Within the vast landscape of industrial manufacturing, the plastics industry has permeated every aspect of life, and the injection molding process has become progressively more demanding and complex as demand has increased.
In this article, we will analyze the complex steps in injection molding process, explore its components, working principles and process advantages, and understand why it occupies an important position in modern manufacturing.
What is injection molding?
Injection molding is an injection-cum-molding molding method. Plastic is plasticized in the heated barrel of the injection molding machine and then injected by a plunger or reciprocating screw into the cavity of a closed mold to form the plastic of the product.
The main features of the injection molding method are fast production speed, high precision, suitable for mass production of complex shaped parts, is one of the important processing methods.
Most thermoplastics and some thermosetting plastics (such as phenolic plastics) can be processed by this method.
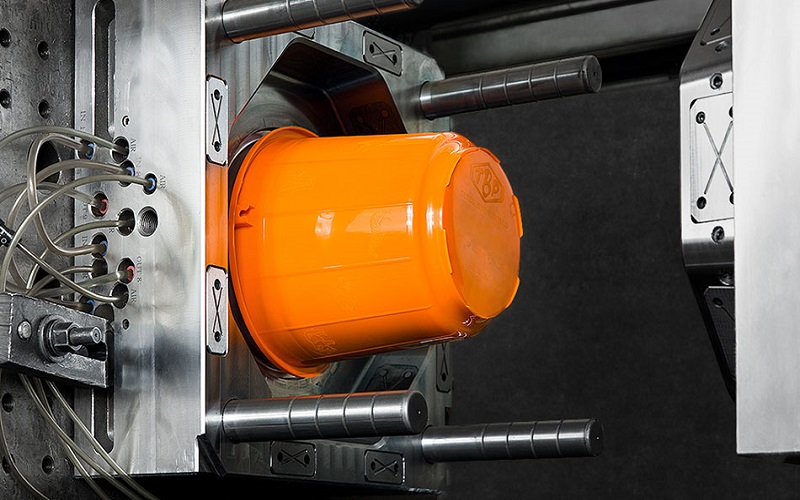
Key Equipment in the Injection Molding Process
Streamlining the injection molding process requires the use of various equipment to ensure efficiency and top-notch quality. Check out some of the key injection molding equipment:
Injection molding machine
As the core equipment of the injection molding process, the injection molding machine is usually divided into two parts: the injection unit and the clamping unit.
The role of the injection unit is to complete the melting and injection of plastic within a certain period of time, mainly composed of plasticizing parts (including nozzles, barrels and screws), hoppers (including drying devices), screw drive, injection device and injection seat and injection seat moving cylinder.
While the clamping unit uses the mold closing device and mold adjusting device to make the abrasives close to produce systematic elastic deformation to achieve the clamping force, to complete the task of mold closure and locking.
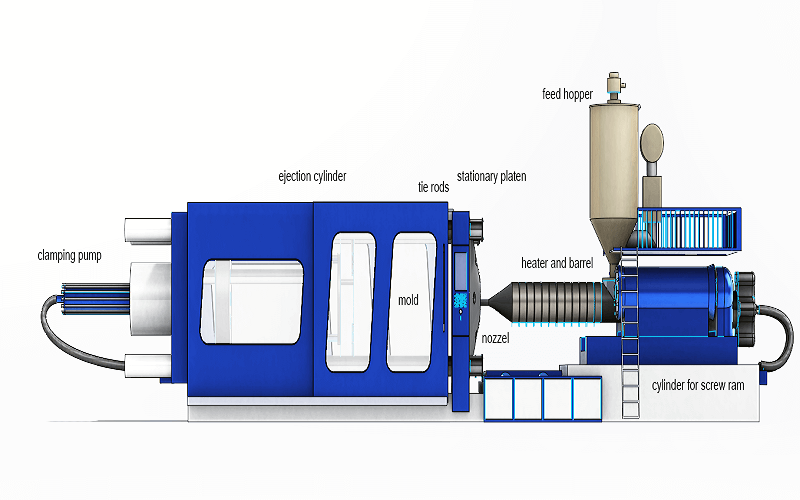
Injection Mold
The injection mold as a key tool in the injection molding process steps, the design and manufacture of its structure and components directly affect the molding quality of the product.
It includes components such as upper mold, lower mold, lap plate, guide pillar, guide sleeve, ejector pin, bottom pin, nozzle and other components.
Different products require different mold structures, so they need to be designed and manufactured according to the shape and size of the product for plastic injection and cooling to form the shape of the product.
Commonly used injection mold materials are P20, 718, NAK80, S136, etc.. These materials have high hardness, high abrasion resistance and high corrosion resistance, and can meet the injection molding processing needs of most products.
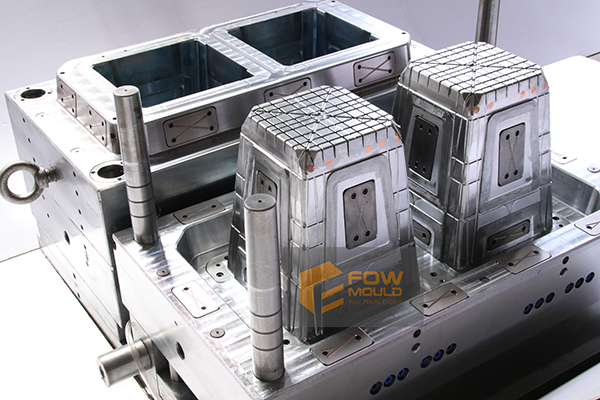
Auxiliary equipment
In addition to the above two main equipments, they also include automatic feeders, dryers, cooling water units, unloaders, etc., which are used to ensure the handling and transportation of raw materials and finished products during the injection molding production process.
The automatic feeder is usually a funnel-shaped device that transports plastic pellets to the injection molding machine. It is important to note that some injection molding materials can contain moisture and must be processed through a dryer before the injection molding process can take place.
What are the steps in injection molding process?
Injection molding process is a repetitive cyclical process that harnesses the power of a screw propelling system to heat materials, melting plastic into a fluid state.
This fluid plastic is then injected into a closed mold, where it undergoes a drying and shaping process, resulting in the final product. In this injection molding cycle, it generally includes the following steps:
Clamping
Before introducing the material, it’s essential to ensure the mold is in a locked position.
Typically, the mold consists of two parts, with each half connected to the injection machine through a clamping mechanism.
As the plastic material is injected into the mold cavity, a dynamic clamping mechanism pushes the two mold halves together, applying enough force to keep the mold firmly closed.
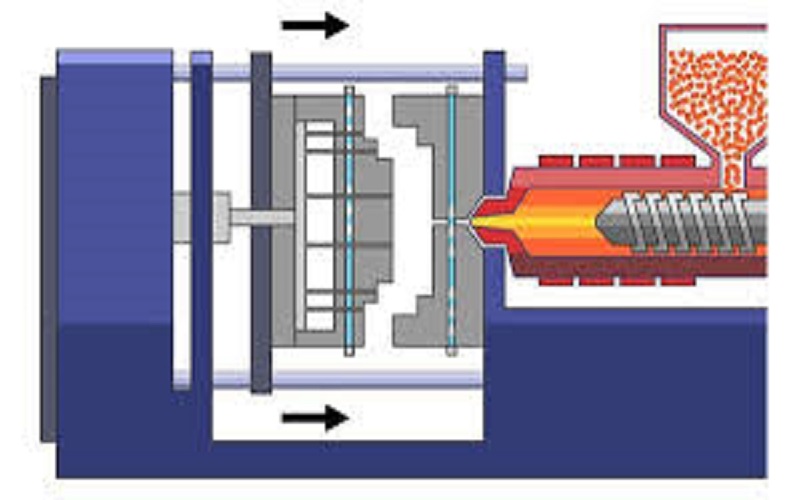
Injection
This is the most crucial step in the injection molding process. The selected thermoplastic or thermosetting material is fed into the machine’s hopper, allowing it to enter the heating barrel inside the injection machine.
Screws continuously stir to accelerate the melting of the plastic pellets, pushing them into the mold cavity.
After fully filling the mold, the screw continues to exert pressure on the molten material to prevent any backflow within the mold.
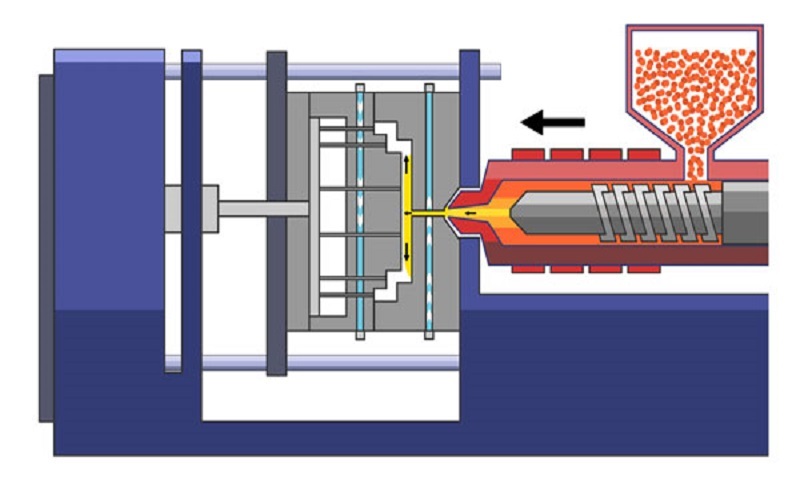
Cooling
After the injection process is complete, the molten plastic begins to cool gradually within the mold. This process automatically starts as soon as the material comes in contact with the mold surface and solidifies, taking the shape of the designated mold.
It’s crucial to strictly control the cooling rate to avoid shrinkage and defects.
Different plastic materials have varying requirements for cooling time; ensuring a thorough understanding of the utilized material is beneficial for determining the precise timing.
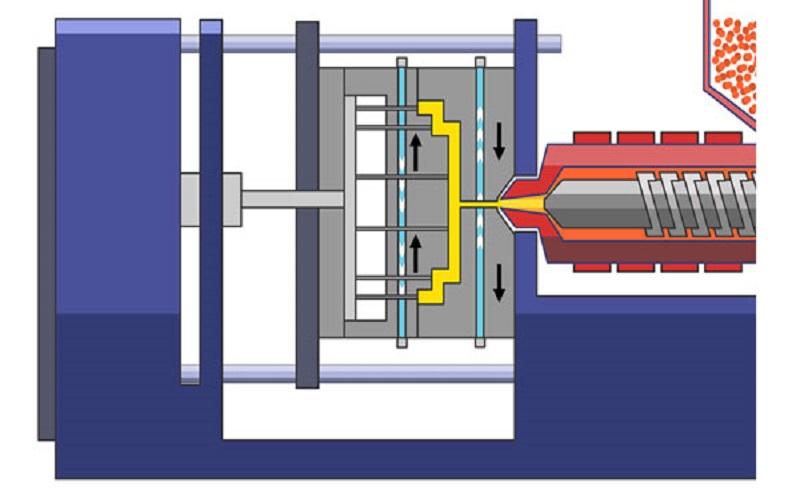
Ejection
Once cooled, the plastic product will still be attached to the mold and can be challenging to remove manually. Therefore, this step is facilitated by ejector mechanisms on the mold.
The injection machine’s ejector plate presses against the mold’s ejector retainer plate.
Subsequently, the retainer plate, along with the ejector pins, moves forward, pushing the plastic product out completely. After a successful ejection, the mold automatically closes.
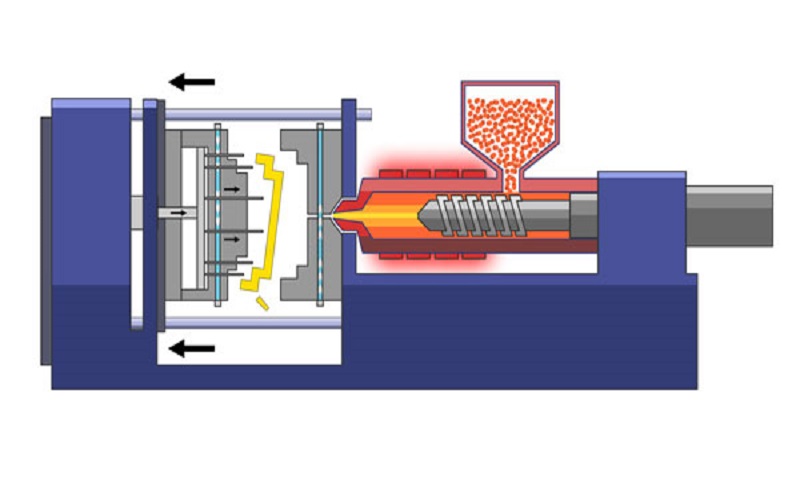
Materials used in the process of injection molding
In the injection molding process, the choice of material is a key factor that determines the performance of the molded part as well as the setting of the injection process parameters.
Thermoplastics, elastomers are some of the more commonly used materials in the injection molding process today. Each material possesses unique properties and process requirements, and the following is information on specific materials.
Types | Categories |
Thermoplastics | PE,PP,PVC,PS,PC,PET,ABS |
Elastomers | Silicone Rubber,SBR |
Others | Nylon,PMMA,POM |
Injection Molding Process Parameters
As a highly efficient manufacturing process, injection molding is very important for the control of injection molding parameters, including temperature, pressure and cycle time variables have a profound impact on product quality.
Melt temperature
Melt temperature is an important parameter in plastic molding. Each plastic material has a corresponding melt temperature.
The temperature from the hopper to the nozzle is gradually increasing, the temperature value of the hopper area is generally 40-50℃ lower than the melting temperature of the plastic, and the temperature of the nozzle area is set to the melting temperature of the plastic.
Mold Temperature
Different materials have various mold temperature ranges. When designing the mold cooling system, it’s crucial to ensure that the temperature difference between the front mold and the back mold is minimal (not exceeding 16℃). A smaller temperature difference helps improve the product’s molding quality and reduce costs.
Back pressure
Adjusting the back pressure can adjust the degree of mixing between the color powder and the plastic material, which affects the molding effect. Appropriate back pressure is generally about 10kg/cm². It can reduce the defects such as color mixing, air bubbles and uneven luster of the plastic parts.
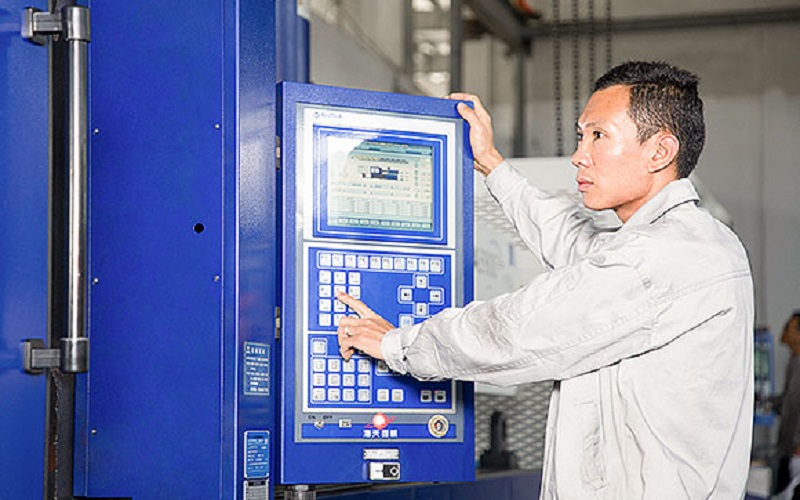
FOWMould——All-Around Injection Molding Company
FOW Mould, as an excellent injection molding supplier for 40 years, we offer a full range of injection molding services.
Whether it is product design or prototype production, we are capable of meeting your needs. While providing high precision mold quality, we are also committed to completing your project in the fastest time possible!
In addition, we have advanced injection molding machines to assist you with your order. Meanwhile, FOW Mould provides a wide range of injection molding materials to meet your needs.
Conclusion
As a core technology in plastic manufacturing, the intricate injection molding process has strict requirements for both equipment and process parameters.
A high-quality injection-molded product necessitates adherence to the steps of injection moulding and precise control of the injection molding process parameters. So, what are you waiting for? Embark on your injection molding journey with FOWMould now!