It is very hard to maintain the uniformity of a product in every batch, and almost every industry produces some waste. However, the question is how effectively one optimizes that wastage. In the plastic injection molding industry, those supplies not up to the mark are marked undercut in maintaining plastic designs.
The undercut injection molding helps ensure uniformity in all supplies and offers suppliers the best with minimum wastage. Therefore in undercut molding, inappropriate designs are discarded by an undercut in the plastic design.
However, before opting for this method it is important to understand the concept of undercut injection molding and stress on the notch why it is important to undercut in plastic design. So, let’s check the know-how of undercut molding and types of undercut in injection molding.
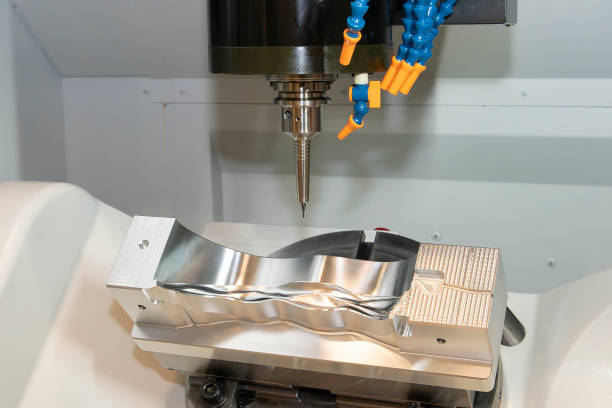
1. What Is An Undercut In Injection Molding
Undercuts are obtained when the flow of heat is more than needed and the products get distracted from their shape. Undercuts in injection molding help the commodity from getting discarded from the batch.
By undercut plastic design, the manufacturers can easily attain the similarity between two not identical articles. Extracting the excess plastic from carving and finishing it to detail, helps to make all articles look the same.
For shredding the portion, it is important to analyze the shape and where the undercut is needed in plastic design. Furthermore, if required, changes have to be done in the mold too. The continuous pouring of molten thermoplastic disturbs the shape of injection molds. Thus, the injection molding units need to undercut molds too.
Undercut in plastic design can be done in two types: external and internal undercut injection molding. In the internal method where internal undercuts are inside the mold and external cuts are outside of the mold, both of them can strike altogether too. These undercutting methods help to stave off the chances of mold or supplies getting rejected directly from the machines.
2. Why Undercuts Are Used In Injection Molding
Undercutting is important for removing excess material from the product and allows the correct geometric shape to acquire from the injection molding without forfeiting the significant parts of the molding. Undercut enables connection from one component to another one with undercuts. They also enhance the design of the product formed. It also plays a major role in the over-molding and insert-molding processes.
Undercut plastic design helps to expand quality that prevents the ejection of material. Moreover, the best part of undercut in injection molding of thermoplastic is it allows the injection molding to recycle the waste and optimize the utilization of plastic materials. There are some disadvantages too that should be taken into account before opting for an undercut plastic design.
Some of the important disadvantages of Undercut injection molding is it makes the demolding of the parts complicated, and thus the process of undercut in the injection molding becomes relatively costly for both the parties involved.
Moreover adding the extra cost of undercut to the project also add more days for delivery by which lead time is extended.
Average injection molding takes 4-7 days to be done but undercuts injection molding might lead to the extension of the initial time period. This eventually disturbs the whole batch and other projects as well. Hence, undercut injection molding may seem easy but it too comes with some cons.
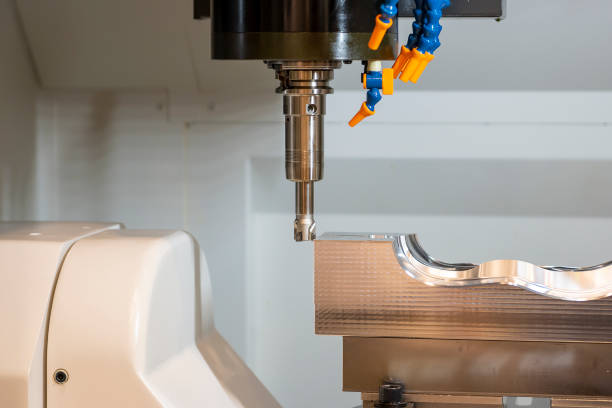
3. How To Avoid Undercut In Injection Molding
It is so true to say injection molding is an essential process for getting things done. However, the addition of undercuts in the plastic design can make the entire project expensive as well as time-consuming.
Hence, a lot of manufacturers tend to avoid the undercut in plastic design and undercut molding. To avoid these undercuts in injection molding, one must consult to expert and finalize the shape. Moreover, there should be no amendments must be introduced when the design is finalized and production has started.
3.1 Move the Parting Lines
Parting lines is the line that divides the mold into two halves and separates the functionality by changing direction and instructing the place. These parting lines are molded together to intersect distinct features. However, there are certain factors, such as material flow, geometry, and others, that influence the intersection of the parting lines.
3.2 Shutoffs
Shutoffs are a tool for engineers and mold design makers to prevent the material from getting in undercut injection molding. They solve all the difficulties of molds before clinching on one mold. Shutoffs are also used when a mold causes trouble and does not satisfy the design of the mold or product.
To solve the problems with shutoffs, design makers need a creative outlook because the majority of the time these designs include hooks, sealing, and spaces for other accessories to be put in. Hence undercut in such a plastic design becomes complicated. Shut off method enables engineers to have a more creative layout of the mold and add in features for a more functional mold.
3.3 Sliding Side Actions
The purpose of every undercut in injection molding is to minimize the waste and maintain the geographical compatibility of the design for molding by adding more parts to it and easing the probability of undercut in plastic design.
So, sliding side actions help in determining the parts that are required and parts that are not required for further process. Moreover, when the tool is open and if undercut molding is required it can be parted easily.
3.4 Bump Offs
Bump-off is the smart way for electing the materials and adding metals in the process. The mold is divided into two halves with similar shapes, sizes, and dimensions to fit in the form again after reconciliation. Molding snap-fit components like lens covers, container closures, and more is a breeze with the help of bumpoffs.
Instead of a side-action cam, an insert is machined with the appropriate dimensions to allow the undercut to be applied, and the insert is then bolted into the mold. The plastic is compressed during the ejection process, freeing it from the undercut. The transition from the bump to the flat surface should be gentle and well-radiused, but not overly rounded.
The material must be pliable enough to bend around the bump without ripping. Thermoplastic polyurethane (TPU), thermoplastic elastomer (TPE), and low-density polyethylene (LDPE) all work quite well (TPU). The ejection of components is an additional factor to think about while planning a bumpoff.
The ejector must be able to penetrate the part’s surface and remove it without damaging it. In order to provide adequate mold surface area for the item to be ejected, it may be necessary to incorporate an ejector plate into the mold design.
3.5 Hand Load
As the name suggests, the hand load technique is a labor incentive technique. Molds are loaded and inserted by hands, and the extra part is removed through hands when the process is done. This method is still in use because some parts are very delicate to be treated by heavy machines hence the use of skilled hands is integral to infusing in the process.
Products in which the hand load method is required are nozzles, toys for babies, bearers, grips, and many more.
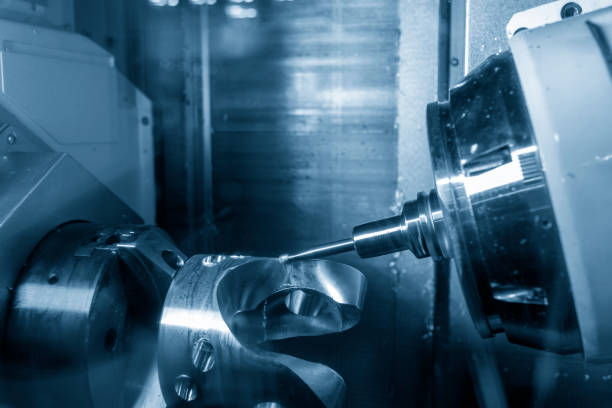
4. Injection Molding Experts Help You Avoid Undercuts
FOW Mould is the best in the plastic injection molding industry and also offers other advanced services for manufacturing thermoplastic products. They have been skilled leaders for decades to execute the business flawlessly and without any trouble.
There are many types of molds for injection molding that FOW Mould offers such as plastic bucket molds and storage box molds. It also includes baby products such as toys, baby strollers, bathtub molds, seat molds, furniture molds, stool molds, and many more. Some of the best injection molding services offered by FOW Mould have been mentioned below.
- Quick Prototyping And Final Design
With their advanced 3D printing and CNC Machines, FOW Mould can produce the best and most accurate prototype in no time. This also enables them to get quick feedback and begin the process of molding as soon as possible. Furthermore, they also ask for design suggestions from the concerned business to cater to the needs of their clients.
- Mold-Making
Mold-making, also known as tooling, can start once the part design is finalized and approved. The metal or metal alloy is used to construct a mold. It consists of a solid center and a hollow surrounding chamber. Both are meticulously crafted to mirror the component’s precise specifications. They are constructed to seem like the manufactured component in terms of size, shape (bends/corners), and texture (splits/ridges). An ideal mold design requires precision and often requires iterative testing to achieve.
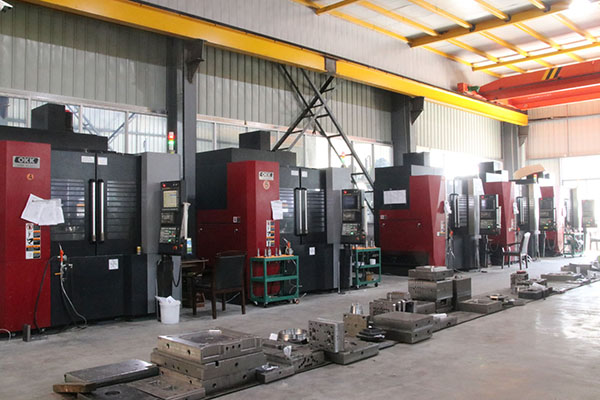
Conclusion
In FOW Mould, the business will only find the best type of mold at the best price and quality. They use high technology to meet the demand with satisfactory results and minimum expenditure and value-for-money commodities. They use types of under-in-injection molding to ensure that their clients get satisfaction only.
Moreover, they believe in optimizing the junk, which is why all the undercut in plastic is reused by FOW Mould to produce as minimum junk as possible. Contact FOW Mould now to get more information and a quotation on this process.