The world of injection molding is intricate and full of unique parameters, and one of the most critical aspects is the SPI mold classification. This system, developed by the Society of Plastics Industry (now known as the Plastics Industry Association), provides a standardized approach to classifying molds. It’s like a language that everyone in the plastics industry can understand, from molders to designers, and even customers.
SPI mold classifications are based on a variety of factors, including the type of mold, the materials used (from mild steel to the highest quality materials), and the mold’s expected lifespan. The classifications range from Class 101, which represents the highest quality and is suitable for extremely high production, to Class 105, typically used for prototype molds and limited production.
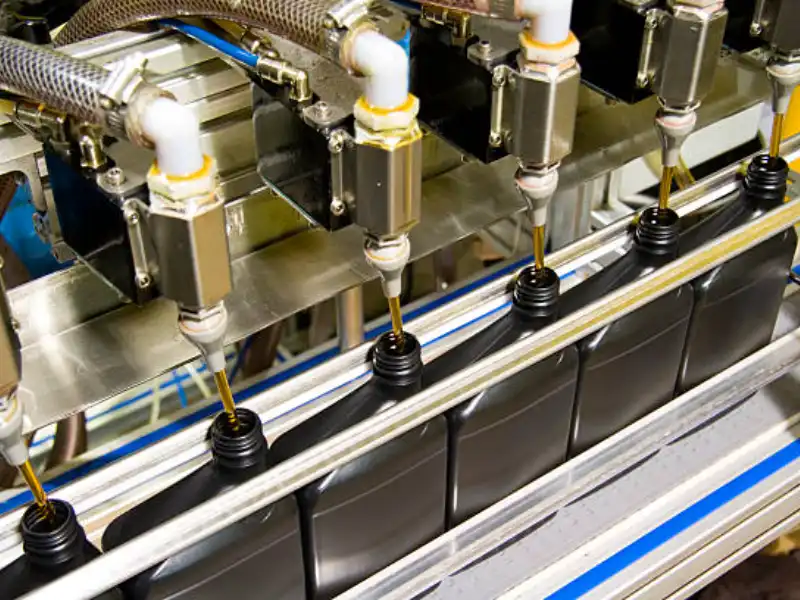
Understanding the Importance of SPI Mold Classification
Why is SPI mold classification so important, you might ask? Well, it’s all about setting expectations and ensuring sufficient strength and quality for the task at hand.
Each mold class comes with its own set of specifications, including the hardness of the tool steel, the number of cavities, and the temperature control provisions. These classifications help to determine the mold’s suitability for different applications, whether it’s for abrasive materials, non-abrasive materials, or something in between.
For instance, if you’re working with corrosive materials, you’ll need a mold made from corrosive resistant material, like stainless steel, with a minimum hardness that can withstand the wear and tear. On the other hand, if you’re dealing with non-abrasive materials, a mold with lower hardness might suffice.
How does hardness factor into SPI Mold Classification?
Hardness is a key factor in SPI mold classification. It’s measured in Rockwell hardness or BHN (Brinell Hardness Number), and it’s a clear indicator of a mold’s durability and resistance to wear.
The hardness of the mold is directly related to the type of steel used. For example, mold bases and wear plates made from tool steel have a higher Rockwell hardness than those made from mild steel. This hardness allows the mold to withstand the pressures of the injection molding process, especially when dealing with abrasive materials.
In the next part, we’ll delve into the specifics of each mold class, starting with Class 101 molds.
Class 101 Molds
When it comes to the pinnacle of mold classifications, Class 101 molds stand tall. Class 101 molds are also known as high production molds.These molds are constructed with detailed mold design, including features like line locks, gibs, and slide cores, crafted from the highest quality materials, ensuring longevity and durability. Designed for extremely high production, they can withstand over one million cycles. The tooling for these molds often requires the use of tool steel with a minimum hardness that can resist abrasive materials, ensuring the mold’s integrity over time.
Temperature control is paramount for these molds. Adequate channels for cooling and heating are essential to maintain the mold’s temperature, ensuring consistent part quality. Given their robustness, Class 101 molds are often the choice for projects that demand tight tolerances and high repeatability.
Class 102 Molds
Class 102 molds strike a balance between quality and cost. Suitable for medium to high production, these molds are designed for projects requiring up to one million cycles. While they might not boast the extreme durability of Class 101 molds, they still offer impressive longevity. The tooling for these molds is often made from high-quality steel, but with a slightly lower hardness than Class 101. These mold features make them a popular choice for projects that require a balance between performance and budget.
Class 103 Molds
For those in the plastics industry looking for a reliable mold for medium production runs, Class 103 molds are often the go-to choice. These molds are designed for projects that require up to 500,000 cycles. They’re crafted from good quality materials, ensuring decent performance without breaking the bank. Their specifications are tailored for non-abrasive materials, making them a versatile choice for a wide range of projects.
Class 104 Molds
When production needs are limited, and the materials used are non-abrasive, Class 104 molds come into play. These molds are ideal for short runs, typically up to 100,000 cycles. Given their limited production scope, they’re often made from milder steel types, which might not have the hardness of their higher-class counterparts but are sufficient for their intended applications.
Class 105 Molds
In the early stages of product development, prototypes are crucial. Class 105 molds, often referred to as prototype molds, are designed for extremely limited production, typically less than 500 cycles. They’re perfect for testing design concepts and functionality before moving on to full-scale production. Given their limited use, these molds might not have the same robust features as higher classes, but they serve their purpose effectively, producing the minimum prototype pieces needed for testing.
The Role of SPI Mold Classification in Injection Molding Process
SPI mold classification plays a crucial role in the injection molding process. For instance, molds designed for high production often feature advanced temperature control systems and corrosion-resistant plating to withstand the rigors of the injection molding process.
For instance, the mold’s hardness, determined by the type of steel used, can significantly impact the mold’s performance during the injection molding process. A mold with high Rockwell hardness is more resistant to wear and tear, making it suitable for molding abrasive materials. On the other hand, molds with lower hardness might be more suitable for non-abrasive materials.
Moreover, the mold classification also dictates the temperature control provisions. For high-production molds, maintaining a consistent temperature is crucial to ensure part quality and reduce cycle time. Therefore, molds in higher classes often come with more sophisticated temperature control systems.
How SPI Mold Classification Impacts Mold Lifespan and Maintenance
On the other hand, lower class molds, such as Class 104 and 105, are designed for lower production volumes and may not have the same lifespan as their higher-class counterparts. They might require more frequent maintenance or replacement, especially when used beyond their intended production volumes.
On the other hand, lower class molds, such as Class 104 and 105, are designed for lower production volumes and may not have the same lifespan as their higher-class counterparts. They might require more frequent maintenance or replacement, especially when used beyond their intended production volumes.
The Relationship Between SPI Mold Classification and Production Costs
The SPI mold classification also impacts production costs. For instance, molds made from cast metal might be more expensive upfront but can offer cost savings in the long run due to their durability and longevity. They can withstand high production volumes, reducing the need for frequent replacements.
Conversely, lower class molds might be more affordable initially, but their shorter lifespan and potential for more frequent maintenance or replacement can add to the production costs over time. Therefore, it’s crucial to consider the total cost of ownership, not just the initial cost, when choosing a mold based on its SPI classification.
Real-World Machining Applications of SPI Mold Classification
In real-world machining applications, the SPI mold classification can guide the selection of the right materials and techniques. For instance, molds designed for high production might require advanced machining techniques and high-quality materials like RC (Rockwell C) hardened steel.
For high-production molds, such as Class 101 and 102, the machining process must adhere to tight tolerances to ensure the mold’s durability and performance. This often involves using advanced machining techniques and high-quality tool steel to achieve the desired hardness and precision.
On the other hand, for prototype molds or low-production molds, the machining process might not require the same level of precision or hardness. Instead, the focus might be on speed and cost-effectiveness, using more affordable materials and faster machining techniques.
The following table provides a quick reference for the different machining applications and considerations for each SPI mold class:
Mold Class | Production Volume | Machining Techniques | Material |
Class 101 and 102 | High | Advanced techniques, tight tolerances | High-quality tool steel, RC hardened steel |
Class 103 | Medium | Balanced approach, moderate tolerances | Good quality materials |
Class 104 and 105 | Low/Prototype | Speed and cost-effectiveness, looser tolerances | More affordable materials |
Common Misconceptions About SPI Mold Classification
Despite its importance, there are some common misconceptions about SPI mold classification. For instance, some might believe that molds with higher hardness or more advanced features are always better, but this isn’t always the case. While they offer superior durability and performance, they might not always be the most cost-effective choice, especially for low-volume or prototype projects.
Another misconception is that the hardness of the mold is the only factor that matters. While hardness is crucial, other factors, such as the mold design, ejection mechanism, and temperature control provisions, also play a significant role in the mold’s performance and lifespan.
Conclusion
In conclusion, understanding and correctly applying SPI mold classification, a system developed by the Society of the Plastics Industry, can significantly impact the efficiency and success of your injection molding projects. By choosing the right mold for your specific needs, you can balance quality, cost, and production volume, ensuring the best possible outcomes.
Remember, the right mold classification for your project depends on various factors, including the type of material, production volume, and cost objectives. So, take the time to understand each mold class and make an informed decision. After all, in the world of injection molding, the devil is in the details!
That concludes our comprehensive guide to SPI mold classification. We hope it has shed light on this crucial aspect of the plastics industry and will help you make more informed decisions in your future projects.
Ready to take your injection molding projects to the next level? With FOWMould’s commitment to precision, quality, and customer satisfaction, you’re in capable hands. Reach out to us today and let’s create something exceptional together!