Reaction injection molding is an advanced polymer molding technology that centers on injecting two or more low viscosity liquid polymers or monomers into a closed mold cavity.
This is done after precise metering and efficient mixing, where they undergo rapid chemical reactions to directly polymerize and solidify into the final product.
This “mixing, reacting, and molding” process makes RIM especially suitable for manufacturing components with complex structures, large dimensions, or special material properties such as high impact strength, elasticity, and self-skinning foam structures. It effectively overcomes the limitations of traditional injection molding in certain applications.
As a significant method in plastic processing, RIM process plays a crucial role in the automotive industry, furniture manufacturing, construction materials, and electronic device housings.
This article will delve into the principles and processes of reaction injection molding, as well as its innovative applications across various industries, showcasing the cutting-edge appeal and future potential of this technology.
What Is Reaction Injection Molding?
Reaction Injection Molding (RIM) is an injection molding method where a chemical reaction occurs during the injection molding process.
Unlike traditional injection molding that uses polymers, this method involves two liquids or more liquid monomers or prepolymers, which are combined in specific proportions in a multi stream mix head.
They are then mixed uniformly under pressure and immediately injected into a closed mold and back to the storage tanks in a continuous loop.
The two liquids combine to create an exothermic reaction where they polymerize to form a molded parts.This RIM process can achieve a broad range of physical properties.
Since the raw materials are in liquid components, they can quickly fill the mold cavity with relatively low pressure, reducing both clamping force and mold costs, making it particularly suitable for high volume production.
Through a variety of chemical reaction, these polymers expand, thicken, and harden only after they’re injected into the heated mold, accommodating much more intricate designs than ordinary plastic injection molding.
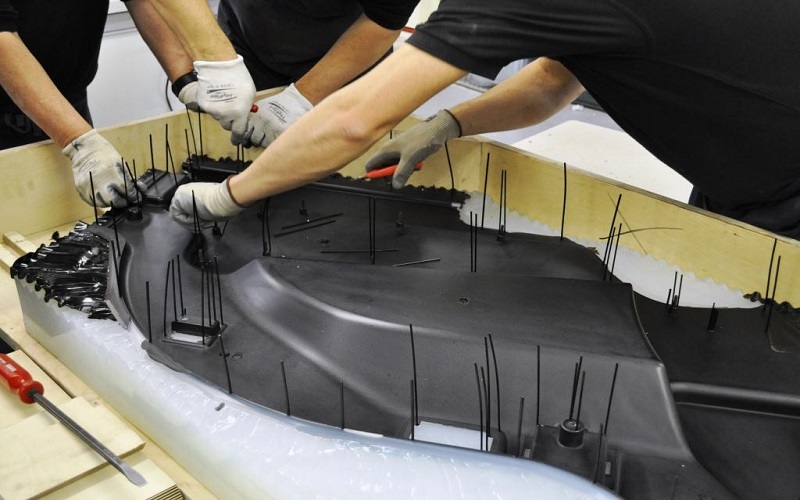
What Materials Are Used In reaction Injection Molding?
Initially, RIM was only used for polyurethane materials, but with advancements in process technology, it can now be applied to a variety of materials such as epoxy, nylon, polyurea, and polycyclopentadiene.
Polyurethanes: Polyurethane parts produced via RIM can be engineered to be solid (either rigid or elastomeric), fully foamed (rigid foam or flexible foam), or possess an integral skin structure combining a dense, solid outer layer with a lower-density foam core.The result is polyurethane parts with much lighter weight, and more intricate designs than those created by ordinary injection molding.
Polyureas: Similar to polyurethanes but faster-reacting, used for applications requiring high abrasion resistance and toughness.
Dicyclopentadiene (DCPD): A thermoset resin used for large, durable parts like automotive body panels, offering high impact resistance and dimensional stability.
Epoxy : Less common but used for high-strength, heat-resistant parts in specialized applications like aerospace or electronics.
Nylon (Polyamide) : Employed for structural components needing rigidity and thermal stability.
Additives like fillers (e.g., glass fibers, carbon fibers), pigments, and release agents may be included to enhance properties such as stiffness, aesthetics, or mold release.
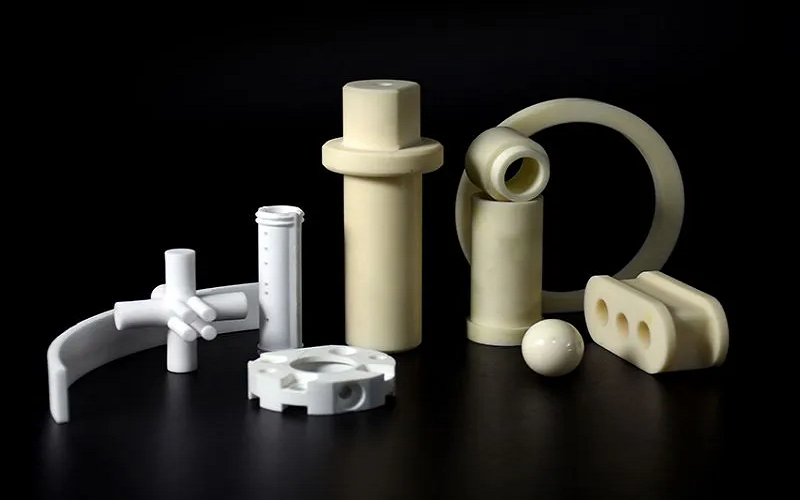
Types of Reaction Molding
Reaction Injection Molding encompasses several variations, each tailored to specific applications and material properties. The main types include:
Standard RIM: Involves mixing two liquid components (typically isocyanate and polyol for polyurethanes) that react in a mold to form a solid thermoset part. Used for automotive parts, medical devices, and enclosures due to its ability to produce large, complex shapes with good surface finish.
Structural RIM (SRIM):Alternately, parts can be strengthened with a fiber mesh in a process called structural reaction injection molding (SRIM).Incorporates reinforcing materials like glass or carbon fibers into the mold before injecting the reactive mixture. This enhances strength and stiffness, making it ideal for structural components such as automotive bumpers or industrial panels.
Reinforced RIM (RRIM): Similar to SRIM but uses fillers (e.g., milled glass, mica, or wollastonite) mixed directly into the liquid resin before injection. It improves rigidity and dimensional stability, commonly used for exterior automotive parts like fenders.
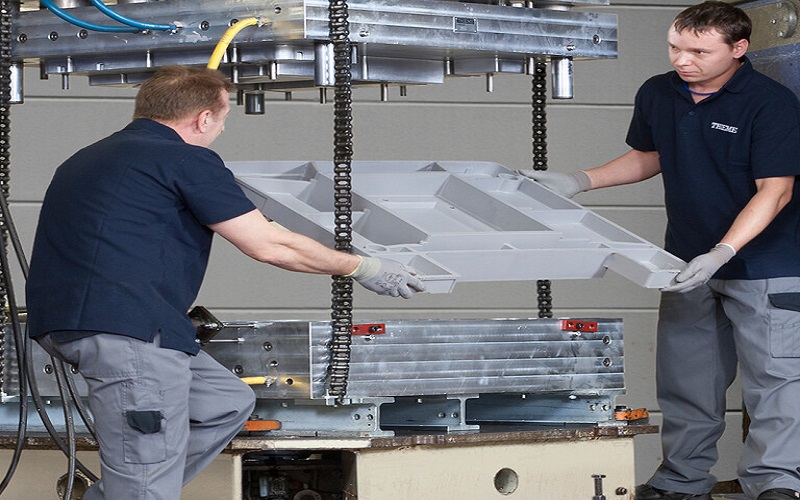
The RIM Process
The manufacturing process of rim parts involves a series of precise steps to create high-quality, thermoset polymer components. Below is a detailed outline of the rim process:
Material Preparation and Delivery
The RIM process begins with polymer liquids stored in storage tanks that are eventually dispensed by high-pressure industrial pumps.
Mixing
Two liquid components are precisely metered and injected under high pressure (usually 10-20 MPa or 1500-3000 psi) into a specially designed mix head.
Inside the mix head, these high-pressure liquid streams collide at extremely high speeds (impingement mixing), creating intense turbulence that ensures molecular-level uniform mixing within a very short time (milliseconds).
This rapid and efficient mixing is crucial for achieving uniform final product performance and must be completed before significant chemical reactions begin.
Injection
The thoroughly mixed liquid reaction mixture is injected through the nozzle of the mix head into a pre-closed and usually heated mold cavity (to facilitate curing) at relatively low pressure, typically much lower than traditional thermoplastic injection molding.
The low viscosity liquid easily fills the complex shapes of the mold cavity and large components. A laminar flow filling method is usually adopted to avoid air entrapment.
In-Mold Chemical Reaction and Curing
The liquids are mixed at high velocity (1200 psi) using an impinging mixer before being transferred into the mold for the curing process.
Once the mixture enters the mold cavity, pre-added catalysts initiate or accelerate the chemical polymerization reaction between the components (e.g., the formation reaction of polyurethane).
This is an exothermic reaction, where the heat generated by the chemical reaction, along with the heat provided by the mold, promotes the rapid curing of the material (transitioning from liquid to solid).
If the formulation contains foaming agents, the reaction heat will cause them to vaporize, producing gas that forms a foam structure. For self-skinning foam, the mold surface temperature is lower, inhibiting foaming near the mold walls, creating a dense skin, while a foam core forms internally.
The curing time is relatively short, typically ranging from several tens of seconds to a few minutes, depending on the material system, part size, and wall thickness.
Demolding
Once the part reaches sufficient strength and hardness (i.e., fully cured), the mold can be opened, and the molded product can be ejected or removed. To facilitate demolding, a release agent is usually pre-applied to the inner surface of the mold.
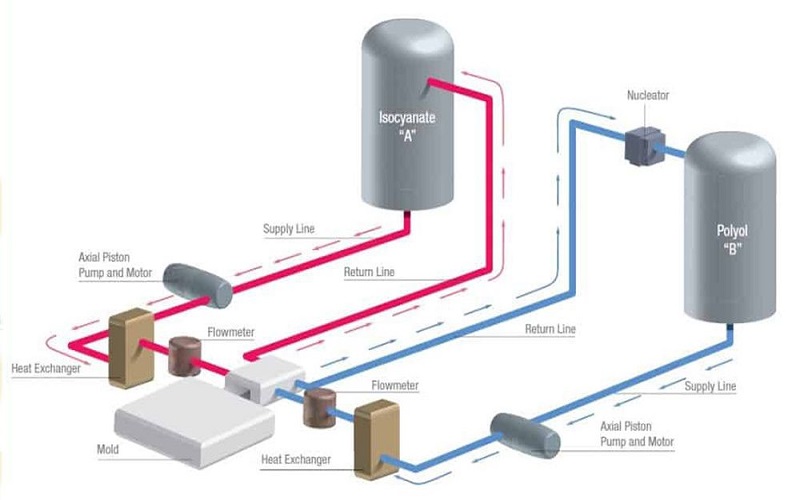
Advantages of Reaction Injection Molding
The RIM molding process holds an array of valuable benefits. Here are a few that our customers have found beneficial
Cost Efficient
As liquid polymers require less pressure and lower temperatures to complete the part than traditional ingredients such as metals, RIM provides a further money-saving benefit.
Lighter Weight
Reaction Injection Molding is often utilized for the molding of strong, lightweight parts that are easily painted, making them ideal for automotive and aerospace applications where weight reduction is critical.
Design Flexibility
Through the RIM design process raw materials and molding techniques can be selected, and customized, to deliver the desired weight, strength, density and hardness characteristics that you are looking for.
Application Of Reaction Injection Molding
Reaction Injection Molding is a low pressure, low temperature process used to RIM mold many types of plastic parts. This process is typically used for the medical, industrial and automotive industries.
Medical: RIM is used for biocompatible, lightweight, and durable parts like MRI machine covers, prosthetics, or equipment enclosures, where precision and aesthetics matter.
Industrial: Ideal for robust enclosures, panels, or machinery covers that need chemical resistance and impact strength.
Automotive: Commonly used for exterior and interior parts (e.g., spoilers, fascias, or seat foam) due to its ability to produce large, lightweight, and high-impact components.
Aerospace and Consumer Goods: Suitable for lightweight, structural parts or aesthetically pleasing housings in smaller quantities.
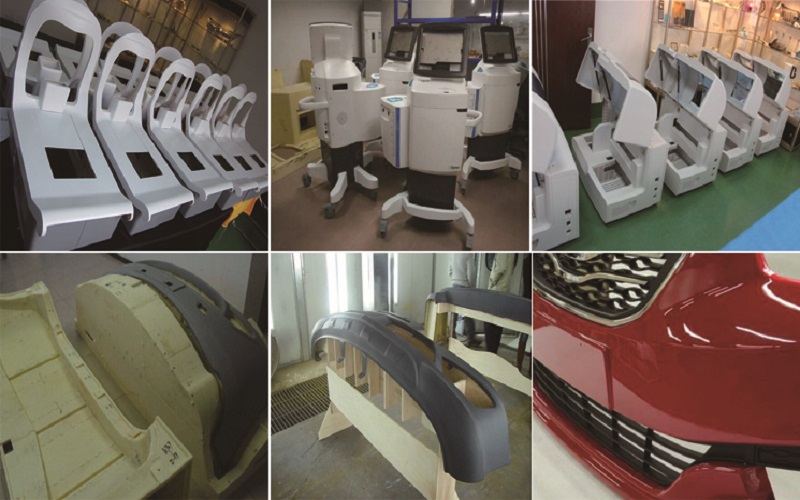
Reaction Injection Molding vs Traditional Injection Molding
Reaction injection molding and traditional injection molding differ significantly in terms of processes, materials, and applications.
RIM involves mixing two liquid components (such as polyol and isocyanate for polyurethanes), which are then injected into a mold at low pressure (50–100 psi) and lower temperatures, where they undergo a chemical reaction to form a non-remeltable thermosetting polymer. This process is suitable for producing large, lightweight parts with complex geometries.
In contrast, traditional injection molding melts thermoplastic materials and injects them into steel molds at high pressure (5000–20000 psi) and high temperatures. The material solidifies through cooling and can be remelted and recycled, making it suitable for medium to small-sized parts with high precision and uniform wall thickness.
RIM supports direct encapsulation of inserts (such as metal or electronic components) within the mold, providing seamless integration superior to injection molding, cast molding, and vacuum forming.
RIM molds are cost-effective, ideal for medium to small batch production and rapid prototyping, whereas traditional injection molds are costlier and better suited for large-scale production.
RIM parts offer excellent impact and chemical resistance, commonly used in automotive bumpers and medical device housings; traditional injection molding is often used for consumer electronics and packaging. The choice between the two depends on part size, production volume, and performance requirements.
Conclusion
Reaction Injection Molding (RIM), with its unique low-pressure and low-temperature process, offers an efficient solution for manufacturing large, lightweight, and complex thermoset parts.
It achieves diverse material properties through rapid chemical reactions, supporting customization from rigid to foamed structures, and allows seamless encapsulation of inserts within the mold, distinguishing it significantly from traditional molding processes.
RIM’s extensive applications in the automotive, medical, and industrial sectors demonstrate its cost-effectiveness and design flexibility in producing medium to small batches of high-performance parts.
Although not suitable for large-scale or recyclable material scenarios, RIM’s excellent impact resistance, chemical stability, and rapid prototyping capabilities make it a crucial technology driving innovation in modern manufacturing, with limitless future potential.