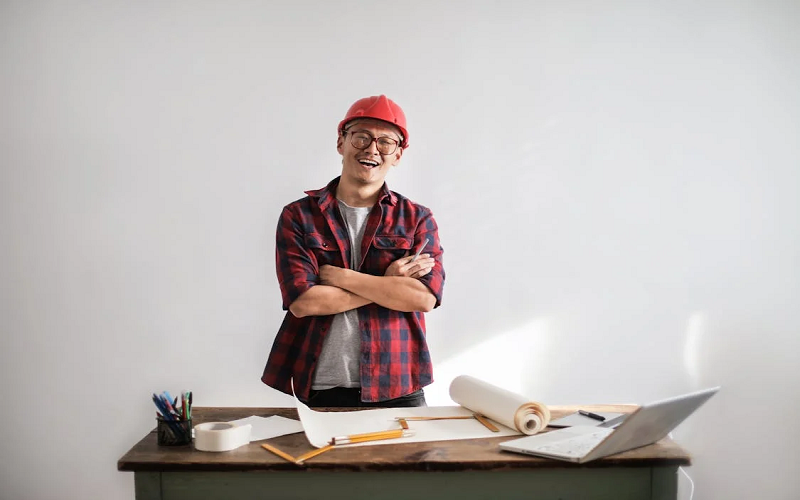
Share :
Share :
Injection molding process is prone to distortions in the final product, which goes by the name of warpage. A significant molding defect, warpage in injection molding can be of various types. It can impact the entire look of the product and can also compromise the integrity of the product, rendering it completely useless. Warpage leads to a wastage of time and resources.
Warpage is a defect that occurs for a variety of reasons. Suppose the manufacturer has some knowledge of material science, plastic flow behavior, and the tool settings of the injection molding machine. In that case, warpage can be reduced and even prevented during the mold making process.
Warpage in plastic injection molding is a common defect encountered by manufacturers. The deformation, called the warped part, is liable to further damage by mechanical forces and experiences unprecedented shrinkage during the molding process.
The intended shape is very twisted or distorted during the cooling process, which is seen when the mold is ejected. The distortion can be the bending, twisting, folding, or bowing of the mold. Warpage can also be seen during ejection, and any alteration which is required post ejection can prove to be very expensive for any manufacturer.
Warpage is a defect that results because of certain set conditions that occur during the injection molding process. The most common causes that lead to warpage include:
Checking the temperature variation across the mold, looking at the mold structure and mould design, and knowing the flow rate of the plastic you have chosen are just some of the tips you need to keep in mind to prevent warping. Other solutions depend on specific problems.
The mold temperature standards need to be met while manufacturing to prevent warpage. If the mold temperature is not high enough, the plastic in the mold will solidify before it is meant to, which can cause unwanted distortions. Depending on the mold temperature, the solidification will happen at different rates, which will cause warpage. This can be prevented by following the instructions of the resin supplier. Adjust the mold temperature, and the process should give favorable results.
Along with low mold temperatures, uneven mold temperatures can also cause warpage in molds. You can check to see if there is more than a 10-degree temperature difference across different parts of the mold. If you find a drastic temperature difference, make it level, or else warping, and uneven shrinkage will occur in the mold.
While doing injection molding, the flow rate of the material needs to be proper for it to be set appropriately. While dealing with different plastics, manufacturers are the best advisors on the flow rates of different materials. Depending on the type of molding you are doing, the material selection should be made accordingly.
For overmolding, you would require materials that are more strong and durable. Even for thin-walled products, stiff materials that give a rigid appearance upon setting are the best. But if you choose a stronger material for molding, there is a risk of the material setting unevenly. The setting can also occur before the mold is fully packed, which can cause shrinkage and eventually lead to warpage. Contact the material supplier to better understand the flow rate of the plastic before beginning the molding process.
If the gate size of the mold is wrong, the material will not flow properly into the mold, which can cause warping during the molding process. The mold filling rate will not be adequate if the gate size is too small, and it can cause pressure loss from one point to another in the mold. This stress is what will cause warpage after the molding is done.
Gate location is closely related to the gate size problem. Both issues cause a pressure loss which can lead to warpage. If the gate location is at a part that is thinner and the material has to pass through the narrow part to get to the thicker end of the mold, the pressure created can cause warping.
This issue with gate size can be solved by altering the shape of the mold based on the material you are using for the insert molding. The ideal way to deal with this issue is to increase the gate size so that the warpage does not occur at all. For the gate location, the pressure drop is a significant factor leading to distortion; the mold will need to be redesigned from scratch so that these conditions are removed. Additional gates can also be added to the old mold to reduce the pressure and make the filling more convenient.
Warpage occurs when there is a visible distortion of a part of the mold which does not adhere to the boundary set by the injection mold cavity. Avoiding warpage does not require a lot of effort, just a little vigilance from the manufacturers. Preventing warpage will also require altering the injection molding tools and the product design used in the molding machines. The issues with the molding process can be checked and rechecked to isolate the problem, and then steps can be taken to fix it. In case warpage still occurs after all precautionary measures, contacting the engineer and isolating the cause is the best bet.
Please contact us using the form below or emailing (harry@fowmould.com)