Polystyrene is a common transparent thermoplastic widely used in making instant noodle cups and disposable food containers.
However, polystyrene is not limited to a single type.
It includes various forms such as General Purpose Polystyrene (GPPS), High Impact Polystyrene (HIPS) , Expanded Polystyrene (EPS), and Syndiotactic Polystyrene (SPS).
This article will detail the unique properties, primary applications, and environmental performance of each type of polystyrene.
Keep reading as we uncover the mysteries of these four types of polystyrene.
What Is Polystyrene?
Polystyrene (PS) refers to the polymer synthesized from styrene monomers through a free radical polymerization reaction.
Typically, PS has a head-to-tail structure with a saturated carbon chain as the main backbone and conjugated benzene rings as side groups.
This irregular molecular structure increases the rigidity of the molecule, making PS a non-crystalline linear polymer.
Due to the presence of benzene rings, PS has a high glass transition temperature (Tg) of 80-82°C, which makes it transparent and hard at room temperature.
However, the rigidity of the molecular chains also makes PS prone to stress cracking.
The most notable feature of PS plastic is its high transparency, with a light transmittance rate of over 90%.
It also has good electrical insulation, is easy to color, has good processing fluidity, and is resistant to chemical corrosion.
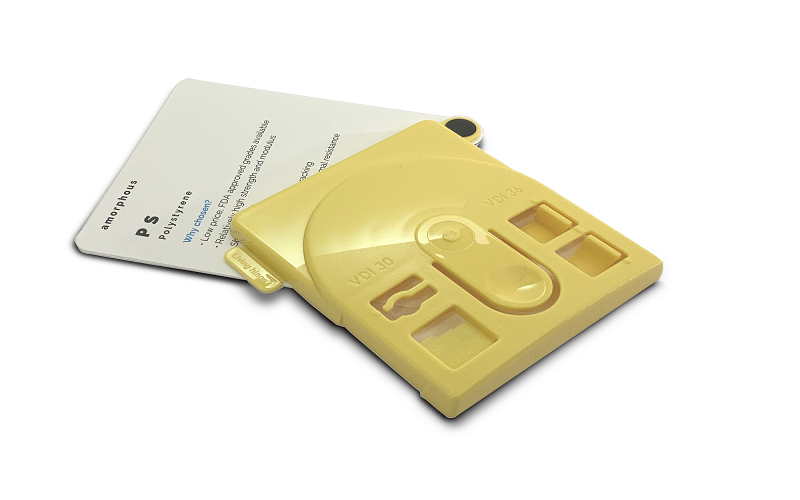
What Are the Different Types of Polystyrene?
Polystyrene generally has four types: General Purpose Polystyrene (GPPS), High Impact Polystyrene (HIPS), Expanded Polystyrene (EPS), and Syndiotactic Polystyrene (SPS).
The specific properties of each type are as follows:
1.General Purpose Polystyrene (GPPS)
GPPS is a colorless, odorless, tasteless, glossy, and transparent solid in bead or pellet form, produced by free radical or ionic polymerization of styrene monomers.
Basic Properties: It has high transparency and good electrical properties, is radiation-resistant and has low water absorption, but it is brittle, has low impact strength, and cannot withstand boiling water and high temperatures.
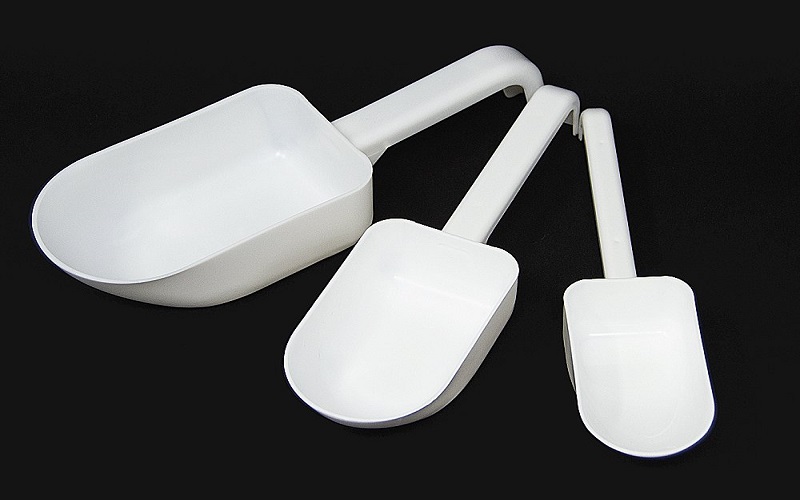
2.High Impact Polystyrene (HIPS)
HIPS is a thermoplastic material made by modifying polystyrene with elastomers, where a small amount of polybutadiene is grafted onto the polystyrene matrix.
Basic Properties: HIPS inherits the dimensional stability of GPPS and has better impact strength and rigidity, good gloss, and is easy to paint.
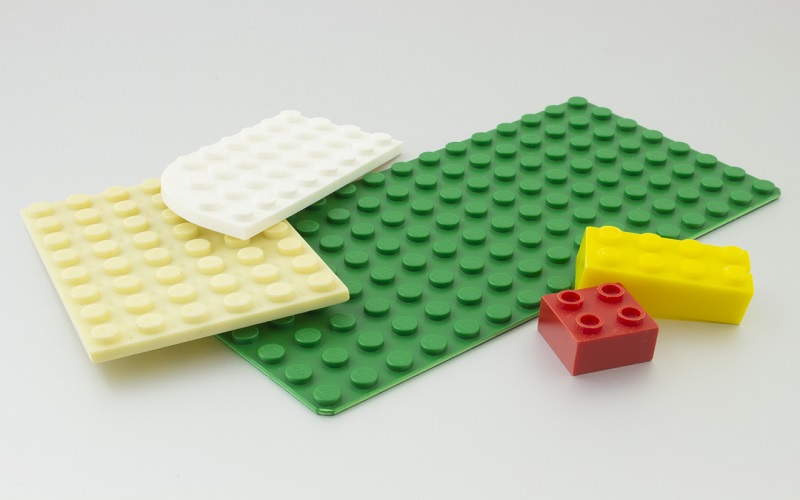
3.Expanded Polystyrene (EPS)
EPS is a lightweight material made by introducing an expanding agent into polystyrene resin, causing it to expand under high temperature and pressure.
Basic Properties: It has a low relative density (1.05g/cm³), low thermal conductivity, is insoluble in water, resistant to impact and vibration, and provides insulation, soundproofing, moisture resistance, and shock absorption.
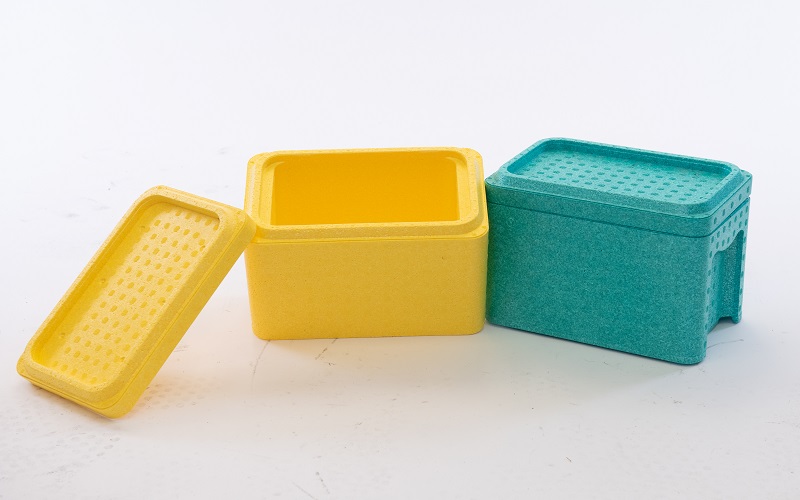
4.Syndiotactic Polystyrene (SPS)
SPS refers to a crystalline polystyrene obtained using a highly oriented catalyst system—metallocene catalysts.
Basic Properties: It has good heat resistance and corrosion resistance, is inexpensive and readily available, but, like general-purpose polystyrene, it is brittle.
Property | GPPS | HIPS | EPS | SPS |
Density(g/cm³) | 1.04-1.09 | 1.04-1.06 | 1.05 | 1.01-1.4 |
Tensile Strength(MPa) | 45 | 15-30 | 0.2-0.5 | 41 |
Flexural Strength(MPa) | 60–100 | 40–70 | 0.2–0.5 | 70–100 |
Thermal Conductivity(w/(m·K)) | 0.04~0.15 | 0.16 | 0.03–0.04 | 0.16 |
Glass Transition Temp (°C) | 80–105 | 70–80 | 80–82 | 100–120 |
Types Of Processes For Manufacturing PS Plastics
Polystyrene plastics can be processed into various products using multiple molding methods, mainly including injection molding, extrusion molding, and foam molding.
Injection Molding
The conditions for polystyrene injection molding are roughly as follows: barrel temperature around 200°C, mold temperature 60–80°C, injection temperature 170–220°C, pressure 60–150 MPa, and compression ratio 1.6–4.0.
However, for flame-retardant grade HIPS, the processing temperature must be below 240°C to prevent degradation reactions of the additives.
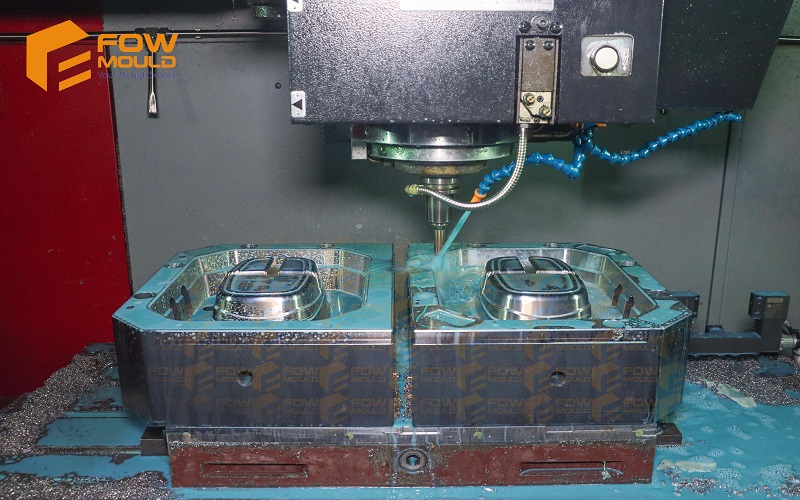
Extrusion Molding
During extrusion molding, the commonly used screw length-to-diameter ratio (L/D) is 17–24, with air cooling, and extrusion temperatures ranging from 150–200°C.
Common extruded PS products include pipes, rods, sheets, films, and fibers.
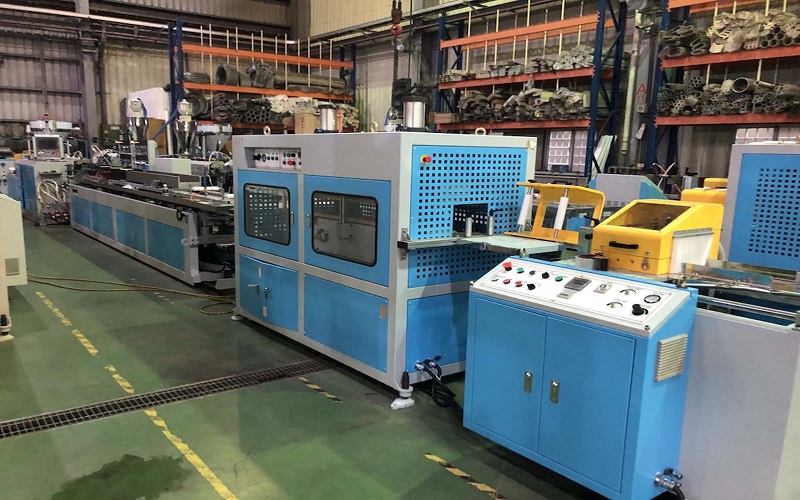
Foam Molding
Currently, the one-step foam molding process is primarily used for polyurethane foam.
This involves adding raw materials such as polyether (or polyester) polyols, diisocyanates, catalysts, and other additives together, then mixing them at high speed before foaming.
This method has the advantages of simplicity, low equipment investment, and ease of operation and management.
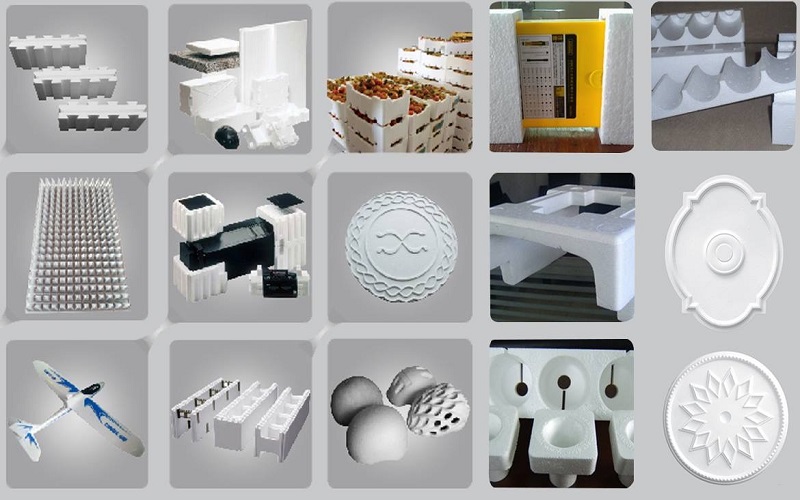
How To Use The Different Types Of Polystyrene?
Each type of polystyrene has its own unique characteristics and drawbacks, making them suitable for various application fields.
For example,GPPS is ideal for manufacturing many transparent containers, disposable tableware, stationery, and electronic device housings.
HIPS is primarily used for packaging and disposable items, especially food packaging materials and tableware.
EPS, as a foam plastic, is widely used for shockproof packaging materials for mechanical equipment, instruments, household appliances, handicrafts, and other fragile and valuable products, as well as for fast food packaging.
As for SPS, it is mainly used as engineering plastics for gears and bearings, high-performance electronic insulation materials, high-temperature automotive parts , heat-resistant food containers, and high-strength packaging materials.
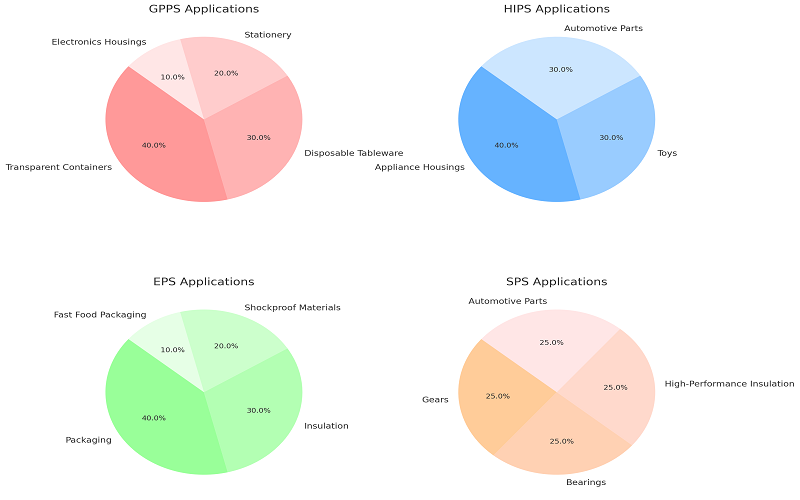
Which Types Of Polystyrene Can Be Recycled?
In plastic recycling symbols, the number “6” represents polystyrene, indicating that PS is theoretically recyclable plastic.
However, the practicality of recycling different types of polystyrene varies due to their unique properties and applications.
For instance, GPPS is low-cost and often used to make various everyday items and disposable tableware.
However, because GPPS is extremely difficult to degrade, it can lead to environmental pollution, commonly known as “white pollution,” especially in areas with underdeveloped recycling systems.
HIPS presents recycling challenges due to the rubber components added to enhance its impact resistance, making the recycling process more complex.
The most severe issue lies with the recycling of Expanded Polystyrene .
While EPS is inexpensive to produce, its manufacturing often involves the use of chlorofluorocarbons (CFCs) or butane as blowing agents, which can cause environmental pollution.
Moreover, EPS products are hard to degrade and can easily contribute to “white pollution.”
Therefore, it is recommended to avoid using disposable plastic tableware whenever possible and to make efforts to improve PS recycling systems.
This includes increasing investment in recycling technologies to enhance the recycling rates of polystyrene.
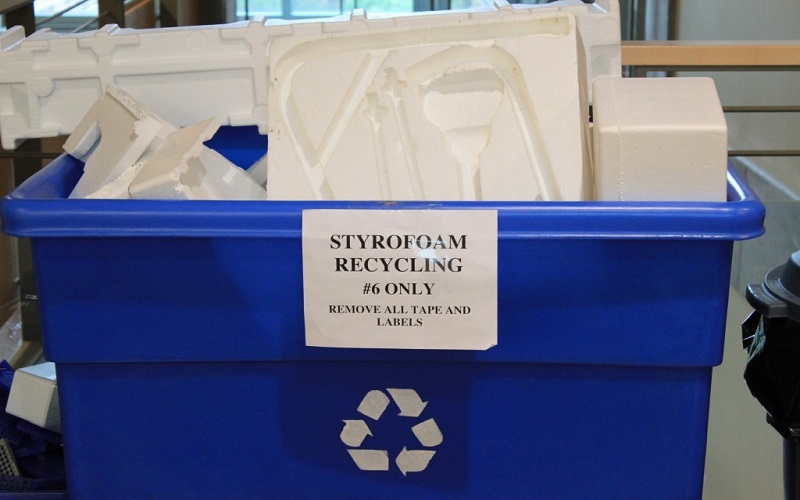
Identification Of The Safety Of Polystyrene
The question “Is polystyrene safe?”has always been a topic of concern. In fact, polystyrene is a material with very low toxicity and is considered a hygienic and safe type of plastic.
Polystyrene products commonly encountered in daily life, such as disposable plastic lunch boxes, generally pass national safety certification standards, and are therefore safe to use.
However, although PS plastic itself is non-toxic, it can undergo thermal decomposition at high temperatures, producing harmful gases such as hydrogen chloride.
Long-term exposure or improper usage conditions may cause health issues such as dizziness and general discomfort.
Additionally, plastic tableware can experience chemical migration at high temperatures, especially when in contact with hot food or beverages, potentially releasing some chemicals that pose health risks.
Therefore, when using polystyrene plastic tableware, it is advisable to avoid using it to hold strong acidic substances (like orange juice), strong alkaline substances, or placing it in the microwave for heating.
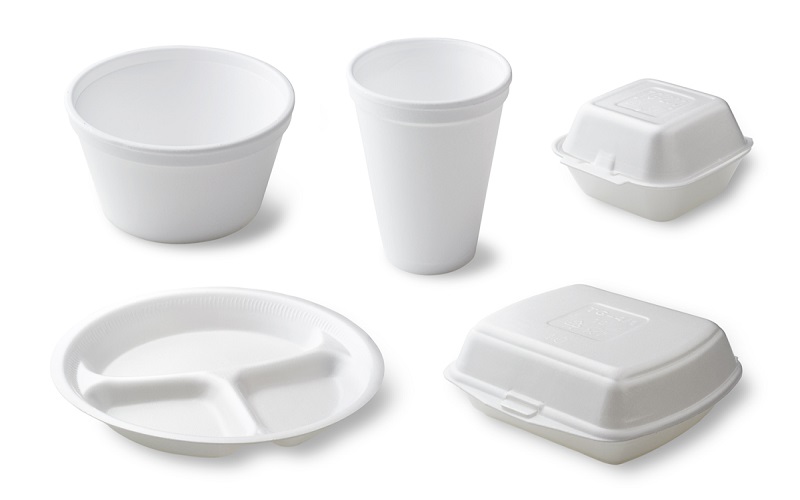
Conclusion
From the above content, we understand that each type of polystyrene has its own unique properties and applications.
GPPS is highly transparent, commonly used for food containers, disposable tableware, and stationery, but it is brittle, difficult to degrade, and can cause environmental pollution.
HIPS has good impact strength and rigidity, suitable for appliance housings, toys, and automotive parts, but the addition of rubber components makes the recycling process more complex.
EPS is a type of styrofoam, widely used for packaging, construction, and fast food packaging, though the blowing agents used in its production may pollute the environment and it is difficult to degrade.
Finally, SPS has excellent heat and chemical resistance, mainly used for engineering plastics, electronic insulation materials, and high-temperature automotive parts, but it has fewer recycling channels.
If you would like to learn more about polystyrene and other types of plastics, and how they can benefit your projects, please contact FOWMOULD immediately.