Rotational molding, also known as rotomolding, is a versatile and cost-effective manufacturing process used to produce hollow plastic parts with uniform wall thickness and complex geometries.
By rotating a mold biaxially in a heated environment, plastic material inside the mold melts, coats the interior surface, and solidifies into the desired shape upon cooling.
Rotational molding excels for low to medium volumes, and mold creation costs are cost effective compared to injection molding or blow molding.
In the following content, we will delve into the principles, processes, advantages, and specific applications of rotational molding, exploring how it provides innovative and efficient solutions for plastic product manufacturing.
What Is Rotational Molding?
Rotational molding, as also called roto molding, creates hollow plastic parts by heating and rotating a mold filled with powdered plastic.
Once the mold is closed, it rotates along two perpendicular axes while being heated. Under the influence of gravity and heat, the plastic material gradually coats, melts, and adheres uniformly to the entire surface of the mold cavity, forming a shape identical to the cavity. The product is then cooled and removed from the mold to achieve the desired shape.
Rotationally Molded Plastic Products are hollow and virtually stress free because they are molded without any external pressure.
This low pressure process ensures that the molten plastic, potentially fortified with corrosion and static-resistant additives, uniformly coats the interior walls of the mold cavity.
Rotational molding is a method used in production process, primarily for manufacturing medium, large, or extra-large hollow, seamless products, such as transport containers, wheelbarrow tubs, boat hulls, mannequins, industrial storage tanks, and reservoirs.
The largest containers can reach up to 100,000 liters.This process is difficult to achieve with injection molding and blow molding.
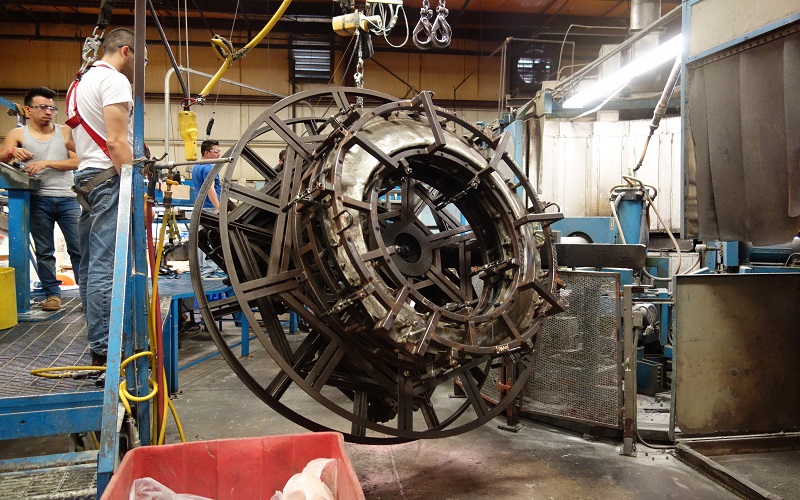
Rotational Molding Process
The basic principle of rotational molding process can be understood as the With-Drawal theory of liquid, where the inner wall of the mold cavity is equivalent to the surface of an object immersed in liquid.
Depending on the lifting speed and liquid viscosity, a corresponding liquid coating layer is formed. Here, the liquid refers to the molten resin powder.
1. Application of Release Agent
Applying a release agent on the mold is essential for easy removal of the product from the mold. It also effectively prevents damage to the product due to strong adhesion between the product and the mold during demolding.
The mold spindles are affixed to a rotating axis, facilitating consistent coating of parts during production.
2. Installation of Inserts and Related Molding Accessories
Inserts primarily serve to locally reinforce the product, while molding accessories refer to modules used for forming threads or special parts. They must be properly installed in predetermined positions before adding material to the mold.
3. Material Loading
Before adding material, precise measurement is necessary. If additives are required, the components need to be premixed.
Accurately measure the weight of plastic powder needed for the final product, add it to the bottom of the split mold, then secure the two halves of the mold together and mount them on the rotating axis.
4. Mold Closure
Before closing the mold, ensure that any residual material at the joint is removed. The mating surfaces must fit perfectly to prevent material leakage during molding processes.
5. Heating
Place the mold filled with material into the heating chamber (or use other heat sources like gas flames) with the temperature set above the resin’s melting point. The mold rotates along two perpendicular axes, heating until it reaches the specified temperature.
Additionally, enough room must be left between the parallel walls to allow for the melt-flow to move properly throughout the mold.
Initially, if powder material is used, a porous layer forms on the mold surface, which gradually melts into a uniform wall thickness layer during the heating cycle. If liquid material is used, it flows and coats the mold surface, stopping once the gel point is reached.
6. Cooling process
Once the resin is fully melted, transfer the mold to the cooling station, where it continues to rotate while being cooled by forced air or water spray.
7. Demolding and Mold Cleaning
Care must be taken to avoid damaging the product during demolding. Additionally, any residual material and debris should be thoroughly cleaned from the mold in preparation for the next molding cycle.
New rotational molding ovens are being designed to improve manufacturing efficiencies and provide better process control through automation advancements.
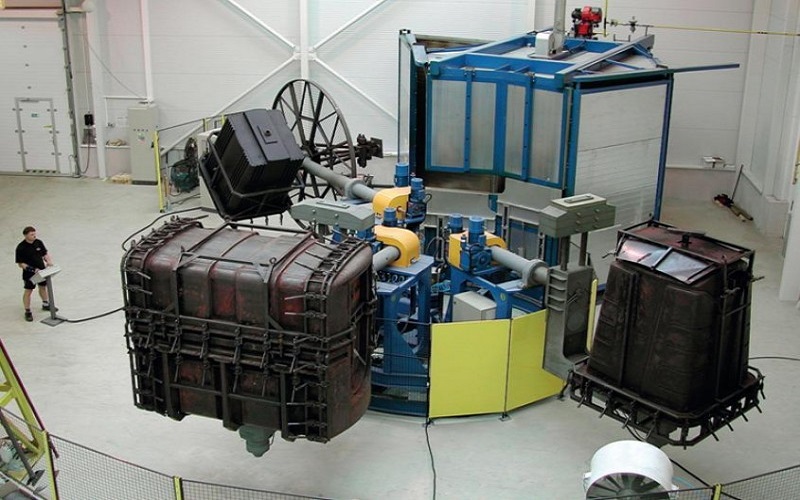
Characteristics Of Rotational Molding
Uniform Wall Thickness and Seamless Design: Rotational molding produces parts with consistent wall thickness, free of corner scraps and weld lines. It is capable of forming products with a wide range of wall thicknesses, typically from 1 to 16 mm for polyethylene parts.
However, thicker mold walls are challenging to mold due to material viscosity. This manufacturing process is particularly ideal for plastic products with wall thicknesses of 2 to 5 mm.
Hollow or Shell Products: The process is primarily suited for hollow vessels or shell-like products, with limited applicability for solid parts. The surface quality of the molded product is highly dependent on the mold cavity’s surface condition.
Lower Dimensional Precision: Rotational molding typically achieves a dimensional accuracy of ±5%, which is relatively low compared to other molding processes.
Types Of Rotational Molding Machines
A rotational machine is a specialized piece of equipment designed to produce hollow plastic parts through the rotational molding process.
Based on their structure, motion mode, and application scenarios, rotational molding machines can be categorized into various types.
Each type differs in mold movement, heating and cooling chamber design, and suitable products. Here are the common types of rotational molding machines and their characteristics:
Biaxial Machine
This is the most common type of rotational machine, where the mold rotates continuously 360° on two perpendicular axes (main and secondary axes). The mold achieves biaxial full rotation through the rotational molders’ arms, ensuring the plastic material evenly coats the inner wall of the mold.
The equipment is equipped with separate heating and cooling zones, suitable for producing complex-shaped, uniformly thick medium to large hollow parts, such as storage tanks, containers, toys, and automotive parts.
Rock and Roll Machines
This is a simplified design of a rotational machine, where the mold rocks at a limited angle on one axis while rolling 360° on another axis.
Roll machines drive the mold to rotate fully along the longitudinal axis, combined with rocking motion on the horizontal axis (usually ±45° to ±90°). It is specifically designed for elongated or asymmetrical products, such as canoes, boat hulls, long pipelines, or storage tanks.
Shuttle Machine
In this type of rotational machine, the mold moves back and forth between the heating chamber and cooling chamber via a swinging device, with rotation typically being biaxial or uniaxial.
The heating and cooling chambers are separately arranged, and the mold moves between the two areas to complete the long heating cycles and cooling cycles.
This machine is suitable for producing medium to small-sized products such as containers, enclosures, and amusement park components.
Open Flame Machine
This is a more traditional type of rotational molding machine, using an open flame to directly heat the mold, with cooling usually conducted in an open environment. By driving the mold to rotate biaxially, the mold is exposed to the flame for heating.
This equipment does not have an enclosed heating station and uses gas flames for direct heating, with cooling typically done by natural air cooling or simple water cooling. It is suitable for simple, large, low-precision products, such as storage tanks or agricultural containers.
Material Selection For Rotational Molding
Rotational molding is a versatile manufacturing process that utilizes a variety of materials to produce hollow plastic parts.
Polyethylene (PE)
Polyethylene , particularly Low-Density Polyethylene (LDPE), Linear Low-Density Polyethylene (LLDPE), and High-Density Polyethylene (HDPE), is the most commonly used material in rotational molding.
After the advent of powdered polyethylene in the early 1960s, molding companies began using PE for rotational molding to produce PE storage tanks, large pipes, and other industrial products, greatly advancing the development of the rotational molding process.
Polyethylene grades that were designed specifically for rotational molding, and hot air ovens were developed.
Polypropylene (PP)
Polypropylene is a semi-rigid thermoplastic widely utilized in rotational molding for applications demanding greater stiffness and heat resistance than PE.
Offering enhanced structural rigidity, PP can endure temperatures up to 100-120°C and exhibits excellent resistance to harsh chemical environments.
Its robust properties make it an ideal choice for producing durable components within roto moldingmachines, ensuring reliable performance in challenging conditions.
Polyvinyl Chloride (PVC)
In the 1940s, rotational molding emerged as a pioneering process for crafting balls from PVC paste, marking an early milestone in the production of hollow plastic products. Typically processed as a liquid plastisol or micronized powder, PVC was adeptly handled by rotational molders, leveraging the unique capabilities of molding machines to create seamless and durable items with consistent quality.
Other Materials
Cross-Linked Polyethylene (XLPE) is an advanced variant of polyethylene engineered through cross-linking to deliver superior strength, enhanced chemical resistance, and exceptional durability.
This material is ideal for demanding applications such as fuel tanks, chemical storage containers, and high-performance components.
Processed in a manner similar to standard polyethylene within the heating chamber of a molding machine, XLPE requires specific additives and a controlled curing process to achieve its cross-linked structure, ensuring optimal performance and longevity in challenging environments.
Design Guidelines for Rotational Molding
When designing plastic parts for roto molding, there are several special considerations to keep in mind:
Wall Thickness: Ensuring consistent wall thickness is crucial for structural integrity and performance. While the process naturally allows for uniform thickness, design elements like ribs can help maintain this consistency, especially in areas prone to warpage.
Flat Surfaces: Large flat surfaces can lead to warping issues. To mitigate this, it’s advisable to avoid extensive flat sections. If flat surfaces are necessary, consider breaking them up with ribs or other reinforcing features to enhance stability.
Draft Angles: Draft angles are essential for the easy removal of the part from the mold. A draft angle of at least 1° on the outside walls is recommended to facilitate this process, assuming there are no rough surfaces or holes that could complicate demolding.r holes).
Corner Radii:Incorporate generous corner radii, with a minimum radius of 1-2 times the wall thickness (e.g., 4-8 mm for a 4 mm wall) for both internal and external corners.
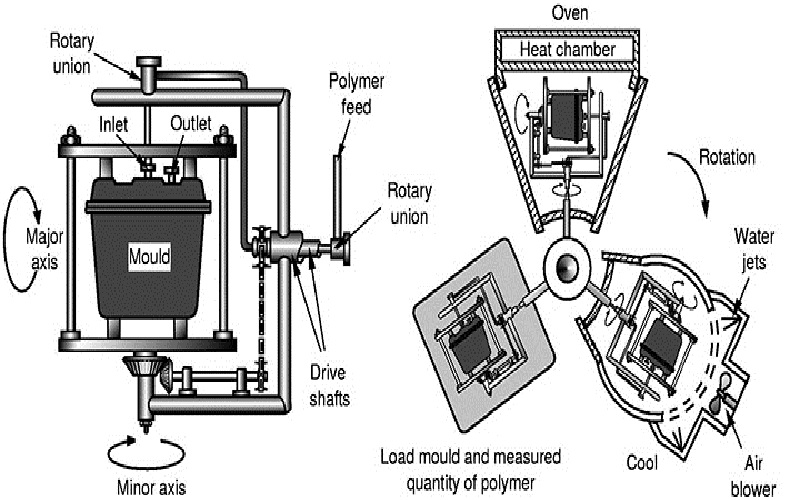
Application Of Roto Molding
With the development of rotational molding process and its products are constantly expanding the range of applications, some representative applications can be cited as follows:
Containers: Plastic bottle, storage tanks for various liquid chemicals (such as acids, alkalis, salts, chemical fertilizers, pesticides, etc.), and battery casings.
Automotive: Air conditioning ducts, backrests, armrests, gasoline containers (gasoline storage tanks and fuel tanks for cars and airplanes).
Sports Equipment: Water polo balls, floats, bicycle seat cushions, small boats, and shock absorbers between boats and docks.
Boxes, Shells And Large Pipes: Turnover boxes, garbage bins, machine casings, protective covers, and lampshades.
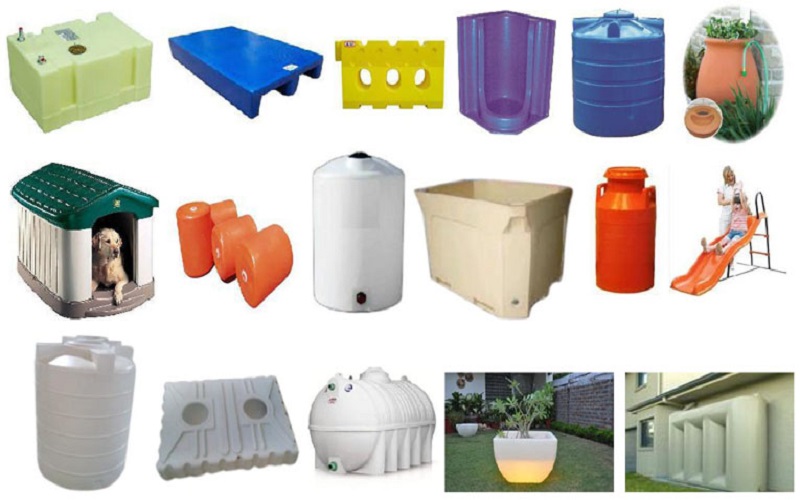
Advantage Of Rotational Molding
Roto molding offers numerous advantages that make it a preferred manufacturing process for producing hollow parts. Below is a concise overview of the key advantages:
Consistent Wall Thickness
Rotomolding can produce parts with consistent wall thickness, thicker corners for added strength, double-wall construction and the ability to easily incorporate inserts.
The biaxial or rock and roll motion of roll machines ensures even distribution of plastic material within the mold, resulting in seamless parts with uniform wall thickness.
Eliminates weak points like weld lines, enhancing structural integrity and durability for products like tanks, containers, and kayaks.
Low Tooling Costs
Rotational molding excels in small-batch and custom production due to its low mold and tooling costs. Utilizing rotational molding machines with simple, affordable molds—typically made from aluminum or steel—the process is ideally suited for short or low-volume production runs.
Minimal Material Costs
Rotational molding uses precise amounts of material (e.g., powder or liquid plastisol), with no runners or sprues, resulting in minimal waste compared to injection molding.
This efficiency, achieved through the even coating of molds by roll machines, reduces material costs and supports sustainable production for environmentally conscious applications like recycling bins or water tanks. The process’s low waste profile enhances its cost-effectiveness across various industries.
Disadvantage Of Rotational Molding
The main disadvantages of rotational molding are:
High energy consumption: This is due to the repeated heating and cooling that the mold and mold frame undergo in each molding cycle;
Long molding cycles: Since heat is primarily conducted through the plastic in a static state, rotational molding requires extended heating times,which can be a challenge for high volume production.
It can only produce hollow or shell products, making it difficult to process solid items. Additionally, the surface condition of the product greatly depends on the surface of the mold cavity.
Conclusion
In conclusion, products manufactured through rotational molding exhibit uniform wall thickness, dimensional stability, no weld lines, and minimal waste, making it a cost-effective and efficient molding method.
With its advantages of low tooling costs, minimal material waste, and flexible material selection, rotational molding demonstrates strong vitality and broad application prospects in modern manufacturing.
With continuous technological innovations and breakthroughs, it is anticipated that more molding companies will develop high-quality rotationally molded solutions suitable for various industries.