting Point(°C) | 175 |
Tensile Strength(MPa) | 70 |
Elongation at Break(%) | 25–40 |
Glass Transition Temperature(°C) | -60 |
Shrinkage Rate(%) | 1.8–2.2 |
Coefficient of Friction | 0.25 |
Advantage Of Delrin Material
Delrin, as a high-performance engineering thermoplastic, stands out among numerous materials due to its unique combination of properties, offering significant advantages for industrial and consumer applications.
Below are the primary benefits of Delrin plastic:
Superior Mechanical Properties
Delrin boasts high tensile strength (approximately 70 MPa), exceptional rigidity, and excellent fatigue resistance, with mechanical properties approaching those of certain metals.
This enables it to replace traditional metal components in the production of gear wheels, bearings, springs, and other parts requiring high strength and stiffness.
Excellent Dimensional Stability
Thanks to its high crystallinity and low water absorption, Delrin maintains high precision and shape stability under varying temperature and humidity conditions.
Its good dimensional stability makes it a preferred material in precision manufacturing, such as for instrument components and connectors.
High Wear Resistance
Delrin’s low friction coefficient and superior wear resistance make it excel in sliding or frictional applications.
It delivers long-term performance without the need for additional lubrication, an advantage that is particularly pronounced in formulations containing polytetrafluoroethylene (PTFE) lubricants (e.g., Delrin 500TL), making it ideal for high-wear scenarios.
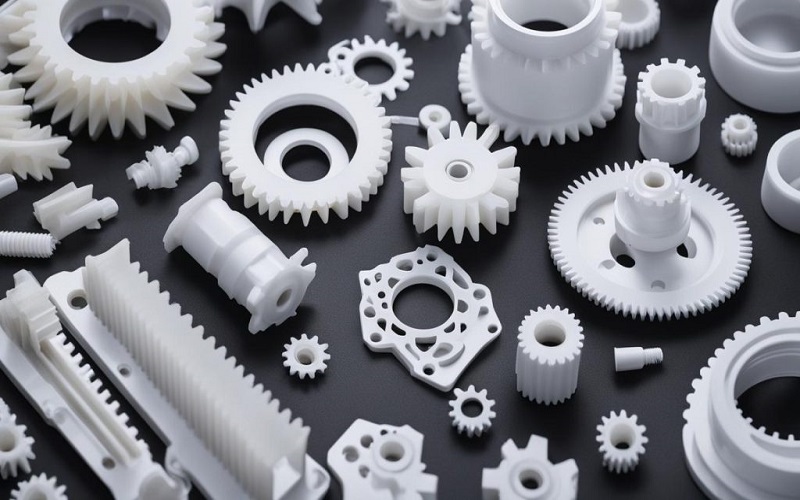
Disadvantages Of Delrin Material
The drawbacks of Delrin primarily focus on its chemical resistance, thermal performance, and environmental adaptability, which limit its applications under extreme conditions.
Limited Heat Resistance
The long-term usage temperature of Delrin is typically between 80°C and 100°C. Although it can temporarily withstand up to 230°C after stabilization treatment, prolonged exposure to high temperatures can lead to performance degradation and even decomposition, releasing formaldehyde gas. This makes it unsuitable for continuous high-temperature applications.
Poor Flame Retardancy
Delrin’s flame retardancy is relatively weak, with a UL94 flammability rating of only HB (slow burning in horizontal testing). It is prone to burning and lacks self-extinguishing properties in environments with high fire risk. Therefore, other materials should be considered for applications requiring high fire resistance.
Tendency for Thermal Oxidative Aging
Under conditions where high temperatures and oxygen coexist, Delrin is prone to thermal oxidative aging, leading to brittleness or performance degradation. Although adding antioxidants can mitigate this issue, additional formulation optimization is needed to extend its service life.
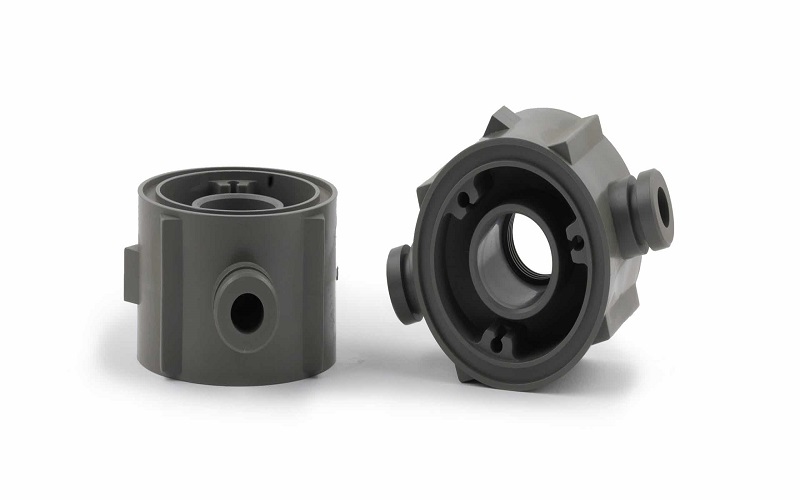
Manufacturing Process Of Delrin Parts
As a manufacturing materials, Delrin is extensively utilized in precision engineering due to its mechanical properties and ease of processing.
The creation of delrin parts involves several established manufacturing processes, each customized to meet the specific needs of the final product.
Below is an overview of the primary methods and key considerations in the production of Delrin components.
Injection Molding
Delrin Injection molding is the most common method for producing delrin parts, especially for high-volume production of complex shapes.
This method allows for high precision, tight tolerances, and the ability to produce intricate geometries like gears, clips, and housings. Delrin’s low viscosity when molten ensures good flowability, making it ideal for detailed designs.
Due to Delrin’s high crystallinity (up to 70%), it exhibits a shrinkage rate of 1.8%–2.2%. Mold design must account for this to avoid dimensional inaccuracies.
Additionally, maintaining proper mold temperature (typically 80°C–100°C) and avoiding overheating (above 230°C) are critical to prevent decomposition, which can release formaldehyde gas.
CNC Machining
CNC machining is often employed for low volume production or to create high performance engineering components from extruded Delrin stock (e.g., rods or sheets).
Using computer-controlled tools, Delrin is cut, drilled, or milled into the desired shape. Common machined parts include bearings, valve components.
This process is ideal for producing custom parts with tight tolerances and complex geometries, ensuring excellent dimensional stability and surface finish.
Extrusion
Extrusion is used to create continuous shapes such as rods, sheets, or tubes, which can later be machined into final parts.
Extruded Delrin stock shapes are ideal for secondary machining processes, offering flexibility for custom parts like bushings or spacers.
Uniform cooling is essential to prevent internal stresses or warping due to Delrin’s high crystallinity. The extrusion process also requires careful temperature control to avoid thermal degradation.
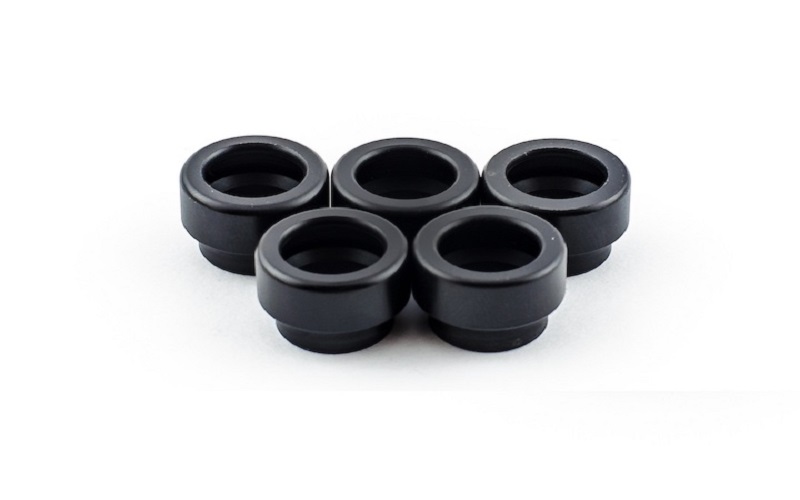
Applications Of Delrin Plastic
Delrin’s applications span across industries such as industrial manufacturing, consumer goods, automotive, medical, and electronics, with its success attributed to its excellent balance of strength, wear resistance, and processability.
Industrial Applications
Delrin is widely used in the industrial sector to manufacture parts requiring high precision and durability. Its low abrasion resistance and wear-resistant properties make it an ideal choice for gears, bearings, door systems, and pump components.
Consumer Goods
Delrin is favored for its smooth surface, durability, and ease of processing. Everyday items such as zippers, toys, and commonly used clips and fasteners can be made from Delrin material.
Automotive Industry
In automotive manufacturing, Delrin’s lightweight nature and chemical resistance make it a preferred alternative to metal. It is commonly used in fuel system components, safety restraint devices, window regulator gears, and door lock mechanisms.
Additionally, Delrin’s low friction and wear resistance reduce component wear, thereby enhancing service life.
Electrical Insulation
Delrin’s insulating properties and dimensional stability make it an ideal material for connectors, switches, and insulating components in the electronics industry, maintaining performance across varying temperature and humidity conditions.
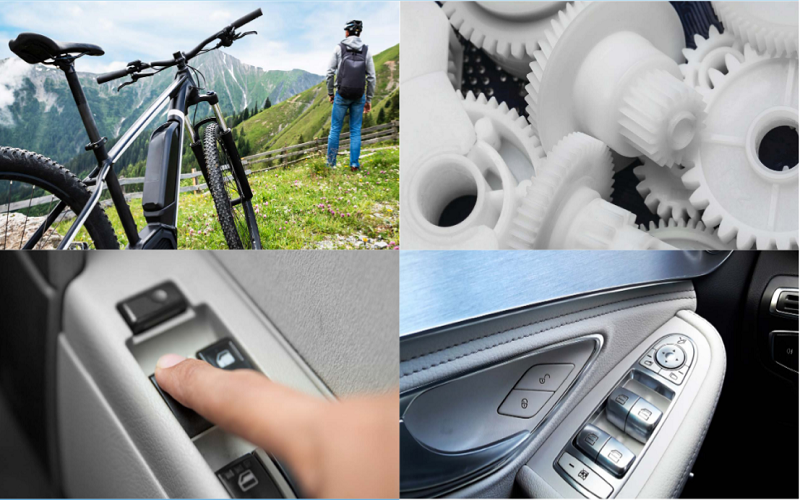
Delrin vs Other Plastics
We will conduct a comparative analysis of Delrin with two other materials: Nylon and ABS:
Delrin vs Nylon
Delrin and Nylon are both commonly used engineering plastics, but they have significant differences in moisture absorption and wear resistance.
Delrin has an extremely low moisture absorption rate (0.2%-0.5%), allowing it to maintain excellent dimensional stability in wet environments.
In contrast, Nylon has a higher moisture absorption rate (for example, Nylon 6 can absorb 1.5%-3%), which can lead to dimensional swelling and performance degradation after moisture absorption, potentially becoming an issue in high-precision applications.
Delrin has a lower coefficient of friction and higher wear resistance, particularly excelling in self-lubricating properties compared to Nylon. While Nylon also has some wear resistance, its higher friction coefficient makes it more prone to wear under high loads or unlubricated conditions.
Therefore, Delrin is more suitable for sliding parts such as gears and bearings, while Nylon is more commonly used in scenarios requiring a certain level of toughness and impact resistance, such as ropes or gaskets.
Additionally, Delrin has higher rigidity, whereas Nylon offers greater flexibility and impact resistance, making each material suitable for different applications. For more information, please click to read “Delrin vs Nylon.”
Delrin vs ABS
The notable differences between Delrin and ABS primarily lie in wear resistance and dimensional stability. ABS has lower tensile strength (around 40-50 MPa) and less rigidity compared to Delrin, but it offers greater toughness and impact resistance, particularly performing better at low temperatures.
Delrin is renowned for its low friction coefficient and excellent wear resistance, making it suitable for sliding components such as gears and bearings. ABS, on the other hand, has poorer wear resistance and a higher friction coefficient, generally making it unsuitable for high-friction applications.
Delrin has an extremely low moisture absorption rate (0.2%-0.5%), allowing it to maintain high precision and shape stability under varying temperature and humidity conditions. ABS has a slightly higher moisture absorption rate (around 0.3%-1.5%), which may cause slight expansion in humid environments, affecting dimensional accuracy.
Overall, Delrin excels in strength, wear resistance, and dimensional stability, making it ideal for engineering applications requiring high precision and durability.
In contrast, ABS is better suited for consumer goods and decorative purposes due to its impact resistance, processing flexibility, and cost advantages. For more information, please click to read “Delrin vs ABS.”
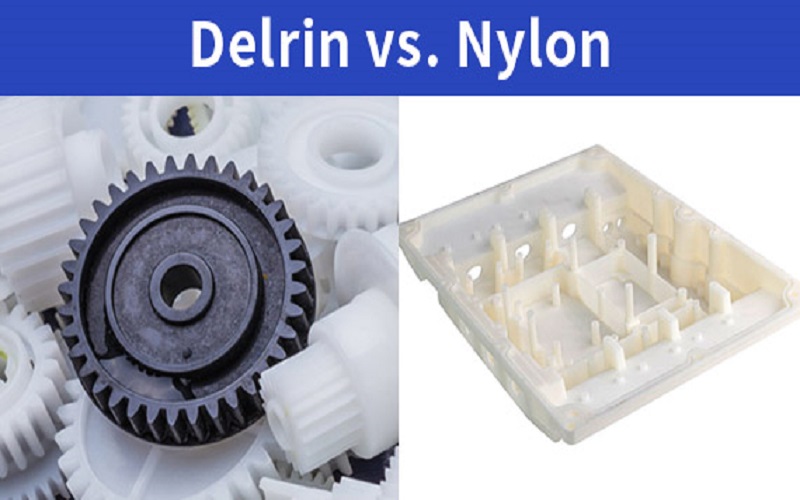
Conclusion
For injection molding manufacturers, Delrin material is undoubtedly a versatile manufacturing material. Its high performance and excellent mechanical properties make it stand out in numerous industrial applications.
Delrin’s low friction coefficient and high wear resistance make it a key player in engineering components that require precision and durability. Additionally, Delrin’s exceptional dimensional stability and low moisture absorption ensure its reliability under various environmental conditions.
Despite some limitations in high-temperature and chemical exposure, Delrin is highly regarded for its extensive use in the automotive, electronics, and consumer goods sectors.
If you are looking to start an injection molding project with Delrin material, please contact FOWMOULD! With 40 years of rich experience as a professional injection molding manufacturer, we have the capability to provide you with customized Delrin injection molding solutions at the most cost-effective prices.