In our daily lives, PU foam is ubiquitous, playing an important role in everything from comfortable sofas and mattresses to energy-efficient refrigerators and refrigerated vehicles.
This porous polyurethane material not only boasts excellent physical properties but also features eco-friendly characteristics, making it an indispensable new material in modern industry.
This article will delve into the preparation, types, and application advantages of PU foam across various industries, aiming to reveal how this material plays a critical role in technological innovation and sustainable development.
What Is Polyurethane Foam?
Polyurethane (PU) is a high-performance polymer material formed by the polycondensation reaction of polyols and polyisocyanates, known for its excellent mechanical properties and high plasticity.
Its synthesis dates back to 1937 when Professor Byaer first synthesized linear polyurethane resin using 1,6-hexamethylene diisocyanate and 1,4-butanediol as raw materials.
The main polyurethane products include the following: foam plastics, elastomers, fiber plastics,coatings, adhesives, and polyurethane sealants, among which foam plastics account for the largest proportion.
Polyurethane foam is a polymer formed by the mixing of isocyanate and polyether as the main raw materials, with the help of blowing agents, catalysts, flame retardants, and other additives, through specialized equipment and high-pressure spraying on-site foaming.
PU foam is a high-performance cushioning material known for its excellent elasticity, elongation, compressive strength, and flexibility, as well as good chemical stability.
They are versatile materials used as structural building components, molded parts, flexible cushion materials, and adhesive/sealants .
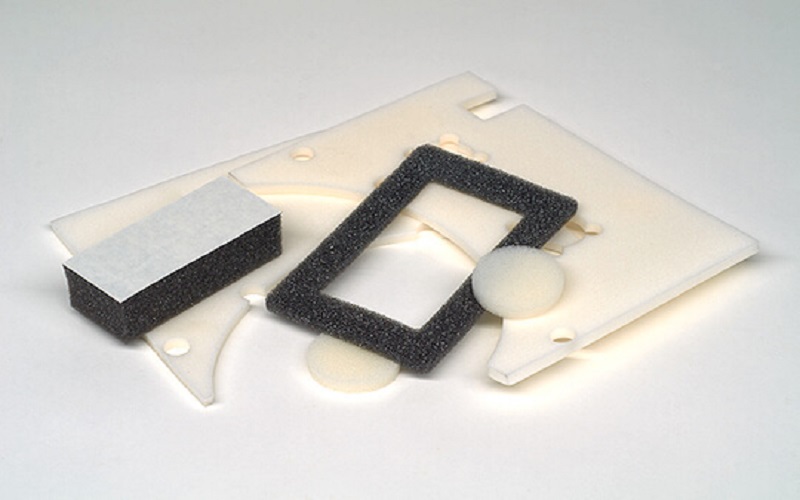
Types Of PU Foam
Based on its structure and performance, polyurethane foam can be divided into two foam types: flexible foam and rigid foam,the market share between these two types is largely equal.
Flexible Polyurethane Foam
Structure: Mostly open-cell structure, divided into skinned and non-skinned types.
Performance: Features low density, good elasticity and resilience, sound absorption, breathability, and thermal insulation.
Applications: Flexible polyurethane foam commonly used in sofa furniture, pillows, cushions, toys, clothing, and soundproof linings.
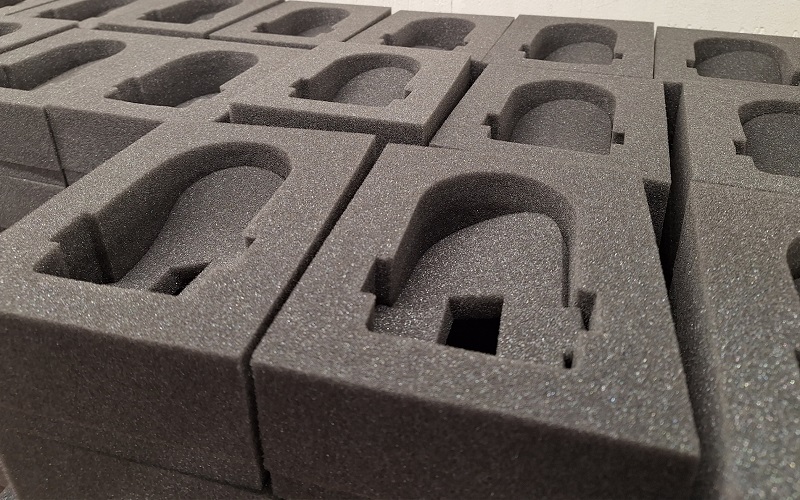
Rigid Polyurethane Foam
Structure: Closed-cell structure with low thermal conductivity (0.022~0.033W/(m*K)), the lowest among all insulation materials.
Performance: Offers thermal insulation and waterproofing functions, highly energy-efficient, shock-resistant, compressive, and heat-insulating.
Applications: Rigid foam products mainly used for building exterior wall insulation, integrated roof waterproofing and insulation, cold storage thermal insulation, and pipeline insulation materials.
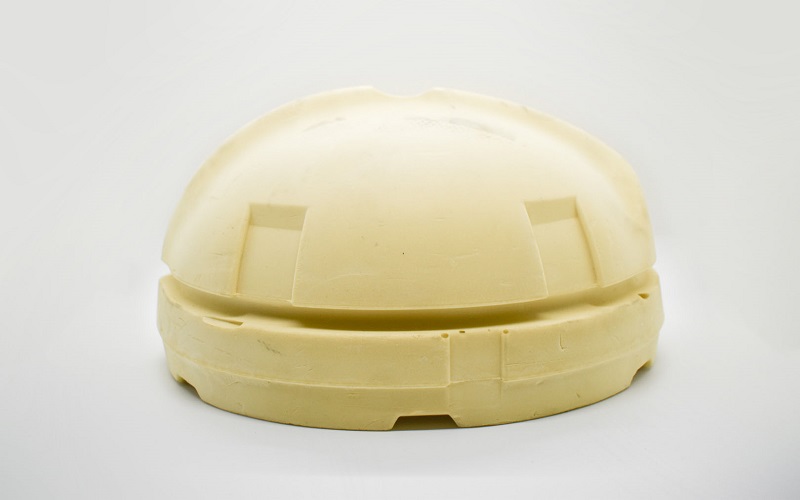
Physical Properties of Polyurethane Foam
The physical properties of PU Foam are the core advantage behind its widespread applications.
Firstly, it boasts an extensive density range, from ultra-light foams as low as 10 kg/m³ to high-density materials exceeding 100 kg/m³, allowing precise adjustments tailored to specific uses.
Secondly, PU Foam exhibits remarkable elasticity and resilience, particularly in its flexible form, where it swiftly regains its original shape after compression.
Additionally, its excellent thermal insulation stems from gas trapped within its closed-cell structure, with thermal conductivity typically ranging between 0.02 and 0.04 W/(m·K), making it an ideal choice for insulation purposes.
Open-cell foams, on the other hand, excel in sound absorption, finding frequent use in noise control applications.
In terms of durability, PU Foam demonstrates good resistance to water, oil, and various chemicals, though prolonged exposure to ultraviolet light may lead to signs of aging.
Its low density and thermal conductivity combined with its mechanical properties make them excellent thermal and sound insulators, as well as structural and comfort.
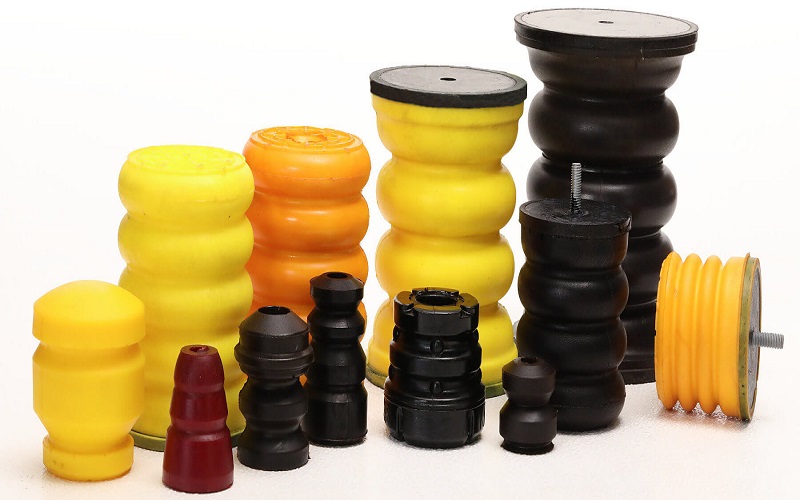
How Does Polyurethane Foam Work?
Polyurethane foam is the result of a chemical reaction when its two components are mixed. The basics of the reaction are the expansion and and curing process that define its structure and performance.
The Chemical Reaction
At its core, PU Foam is created by combining two primary ingredients: an isocyanate (such as MDI or TDI) and a polyol. When these two liquids mix, they undergo an exothermic reaction—an addition polymerization—forming the polyurethane polymer.
This reaction generates heat, which plays a critical role in the next step. Simultaneously, a blowing agent (often water or a specialized gas like pentane) is introduced.
When water reacts with the isocyanate, it produces carbon dioxide gas, while other blowing agents vaporize under the reaction’s heat. These gases create bubbles within the mixture, initiating the foaming process.
Expansion and Structure Formation
As the chemical reaction progresses, the carbon dioxide or vaporized blowing agent expands the polymer matrix, causing it to rise and form a foam. The structure of this foam depends on additional factors, such as surfactants and catalysts.
Surfactants stabilize the bubbles, ensuring a uniform cell structure, while catalysts control the reaction speed, balancing the foam’s expansion and solidification. Depending on the formulation, PU Foam can be formed into open or closed cell structures.
Open-Cell vs. Closed-Cell Foam
The resulting foam can be either open-cell or closed-cell, each with distinct properties. Open-cell foam has interconnected pores, allowing air and sound to pass through easily, making it excellent for acoustic insulation.
Closed-cell foam, with sealed bubbles, traps gas inside, enhancing thermal insulation and moisture resistance. This structural versatility is a key reason for PU Foam’s widespread use.
How It Works in Practice
Once cured, PU Foam’s functionality stems from its cellular structure. In theory, foam blocks of several kilometres in length could be produced this way.
In reality, the foam blocks are typically cut at a length of between 15 and 120m, cured and stored for further processing. Cured foam can only be cleaned by mechanical ways like utility knife etc.
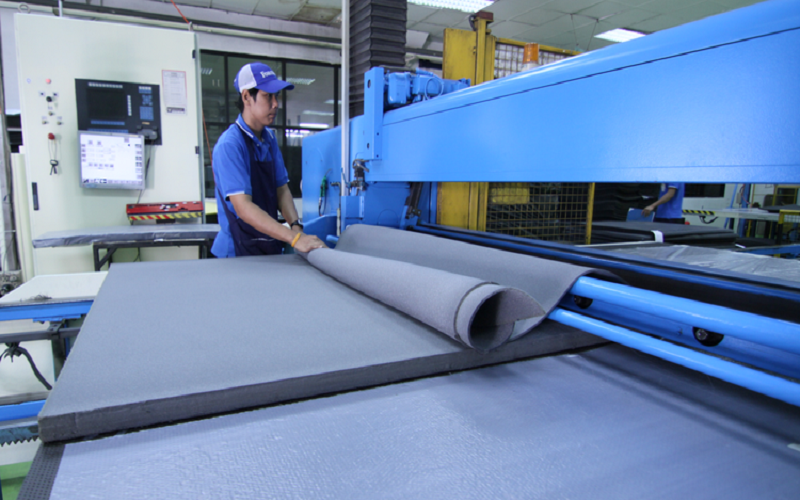
What Are PU Foam Used for?
Polyurethane foam are specially formulated by developers to meet a diverse range of physical, thermal and electrical properties.
Polyurethane foam manufacturers are able to adjust the density, firmness, and other properties of polyurethane foam to suit specific applications.
Automotive Industry
Flexible and semi-flexible polyurethane foams are used extensively for interior components of automobiles , in seats, headrests, armrests, roof liners, dashboards and instrument panels.
Packaging
PU foam is typically used for cushioning packaging or padding materials for high-end precision instruments and valuable equipment. It can also be made into protective packaging containers with excellent cushioning properties.
Construction
Polyurethane foams can be formulated to have excellent adhesion to different surfaces.Rigid PU Foam is used for thermal insulation in walls, roofs, and floors, as well as sealing gaps around windows and doors. Its closed-cell structure also provides moisture resistance for foundations and pipes.
Furniture And Bedding
Flexible polyurethane foam is a cornerstone in the furniture and bedding industries, valued for its ability to provide comfort, support, and durability.
It is widely used in the production of mattresses, sofa cushions, and upholstered chairs, where its adjustable firmness and resilience cater to a variety of consumer preferences.
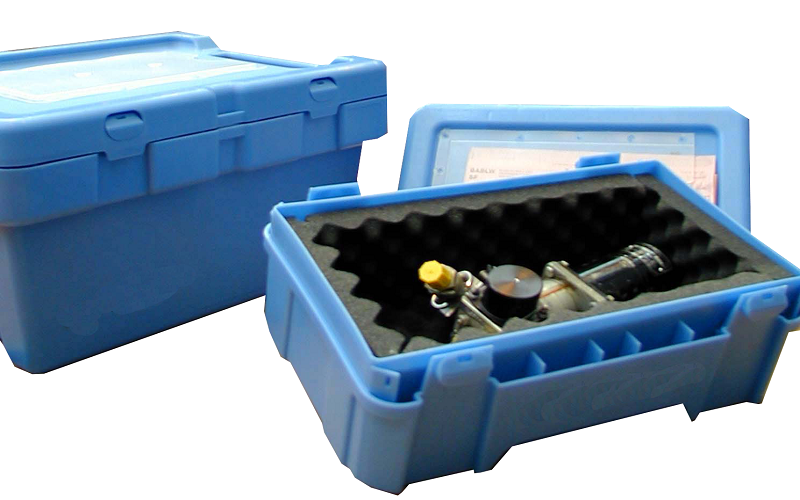
Is PU Foam Safe?
During the production and processing of polyurethane foam , toxic substances like isocyanates may be released. Inhaling these can irritate the respiratory system, causing coughing, wheezing, or shortness of breath, and in severe cases, leading to breathing difficulties or suffocation.
Direct contact with polyurethane may trigger skin allergic reactions, such as redness, itching, or rashes, which could worsen into dermatitis or eczema if untreated. Wearing gloves and protective gear is recommended to avoid skin exposure.
To meet fire safety standards, many PU Foam commercial products include flame retardants to enhance fire resistance. However, untreated PU Foam burns easily in fires, releasing toxic fumes like carbon monoxide and hydrogen cyanide.
Even with retardants, combustion byproducts may remain hazardous. Thus, selecting products meeting fire safety standards is critical in high-risk settings like buildings or vehicles.
Overall, PU Foam’s safety hinges on production quality, usage conditions, and proper precautions. Opting for high-quality, standards-compliant products and adhering to usage guidelines are key to ensuring its safety.
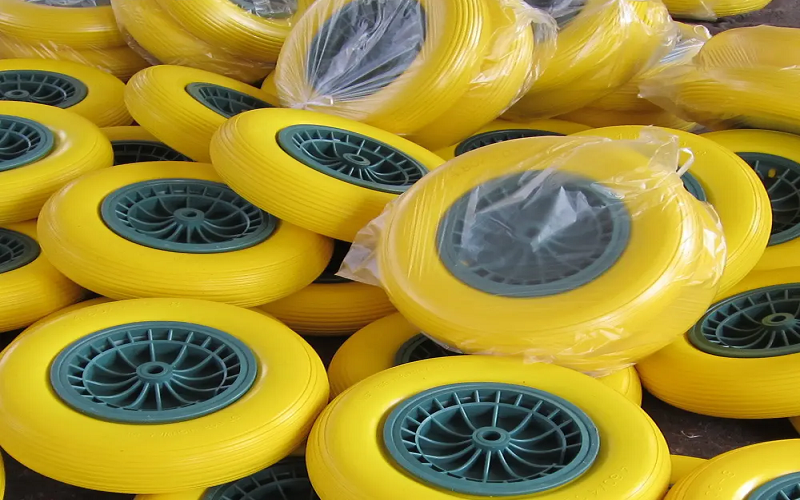
Advantages of PU Foam
PU Foam stands out among materials due to its unique combination of properties, making it indispensable in industrial and everyday applications. Its key advantages include:
Versatility and Customizability
PU Foam can be tailored through formulation and processing, ranging from soft to rigid and low to high density. This adaptability suits diverse needs, such as soft foam for comfortable mattresses or rigid foam for sturdy insulation panels.
Excellent Thermal Insulation
Rigid PU Foam, with its closed-cell structure and low thermal conductivity (typically 0.02-0.04 W/(m·K)), excels as a thermal insulator. It’s widely used in building insulation and cold-chain equipment, reducing energy loss effectively.
Superior Elasticity and Comfort
Flexible PU Foam offers excellent elasticity and resilience, quickly regaining its shape after compression. This makes it ideal for furniture, mattresses, and car seats, delivering lasting comfort.
Lightweight Strength
PU Foam is lightweight yet strong, particularly in its rigid form. This quality is valuable in automotive and aerospace industries, where it reduces weight while maintaining structural integrity.
Effective Sound Absorption
Open-cell PU Foam absorbs sound waves efficiently, reducing noise levels. It’s commonly used in acoustic insulation for buildings, car interiors, and industrial settings, creating quieter environments.
Ease of Processing and Adhesion
PU Foam is easily molded through spraying, casting, or molding into complex shapes. Its ability to adhere firmly to surfaces during expansion makes it excellent for sealing and filling applications.
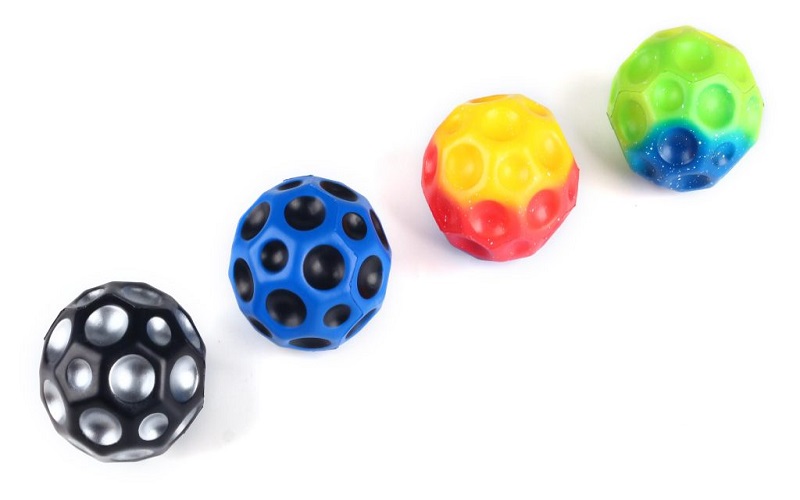
Disadvantages Of PU Foam
The disadvantages of polyurethane foam (PU Foam) primarily include the following aspects:
Flammability
Polyurethane foam has poor thermal conductivity, which can lead to heat accumulation in localized areas. Untreated PU Foam has a low oxygen index and high flammability. In a fire, it burns rapidly, releasing large amounts of toxic smoke and gases, such as carbon monoxide and hydrogen cyanide, significantly increasing the fire’s hazards.
Higher Cost
The production of polyurethane foam involves relatively high costs, resulting in more expensive end products. Additionally, its foaming efficiency decreases at low temperatures, limiting its usability in colder seasons and adding seasonal constraints to its application.
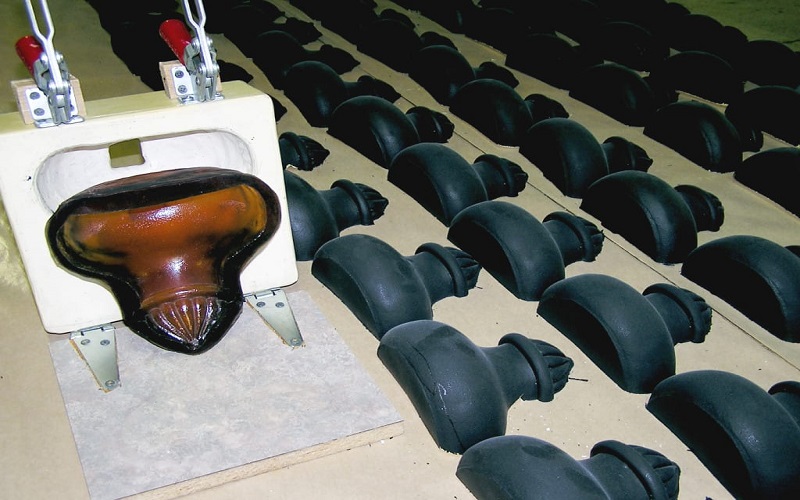
Conclusion
In conclusion, polyurethane foam stands out as an ideal choice for modern energy-efficient buildings due to its high thermal insulation efficiency, optimal space utilization, long-lasting insulation lifespan, excellent flame retardant properties, and ease of installation.
With continuous technological advancements and growing environmental awareness, the application prospects of polyurethane foam will be even more promising.