As the “golden plastic,” Polysulfone (PSF) occupies an important position among many high-performance engineering plastics due to its outstanding thermal stability and mechanical properties.
Consequently, PSF injection molding has become the primary process for manufacturing PSF products in the industry.
This article will take an in-depth look at the core technologies of PSF injection molding and guide molders on how to better utilize the potential of this material.
What is Polysulfone?
Polysulfone (commonly abbreviated as PSF or PSU) is a type of thermoplastic resin with a molecular main chain containing sulfone groups (-SO2-) and sub-aromatic units.
There are three main types: the standard Bisphenol A type PSF (commonly referred to as polysulfone), polyarylsulfone, and polyethersulfone.
In the 1960s, the United States-based company Union Carbide Corporation (UCC) completed the development of PSF and began industrial production in 1965, achieving a production capacity of 4,500 tons per year.
The product was marketed under the trade name Udel®PSU.
In 1976, UCC introduced polyphenylsulfone Radel®R, and in 1983, they launched polyarylsulfone Radel®A.
In 1986, Amoco Polymers acquired the PSF business from UCC. Later in 2001, the business rights were obtained by the Belgian company Solvay, which became a world leader in PSF production.
In 1987, the German company BASF started producing and selling PSF under the brand name Ultrason®S.
By 2004, BASF’s production capacity for PSF had reached 6,000 tons per year.
Currently, the main producer of PSF in Japan is Sumitomo Chemical.
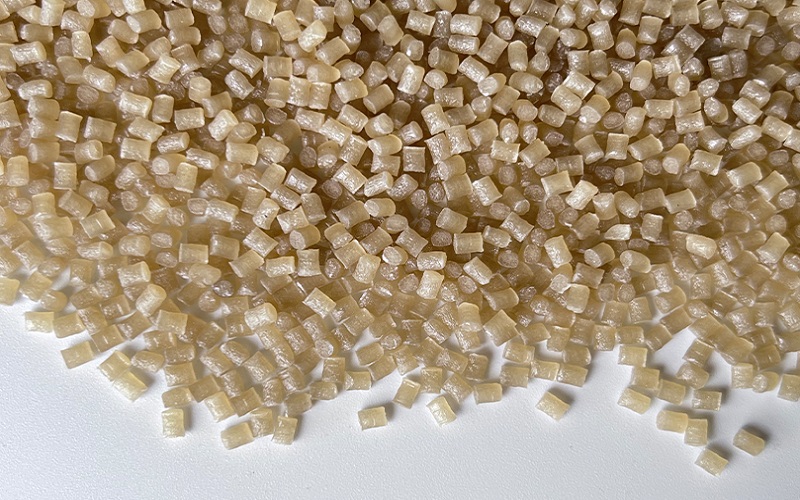
Properties of PSF Materials
Polysulfone (PSF) is an amber transparent solid material with a density of 1.24g/cm3 and a melting point above 280°C.
Mechanical Properties: As a special engineering plastic, the mechanical properties of PSF under high temperature conditions are better than those of general engineering plastics.
And its tensile strength, impact strength, etc. change less in the range of -60~120℃.
Heat resistance: PSF has high heat resistance, take polyethersulfone (PES) as an example, its thermal deformation temperature is 200~220℃, continuous use temperature is 180~200℃, glass transition temperature is 225℃, and it can be used continuously in steam above 100℃.
Creep resistance: PSF has good dimensional stability with little creep at high temperatures.
Flame retardant: PSF can reach UL94 V0 level without adding flame retardant, low smoke, it is one of the special plastics with better flame retardant.
Chemical resistance: PSF is resistant to acids, alkalis, inorganic salts, gasoline, oil, lubricants and Freon.
Safety: PSF is a class of food-grade and hygienic polymer materials recognized by FDA and EU.
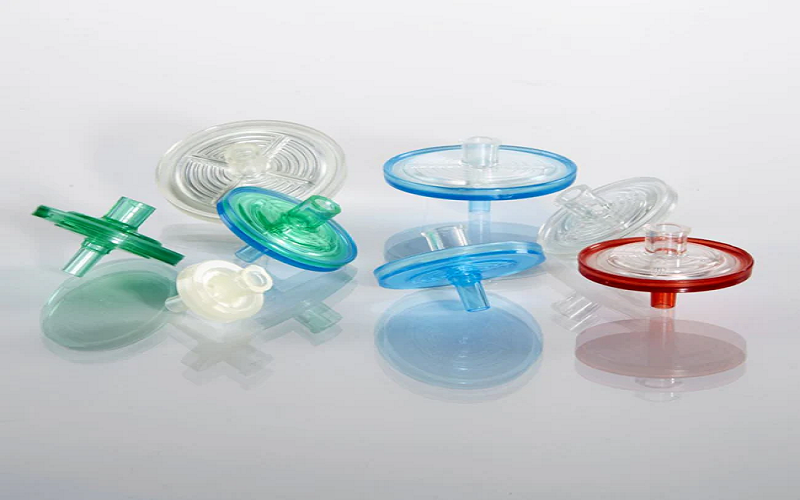
Design of Injection Molded PSF Products And Molds
When designing products and molds made of polysulfone , it’s crucial to consider the following key factors to ensure the quality of the products and the efficiency of production:
Wall Thickness
Due to the poor flowability of PSF melt, the ratio of melt flow length to wall thickness is approximately 80.
Therefore, the recommended wall thickness of PSF products should not be less than 1.5mm, generally more than 2mm. Additionally, since PSF plastic products are sensitive to notches, it’s advisable to use rounded transitions at right angles or sharp corners to avoid stress concentration.
Draft Angle
Given that PSF’s molding shrinkage rate is relatively stable (0.4% – 0.8%) and the shrinkage in the direction of melt flow is consistent with the vertical direction, a draft angle of 50:1 is recommended for ease of demolding.
Mold Surface Treatment
To achieve a glossy and smooth appearance for the products, the surface roughness of the mold cavity should be controlled to be above Ra 0.4.
Runner Design
To facilitate the flow of the melt, the main runner of the mold should be designed short and thick, with its diameter at least half of the product thickness, and a slope of 3° – 5°.
The cross-section of the sub-runners should preferably be circular or trapezoidal to minimize bending.
Gate Design
The form of the gate can vary according to the specific requirements of the product.
However, the gate size should be as large as possible, and the straight part of the gate should be as short as possible, ideally between 0.5 – 1.0mm.
The feed gate should be located on the thicker sections of the product to ensure stable material flow.
Venting Design
Due to the high injection pressure and fast injection rate required for PSF, especially for thin-walled products, effective vent holes or slots should be set up to ensure timely air evacuation from the mold.
The depth of these vents or slots should be controlled to be less than 0.08mm to prevent melt leakage while allowing effective venting.
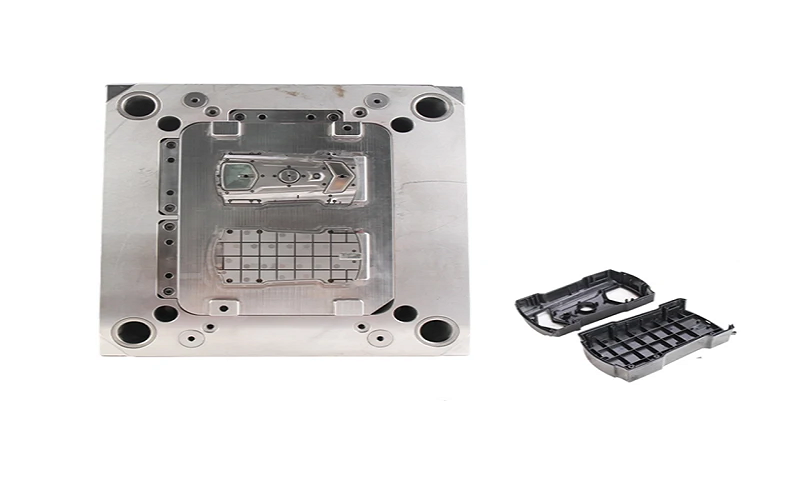
Parameter Settings for PSF Injection Molding
The moldability of PSF plastic is similar to that of PC (polycarbonate), with poor thermal stability, beginning to decompose at 360 degrees Celsius.
Given that the moisture absorption rate of PSF material is between 0.2% to 0.4%, it must be pre-dried using air circulation at 120 to 140°C for 4 to 6 hours.
In the actual injection molding process, adjustments are mainly made based on the following injection molding conditions.
Cylinder temperature | 300℃ | Mold temperature | 120-140℃ |
Injection pressure | 100-140MPa | Injection rate | low |
Screw speed | 15~45 r/min |
|
|
It should be noted that PSU is an amorphous polymer and the products are transparent. Therefore, mold release agent should be used as little as possible or not used in molding;
After molding can take annealing treatment glycerin bath annealing treatment, 160 degrees, 1-5 minutes; or take air bath 160 degrees, 1-4 hours.
The annealing time depends on the size and wall thickness of the product.
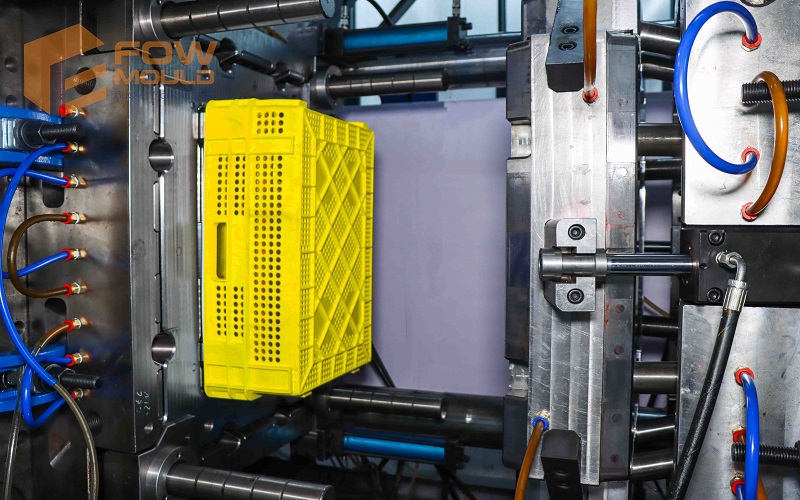
Applications of PSF Plastic Molding
Medical Industry
PSF material is non-cytotoxic and can withstand sterilization methods such as high-pressure steam, ethylene oxide, and low temperature, complying with ISO10993 standards.
It is suitable for use in Class II and Class III medical devices.
Due to its lightweight, X-ray transparency, and high design flexibility, PSF material is gradually replacing metal in medical applications, including sterilization trays, surgical retractors, dental instruments, etc.
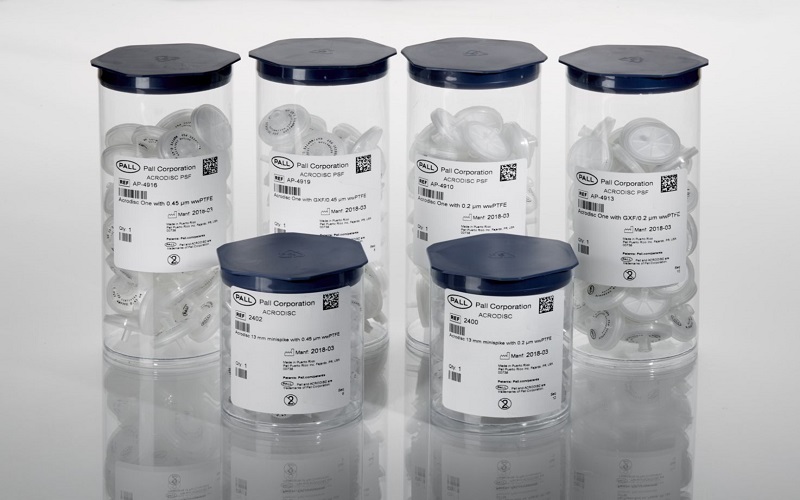
Food Contact
PSF material, known for its stable performance and non-toxicity, meets the regulatory requirements of the U.S.
Food and Drug Administration and the European Commission for food and contact applications.
It is widely used in food contact areas, such as baby bottles, microwave cooking utensils, coffee filters, egg cookers, breast pump components, beverage and food contact utensils, etc.
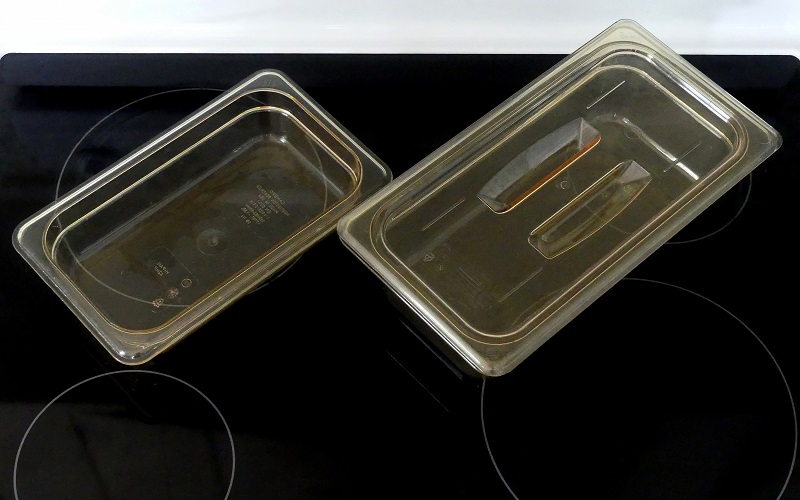
Aviation
In the aerospace industry, PSF injection-molded parts are utilized for their wear resistance and load-bearing properties, producing components like thrust rings, lighting parts, and air conditioning system seals.
Its plasticity and heat resistance make it suitable for protective cover components, electric gears, battery covers, detonators, electronic ignition device components, etc
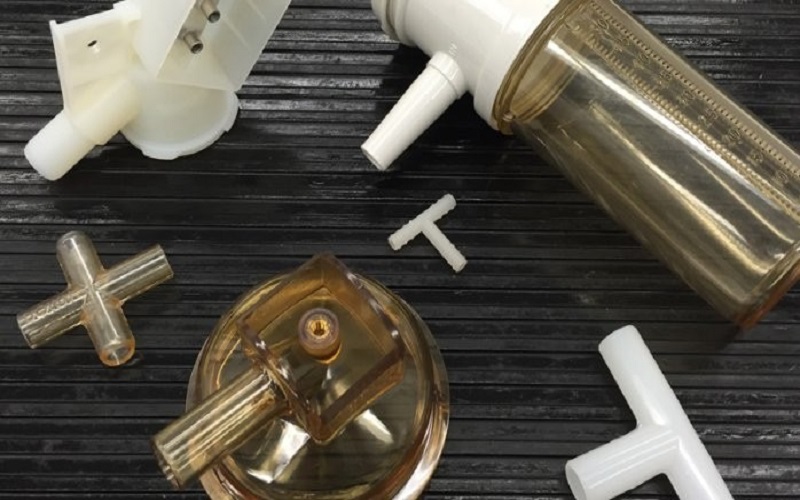
Electronics and Electrical
PSF, with its inherent flame retardancy and excellent heat resistance, is ideal for manufacturing precision-toleranced, rigid, thermally stable, and well-insulated electronic components.
Examples include high-temperature contactors, transformer insulating parts and sleeves, coil frameworks, terminal blocks, printed circuit boards, alkaline battery boxes, and more.
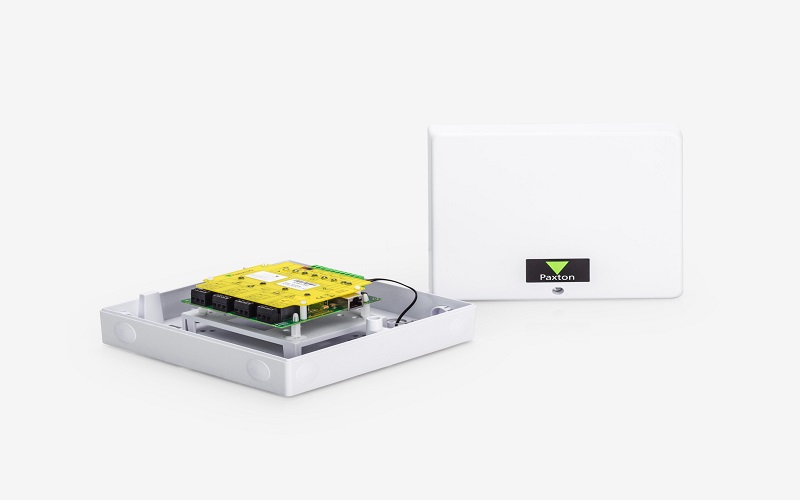
Conclusion
Whether it’s stability under high temperatures, chemical resistance, or safety in special applications like medical equipment and food contact materials, PSF has proven its significance as an injection molding material.
FOWMOULD fully understands these advantages and is eager to offer more professional PSF injection moulding services to our clients, assisting you in seamlessly transitioning from concept to final product.
We look forward to collaborating with you to explore the endless possibilities of PSF in your projects.