Thermoplastic Elastomer (TPE), as a novel material combining the elasticity of rubber with the processing convenience of plastic, is increasingly becoming an indispensable part of modern industry and daily life.
Its unique properties unlock boundless possibilities in fields such as automotive, medical, and consumer goods.
TPE not only aligns with sustainable development trends through its eco-friendly and recyclable characteristics but also pushes the boundaries of materials science with its exceptional adaptability and multifunctionality.
This article will delve into the properties, classifications, and wide-ranging applications of TPE ,revealing how this material paves the way for future innovation.
What Is Thermoplastic Elastomer (TPE)?
The molecular structure characteristics of thermoplastic elastomers are defined by their composition, which includes different resin segments and silicone rubber segments connected by chemical bonds.
The resin segments form physical cross-linking points through intermolecular forces, while the rubber segments consist of highly elastic chains that contribute to the material’s elasticity.
The physical cross-linking of the plastic segments changes reversibly with temperature, showcasing the plastic processing characteristics of thermoplastic elastomers.
As a result, thermoplastic elastomers possess the physical and mechanical properties of vulcanized rubber and the processing capabilities of thermoplastic plastics. They are a new type of polymer material that bridges the gap between rubber and resin, often referred to as the third generation of rubber.
The journey of TPE began in 1958 when Bayer first synthesized thermoplastic polyurethane (TPU) material, followed by the advent of styrenic block copolymers (SBCs) in 1963, which marked a significant milestone in the development and application of thermoplastic polyamide elastomers.
Due to their remarkable properties, TPEs have found widespread use in various industries. They are employed in making everyday products like shoes and hoses, and industrial items such as seals and gaskets.
Additionally, TPEs can modify other plastics like polyvinyl chloride, PE, and PP, enhancing their performance and broadening their application scope. This versatility has led to the rapid growth and diversification of TPEs in modern manufacturing.
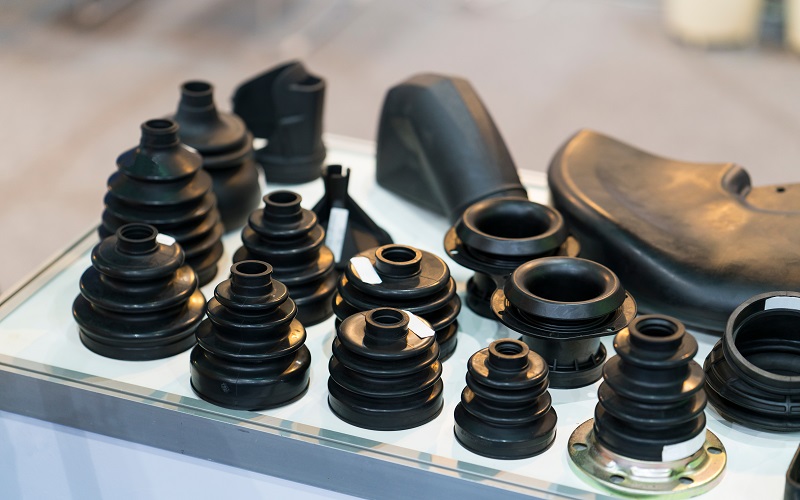
Types of TPE
Thermoplastic elastomers encompass a wide array of materials, each with unique properties and applications.
The most common types include styrenic thermoplastic elastomers, styrenic block copolymers (SBCs), polyolefin blends (TPOs and TPVs), thermoplastic polyurethanes (TPUs), thermoplastic copolyester, tpes thermoplastic elastomers, elastomeric alloys, and customised polymers.
These raw materials are integral to various sectors due to their essential characteristics, which we will explore in detail within the field of material science, highlighting any material difference.
Thermoplastic Styrenic Block Copolymers
Styrenic block copolymers, also known as SBCs or TPS, are one of the earliest and most researched types of block copolymer styrene block copolymers.
They are copolymers of butadiene or isoprene with styrene and closely resemble SBR rubber in performance. Common SBC variants include SBS, SIS, SEBS, and SEPS, each offering excellent elasticity, abrasion resistance, and weatherability.
These properties make SBCs ideal for applications in footwear, wire and cable applications, toys, and automotive components, thanks to their good electrical insulation properties.
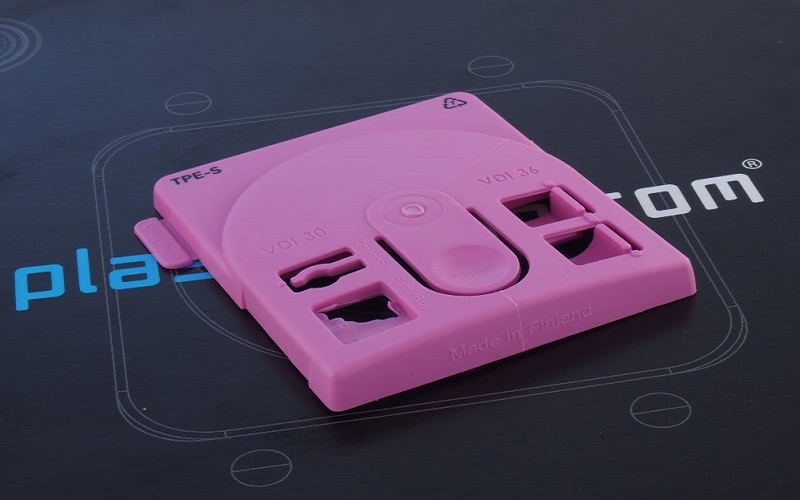
Thermoplastic Polyolefin Elastomers (TPE-O or TPO)
TPO materials, often referred to as thermoplastic olefins, are thermoplastic elastomers that consist of polypropylene as the hard segment and EPDM rubber as the soft segment.
TPOs are lightweight, with a specific gravity of around 0.88, and can withstand temperatures up to 100°C. They also exhibit excellent weather and ozone resistance, making them suitable for automotive seals, waterproofing materials, and cable insulation.
Through dynamic vulcanization, TPO can be transformed into TPV materials, enhancing its mechanical properties and extending it applicable to a broad range of fields
Thermoplastic Polyurethane
Thermoplastic polyurethane (TPU) is formed by reacting isocyanates with polyols, producing a material with exceptional mechanical strength, abrasion resistance, and flexibility. TPU materials are particularly valued for their superior wear resistance and oil resistance, which makes them ideal for footwear, medical fabrics, and military equipment.
However, TPUs have limitations such as lower heat resistance and susceptibility to yellowing upon exposure to UV light.
Thermoplastic Polyester Elastomers
Thermoplastic Polyester Elastomers (TPE-E), also known as Thermoplastic Copolyesters (TPC), are a class of block linear copolymers renowned for their exceptional balance of strength, flexibility, and thermal stability.
The combination of these segments results in a versatile material that excels in applications requiring durability and elasticity, such as automotive parts, industrial belts, and flexible hoses.
Key Properties Of Thermoplastic Elastomers
Thermoplastic Elastomers (TPEs) are valued for their unique combination of characteristics that bridge the gap between rubber and plastic. Below is a detailed overview of their key material properties:
Elastic Properties
One of the standout features of TPE materials is their remarkable elasticity, which exemplifies their typical elastic properties. TPEs can stretch to twice their original length and return to their desired shape, showcasing their high elasticity and resilience.
This property is particularly beneficial in applications requiring durability and flexibility, such as seals, gaskets, and flexible joints, due to their high elastic properties, elastomeric properties, rubber like properties, flexible polymer compounding, natural rubber, and flexible pvc.
Chemical Resistance
The chemical resistance of TPE compounds varies depending on their formulation, making some types more suitable for harsh environments than others.
For example, thermoplastic polyolefins (TPOs) are known for their excellent chemical resistance, while the inclusion of thermoplastic polyamides in TPE-A enhances oil resistance and mechanical strength.
This material stability allows TPE-s to be tailored for specific uses in chemically aggressive settings.
Temperature Resistance
Different types of TPEs exhibit varying levels of high temperature resistance, a critical factor for their use in automotive and industrial applications.
Many TPEs can withstand temperature extremes, from -30°C to +150°C, ensuring their performance in demanding environments.
This makes TPEs a reliable choice for applications requiring consistent performance across a wide temperature range.
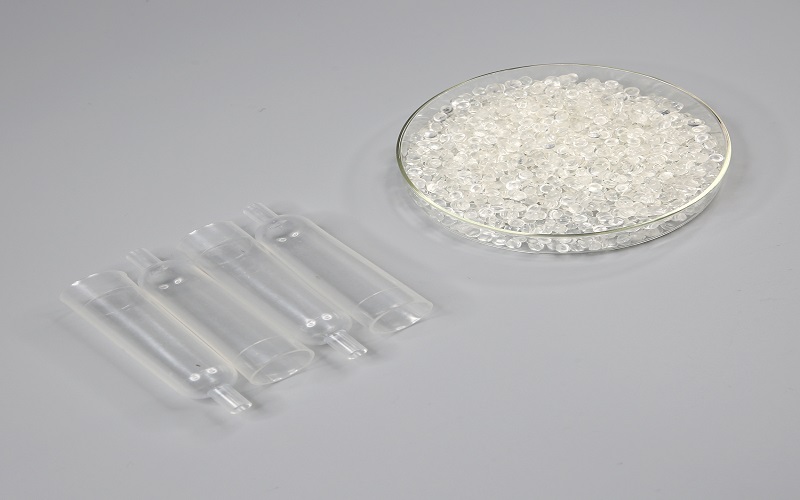
TPE Processing Methods
Thermoplastic Elastomers seamlessly blend the resilient mechanical properties of vulcanized rubber with the streamlined processing benefits of thermoplastics, offering significant advantages in manufacturing.
Unlike thermoset rubbers, which require time-intensive vulcanization, TPE s eliminate this step, simplifying production, reducing cycle times, and lowering costs.
Additionally, advanced variants like Thermoplastic Vulcanizates (TPVs) deliver enhanced performance, combining superior elasticity and durability for demanding applications.
Injection Molding
Injection molding is a processing method of tpe , prized for its precision and efficiency. During injection molding, TPEs behave as other thermoplastics in hot runners without major problems
This method enables the creation of intricate, high-quality parts with smooth finishes, making it ideal for diverse applications such as automotive components, medical devices, and consumer goods.
The versatility of TPE injection molding supports complex geometries and overmolding, ensuring both functional performance and aesthetic appeal.
Extrusion
Extrusion is another key technique for TPEs, where molten material is shaped into continuous profiles through a die.
This process excels in producing complex, uniform shapes like cable sheathing, seals, and tubing, often co-extruded with other materials for enhanced functionality.
TPE extrusion’s adaptability makes it a go-to choice for applications requiring consistent, high-performance profiles in industries ranging from construction to electronics.
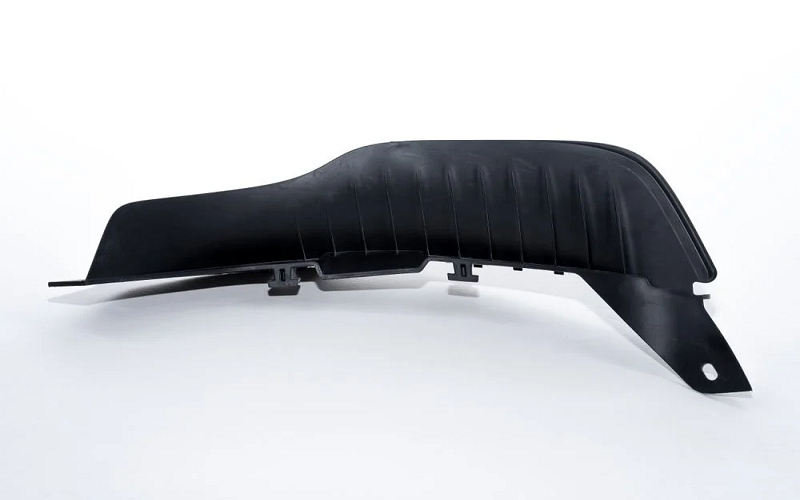
Applications of TPE Products
The versatile nature of thermoplastic elastomers allows them to meet the needs of various industries, including automotive, medical, consumer products, and sporting goods. Their dual properties of rubber and plastics make TPEs indispensable in modern manufacturing.
Automotive Sector
In the automotive sector, TPE s are used for components such as airbag covers and constant velocity joint boots. Their lightweight nature contributes to fuel efficiency, making vehicles more economical and environmentally friendly.
Medical Devices
Medical grade tpes play a crucial role in healthcare applications due to their unique properties. They resist degradation from various fluids, ensuring durability in medical devices such as tubing and medical oxygen masks. TPEs meet rigorous safety standards, making them suitable for critical healthcare applications.
Consumer Products
TPEs are widely used in consumer products to enhance comfort and functionality. From ergonomic grips for tools to flexible and lightweight shoe soles, TPE s improve the user experience in everyday items.
Sporting Goods
In the realm of sporting goods, TPEs are prized for their elasticity, abrasion resistance, and non-slip properties. They are used in products such as resistance bands, yoga mats, ergonomic bike grips, and golf club grips, enhancing performance and durability.
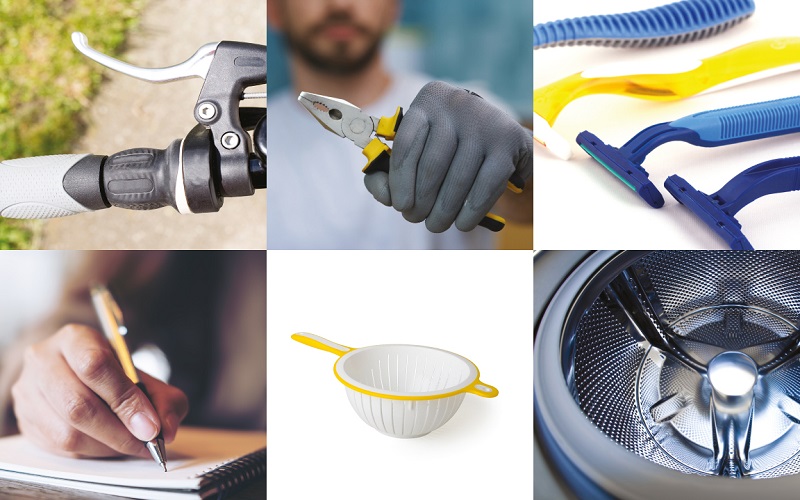
Advantage Of TPE
The advantages of thermoplastic elastomers are numerous, making them a preferred choice in various industries. Their superior processing capabilities, exceptional elasticity, and environmental benefits make TPEs stand out.
Outstanding Elasticity And Flexibility
TPEs exhibit high elastic recovery, combining the elasticity of rubber with the processability of plastics. They maintain flexibility even in low-temperature environments, making them suitable for automotive interiors and sports equipment that require weather resistance, particularly when using a tpe blend.
Processing Advantages
TPEs do not require vulcanization, allowing for direct molding through injection molding, extrusion, and blow molding processes.
TPEs can be easily colored, textured, or blended with additives to achieve specific aesthetic or functional properties.
Additionally, TPE production consumes over 25% less energy than traditional rubber, making it both time and cost-efficient.
Environmental Benefits
TPEs are non-toxic and free from harmful additives like plasticizers and heavy metals, complying with EU ROHS, REACH, and FDA food contact standards. They are suitable for medical tubing and taste free sealing solutions for children’s toys.
Moreover, TPEs support closed-loop recycling and some bio-based TPEs are biodegradable, reducing environmental impact.
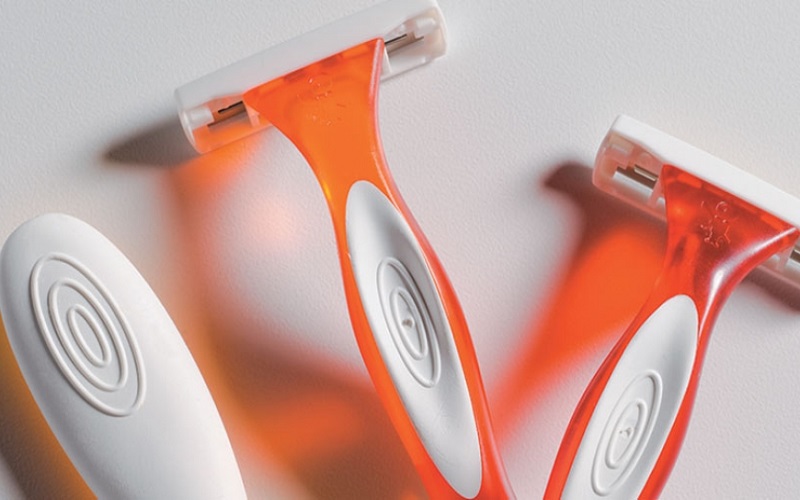
What Are The Disadvantages Of TPE?
Despite their many advantages, TPEs have some limitations:
Limited High-Temperature Performance
TPEs typically soften or lose elasticity at elevated temperatures, with most standard grades functioning optimally below 120°C. This restricts their use in high-heat environments, such as under-hood automotive components or industrial settings, where thermoset rubbers or high-performance plastics may be preferred.
Specialized TPE grades with enhanced heat resistance exist but often come at a higher cost, reducing cost-effectiveness.
Susceptibility to Creep
Under prolonged mechanical stress or load, TPEs may exhibit creep, a gradual deformation over time. This can compromise dimensional stability in applications requiring constant pressure, such as seals or gaskets, necessitating careful design and material selection to minimize this effect.
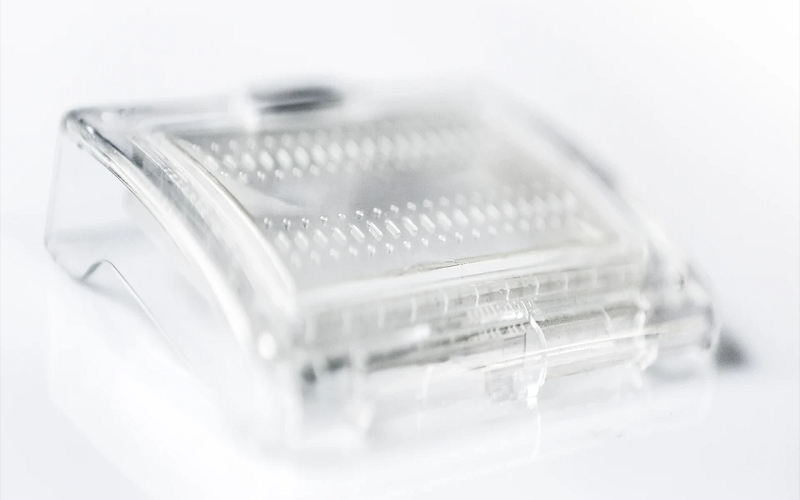
Is TPE A Safe Material?
Safety is a significant consideration when selecting materials for various applications, and TPEs excel in this regard when used within regulated conditions.
High-quality TPE materials are free from harmful substances like phthalates and bisphenol A (BPA), and they meet stringent standards such as FDA, LFGB, and EU regulations for food contact.
This makes them suitable for products like food packaging, medical devices such as gloves and catheters, and children’s toys.
Additionally, TPEs do not easily cause allergic reactions or irritations upon contact with skin, making them ideal for prolonged use in medical and consumer applications.
However, it is crucial to ensure the quality and sourcing of TPE materials. Inferior TPEs might contain excessive plasticizers or heavy metals, so it is essential to choose certified products from reputable brands.
While TPEs are generally safe, exposure to extreme conditions, such as high temperatures above 121°C, can lead to thermal degradation, releasing low molecular weight substances. Long-term exposure to organic solvents or UV radiation can also cause swelling or aging.
In summary, the answer to “Is TPE safe?” is a resounding yes for high-quality, certified TPEs used within their recommended conditions.
Their non-toxic, hypoallergenic nature and compliance with rigorous standards make them a trusted material for food, medical, and consumer applications.
However, careful selection and awareness of environmental limitations are crucial to maximizing their safety and performance.
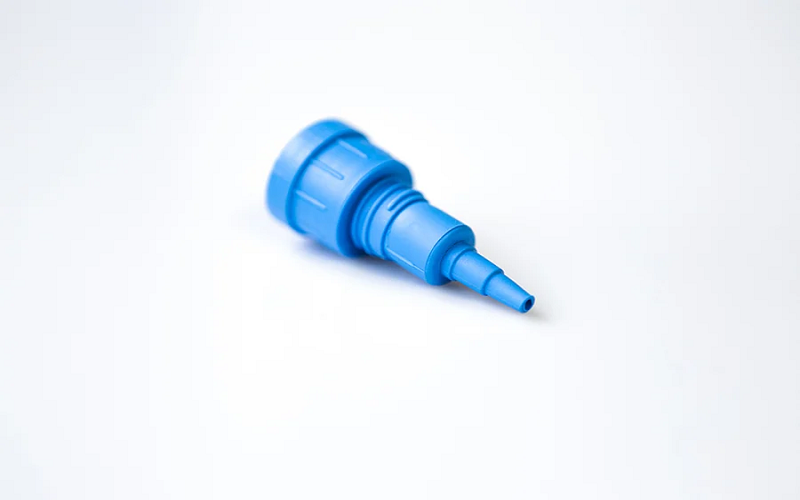
Summary
Thermoplastic elastomers have emerged as a revolutionary material, combining the best properties of rubber and plastics. They offer exceptional elasticity, chemical and temperature resistance, and are easy to process using standard plastic manufacturing techniques.
TPEs find applications in diverse fields, from automotive parts and medical devices to consumer products and sporting goods. Despite some limitations, such as lower heat resistance compared to traditional rubber, the advantages of TPEs in terms of versatility, processing efficiency, and environmental sustainability make them a superior choice for many applications.
As industries continue to innovate, TPEs are poised to play an increasingly vital role in the development of new and improved products.