In recent years, the application of gas and water-assisted injection molding techniques has shown significant effectiveness in solving hollow structures and injection stresses in plastic products.
In this article, we will explore in-depth the molding principles of water-assisted injection molding, its process characteristics, and its applications in various fields.
What Is Water Assisted Injection Molding?
Water-assisted injection molding is a new molding method for producing hollow or partially hollow plastic products.
This injection molding process utilizes a pressure-raising device to generate high-pressure water, which is injected into the mold cavity already partially pre-filled with molten material.
Using the pressure of the water to push the melt forward and fill the cavity.
The front edge of the water acts like a displacement piston, exerting force on the molten core of the part.
From the front edge of the water to the transition section of the melt, a very thin layer of plastic film solidifies.
It acts like a high-viscosity core, further pushing the polymer melt to form a hollow body.
Finally, the water is expelled from the part using gravity or compressed air, and after cooling and demolding, the finished product is obtained.
Especially for thick-walled workpieces, the cooling time can be significantly reduced with water assistance compared to gas assistance.
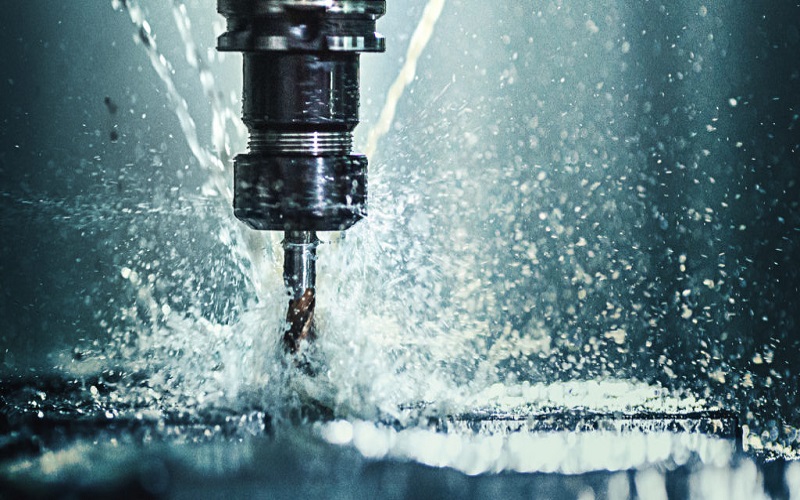
Water-Assisted Injection Molding Process
Water-assisted injection molding primarily utilizes two processes: the bullet method and the gas-assisted plus water-assisted composite process.
Each of these processes has distinct characteristics. The bullet method produces parts with thinner wall thicknesses and smaller internal diameter deviations.
In contrast, the gas-assisted plus water-assisted composite process results in parts with smoother inner walls.
Additionally, the complete expulsion of water from the channels using gas in this composite process ensures complete drying of the parts.
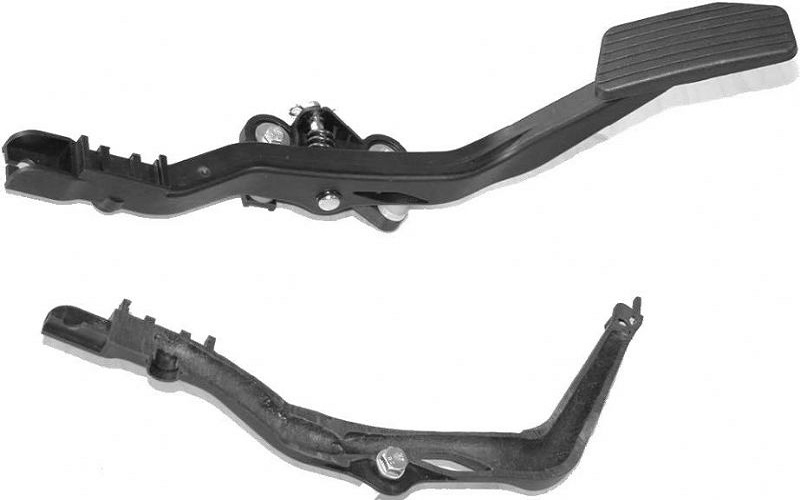
Materials for Water Assisted Molding
Several material suppliers are developing materials suitable for water-assisted molding processes.
Significant progress has been made with polyamides (nylons) replacing the fluid transmission lines and metal parts used in the engine compartments of automobiles.
These special materials have been modified to achieve slower crystallization rates, avoiding premature solidification and perforation (or fuzzing).
The new pa materials are either PA6 or PA66 types and often contain glass fibers or glass fiber-mineral fillers.
Materials based on PA66 exhibit better corrosion resistance to ethylene glycol coolants.
Some injection molding companies are using polypropylene material in water-assisted molding processes.
While others are evaluating the potential applications of unfilled acrylonitrile-butadiene-styrene (ABS), aliphatic polyketone, and polybutylene terephthalate (PBT) base materials.
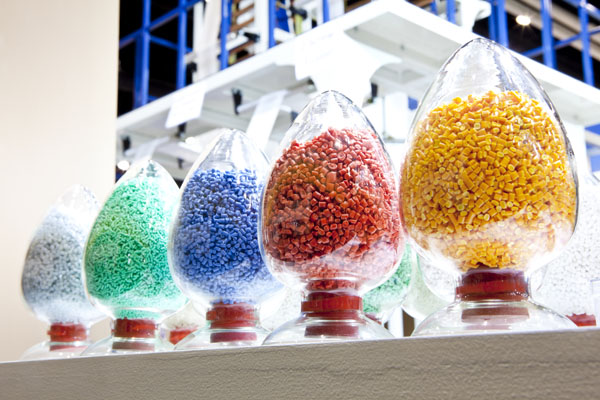
Advantages of Water Assist Injection Moulding
Due to water’s incompressibility, the front end of the water forms a solid interface, squeezing the inner wall of the product into a cavity.
The front end of the water also serves to rapidly cool the product.
Therefore, water-assisted molding has several advantages over gas-assisted molding:
(1) Shortens the product’s molding cycle
(2) Uniform wall thickness
(3) Reduced Residual Stress
(4) Improved inner wall smoothness
(5) Lower price of water as a medium
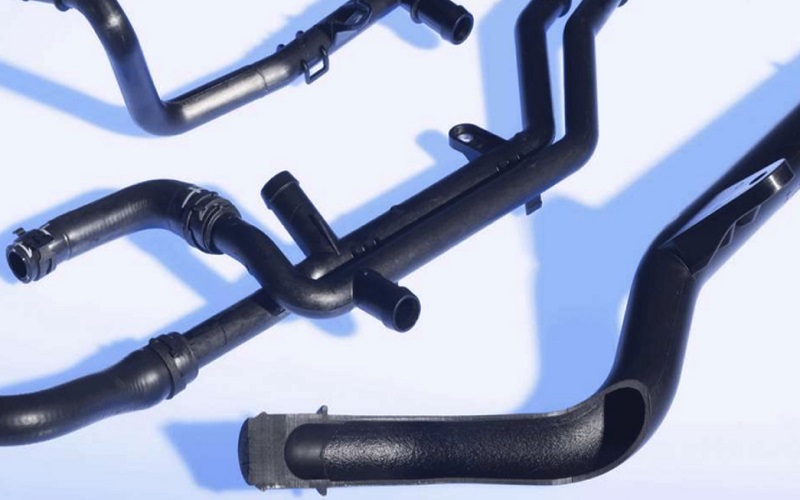
Disadvantages of Water-assisted Injection Molding
Although water-assisted molding has many advantages that gas-assisted molding cannot match, it also has some shortcomings:
(1) Increased drainage process
(2) Water leakage problem
(3) Corrosion of mold materials by water
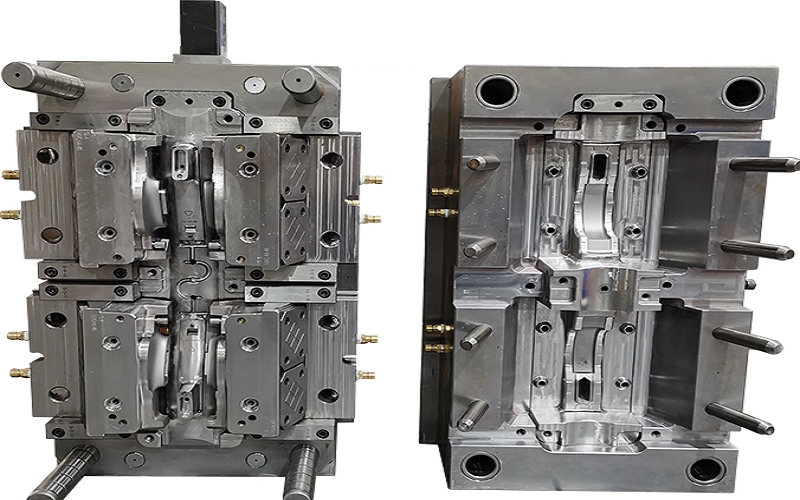
Applications of Water Assist Injection Molding
The demand for Water Assisted Injection Molding technology mainly comes from suppliers of hollow automotive products.
This technology is often applied to cooling systems, producing hard, fiber-reinforced nylon pipes.
It allows for larger hollow tube sections, saving space in the front engine compartment and offering greater design flexibility.
Currently, water-assisted injection molding pipelines have been used in vehicle models such as the C095.
Compared to metal pipes, this technology achieves a 42% weight reduction per pipe, contributing to the overall weight reduction of the vehicle.
For lightweight and durable furniture components, water-assisted molding enables larger cross-sectional spaces and thinner walls, saving materials and shortening the molding cycle.
Therefore, it is commonly used to produce various handles, armrests, furniture legs, and door knobs.
Additionally, when producing special products with water-assisted injection molding, there is no need for drainage – colored water is injected into the core of the melt and retained inside.
This results in attractive products with a clear plastic outer layer and a colored water core.
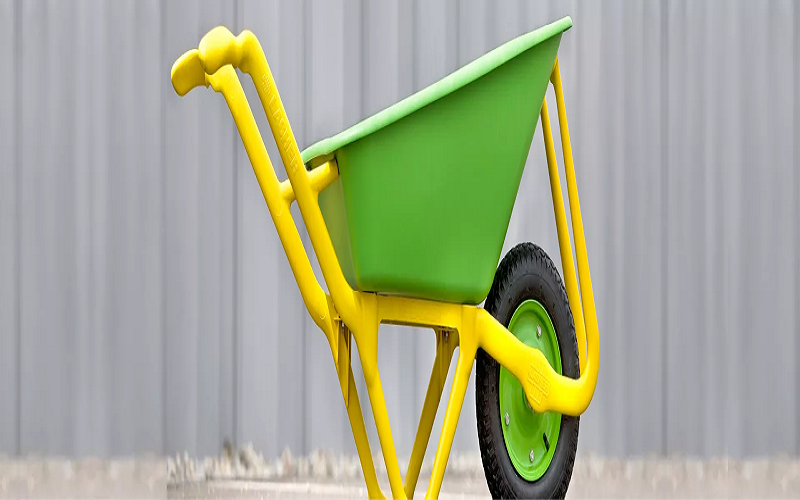
Comparison Of Water Assist And Gas Assist Molding
Water Assisted Injection Molding is an auxiliary injection molding technology that has been developed based on Gas-Assisted Injection Molding .
Compared to gas assist injection molding using nitrogen, the primary advantage of water-assisted molding lies in water’s rapid cooling efficiency.
Water has a thermal conductivity 40 times higher than nitrogen, and its heat capacity is four times greater than that of gases.
For thick-walled components, cooling times can be reduced by 30-70% with water assistance compared to gas assistance.
Moreover, when producing large-diameter conduits, water-assisted injection molding can result in thinner wall thicknesses, more uniform cross-sections, and smoother internal surfaces.
Gas-assisted injection molding, as a very mature technology, has been used in the plastic processing industry for many years.
One of its most important applications is the production of thick-walled plastic parts, such as handles and similar products.
Plate-shaped parts or other plastics with locally thickened areas also constitute an important application area for gas-assisted molding.
In contrast, water-assisted injection molding is a relatively new technology, having only been around for about six years since the initial results of the technology were published by the Institute of Plastics Processing (IKV) in Germany.
However, this technology has been rapidly developing.
In practical production, plastic parts with functional spaces or channels are increasingly using water-assisted injection molding technology.
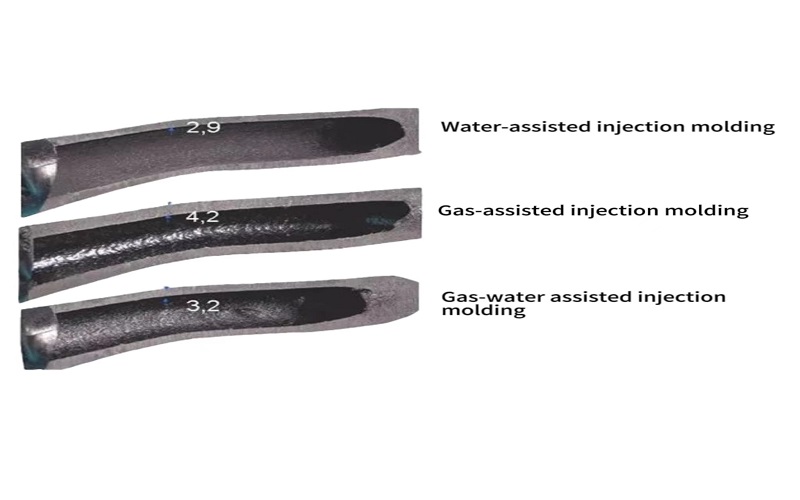
Conclusion
Water Assisted Injection Molding, as a novel injection molding technology, has clear advantages over other injection molding techniques.
When compared with gas-assisted injection molding, it becomes evident that water-assisted injection molding has a broader potential for future applications.
For more information about injection molding, please contact FOWMOULD.
We will become your most trustworthy injection molding partner!