Introduction
TPU stands for thermoplastic polyurethane and is a type of thermoplastic elastomer. It is a highly versatile material that is used in a wide range of industries due to its many beneficial properties.TPU combines the best qualities of plastic and rubber while providing high elasticity and mechanical strength.TPU mold is the mold or form used in the process of molding this thermoplastic material, which is commonly used in industries such as automotive, medical and consumer products. Products produced using tpu mold include things like flexible cell phone cases, medical devices, power tools, footwear and many other items.
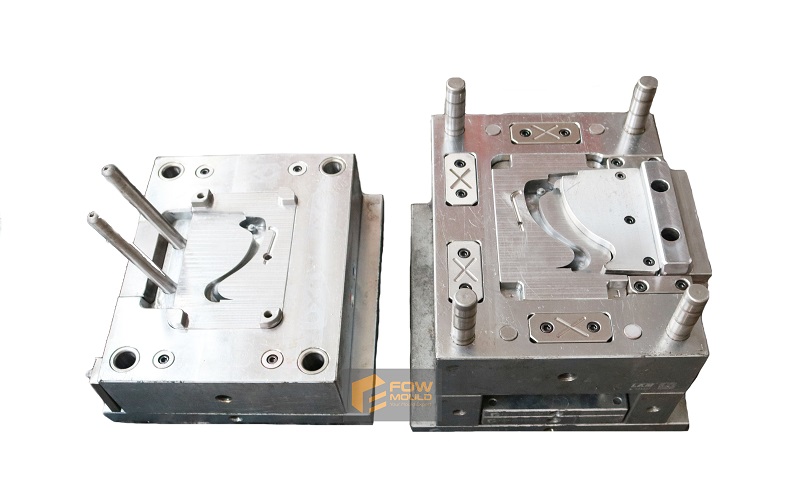
The key points of designing a TPU Mold
Due to the special properties of TPU material, designing TPU (thermoplastic polyurethane) molds is a complex process that requires an in-depth understanding of TPU properties and the specifics of the molding process. Here are a few factors to keep in mind during the design process:
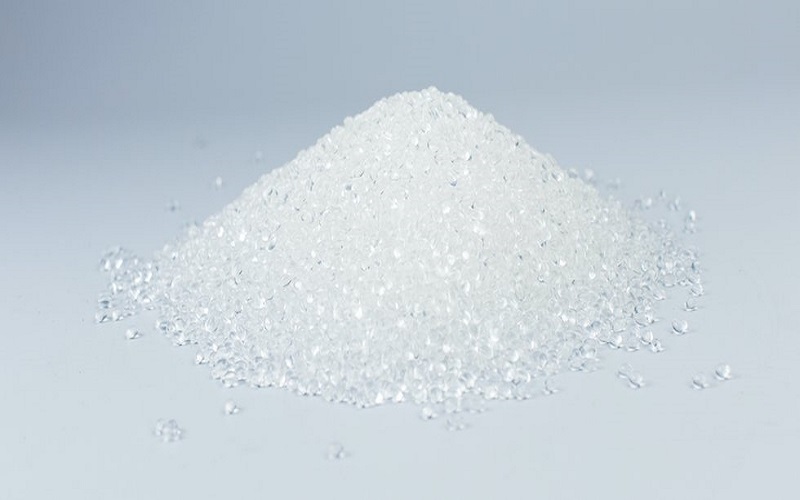
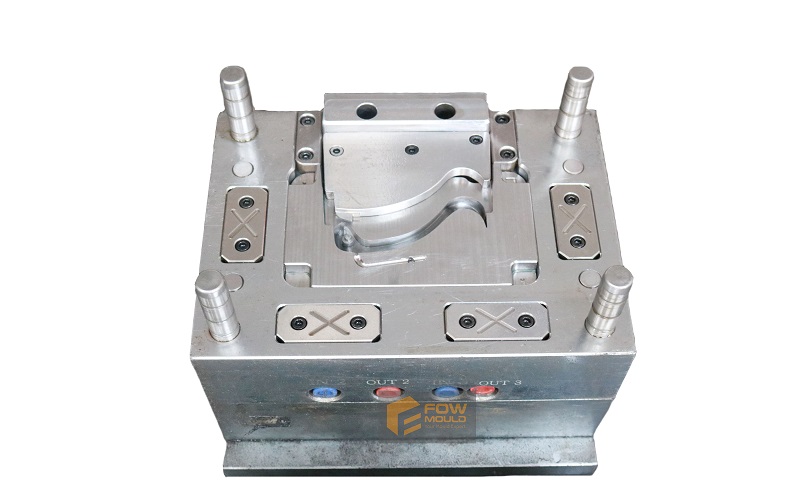
Mold Material:The material of the mold itself also matters. The mold needs to withstand the heat and pressure of the injection molding process and should not react chemically with the TPU. Steel and aluminum are commonly used.
Draft Angles:Unlike rigid plastics, TPU is highly flexible, which allows it to adhere to the mold. To prevent this, molds should incorporate draft angles, which are tiny angles on the vertical walls of the mold to facilitate ejection of the part after it has cooled. These angles prevent the part from sticking to the mold and make the ejection process smoother and more efficient.
Wall Thickness:The thickness of the wall in the part design is a critical factor. Even, consistent wall thickness can help ensure a uniform cooling rate, which in turn minimizes warping and shrinkage. Variations in wall thickness can lead to differential cooling, leading to internal stresses and potentially causing the part to warp or distort.
Shrinkage:All thermoplastic materials, including TPU, shrink to some degree as they cool. This shrinkage needs to be considered in the mold design to ensure that the final part conforms to the desired dimensions. shrinkage of TPU varies depending on the specific grade of the material, but generally ranges between 1.0% and 2.5%. It is critical to consider this in the design phase to ensure that the correct size and shape of the part is produced.
Gating and Vents:The arrangement of the gates and vents is critical, allowing material to enter the mold and the vents to allow air to escape. The distribution of these two is a key factor in the way the material fills the mold and the way it cools, affecting the quality of the final part molded.
TPU mold injection molding details
Injection molding is a common method for processing Thermoplastic Polyurethane (TPU), a versatile and highly durable material.The details of injection molding of TPU moulds are critical to achieving precise and consistent products.
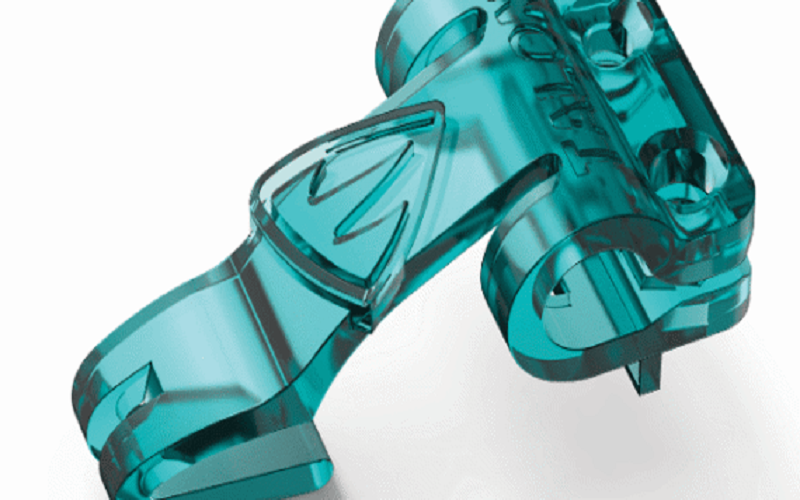
Inside the barrel of the machine, there is a screw mechanism that mixes and heats the TPU pellets. The heat and friction generated by the rotating screw melts the TPU into a liquid state. the TPU pellets are heated to a specific melting point, typically between 190°C and 210°C (374°F and 410°F), and the screw mechanism moves the melted TPU into the mold under high pressure.
Injection speed, pressure, and holding pressure all affect the quality of the final part. Generally, TPU mould requires moderate to high injection speed and pressure. A longer holding pressure may be needed to prevent shrinkage and ensure the mold is fully filled.
After the part is ejected, it may require some finishing work such as removing the sprues, runners, or gates, and any other post-molding operations like painting or coating.
Finally, it is important to consider the maintenance of the TPU mould to ensure its longevity and optimum performance. The mold should be cleaned and inspected regularly to ensure there are no signs of wear or damage that could affect the product quality. Any necessary repairs or adjustments should be made promptly to avoid any potential production delays or defects.u
Application of TPU mold
The application of TPU (thermoplastic polyurethane) mold is widely used in various industries due to its exceptional properties such as high durability, flexibility, and resistance to abrasion. It is a material that can be easily molded into any shape or design, making it a preferred choice for manufacturing various products.
Automotive Industry
TPU molds are well known for their versatility in the automotive industry. One of the reasons for the popularity of molds made of this material is its resistance to oil, grease and wear, making it an excellent tool for making various parts such as cable insulation, seals and gaskets, as well as an ideal material for making interior parts and under-the-hood components.

Consumer Electronics
When it comes to protecting cell phones, tablets and other electronic devices, cases have become a popular item. This is where TPU molds come in handy. Thanks to its durability, flexibility and impact resistance, it has become a popular choice for cell phone case manufacturers. With the advent of TPU mold technology, manufacturers can produce custom cases for devices of all shapes and sizes.
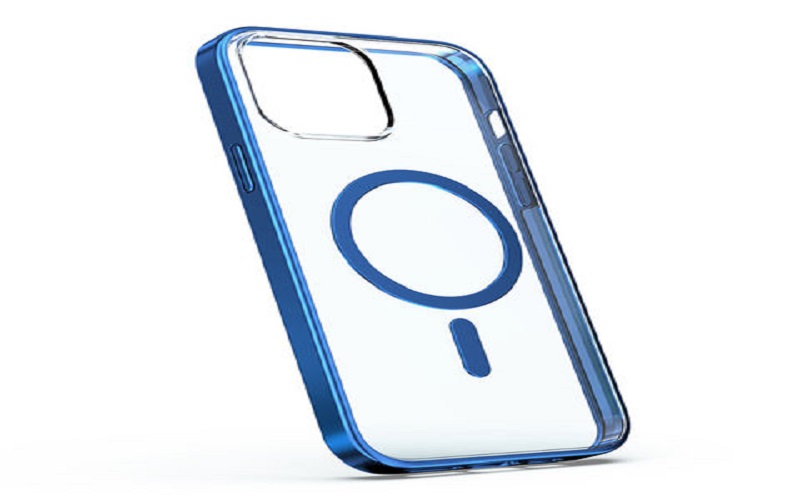
Medical Industry
In the rapidly evolving medical industry, there is always a need for high quality medical devices that are reliable, safe and durable. Due to its excellent biocompatibility, flexibility and chemical resistance, TPU mold is used for catheters, tubing and even medical wearable devices.
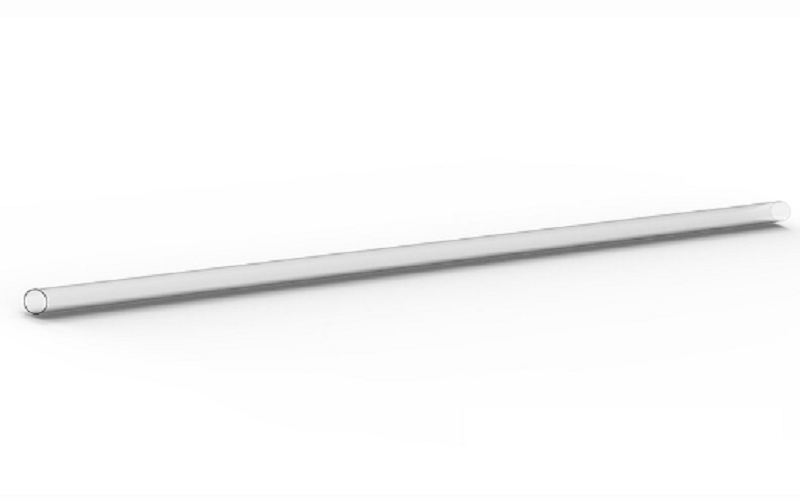
Aerospace Industry
Ideal for aerospace applications, TPU molds stand out for their lightweight properties, high performance capabilities at extreme temperatures, and resistance to oils and chemicals. Given these benefits, TPU mold can be used to manufacture a variety of parts such as seals, gaskets, insulation, fuel lines and other components for aerospace applications.
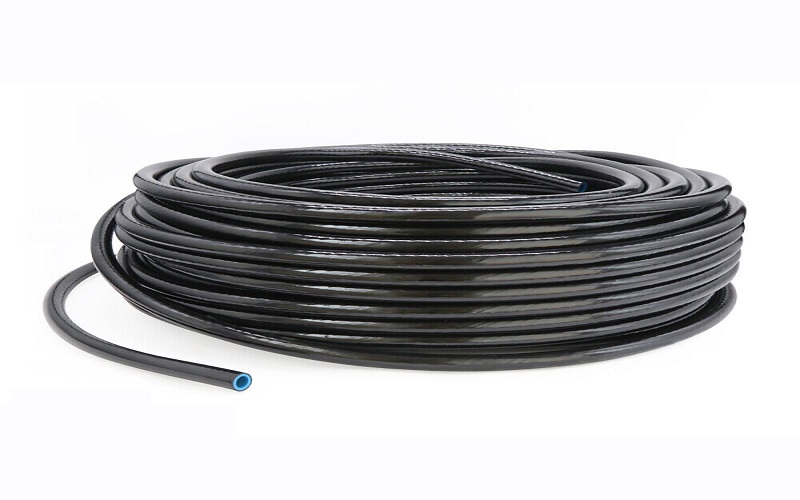
The benefits of using TPU mold
In the manufacturing field, the use of tpu mold has become the first choice for many companies.TPU moulds are known for their high resistance to abrasion, oil, and chemicals, making them suitable for manufacturing products that require long-lasting durability.
TPU mould can be engineered to have different levels of hardness, flexibility, and rigidity depending on the application and industry requirements.
One of TPU’s standout features is its exceptional durability, with high abrasion resistance, toughness, and strength. It’s no wonder that end products made with TPU can withstand a lot of wear and tear, making it perfect for those high-use items.
TPU is also resistant to many different chemicals, including oils and greases. This makes it ideal for products that are exposed to harsh environments or need to resist certain substances.
In addition, the TPU mold is weather resistant and thermally stable. This means that it can withstand harsh environmental conditions and a wide temperature range, making it an excellent choice for outdoor applications that need to withstand high temperatures or cold environments.
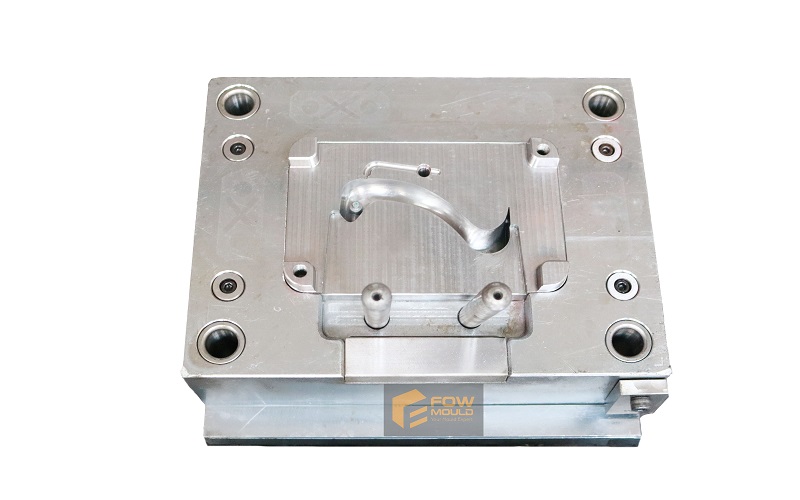
How to choose TPU mold supplier
First, the supplier should have experience in producing TPU molds for your project or application. Different types of TPU may require different molding techniques, and you want to make sure your supplier understands the complexities of this material. It is also important to evaluate the supplier’s production capabilities and lead times to ensure they can meet your production needs.
In addition, consider the supplier’s reputation for quality and customer service. Reading customer reviews or looking for references may be helpful in this regard.
FOW Mold offers professional mold design, plastic product design and mold manufacturing services using TPU parts. Our expertise also includes the production of accurate prototypes with 3D printers and high resolution machines. You can contact us for more professional assistance.
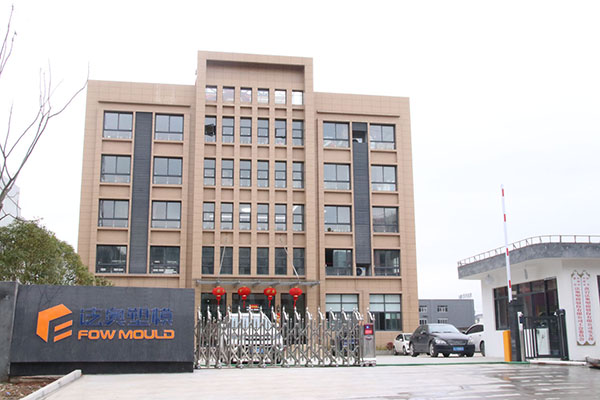