With the growing demand for thinner plastic products, thin wall injection molding has become a core process in the manufacturing of lightweight plastic components.
However, mastering this technology is no easy task, as the reduction in injection molding wall thickness imposes specific requirements on structural design, material properties, mold configuration, and injection molding processes.
This article delves into the fundamentals of thin wall injection molding and presents practical strategies for leveraging this technology to efficiently and reliably produce high quality plastic parts.
What Is Thin Wall Injection Molding?
Thin wall injection molding is a specialized form of injection molding that enables manufacturers to create thinner and lighter parts without sacrificing structural integrity.
Its definition typically includes the following criteria:
Flow length-to-thickness ratio: The ratio of the flow length (L), measured from the point where the molten plastic enters the mold to the farthest point it must fill, to the average wall thickness (T) is generally required to be 100 or 150 or greater.
Wall thickness standard: The molded part has a wall thickness of less than 1 mm, with a projected area exceeding 50 square centimeters.
Proportional standard: The wall thickness of the molded part is less than 1 mm (or 1.5 mm), or the thickness (t) to diameter (d) ratio is below 0.05, particularly for disc-shaped parts.
This injection process relies on an injection molding machine injecting molten plastic at high injection speeds and pressure into a precisely designed mold.
Thin wall molding not only enables the production of lightweight plastic components but also typically allows for shorter production cycles, significantly improving manufacturing efficiency.
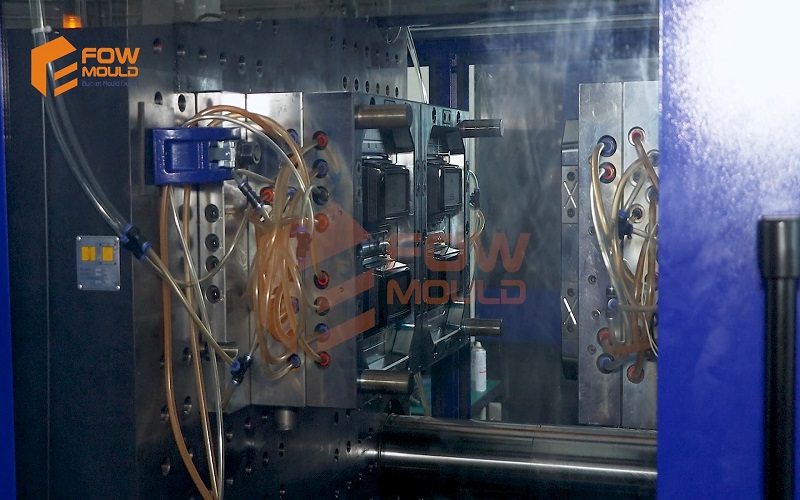
Typical Application Of Thin Wall Plastic Parts
Thin-wall injection molding technology is widely utilized across multiple industries due to its ability to produce lightweight, precise, and cost-effective components.
Key applications include:
Food Packaging: This technology is ideal for creating disposable tableware, beverage cups, lids, and yogurt containers, offering durability and convenience while meeting strict hygiene standards.
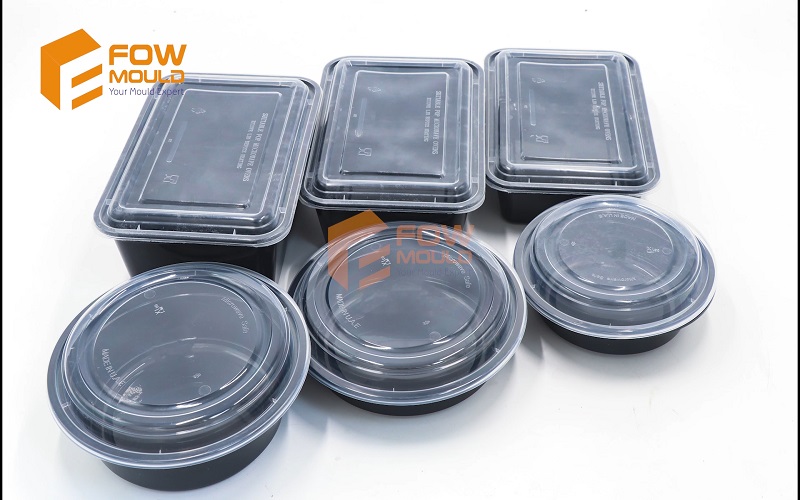
Medical Devices: It enables the production of precision items like medical syringes, test tubes, and petri dishes, where thin walls ensure functionality and material efficiency in sterile environments.
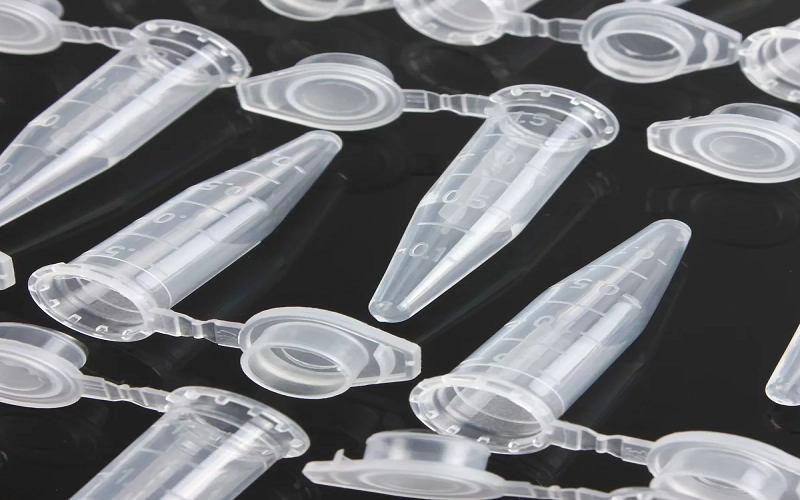
Electronics: Thin-wall molding is used to manufacture sleek, lightweight components such as mobile phone cases and wearable device parts, balancing aesthetics with structural integrity.
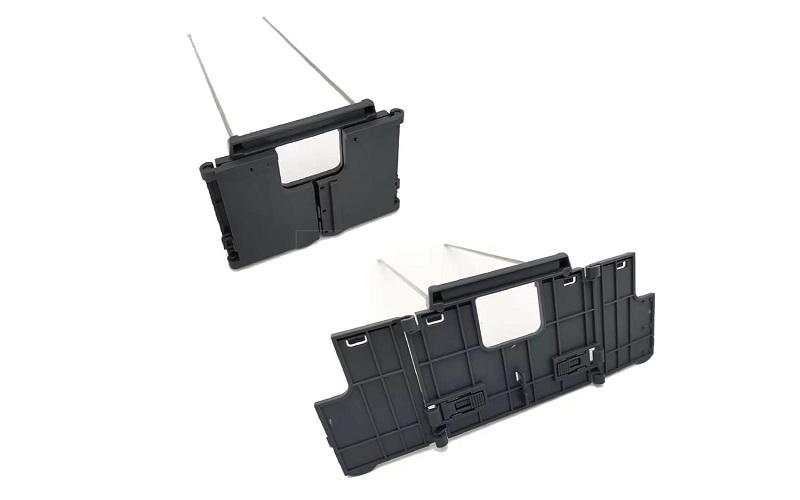
Automotive Manufacturing: The process supports the creation of body parts, interior trim, and other components, delivering strength and reduced weight to enhance vehicle efficiency and design.
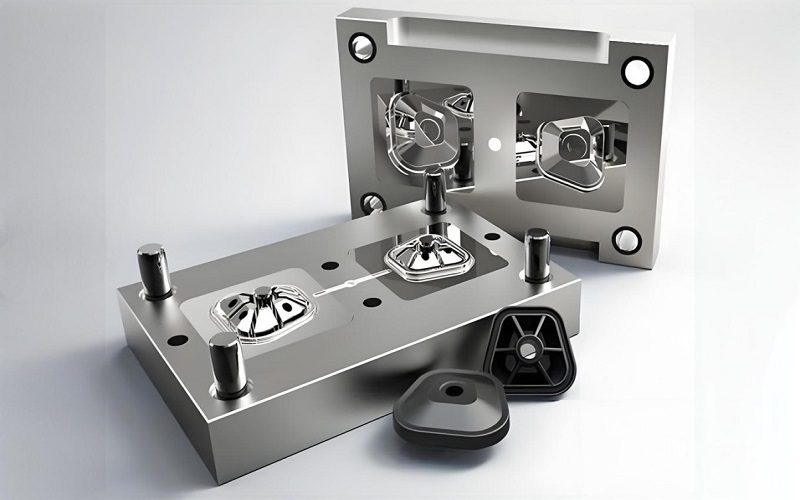
These applications highlight the versatility and efficiency of thin-wall plastic parts in meeting diverse industry demands.
Advantages of Thin Wall Injection Molding
The advantages of thin wall injection molding include the following:
Material Savings
Thin wall injection molded products are lighter and thinner, significantly reducing raw material costs.
Compared to traditional thick wall molding, the reduced weight of thin wall products leads to lower material consumption.
Shorter Molding Cycle Time
Thin wall injection molding requires less material to cool, reducing the injection volume by 10-40%, which shortens the material storage and injection time.
Additionally, thin walled parts cool more quickly, resulting in a significant reduction in cooling time.
Lightweighting
Thin wall injection molded products typically have wall thicknesses of 0.5mm or less, which results in significant weight reductions.
For example, reducing the wall thickness of automotive parts from 2.5-3.0mm to thinner wall thicknesses can reduce weight by 10-40%, thereby improving fuel efficiency.
By opting for thin wall molding over traditional injection molding, companies can save material, boost productivity, achieve a lower cost-per-part , and reduce shipping-related fuel usage and carbon emissions.
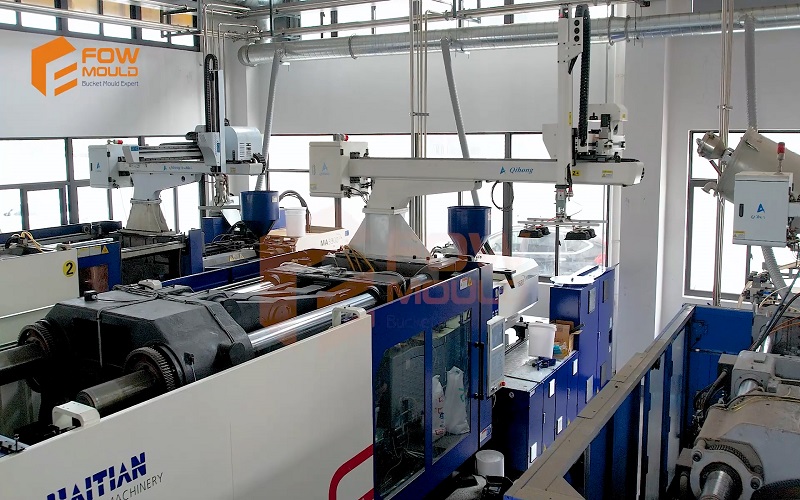
Common Issues And Solutions In Thin Wall Plastic Injection Molding Process
While thin wall plastic components offer numerous advantages, they also present significant challenges to manufacturability.
The reduced wall thickness often makes it difficult to produce these components using conventional injection molding methods.
When molding thin wall plastic parts, several common issues arise that require specialized solutions to overcome.
Issue | Cause | Solution |
Insufficient Filling | – Short injection time or insufficient pressure. – High flow resistance in thin-wall sections. | – Increase injection pressure and speed. – Optimize mold design (e.g., runner and gate size). – Use plastic materials with higher flowability |
Flash Formation | – Poor mold clamping force. – Misalignment of mold parting lines. – Excessive injection pressure. | – Ensure proper mold alignment and fit. – Adjust clamping force. – Reduce injection pressure if excessive. |
Warping | – Uneven wall thickness. – Uneven cooling. – High residual stress due to improper packing or cooling. | – Ensure uniform wall thickness. – Optimize cooling channel design. – Adjust packing pressure and cooling time. |
Bubbles | – Trapped air or impurities in the material. – Improper drying of materials. – Inadequate venting in the mold. | – Pre-dry materials to remove moisture. – Improve mold venting and design (e.g., add vent channels). – Use high-quality materials with minimal impurities. |
Shrinkage | – High shrinkage rate of materials. – Inconsistent cooling. – Large flat areas prone to shrinkage. | – Optimize material selection for low shrinkage. – Design cooling channels for uniform cooling. – Use packing pressure to compensate for shrinkage. |
Short Shots | – Mold cavity not completely filled before material solidifies. – Insufficient pressure or speed. – Thin walls increase cooling rate. | – Increase injection pressure and injection speed. – Use materials with better flowability. – Adjust mold temperature to delay cooling. |
How To Choose Materials For Thin Wall Molding?
When selecting materials for thin wall molding, the following key factors need to be considered:
1.Flowability: When injection molding thin-walled plastic parts, the fluidity of the plastic should be good, and its flow distance to thickness ratio (l/t) is greater than 150.
Plastic Resin Name | Density Range | Flowability |
PP | 1.0 | Excellent |
PC | 1.7–2.0 | Poor |
ABS | 1.3–1.5 | Moderate |
PA6 | 1.2–1.4 | Moderate |
PS | 1.0 | Excellent |
PC/ABS Blend | 1.0 | Excellent |
POM | 1.2–1.4 | Moderate |
PMMA | 1.5–1.7 | Moderate |
PE | 1.0 | Excellent |
2.Impact Strength: The material’s Notched Izod value (ASTM D256A) should reach 640 J/m or higher to ensure the rigidity of the molded part.
3.Heat Deflection Temperature and Thermal Stability: The material should remain stable at temperatures ranging from 70°C to 95°C.
4.Low-Temperature Impact Rigidity: The material must maintain sufficient rigidity in low-temperature environments to prevent brittleness.
5.Dimensional Stability: The material should have good dimensional stability to ensure that the injection molded part does not experience significant size changes after molding.
Considering the requirements for impact performance, flowability, and heat resistance, materials commonly used for thin wall molding include polypropylene (PP), acrylonitrile-butadiene-styrene (ABS), PC/ABS blends, and nylon.
Design Tips Of Thin Wall Injection Molding
When designing for thin wall injection molding, the key lies in optimizing the geometry of the part and the thin wall mold structure to meet the demands of high-speed and pressure
First and foremost, maintaining consistent wall thickness is critical.This ensures uniform material flow and helps prevent defects like warping and shrinkage.
Next, a well-designed gating system, such as a side gate or hot runner system, can enhance filling efficiency while minimizing pressure loss—think of it as the fast lane for your molten plastic!
The cooling system must also be evenly distributed to maintain consistent mold temperatures across all sections, reducing thermal stress and improving the final product’s quality.
Meanwhile, increasing the density of venting channels ensures effective air removal, keeping those pesky bubbles at bay.
Finally, to address the challenges of demolding thin walled parts (which can cling to molds like a kid to their favorite toy), you can employ pneumatic-assisted ejection or floating core designs.
These methods help minimize deformation and ensure a smooth release.
By implementing these thoughtful design optimizations, you can significantly boost the efficiency and quality of thin wall molding—because every great product starts with a great mold!
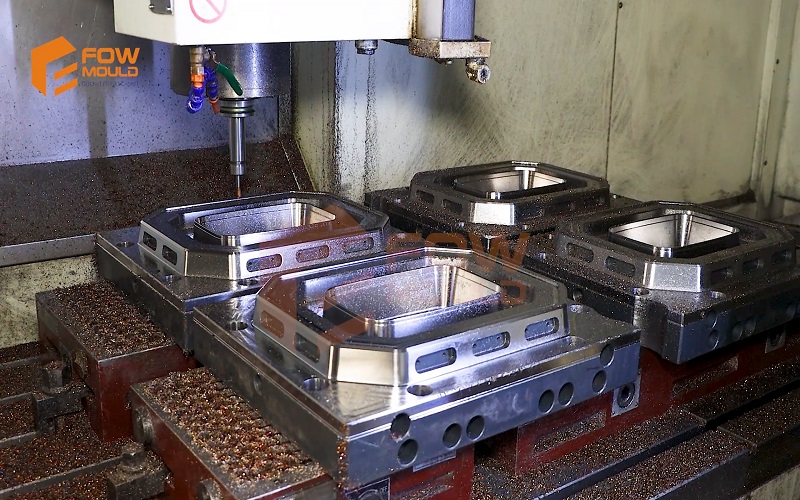
Custom Thin Wall Plastic Injection Manufacturing By FOWMOULD
As a leading thin wall injection molding company in China, FOWMOULD demonstrates exceptional expertise in thin wall mold design and thin wall plastic product manufacturing.
The company is committed to providing high-quality, efficient thin wall injection molding solutions for global customers, offering end-to-end services that encompass everything from mold manufacturing to mass production.
FOWMOULD produces a wide range of thin wall products, including thin wall containers, plastic buckets, and food packaging boxes, catering to the diverse needs of the food, household, and industrial sectors.
Whether it’s lightweight, high-precision plastic products or complex thin wall components requiring specialized designs, FOWMOULD delivers customized solutions to meet the unique requirements of its clients.
Conclusion
In conclusion, thin wall molding offers unique advantages over traditional plastic injection molding, including shorter production cycles and significant material savings.
For industries seeking sustainable and high-performance plastic solutions, this process remains the optimal choice for creating thin wall plastic parts.