Thermoplastics injection molding is a versatile process where heated thermoplastic polymers are injected into a mold to create plastic parts.
This method is highly efficient, reducing waste and allows for the production of durable and recyclable components.
In this article, we explore the fundamentals, advantages, and common materials used in thermoplastics injection molding, providing you with essential insights into this key manufacturing technique.
What Is Thermoplastics Injection Molding?
Thermoplastic injection molding is a versatile manufacturing process designed to produce complex designs with high precision and efficiency. Unlike other molding techniques, it excels in its adaptability to various materials and its ability to create intricate parts with minimal waste.
This thermoplastic injection molding technique involves melting thermoplastic polymers, which are plastics that can be reheated and reshaped multiple times, making them highly recyclable and versatile. Plastic injection molding is an essential technique in this field.
An injection molding machine is composed of several key components that work in harmony to ensure accurate and efficient production. These include the injection unit, where raw plastic pellets are melted into molten plastic, and the clamping unit, which holds the mold halves together during the injection process. The mold itself, often made from high-quality steel or aluminum, defines the shape and details of the final product.
The adaptability and precision of thermoplastic molding make it a preferred choice in various industries. It allows for the production of high-quality, durable parts with complex geometries, which would be difficult or impossible to achieve with other molding methods.
This combination of versatility, precision, and efficiency is what sets thermoplastic injection molding apart from other manufacturing processes.
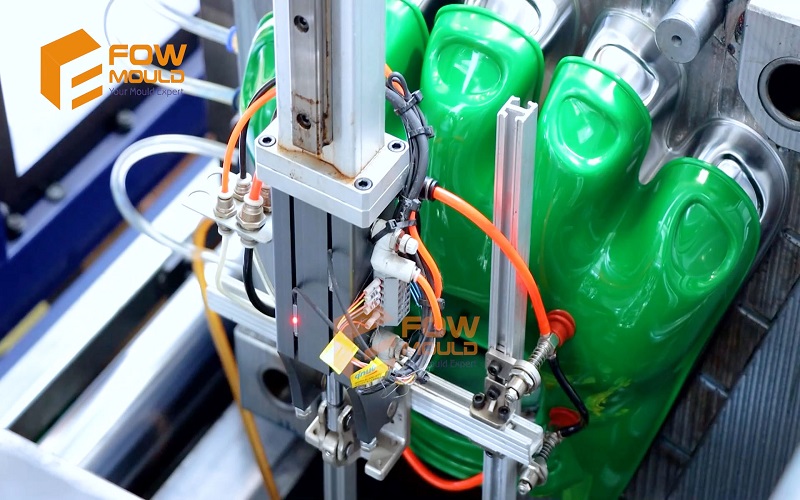
Why Use Thermoplastics in Injection Molding?
Thermoplastics offer several advantages that make them ideal for injection molding. One of the most significant benefits is their recyclability.
Unlike thermosetting plastics, thermoplastics can be reheated and reshaped multiple times without degrading, making them suitable for recycling and reducing waste.
This property not only makes thermoplastics environmentally friendly but also cost-effective, as scrap material can be reused in the production process.
The versatility of plastic materials is another key advantage. They can be customized with various additives to enhance their mechanical and aesthetic properties, allowing manufacturers to tailor the material to specific applications.
Whether you’re looking for high impact resistance, flexibility, or chemical resilience, there’s a thermoplastic material that fits the bill.
This versatility, combined with their efficiency in forming complex shapes and their suitability for mass production, makes thermoplastics a popular choice in the injection molding.
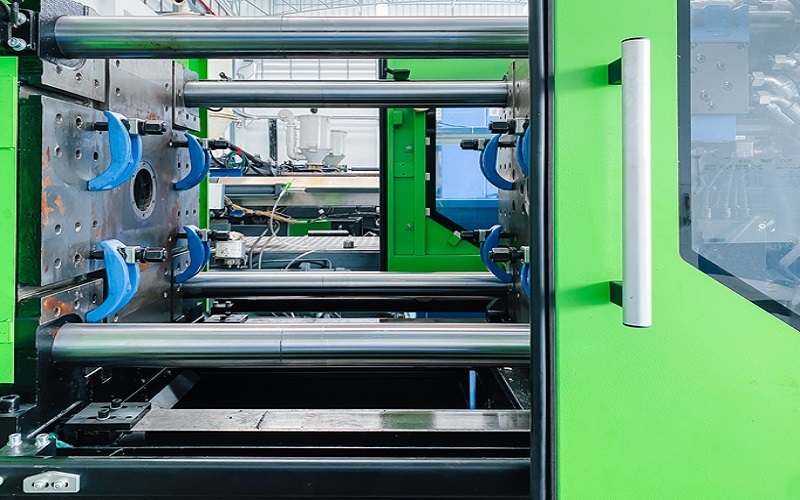
How Does Thermoplastic Injection Molding Work?
The thermoplasticsinjection molding process is a fascinating journey from raw plastic pellets to finished parts. This process involves several carefully controlled steps, each crucial for achieving the desired quality and precision.
It begins with heating the thermoplastic pellets until they become pliable, followed by injecting the molten plastic into a mold cavity under high pressure. Once the plastic has filled the mold, it is cooled and solidified before being ejected as a finished part.
Temperature control, injection speed, and monitoring systems are vital aspects that influence the precision and quality of the products. Specialized machines transform raw plastic pellets into molded parts, highlighting the importance of choosing the right machinery for the process.
Let’s delve deeper into each step, starting with the essential task of material selection.
Material Selection
Choosing the right thermoplastic material is a critical factor that significantly influences the performance and longevity of the molded parts.
The selection process involves considering various properties such as tensile strength, flexibility, impact resistance, and chemical resilience. These properties determine the functionality, aesthetics, and durability of the final product.
The versatility of thermoplastic materials allows them to be easily processed, requiring less energy and resulting in shorter production cycles.
This not only enhances efficiency but also reduces production costs. By carefully evaluating the specific requirements of the application, manufacturers can select the appropriate material that meets the desired shape and performance criteria.
Material Preparation
Material preparation is a crucial step in the injection molding process. Proper drying of raw plastic pellets is essential to prevent moisture-related issues during molding. Moisture in the pellets can lead to defects like splay marks and bubbles in the final product. Therefore, the pellets must be thoroughly dried before being loaded into the injection molding machine’s hopper.
Once dried, the pellets are ready for the next phase of the process. Ensuring that the plastic material is free from contaminants and properly prepared helps achieve consistent quality and reduces the likelihood of defects. This preparation step is vital for maintaining the integrity and performance of the molded parts.
Melting and Injection
The melting and injection phase is where the raw plastic pellets are transformed into molten plastic and injected into the mold cavity. During this stage, the pellets are heated in a barrel until they reach the desired viscosity.
Temperature control is critical to ensure that the plastic melts uniformly and flows smoothly into the mold. The injection unit pushes the molten plastic into the mold cavity. This process occurs under high pressure.
Proper screw speed and shot size are essential for achieving the correct melt quality and ensuring that the mold is filled completely. The clamping unit holds the mold halves together during injection, maintaining the shape and details of the final product.
Fast injection speeds are particularly important for thin-walled parts, as they ensure effective filling and minimize cycle time.
Hot runner systems and insulated runner molds help minimize material waste by reducing runner scrap during the molding cycle. These systems are especially effective for specific materials, improving efficiency and reducing production costs.
By carefully controlling the melting and injection parameters, manufacturers can achieve high-quality molded parts with consistent dimensions and surface finishe
Cooling and Ejection
After the molten plastic is injected into the mold, it undergoes the cooling phase, which is crucial for achieving the final part quality.
Efficient cooling is facilitated by a built-in coolant system that helps reduce cycle times and improve part quality. Cooling time varies based on the thickness of the part. It can take anywhere from a few seconds to several minutes, depending on the specific thermoplastic material employed.
Additional molten plastic is often injected into the mold. This helps to compensate for shrinkage that occurs during cooling.
After the plastic cools down adequately, the two halves of the mold are pulled apart. The completed part is then ejected from the mold. The ejection process uses an ejector bar and ejector pins to push the molded part out of the mold cavities.
Proper timing and sufficient force during the ejection phase are vital to maintaining the quality of the finished part. Factors such as ejection speed and force control help prevent distortion or damage to the molded component.
Mold design features, such as air vents and cooling channels, are essential for controlling the cooling process and preventing defects. By optimizing the cooling and ejection steps, manufacturers can ensure that the final product meets the desired specifications and quality standards.
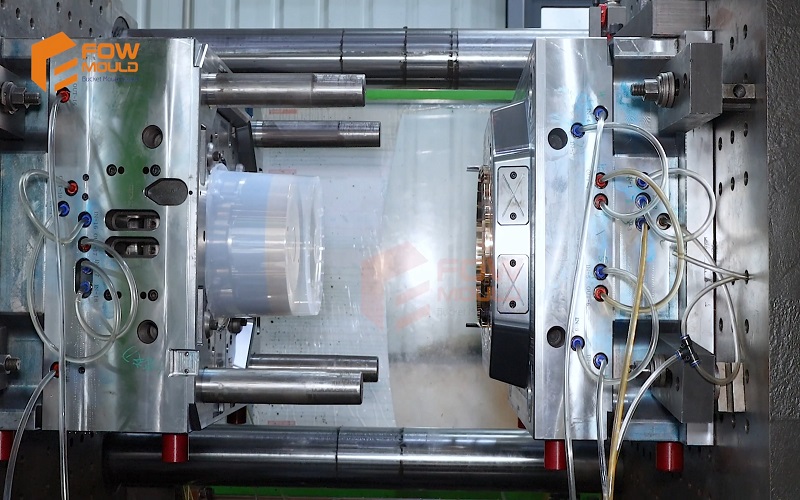
Key Parameters in Thermoplastics Injection Moulding
The success of the thermoplastics injection molding hinges on several key parameters. These parameters include:
Melt temperature
Mold temperature
Injection pressure
Injection speed
These factors play a crucial role in determining the quality and consistency of the final product. Each parameter must be carefully controlled and monitored to ensure optimal results.
Choosing the right injection mold and material is also essential for maintaining manufacturing costs and achieving high-quality components.
The cost of molds can vary significantly based on design complexity and production volume, making it important to select the appropriate mold for the specific application.
Let’s delve deeper into these key parameters, starting with the importance of melt temperature.
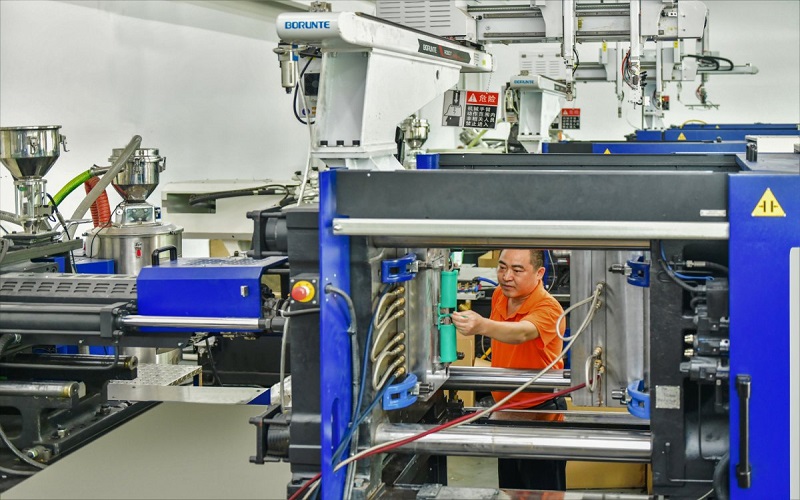
Melt Temperature
Maintaining the correct melt temperature is crucial for achieving a uniform melting process and preventing issues related to incomplete melting. During the melting stage, temperature control is essential to achieve the desired viscosity for effective molding. Excessive melt temperatures can cause material degradation, leading to surface defects on the molded parts.
Understanding the thermal properties of thermoplastics is essential for optimizing the melt temperature. Different thermoplastic materials have varying melting points and thermal behaviors, which must be considered when setting the melt temperature.
By maintaining the correct temperature, manufacturers can ensure that the molten plastic flows smoothly and fills the mold completely, resulting in high-quality parts with precise dimensions and finishes.
Mold Temperature
Mold temperature significantly affects the part’s crystallinity, shrinkage, and cycle time, impacting the overall quality of the molded component. Variations in mold temperature can lead to inconsistent product quality and defects, making it crucial to maintain consistent temperature control throughout the molding process.
Cooling time in injection molding is influenced by the thickness of the part and the specific thermoplastic material used. Proper temperature management ensures that the molded parts achieve the desired crystallinity and dimensional stability. By optimizing mold temperature, manufacturers can improve the quality and efficiency of the injection molding process.
Injection Pressure and Speed
Injection pressure and speed are essential for filling the mold completely and uniformly, impacting the quality of the final product. The typical range of injection pressure used in thermoplastics molding is between 500 to 1500 bar, which helps achieve detail replication and a high-quality surface finish.
The speed at which molten plastic is injected directly influences the filling pattern and density of the part. Proper control of injection pressure and speed ensures that the mold is filled efficiently, reducing the likelihood of defects and ensuring consistent quality.
By optimizing these parameters, manufacturers can achieve high-quality molded parts with precise dimensions and excellent surface finishes.
Common Thermoplastic Used in Injection Molding
Thermoplastic injection molding utilizes a wide range of materials, each with unique properties and advantages.
Common thermoplastic materials used in injection molding include Acrylonitrile Butadiene Styrene (ABS), Polycarbonate (PC), and High-Density Polyethylene (HDPE). These materials offer a combination of cost-effectiveness, durability, and versatility, making them suitable for various applications.
Amorphous thermoplastics, like ABS, typically have better formability and transparency, while semicrystalline types, like HDPE, offer good chemical resistance and mechanical properties. Understanding the characteristics of these materials helps injection molding manufacturers select the most appropriate thermoplastic for their specific needs.
Let’s explore the properties and applications of these common thermoplastic materials in more detail.
Acrylonitrile Butadiene Styrene (ABS)
Acrylonitrile Butadiene Styrene (ABS) is a thermoplastic polymer that is opaque and amorphous. It is recognized for its lightweight and flexible characteristics. It is a terpolymer composed of acrylonitrile, butadiene, and styrene, which gives it a unique combination of strength and moldability. ABS is easily moldable, making it suitable for a wide range of products, from automotive parts to children’s toys.
The impact resistance and toughness of ABS can be enhanced through modifications during the molding process. Molding ABS at higher temperatures enhances the gloss of the final product. Additionally, it increases heat resistance.
These qualities make ABS a popular choice in thermoplastic injection molding for producing durable and aesthetically pleasing parts.
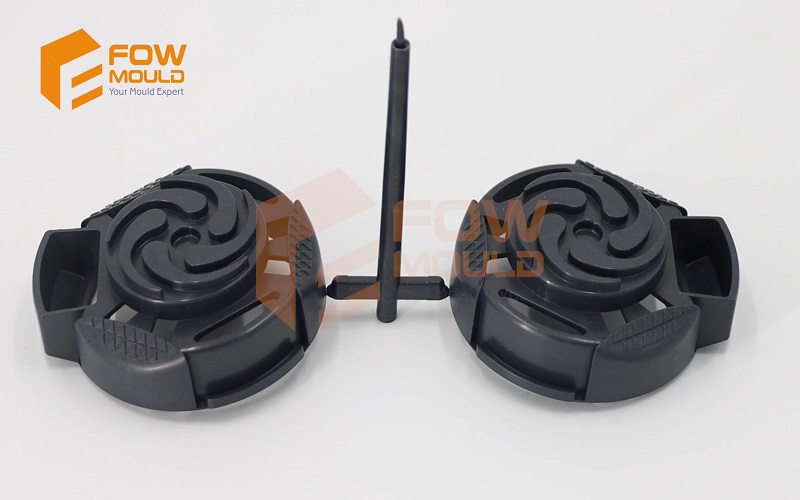
Polycarbonate (PC)
Polycarbonate (PC) stands out for its exceptional strength and flexibility, making it a preferred material in various industries.
Unlike many other thermoplastics, polycarbonate can undergo substantial plastic deformation without breaking, which is a testament to its durability. Its high transparency, allowing for up to 90% light transmission, makes it ideal for optical applications such as eyewear lenses and bulletproof glass.
PC’s high heat resistance, capable of withstanding temperatures ranging from -40°C to 120°C, contributes to its use in demanding environments. This combination of properties makes polycarbonate a excellent choice for applications requiring both strength and clarity, including automotive components, sports equipment, and electronic device housings.
High-Density Polyethylene (HDPE)
High-Density Polyethylene (HDPE) is classified as a thermoplastic polymer known for its high ductility and impact resistance, making it an economical choice for various applications. HDPE is widely used in the production of items like food packaging, plastic bottles, and piping due to its high chemical resistance and durability.
However, working with HDPE requires an experienced molder due to its complex shrink rate, which can pose challenges during the molding process. Despite these challenges, HDPE’s versatility and cost-effectiveness make it a valuable material in thermoplastic injection molding, particularly for products that need to withstand harsh chemical environments and physical impacts.
Applications of Thermoplastics Injection Molded Products
Thermoplastics injection molding finds applications across a wide range of industries, thanks to the versatile properties of thermoplastic materials.
In the automotive sector, thermoplastics are used to manufacture components like dashboards, bumpers, and interior trims, providing a balance of durability and lightweight performance.
The medical field relies on thermoplastics for producing items such as syringes, surgical tools, and even medical implants, owing to their precision and biocompatibility.
Consumer electronics benefit from thermoplastics molding in the production of device enclosures, connectors, and other intricate parts.
The packaging industry extensively uses thermoplastics for creating bottles, caps, and containers, leveraging their durability and ability to form complex shapes.
In construction, thermoplastics are essential for making pipe fittings, electrical components, and various structural elements. Household products like kitchen utensils, toys, and storage bins also commonly use thermoplastics, highlighting their widespread utility in everyday items.
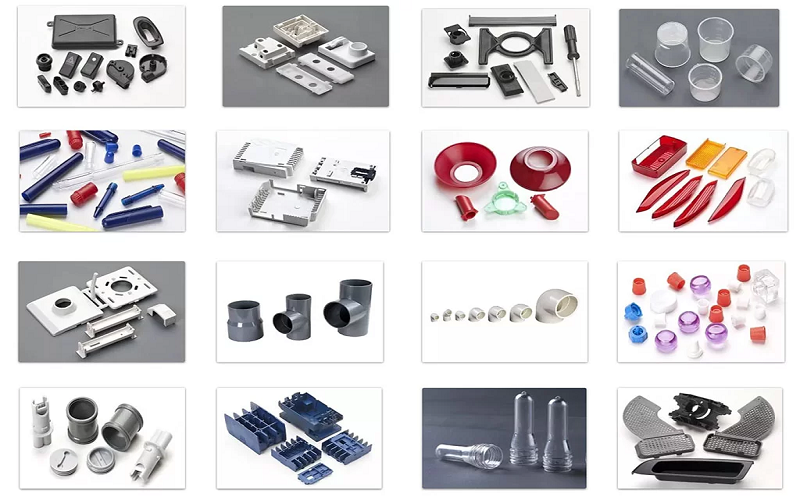
Troubleshooting Common Issues in Thermoplastics Molding
Thermoplastic injection molding, while highly efficient, can sometimes encounter issues that affect the quality of the final product.
Insufficient ventilation in the mold can lead to trapped air, causing defects such as voids and bubbles in the molded parts. Ensuring proper mold design and adequate ventilation helps mitigate these issues.
Low injection pressure or speed can result in incomplete filling of the mold, leading to defects like short shots and poor surface finish. Adjusting the injection pressure and speed to optimal levels ensures that the mold is filled completely and uniformly.
Moisture in the raw material is another common issue that can cause splay marks on the surface of the molded parts. Proper drying of plastic pellets before the thermoplastic molding process
is crucial to prevent moisture-related defects.
Improper cooling times can cause warpage and dimensional changes in the finished product. Ensuring consistent and adequate cooling times helps maintain the integrity and dimensional accuracy of the molded parts.
By identifying and addressing these common issues, manufacturers can improve the quality and consistency of their thermoplastic injection molded products.
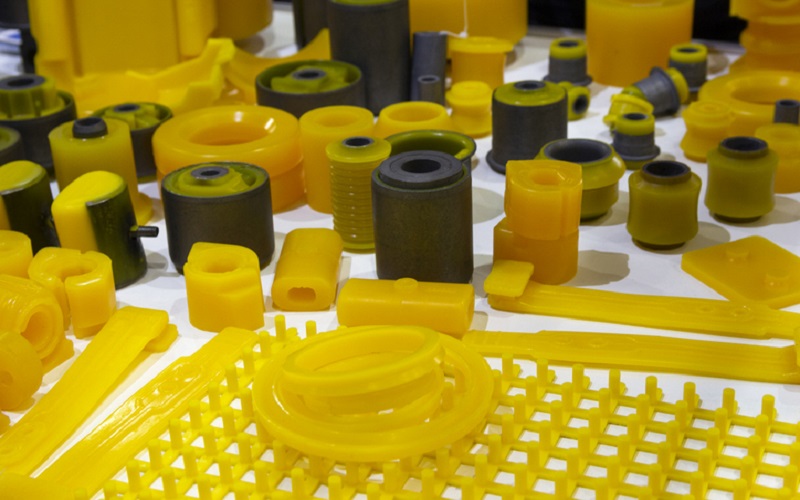
Comparing Thermoplastics with Thermosets
Thermoplastics and thermosets are two distinct classes of polymers, each with its own set of properties and applications. The key difference is found in the material properties. Additionally, the reversibility of their molding processes also sets them apart.
Thermoplastics can be reheated and reshaped multiple times, making them highly recyclable and versatile. This flexibility allows for easier processing and recycling, making thermoplastics a more environmentally friendly option compared to thermosets.
On the other hand, thermosetting plastics undergo a permanent chemical change when molded, making them more rigid and heat-resistant but non-recyclable. This makes thermosets suitable for applications requiring high heat resistance and structural integrity.
While both types of materials are used in injection molding, thermoplastics offer advantages such as flexibility, recyclability, and cost-effectiveness, making them a preferred choice for many applications.
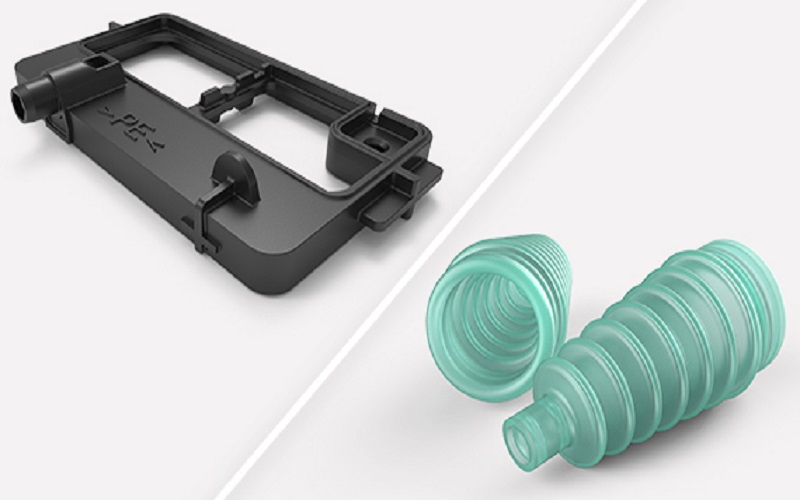
Cost Considerations in Thermoplastics Injection Molding
Cost considerations play a significant role in the selection and use of thermoplastics in injection molding. One of the primary factors influencing cost is the production volume. As production volumes increase, the per part cost decreases because the mold costs are spread over a larger number of items produced. This makes thermoplastic molding an economical choice for mass production.
Material costs for thermoplastics can range from $1 to $5 per kilogram, depending on the type and quality of the material selected. Using 3D printed molds can be a cost-effective solution for low-volume production, enabling quick iterations without the high costs of traditional tooling.
By carefully balancing material selection, production volume, and mold costs, manufacturers can optimize their production process to achieve cost-effective and high-quality results.
Choosing the Right Thermoplastic Material for Your Project
Selecting the appropriate thermoplastic material for your project involves considering several critical factors, including mechanical properties, heat resistance, and application suitability. Mechanical properties such as tensile strength, impact resistance, and flexibility are essential for ensuring that the final product meets the required performance standards.
Evaluating factors like food safety, heat tolerance, and UV resistance is crucial, especially for applications in the food packaging and outdoor industries. Data sheets provide valuable information on the properties and performance of different materials, helping manufacturers make informed decisions.
By assessing these factors and balancing toughness and pliability, manufacturers can select the right thermoplastic material that meets their specific project requirements.
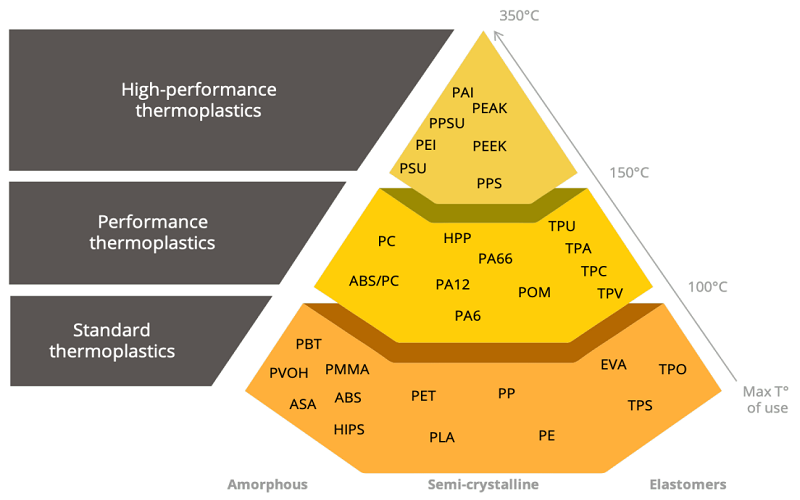
Summary
Thermoplastic injection molding stands out as a critical manufacturing process, valued for its versatility, efficiency, and ability to produce high-quality, precise components across various industries. Its key features—such as strong plasticity, cost-effectiveness, and recyclability—make it an ideal choice for applications ranging from automotive parts to medical devices.
To launch a successful thermoplastic injection molding project, partnering with a reliable and experienced manufacturer is essential.
FOWMOULD, a trusted leader in the field, provides comprehensive one-stop thermoplastic injection molding services, leveraging expertise in material selection, process optimization, and innovative solutions to ensure your project’s success. Contact FOWMOULD today to bring your manufacturing vision to life.
Frequently Asked Questions
What is thermoplastic injection molding?
Thermoplastic injection molding is a manufacturing process where thermoplastic materials are heated to a molten state, injected into a mold, and cooled to form precise parts or products. Thermoplastics can be repeatedly softened by heat and solidified by cooling, making them ideal for mass production.
What is the difference between thermoplastic injection molding and thermoset injection molding?
Thermoplastic injection molding uses reversible thermoplastic materials, allowing products to be recycled and reused. In contrast, thermoset injection molding employs irreversible thermoset plastics that cannot be remelted once cured, offering higher strength but are non-recyclable. The cost of thermoplastic processes is generally lower, and they offer more flexible applications.
What are some common applications of thermoplastic injection molding?
Thermoplastic injection molding is widely applied in industries such as automotive, medical devices, consumer electronics, packaging, and construction. Its versatility makes it essential for producing a diverse range of products efficiently.
What are the main advantages of this process?
Key advantages include strong plasticity (ability to create complex shapes), low processing costs, broad applicability, good chemical stability, and recyclability, making it popular in industries like automotive, appliances, and medical devices.
What are the limitations of thermoplastic injection molding?
Limitations include sensitivity to high temperatures (potential deformation), lower strength compared to metals or thermosets, complex and costly mold designs, and possible quality degradation during recycling.
How can the quality of injection molding be optimized?
Optimization involves selecting appropriate materials, precisely controlling process parameters (e.g., temperature, pressure, and cooling time), designing high-quality molds, and using simulation software to predict and address issues like shrinkage or warping.