TPE (Thermoplastic Elastomer) has both thermoplastic and elastomer properties, which means they are heat-resistant and long-lasting, but retain flexibility. On the other hand, TPU (Thermoplastic Polyurethane) is a form of TPE with high resistance to abrasion, oils, and chemicals.
Due to their flexible qualities, TPE and TPU plastic filaments are used as 3D printing materials where they add a soft touch feature to printed items. Despite the similarities, TPU and TPE have differences that make each material sought after for some applications and less preferred in others. These differences also alter the kind of 3D prints that each material produces.
This blog post looks at TPE vs TPU in relation to their individual basic properties and applications, and the 7 main differences between them.
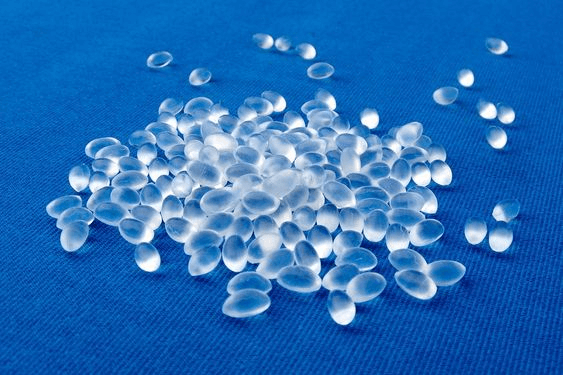
Introduction of TPU Material
TPU, also called thermoplastic polyurethane, is formed through a chemical reaction involving diisocyanate and diols. It is a thermoplastic elastomer renowned for its flexibility, durability, and abrasion resistance as well as its ability to resist oil, grease, and chemicals.
Its characteristics make TPU extremely popular and applicable to a range of markets, including agriculture, medical devices, sports and leisure, and industrial components, among others.
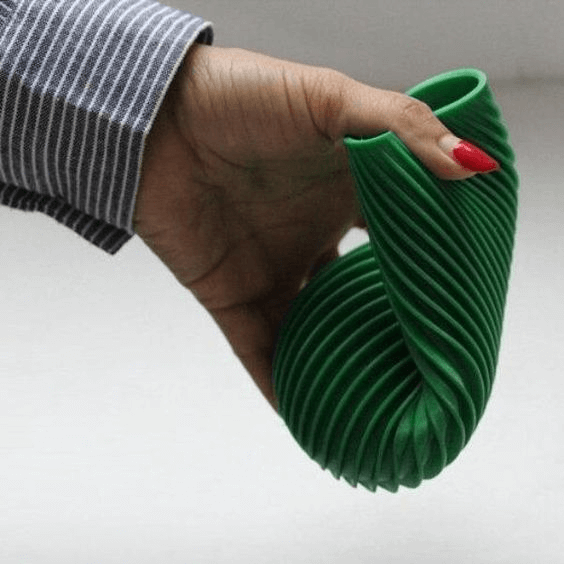
Basic Properties of Thermoplastic Polyurethane
TPU plastic combines several physical and chemical properties, which allows them to provide certain benefits in different applications.
- Abrasion
TPU has excellent abrasion resistance compared to other materials, such as PVC and rubber. It is most preferred in applications, such as specialty cables and automotive parts, where abrasion resistance is required. TPUs abrasion resistance is measured using a wear test, which must comply with standard guidelines, such as DIN 53516 (ISO 4649).
- Shore Hardness
Shore hardness tests TPUs resistance to indentation or penetration by another material or force. TPU materials are of two types: type ‘A’ and ‘D.’ While type A TPUs are flexible and type ‘D’ TPUs are rigid.
- Tensile Strength
The tensile strength of TPU indicates its reaction to uniaxial stress, meaning how much strain occurs before deformation. Having characteristics of both plastic and rubber, TPU has excellent tensile strength, which is measured in the standard ASTM D412.
- Chemical Resistance
Against microbes, such as fungi and bacteria, TPUs are resistant to degradation. However, its resistance ability is impeded when it is constantly exposed to microbial activity in hot or humid areas. Aliphatic TPUs are best for areas with high sunlight as they do not yellow or degrade under UV radiation. Also, TPUs remain stable when in contact with oil or grease.
Common Applications of Thermoplastic Polyurethane
TPU plastic is popularly used for many purposes. The most common are automotive parts, protective cases for consumer electronics, medical devices, and industrial components.
- Automotive Parts
Gear knobs, console parts, instrument panels, and other parts used in automotive interiors have strict requirements, such as abrasion and scratch resistance and good surface quality. Due to their perfect combination of aging and abrasion-resistant properties, TPUs are the most fitted for the automotive industry.
TPUs also have fast cycling performance, making them a cheaper and better solution for the injection molding process.
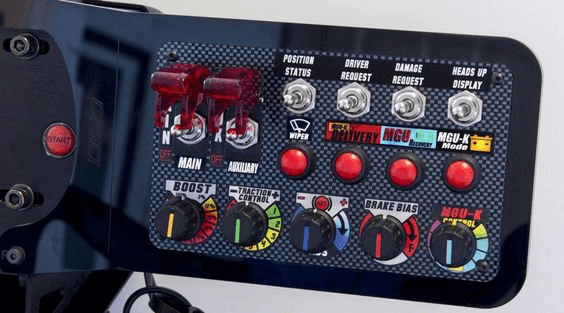
- Protective Cases for Consumer Electronics
TPU offers extreme flexibility at low temperatures, excellent paintability, good impact and environmental resistance, as well as crystal-clear transparency, which is why they are the material of choice for making protective cases for smartphones and other consumer electronics. This material also provides a super handgrip and has an elegant matte finish.
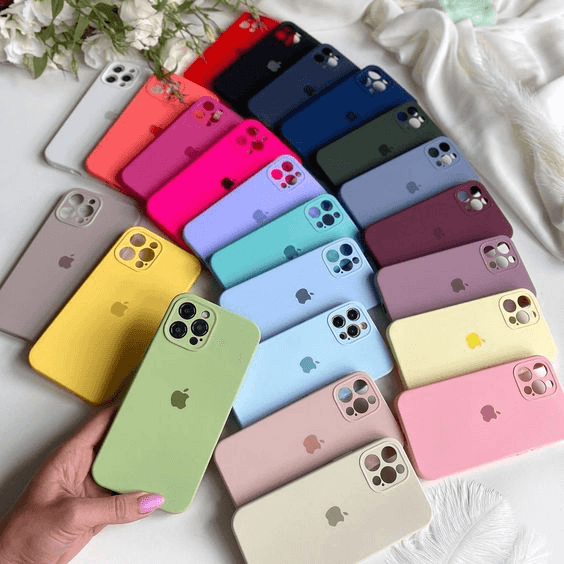
- Medical Devices
As a result of its high-performance characteristics, thermoplastic polyurethane (TPU) is well-known and desirable for medical and healthcare applications.
Its excellent mechanical properties and resistance against oil, grease, and chemicals allow its usage in the production of a wide variety of medical devices, such as diagnostic and artificial respiration devices, healthcare mattresses, and medical instrument cables.
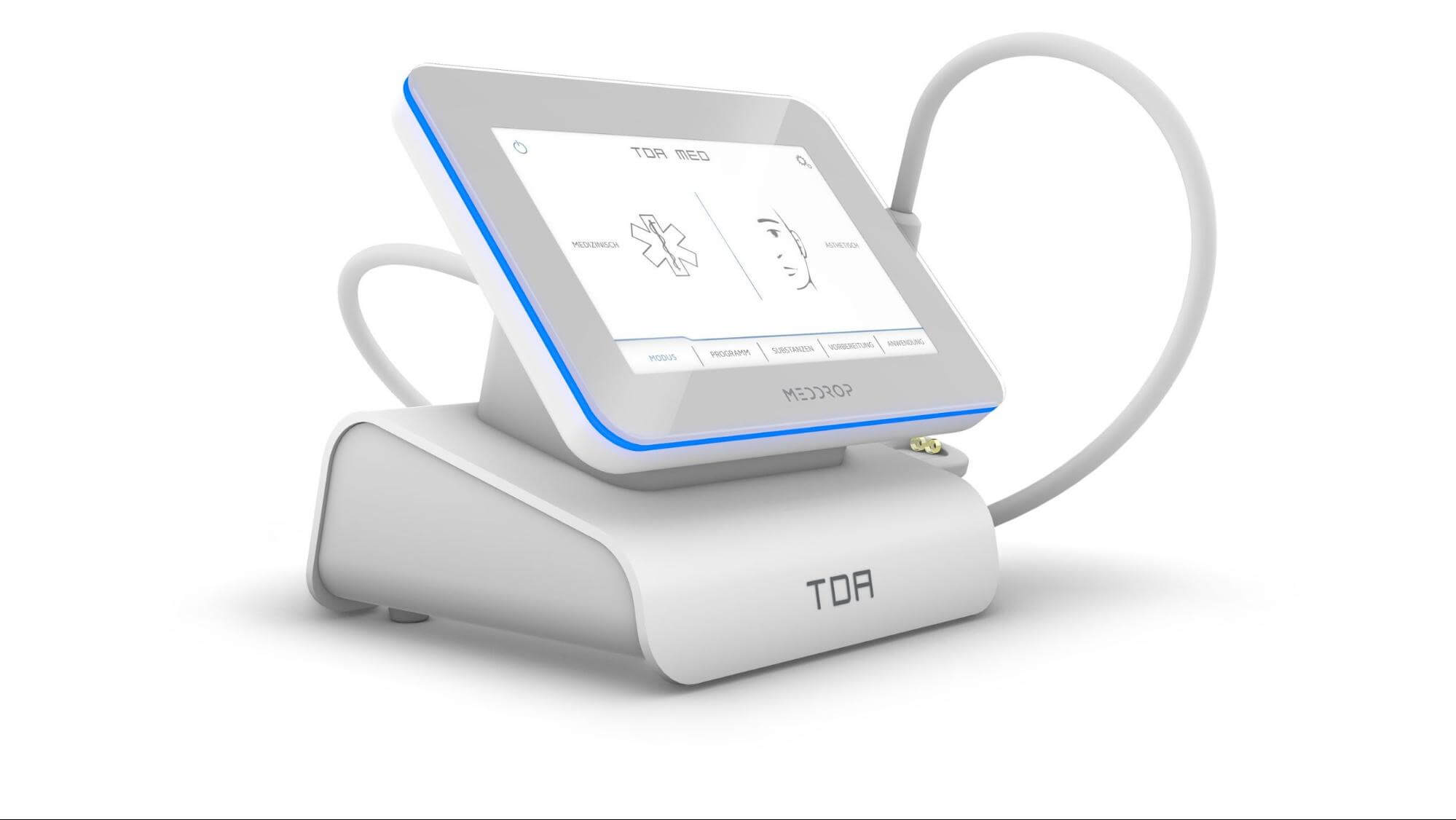
- Industrial Components
Offering low creep and outstanding mechanical strength, TPUs are used as materials for making top-quality industrial components, such as timing and transmission belts, and conveyor belt profiles.
In manufacturing seals and gaskets, TPUs improve flow properties, enable high hydrolysis resistance of industrial seals, and offer low compression at very high temperatures.
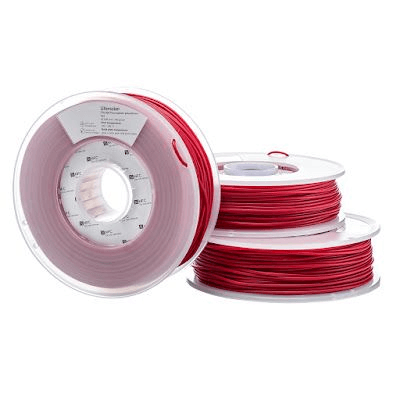
Introduction of TPE Material
Thermoplastic elastomers (TPEs) can also be called thermoplastic rubbers. They can be a combination of two or more polymers or formeIntroduction of TPE materials as unique block copolymers. They combine the performance of rubber with the easy producibility of thermoplastic materials but offer more versatility than either.
TPE material has higher melting points and tensile strength than most homo-polymers of the same molecular weight. This is due to the two-phase separated structure: hard thermoplastic and soft elastomer. Since the two phases retain their properties in the mixture, they are called a two-phase structure.
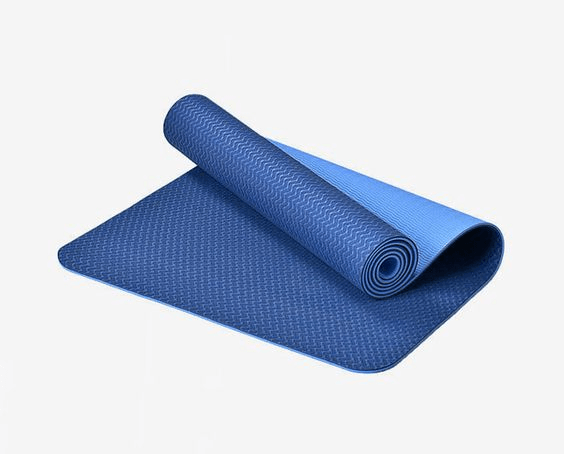
Basic Properties of Thermoplastic Elastomer
The property of any TPE material is a function of the chemistry and nature of the constituents and their morphology. Each TPE material has varying hard and soft phases that influence its properties.
- Mechanical Properties
TPE’s mechanical strength, hardness, abrasion-resistant properties, tear resistance, and compression and tension set above ambient temperature and below softening point are largely affected by its hard phase. The hard phase has inherent plastic properties, such as high-temperature performance, easy processability, and good flexibility.
- Flexibility
TPE properties are a combination of rubber and plastic characteristics. It has an elastic soft phase, which generates rubber-like properties of elongation, durometer hardness (resistance to indentation), low-temperature performance, dynamic properties, and compression and tension set.
- Electrical Properties
Materials used as electrical insulators have certain properties, such as low specific weight, excellent mechanical, chemical, and thermal strength, surface leakage resistance, and easy processing and production.
Since most TPE materials are generally insulators, a proper combination of these properties is found in modern TPEs. However, its insulation properties will depend on the level of polarity in the material.
- Thermal Properties
The thermal properties of a TPE material are essential to its performance and melt processing. The mechanical performance of the hard phase at ambient temperature depends partly on the glass transition temperature and the sub-room temperature performance as well as the brittle point is dependent on the soft phase.
Common Applications of Thermoplastic Elastomer
TPE material is popularly used across many applications. The most common are adhesives, coatings, & sealants, consumer goods, and industrial & construction fields.
- Adhesives, Coatings, and Sealants
TPEs have many qualities, like tack, shear performance, and low melt viscosity, that make them perfect for creating adhesives, coatings, and sealants.
They also offer superior adhesive abilities to various substrates and surface textures, as well as combine temperature flexibility with high heat resistance. They are applied in making tapes and labels, protective films, high-performance adhesives, sprayable coatings, and many sealants.
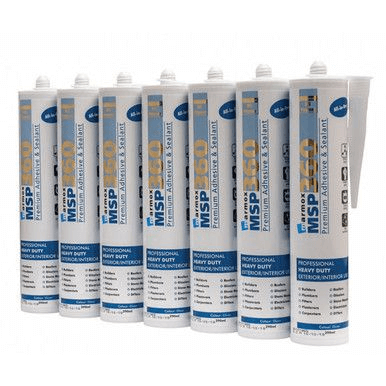
- Consumer Goods
Consumer goods frequently come in contact with the body and they are commonly used in hygienic applications, hence, they are required to be very safe. Thermoplastic elastomers meet many regulatory standards, including FDA, which encourages their use in the consumer goods industry.
They are used to manufacture many products and plastic compounds used daily, from baby toys to plastic handles to packaging materials.
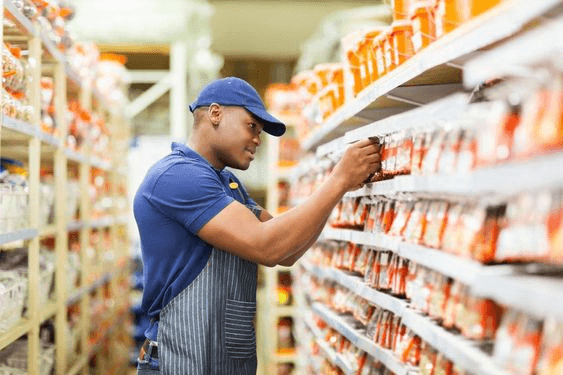
- Industrial and Construction Field
Elastic polymers have a wide array of applications in these industries, These include applications in printing and building, metalworking, machine interior, and renovation works.
Due to their excellent damping ability, TPEs are used to make vibration isolators, drum suspension bushes, springs, and shock absorbers. In construction, they bring environmental resilience, durability, and flexibility to products.
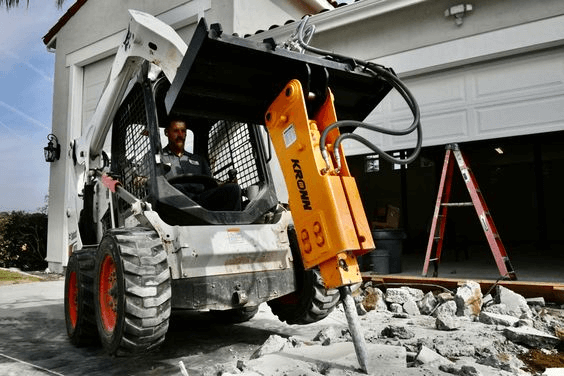
TPE vs TPU: 7 Main Differences
Thermoplastic elastomers and polyurethanes have many differences between them. In general, TPEs are softer and more flexible than TPUs. However, the rigidity of TPUs makes them an easier material to print with.
TPE is also less resistant to abrasion, grease, oils, chemicals, and extreme temperatures than TPU. Although these materials differ, they also share some qualities, such as waterproof, UV resistance, and good heat and impact resistance.
Hardness Range
TPE and TPU both have a certain but adjustable hardness range. While TPEs range from 0A to 100A, TPUs commonly have a hardness range of 60A and 70D.
The hardness range of TPE can be controlled by decreasing the amount of vinyl and that of TPU is mainly controlled by altering the ratio of diisocyanate and polyol. However, the hardness of both materials changes by modifying the level of styrene
Shore hardness measures the rigidity of 3D printing filaments. Because of its softness, 3D printer TPEs are difficult to print. In contrast, TPUs have a high shore hardness and are easier to use for 3D printing.
Mechanical Properties
TPU has more load-bearing capacity, bending resistance, and tensile strength than TPE, making thermoplastic polyurethanes more suitable for heavy industry components than thermoplastic elastomers. The two materials have different molecular segment structures, and TPU supports better resilience and wear resistance than TPE.
Also, blended TPE has a more balanced material microstructure and general properties when compared to polymerized TPU. TPE’s multicomponent is not very conducive to its resilience. For TPEs with high hardness, the amount of polypropylene in the material reduces its resilience, resulting in easy deformation of the product under continuous external force.
TPEs have a soft molecular structure, which gives them a delicate and soft texture feel, and offers a smooth and comfortable product surface. But, TPUs feature strong friction without smooth texture, allowing the material to offer greater abrasion resistance than TPE.
Chemical Resistance
TPU materials have good resistance against many mineral oil-based greases and oils used mainly for hydraulics, while TPE has no oil resistance. TPU and TPE materials biodegrade within 3 to 5 years. Hence, they are both considered sustainable 3D printing materials.
TPU ethers are fuel-resistant and are especially great for making waterproof products. Also, both the polyester and polyether grades of TPU ethers are chemically resistant to solvents, acids, and bases.
Although TPU has a non-toxic nature, it emits dangerous fumes when it comes in contact with fire or other chemicals. When burnt, TPE is non-toxic and has a non-harmful aroma. Unlike TPUs, TPEs offer excellent hydrolytic resistance.
Processing Temperature
The temperature range for TPE is from 150 to 210 degrees Celsius. If the temperature is above that range, TPEs tend to get either brittle and crack or become extremely rigid.
One of the main advantages of thermoplastic elastomers is their suitability for melt-processing techniques like injection molding. This enables the production of high-volume and low-cost parts that otherwise would be manufactured using expensive and complex thermosetting and vulcanizing processes.
TPUs have melt temperatures of between 190 and 220 degrees Celsius. However, this range may increase depending on how hard the TPU material is. Its melting point and max temperature at the end of the barrel increase with its hardness.
TPU products generally have a mold temperature of between 10 to 60°C. A low mold temperature can easily cause a later crystallization, resulting in post-shrinkage of products.
UV Stability
Both TPE and TPU materials offer good UV resistance. UV-stable TPE is created by adding different compositions of stabilizers to the TPE resin. This resin then absorbs or blocks UV radiation before it reaches the polymer matrix. UV-stabilized TPE is used in the manufacture of industrial machinery that is subject to outdoor applications.
Aliphatic TPUs ensure color fastness and superb aesthetic finish on products. They also have superior UV resistance along with other properties. Although UV-stabilized TPU ethers will retain most of their physical properties when exposed to sunlight, they will likely turn yellow. Where yellowing is a concern, aliphatic TPUs instead of TPU ethers are preferred.
Recyclability
Due to their thermoplastic properties, both TPE and TPU materials are completely recyclable, through similar recycling processes as other thermoplastics. They both maintain their structural integrity when reprocessed, enabling the reuse of production waste and the reduction of costs.
Due to the interconnection of hard and soft phases within the block-copolymer chain, TPU is highly recyclable and processable into second-grade high-quality raw materials or products.
TPU plastics are also biodegradable and will likely break down within 3 to 5 years, leaving no toxic residues. TPEs can be recycled within a production process and allow the addition of 1 -15% to the virgin material after testing and risk assessment.
Material Costs
TPE is less expensive than TPU. However, the costs of TPE vs TPU per kilogram vary across the different brands and types. Since the components of TPU and TPEs are usually varied, the material price is also bound to vary as these components have different prices. Other factors, such as density and quality, also affect the cost of these polymers.
Famous brands of TPE filament range from 40 to 140 $/kg and popular brands of TPU filament range from 65 to 180 $/kg.
TPE vs TPU: How to Choose
TPU is one of the categories of TPEs. While these materials can be interchanged in some cases, other situations require the best-suited material. Choosing the perfect material out of these two materials will depend on the following factors: understanding the application, cost-benefit analysis, and tests and evaluation.
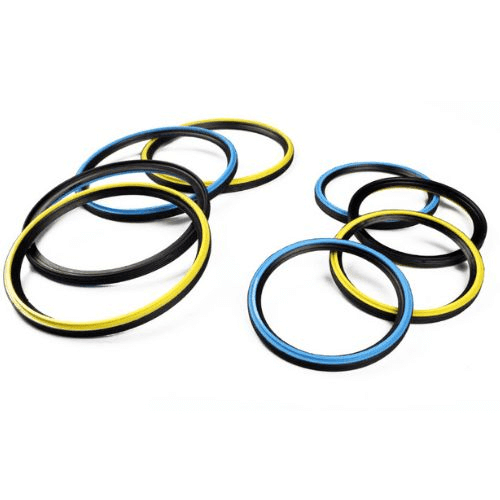
Step 1: Understanding the Application
When choosing between TPU and TPE, it is essential to consider the ideal material choice for the application. TPU is preferred over TPE when manufacturing products with stricter requirements for abrasion and pressure resistance. TPU is also used when a longer life cycle is required.
TPE is more commonly found in consumer products, while TPU is mostly used in the production of heavy industrial components. Other applications of TPE include medical equipment like syringes, intravenous delivery systems, and blood-collection devices.
Step 2: Cost-Benefit Analysis
After considering the application where the material is needed, the next step is checking which option is best for the bottom line. TPEs and TPUs are generally used less frequently than other thermoplastics in 3D printing because they are more expensive.
Thermoplastic polyurethane especially is not as cost-effective as many other comparable thermoplastics, including TPEs. However, analyzing the material cost and how it affects production will help you make the best decision.
Step 3: Test and Evaluate
The material selected should be subjected to various tests to inspect its quality and suitability for application. It should be tested physically for material resistance, shore hardness, tensile strength, abrasion, shrinkage, tear strength, and compressions set.
It should also be tested chemically for its reaction to solvents, acids and bases, oils and greases, microbes, hydrolysis, UV radiation, and flame retardance. All tests should comply with recognized standards, such as VLE specification, TSCA, ISO, and RoHS, among others.
FOW Mould: Offer High-Quality Injection Molds for TPU and TPE Parts
FOW Mould offers a one-stop solution for quality and affordable injection molds for TPU and TPE parts. We offer mold design and manufacture, plastic product design, CNC machining, over-molding, insert molding, and injection molding services to various industries, including automobiles, home appliances, pet products, and furniture molding, among others.
Custom Mold Design and Engineering
FOW Mould specializes in the design of custom injection molds for TPU and TPE parts. We design over molds, insert molds, and plastic injection molds to meet your specifications accurately. With just your mold sketch or sample, we create precise designs according to your requirements.
FOW Mould offers premium quality molds for creating buckets, automotive parts, storage boxes, plastic chairs, toys, home appliances, etc using TPE and TPU materials. Our design experts work closely with you on mold design, material choice, and other details of your mold production.
Precision Mold Manufacturing
FOW Mould operates a reliable mold-making factory manned by a skilled team and equipped with high-end machinery that ensures we create molds with a high level of accuracy. Some of our in-house machinery include wire-cutting machines, engraving machines, lathe machines, and high-speed CNC machines.
By inspecting the quality of molds during each phase of production, we assure you of the best machines for TPE and TPU parts. We strive to help clients create first-rate products and parts at a competitive price.
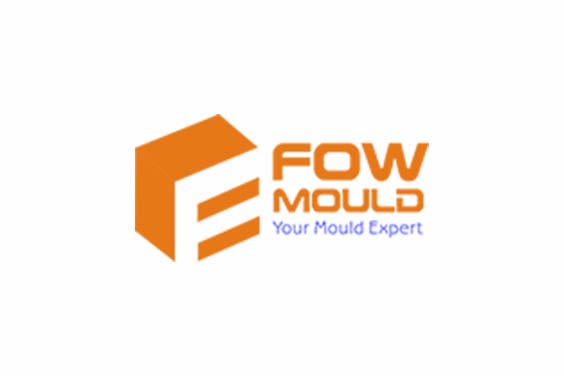
Multi-Material and Multi-Cavity Molds
Multi-material molds combine two or more materials having different properties while multi-cavity molds have more than a cavity of the same part. These molds have a short lead time, resulting in faster completion of TPE or TPU parts. The molding processes require the utmost attention to detail and are best handled by professionals.
FOW Mould is an experienced multi-material and multi-cavity mold manufacturer with an annual capability of over 900 molds. Our molds provide a higher yield rate for better volume returns, assure completion of complex parts, and reduce assembly costs.
Prototyping and Rapid Tooling
Prototypes are experimental models made to inspect the design and fix any problems. This process is very time-consuming, but FOW Mould employs advanced technologies and machines that ensure rapid prototyping is possible. Prototyping can be applied in manufacturing automotive parts and other components in large amounts.
Our rapid tooling process allows prototypes of project parts and tools to be made cheaply and fast. It also allows for early detection and correction of flaws in the prototype before mass production.
Conclusion
TPE and TPU are versatile plastics usable in many functions, from automobile part production to the manufacture of medical devices. They are materials that producers should have in their inventory. In comparing TPU vs TPE, we outlined 7 main differences between the materials, which include hardness range, mechanical properties, chemical resistance, processing temperature, UV stability, recyclability, and material costs.
In general, TPEs are softer and more flexible, making them more suitable for making products with smooth and comfortable surfaces, while TPUs should be used for high-performance applications because of their toughness. However, design and production teams must research to ensure the best material is chosen for each distinct project.
FOW Mould provides professional mold design, plastic product design, and mold-making services using TPE and TPU parts. Our expertise also includes the production of accurate prototypes with 3D printer TPEs and high-resolution machinery. You can contact us for more professional assistance.