Curious about the strongest plastics on the market? In this article, we break down the top options, exploring their strengths and best applications.
From industrial to consumer uses, find out which plastics perform best under extreme conditions. Some of these strong plastics are commonly found in various industrial and consumer applications.
What Makes a Plastic "Strong"?
When we talk about the “strongest” plastics, we’re not just referring to how tough they look or feel—strength in plastics is a precise science, defined by a combination of measurable properties that determine how well a material can perform under stress. These properties make certain plastics stand out as champions in demanding applications, from skyscraper components to spacecraft insulation. Let’s break down the key factors that define a plastic’s strength.
First, there’s tensile strength, which measures a plastic’s ability to resist breaking when pulled apart under tension.
Think of it as the maximum force a material can endure before it snaps—like a rope in a tug-of-war. Compressive strength is another critical factor, highlighting a material’s ability to withstand forces that compress or squeeze it, which is essential in applications involving high impacts.
Next up is impact resistance, the ability to absorb energy from sudden blows without cracking or shattering. This is what makes a plastic tough rather than just hard.
Imagine dropping a heavy tool on a plastic surface—materials with superior impact resistance won’t fracture, making them ideal for safety gear or protective casings.
Beyond tensile strength and impact resistance, heat and chemical resistance are critical. Some plastics can withstand blistering temperatures or corrosive substances without degrading, melting, or losing their structural integrity. This durability is critical for applications like engine parts or chemical storage containers, where exposure to extreme conditions is a daily reality. High resistance to biodegradation is crucial for applications in demanding fields such as aerospace, medical, and industrial uses.
Manufacturing processes can also supercharge a plastic’s strength. For example, reinforcing plastics with fibers—like carbon or glass—creates composite materials that combine the best of both worlds: the flexibility of plastic and the rigidity of the fibers.
This technique can dramatically boost tensile strength and impact resistance, turning an already strong plastic into a powerhouse.
Each of these properties—and the innovations that enhance them—sets the stage for our countdown of the top seven strongest plastics. Let’s meet these heavy hitters!
Polyamide-imide (PAI)
Polyamide-imide, commonly known as PAI, is a new engineering plastic renowned for its exceptional performance under extreme conditions. PAI boasts superior mechanical properties at 250°C and a heat distortion temperature of 269°C. It possesses an unmatched tensile strength of over 172 MPa, with a heat deformation temperature of 274°C under a 1.8 MPa load.
PAI’s strength lies in its unparalleled thermal stability and mechanical properties, allowing it to operate in environments where other plastics fail. It also exhibits excellent creep resistance, meaning it resists deformation under long-term loads.
However, PAI is expensive and challenging to process, requiring high-temperature molding equipment. Additionally, its impact resistance is relatively lower compared to materials like polycarbonate. Despite its impressive toughness and dimensional stability, PAI has limited hydrolysis resistance, which poses challenges for its use in wet environments.
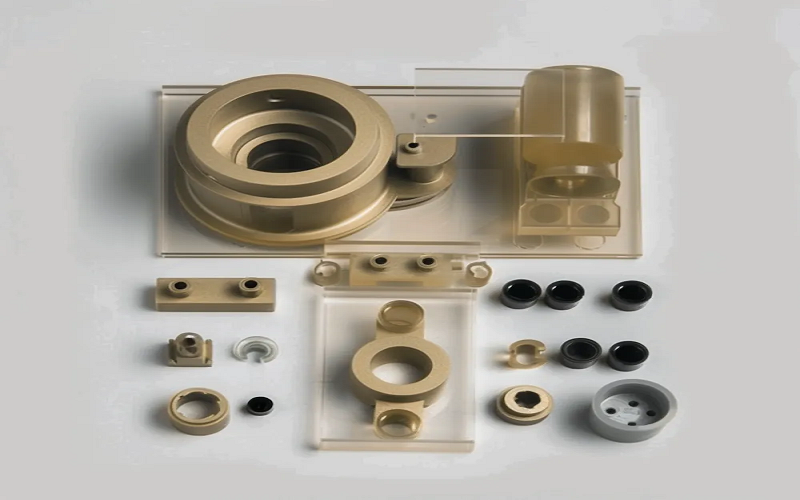
Polyphenylene Sulfide(PPS)
Polyphenylene sulfide, or PPS, is a high-performance thermoplastic resin widely used as a specialty engineering plastic. It offers excellent heat resistance, with a heat distortion temperature often exceeding 260°C, and can be used continuously in the 180-220°C range. PPS plastic also boasts impressive chemical resistance, second only to PTFE, making it ideal for harsh environments.
When reinforced with glass fibers, PPS’s performance is further enhanced. Its impact strength can increase from 27 J/m to 76 J/m, and its tensile strength can leap from 6 MPa to 137 MPa. These characteristics make PPS suitable for various functional films, coatings, and composite materials in electronics, aerospace, and automotive industries.
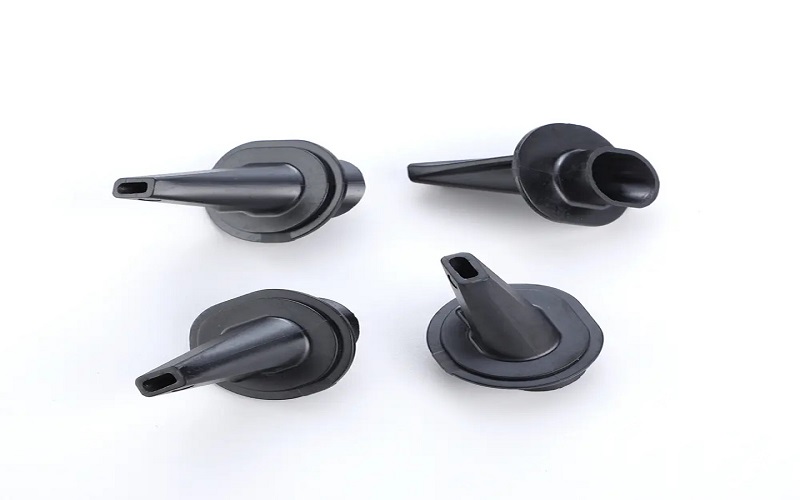
Polyether Ether Ketone (PEEK)
Polyetheretherketone, commonly known as PEEK, is a high-performance thermoplastic renowned for its exceptional combination of strength and resilience. It has a tensile strength of 14,000 psi, allowing it to endure significant mechanical stress without deforming or breaking. PEEK maintains structural integrity at temperatures up to 250°C and resists wear and fatigue, making it a top-tier choice for precision engineering.
PEEK also exhibits remarkable chemical resistance, standing up to harsh substances like acids, oils, and solvents that would degrade lesser materials. Due to its excellent mechanical properties, high-temperature resistance, and wear resistance, Injection Molded PEEK Parts commonly used in manufacturing compressor valve plates, piston rings, and seals.

Nylon
Nylon, also known as Polyamide (PA), is the world’s first synthetic fiber and an essential engineering plastic. Its tensile strength ranges from 8,000 to 12,000 psi, making it suitable for load-bearing applications. Nylon is widely used in textiles, automotive, electronics, packaging, and aerospace industries.
Nylon’s elasticity allows it to endure thousands of bends without breaking, and its wear resistance is the best among all textile fibers. However, it is unstable in strong acids or bases and has high moisture absorption. Despite these drawbacks, nylon is frequently used in 3D printing due to its excellent mechanical properties and wear resistance.
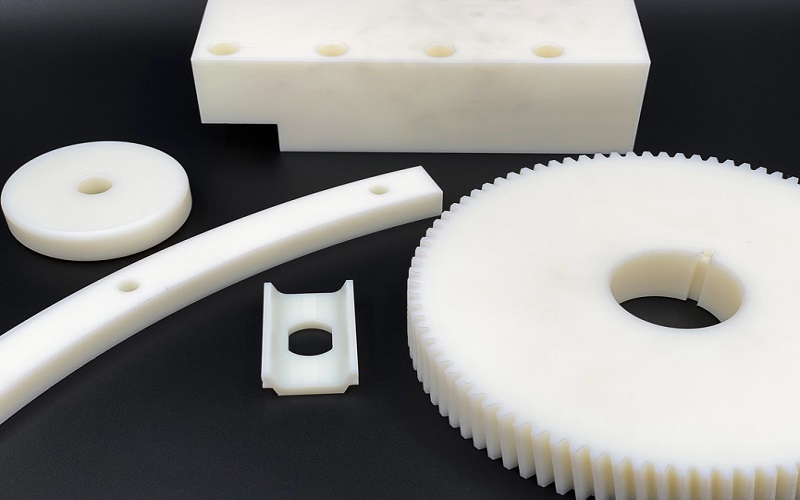
Ultem (PEI)
Ultem, or Polyetherimide (PEI), is a super-engineering plastic made from amorphous polyetherimide. It offers the best balance of properties, including high-temperature resistance, dimensional stability, chemical resistance, flame retardancy, electrical properties, high strength, and rigidity. PEI’s glass transition temperature is 215°C, and it can be used continuously at 160-180°C, with an intermittent maximum usage temperature of 200°C.
PEI has a wide range of chemical resistance, including resistance to most hydrocarbons, alcohols, and all halogenated solvents. It is considered cost-effective compared to other high-strength plastics, maintaining strong performance at a lower cost.
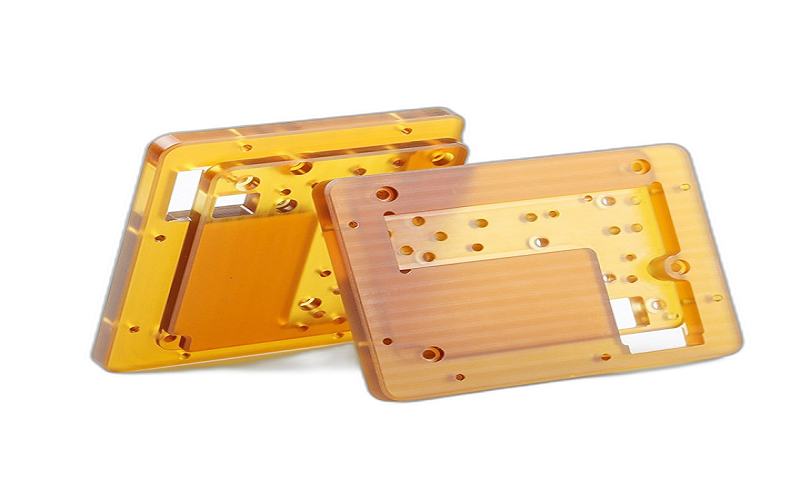
Acrylonitrile Butadiene Styrene (ABS)
Acrylonitrile butadiene styrene, or ABS, is a common thermoplastic made from the copolymerization of three monomers: acrylonitrile, butadiene, and styrene. It offers excellent mechanical and thermal properties, with an elastic modulus of 2.2 GPa and stability in the -40 to 100°C range. ABS is known for its outstanding impact resistance, even at low temperatures.
ABS plastic is widely used in consumer electronics, automotive interiors, and toys like LEGO bricks due to its high strength-to-weight ratio and ease of processing. However, ABS has limited heat resistance and softens at temperatures above 100°C, making it unsuitable for high-temperature environments.
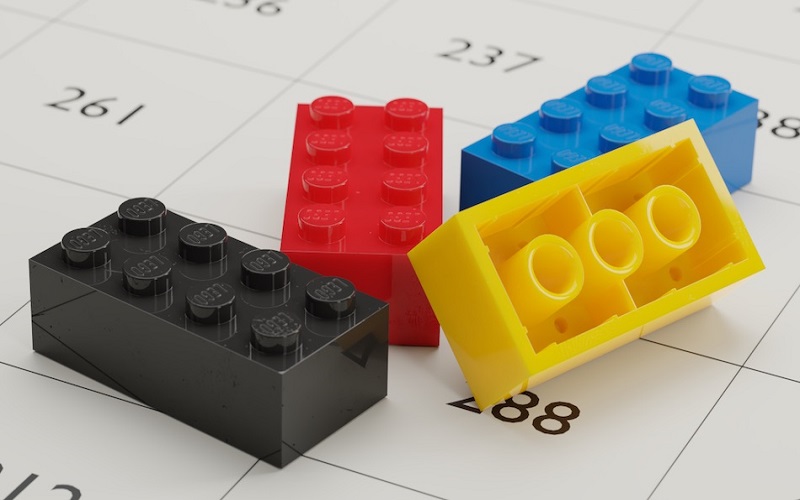
Polycarbonate(PC)
Polycarbonate (PC) is known for its excellent impact resistance, able to withstand intense forces without breaking or deforming. It also offers thermal and impact-related damage resistance, enhancing its durability. Polycarbonate can withstand high temperatures, making it suitable for applications that involve heat.
Common uses of polycarbonate include indoor and outdoor signs, helmets, protective goggles, face shields, and windows, due to both its durability and clarity. While polycarbonate offers many advantages, it is expensive and not very scratch-resistant, which are important limitations to consider.
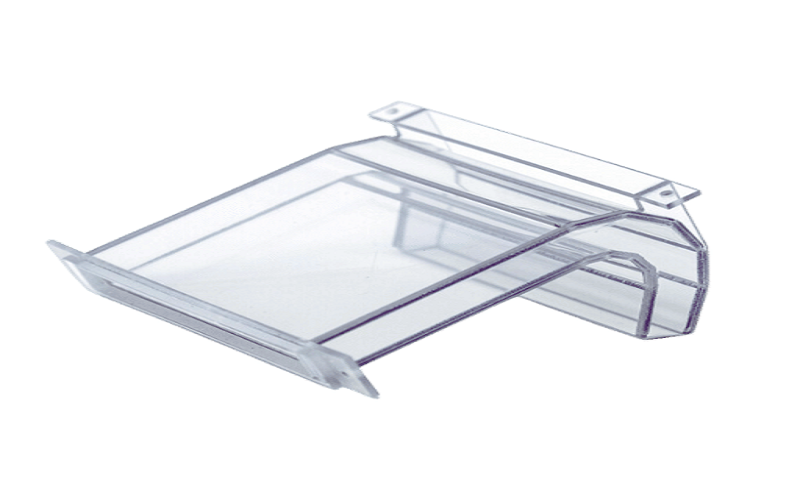
Applications of High-Strength Plastics
High-strength plastics have revolutionized industries by offering lightweight, durable, and versatile alternatives to traditional materials like metal and glass. Their unique properties—ranging from exceptional tensile strength to the highest strength against heat, chemicals, and wear—make them indispensable across a wide array of applications.
Aerospace and Aviation
In aerospace, every gram counts, and durability is non-negotiable. Polyamide-imide is used in the Boeing 787 Dreamliner’s turbine engine bearings, where its thermal stability (up to 275°C) ensures performance at high altitudes.
Polyetheretherketone features in Airbus A350 XWB’s structural brackets, leveraging its 14,000 psi tensile strength to reduce weight while maintaining rigidity in flight.
Automotive Engineering
Carmakers use high-strength plastics to enhance efficiency and durability. PPS is molded into Toyota Prius fuel pump housings, capitalizing on its 260°C heat resistance and reinforced impact strength (76 J/m with glass fibers).
Glass-reinforced nylon powers the intake manifold of Ford F-150 engines, cutting weight while enduring under-hood heat and vibration.
Construction and Infrastructure
High-strength plastics play a crucial role in construction as well. For example, high-density polyethylene (HDPE) rods are favored for their exceptional strength and hardness, which enable them to withstand significant pressure and impact, making them suitable for various high-strength applications.
Furthermore, HDPE rods boast excellent chemical resistance, capable of enduring the corrosive effects of numerous acids, bases, and salts, thereby extending their lifespan.
Medical Devices and Implants
The medical field demands materials that are both strong and safe for the human body. PEEK is a star here, used in Stryker’s Triathlon Knee System for knee replacements, where its biocompatibility and resistance to wear match the body’s needs.
It’s also found in spinal cages from Medtronic, supporting vertebrae with a lightweight alternative to titanium.
Consumer Products And Electrical Connectors
In everyday items and electronics, high-strength plastics replace wood and metal, offering durability and aesthetic appeal. Polycarbonate is the material behind Gorilla Glass Victus, used in Samsung Galaxy S23 screens, providing impact resistance for drop-prone smartphones.
ABS shapes LEGO bricks, with its 4,000–6,000 psi strength ensuring those iconic creations withstand enthusiastic play, while its processability allows vibrant colors.
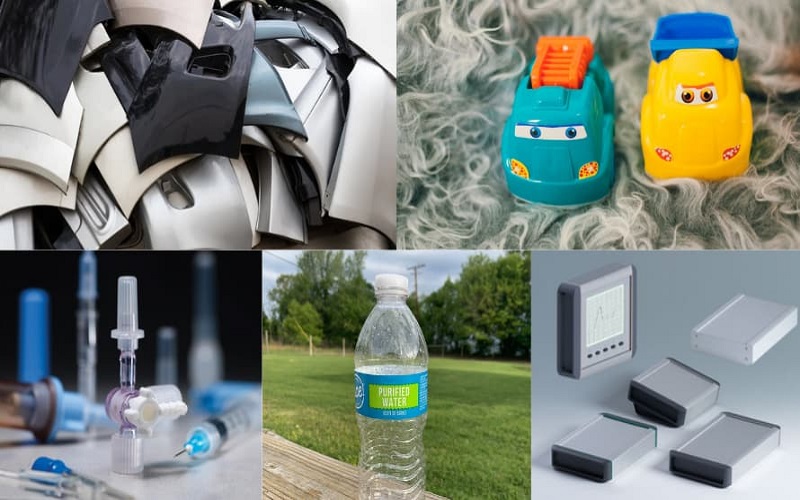
Future Trends in High-Strength Plastics
The future of high-strength plastics is moving towards sustainability, smart materials, and adaptability to extreme environments, bringing revolutionary changes to various industries.
For example, bio-based PEEK and nylon, made using renewable resources like castor oil, reduce the carbon footprint while maintaining excellent tensile strength and durability.
Incorporating nanocomposites, such as adding carbon nanotubes to PPS, can boost tensile strength from 137 MPa to over 200 MPa, making them highly suitable for high-performance electronic devices.
Advancements in 3D printing technology allow for the production of custom PEEK components, such as complex lightweight brackets that can withstand temperatures up to 250°C, promoting personalized manufacturing.
Self-healing PAI, which integrates microcapsules for automatic crack repair, extends the lifespan of gears and bearings. Additionally, recyclable ABS and PPS, regenerated through chemical recycling processes, contribute to a circular economy without compromising their 76 J/m impact strength.
Moreover, a new plastic developed by MIT, 2DPA-1, is significantly stronger than traditional materials like steel and has the potential to transform various industries due to its unique properties.
These innovations not only enhance material performance but also redefine the standards of “toughness,” enabling high-strength plastics to meet broader and more demanding applications in the future.
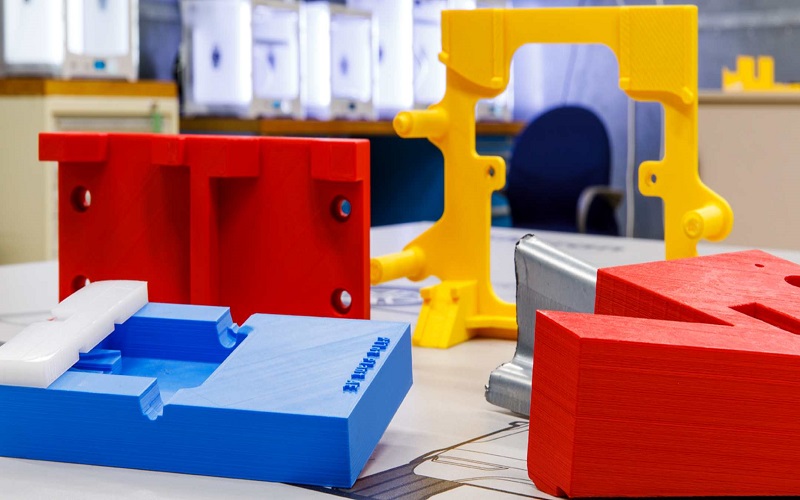
Key Factors to Consider When Choosing Strong Plastics
Choosing the right plastic for a specific application involves more than just picking the strongest material on paper; it’s about finding the best match for your specific needs, including other materials.
Strength in plastics is multi-faceted, and several critical factors should guide your decision-making process.
Tensile Strength and Load Requirements
How much force will the plastic need to withstand? Tensile strength, the ability to resist breaking under tension, is crucial for load-bearing applications like structural components or cables.
For example, PEEK’s 14,000 psi tensile strength makes it ideal for high-stress environments, while ABS, at 4,000–6,000 psi, suits lighter-duty tasks. Match the material’s capacity to your project’s demands.
Impact Resistance
Will the plastic face sudden shocks or drops? Impact resistance determines how well a material absorbs energy without cracking. Polycarbonate excels here, perfect for safety gear, while PAI might falter in high-impact scenarios despite its thermal prowess.Assess whether toughness under impact is a priority.
Temperature Tolerance
What’s the operating environment like? Plastics vary widely in heat resistance. PAI thrives at 275°C, making it a go-to for aerospace, whereas ABS softens above 100°C, limiting it to milder conditions.Ensure your choice can handle the thermal extremes it’ll encounter.
Chemical Exposure
Will the plastic be exposed to harsh substances? Chemical resistance is vital in corrosive settings—PEEK resists acids and oils effortlessly, while nylon weakens against strong acids despite its versatility.Identify the chemicals in play and pick a plastic that won’t degrade.
Wear and Friction Resistance
For moving parts like gears or bearings, durability against abrasion matters. PPS shines with low wear rates (e.g., PPS at 0.04g loss after 1,000 cycles), while ABS might wear faster under constant friction.Consider how long the material needs to last under contact stress.
Cost and Processability
Budget and manufacturing constraints can’t be ignored. High performers like PEEK and PAI come with steep price tags and require specialized processing, whereas ABS and nylon offer affordability and ease of molding.Balance performance needs with economic feasibility.
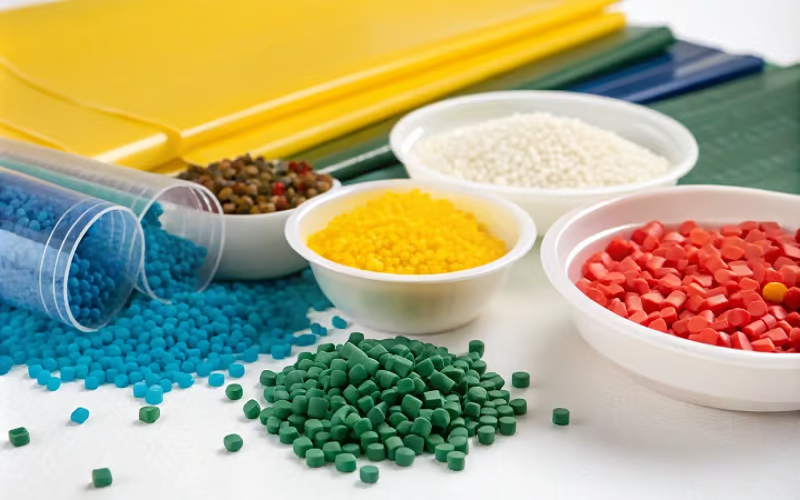
Summary
In summary, the seven strongest plastics each bring unique properties to the table, making them indispensable in various high-stress applications. From aerospace to medical devices, these materials push the boundaries of what’s possible, offering unparalleled strength, durability, and versatility.
As we look to the future, advancements in sustainability, smart materials, and manufacturing techniques promise to further enhance the performance and applicability of high-strength plastics. Knowing about these options can save you money without sacrificing quality and help you create great products that are capable of withstanding significant stress.