ABS plastic, with its excellent mechanical properties, outstanding impact resistance, and ease of processing and molding, plays a central role in industrial design and plastic production.
By altering formulations and manufacturing processes, different types of ABS plastic can exhibit varied physical and chemical properties to meet specific application needs.
In the following content, we will explore the diversity of ABS plastic and illustrate its significant role in modern manufacturing.
What Is ABS Plastic?
ABS plastic is a terpolymer composed of three monomers: acrylonitrile, butadiene, and styrene, each imparting different properties to the plastic.
Acrylonitrile provides high strength, thermal stability, and chemical stability; butadiene contributes toughness and impact resistance; styrene offers ease of processing, high gloss, and high strength.
Combined, these monomers form ABS plastic, which is known for its excellent comprehensive performance, toughness, hardness, and rigidity.
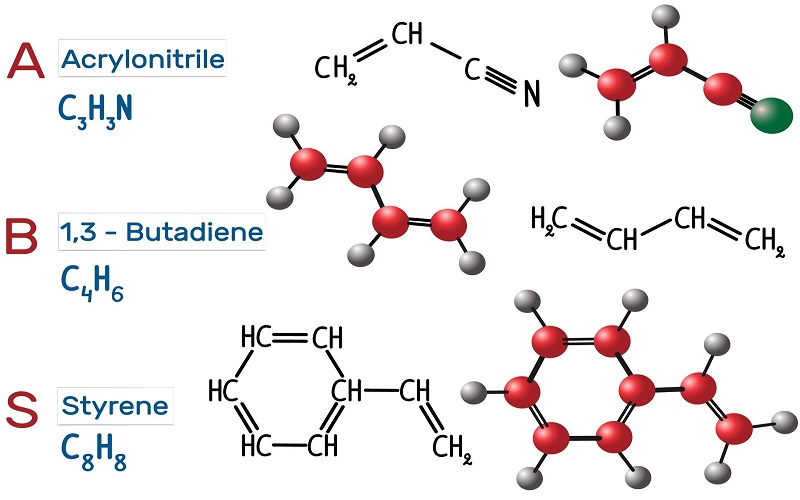
Properties Of ABS Plastic
ABS is favored across multiple industries primarily due to its excellent inherent properties and compatibility with various manufacturing processes.
Below are the main characteristics of ABS plastic:
Impact Resistance
ABS boasts high impact strength, excellent wear resistance, and good dimensional stability, making it suitable for bearings operating under moderate loads and speeds.
Glossy Surface
ABS is an opaque, ivory-colored granular material with low water absorption, which is non-toxic and odorless.
Its products can be dyed in various colors and feature a high glossiness of 90%.
Thermal Properties
ABS has limited heat resistance with a deformation temperature ranging from 93 to 118°C, which can be increased by approximately 10°C through annealing.
It remains tough at -40°C and is suitable for long-term use between -40 and 85°C.
Electrical Insulation
ABS exhibits good electrical insulation properties, maintaining performance across a broad range of frequencies and despite variations in temperature and humidity.
Chemical Resistance
ABS has good chemical resistance, unaffected by water, inorganic salts, alkalis, and various acids.
However, it is soluble in ketones, aldehydes, and chlorinated hydrocarbons, and exposure to glacial acetic acid and vegetable oils can cause stress cracking.
Flammability
The oxygen index of ABS is 18.2, classifying it as a flammable polymer.
When burned, it emits a yellow flame accompanied by black smoke, chars without dripping, and releases a distinct cinnamon odor.
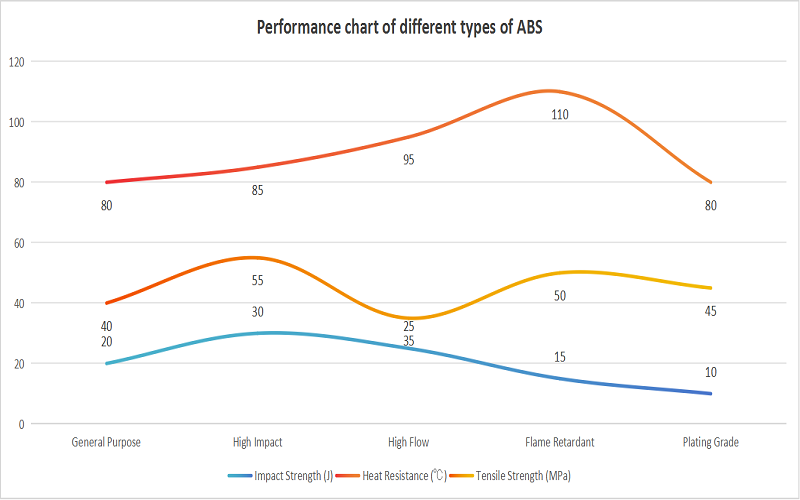
5 Types Of ABS Plastic Grades
In the production of ABS plastic, different types are created by adjusting formulations and improving properties to suit various processing methods and applications.
Below are five types of ABS , each with distinct properties and uses:
1.General Purpose ABS
General Purpose ABS has good impact resistance and moldability, and can be processed through injection molding, extrusion, and thermoforming.
Due to its excellent overall performance and cost-effectiveness, it is widely used in appliances, electronics, and automotive industries.
2.High Impact ABS
High Impact ABS is made by incorporating fillers or rubber modifiers into ABS plastic, primarily to enhance its impact resistance and slight deformability.
It features outstanding strength and toughness, and excellent crack resistance, making it suitable for use in electronics, automotive, and toys.
3.High Flow ABS
High Flow ABS is produced by adding slightly higher molecular weight styrene monomers and modifiers to standard ABS.
It offers significantly enhanced fluidity and good moldability, making it ideal for applications in painting, thin-wall injection molding, and industrial processing.
4.Flame Retardant ABS
Flame Retardant ABS is developed by adding flame retardants to the base ABS material, achieving flame-resistant properties and overcoming the flammability of standard ABS.
It is primarily used in applications requiring both electrical insulation and flame retardancy, such as in housings for electrical and electronic devices, and components for electrical switches.
5.Plating Grade ABS
This type of ABS plastic includes specific light stabilizers and modifiers to provide excellent surface quality and platability.
Plating Grade ABS is extensively used in electronics, telecommunications equipment, automotive, and home appliances.
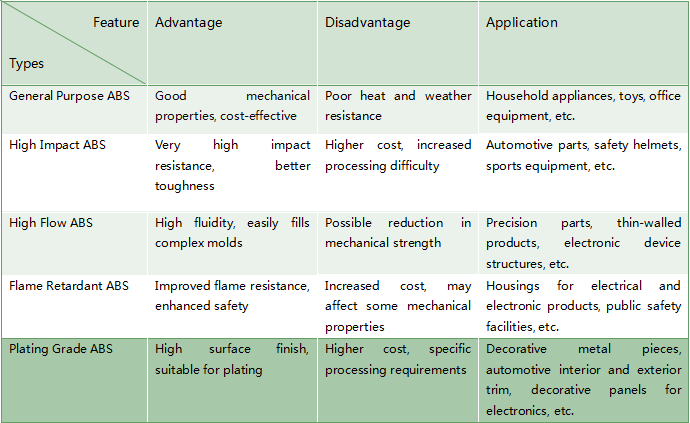
Types Of Manufacturing Processes For ABS Plastic
ABS plastic, known for its excellent mechanical properties and ease of processing, can be manufactured using various molding techniques.
Injection Molding of ABS
Injection molding is widely used for creating ABS plastic products like toys, appliance components, and electronic casings.
The molecular structure of heat-resistant ABS improves its thermal resistance but also raises internal stresses, which can lead to stress cracking, whitening, and brittleness.
Thus, managing internal stress is essential in the ABS injection molding process to ensure product quality.
3D Printing with ABS
ABS was one of the first plastics used in industrial 3D printing, popular for its low cost, good mechanical properties, excellent toughness, and impact resistance.
It is important to keep ABS dry before printing, and it is recommended to use a 3D printer with an enclosed chamber.
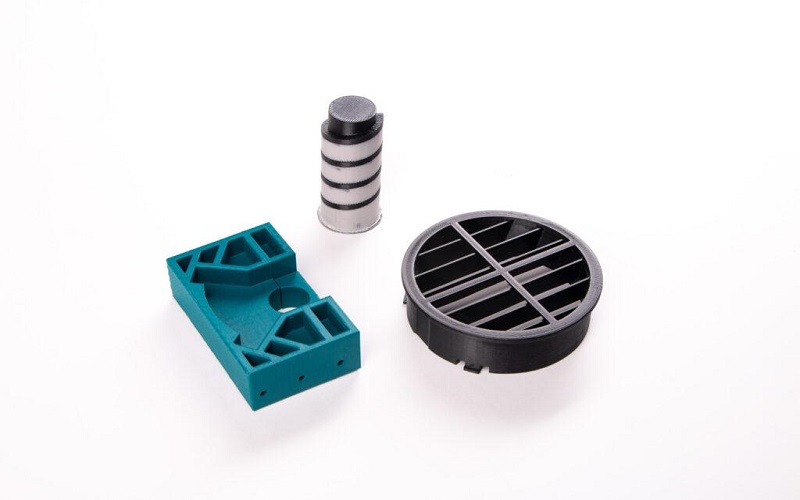
Extrusion Molding of ABS
Extrusion is another common method for processing ABS, mainly used to produce continuous plastic products such as pipes, profiles, and films.
During the extrusion process, ABS pellets are first melted in the heating zone of the extruder and then extruded through a die of specific shape to form continuous long materials.
Extrusion-molded ABS products typically have good surface smoothness and dimensional consistency, suitable for mass production.
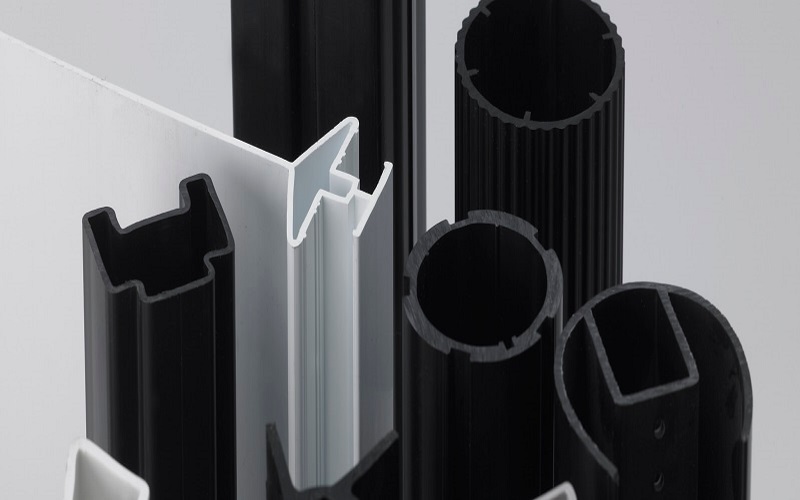
For ABS plastic molding manufacturers, these processes undoubtedly offer a manufacturing solution that is both efficient and ensures product quality.
The Environmental Impact Of ABS Materials
From an environmental perspective, ABS is not biodegradable, meaning it can have a long-lasting impact on the environment. When ABS plastic is discarded and enters landfills or natural environments, its non-degradable nature means it can persist for decades or even longer.
This persistence may lead to soil and water contamination, posing threats to wildlife and plant life.
Additionally, the production process of ABS itself also places a burden on the environment.
Producing ABS requires significant amounts of fossil fuels, consuming energy and generating greenhouse gases and other pollutants that negatively affect climate change and air quality.
During the processing of ABS, various chemical additives such as plasticizers and flame retardants are also used, which, if not properly managed, can further compromise ABS safety and pollute the environment.
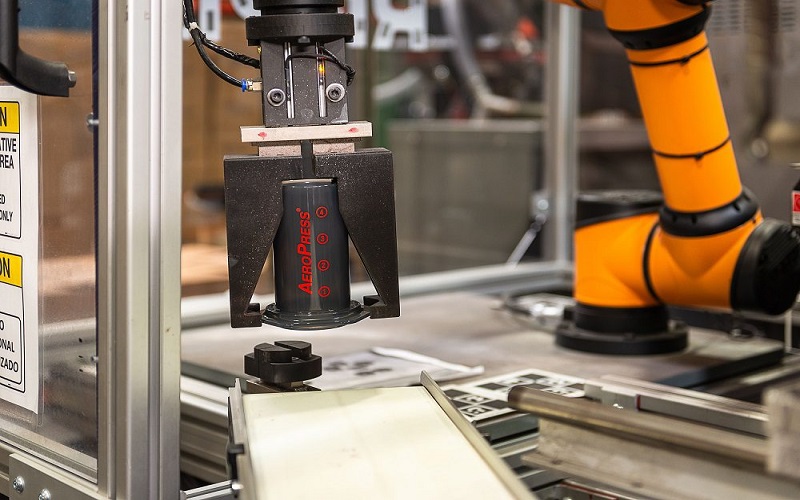
Future Developments In ABS Materials
To avoid the harmful components of plastic additives, researchers are exploring ways to enhance ABS performance by incorporating additional materials.
For instance, adding nanoparticles or high-performance fibers is being investigated to improve its strength and durability.
Additionally, to address the environmental impact of ABS, researchers are working to develop biodegradable ABS materials that can naturally decompose at the end of their life cycle, thereby reducing environmental impact.
Many companies and research institutes are searching for eco-friendly alternatives to ABS.
Bio-based materials such as polylactic acid (PLA) and polyhydroxyalkanoates (PHA) are considered sustainable substitutes for ABS.
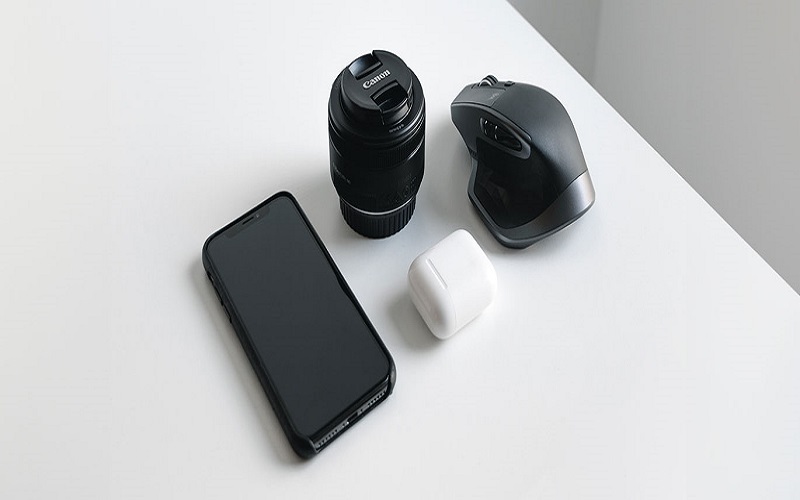
Conclusion
In summary, there is a wide variety of ABS plastics, each type having its own advantages, disadvantages, and suitable applications.
When selecting ABS plastic, it is necessary to choose a cost-effective and quality-stable type based on the specific application and environment to ensure product quality.