With the continuous emergence of new materials and processes, as well as the widespread application of smart manufacturing, PPO injection molding technology maintains its significant position in the manufacturing of high-performance components, providing robust support for the development of related industries.
In the content that follows, we will delve deeper into the specific processes, technical key points, and practical applications of PPO injection molding, enhancing our understanding of this technology.
What Is PPO?
Polyphenylene ether (PPO), also known as polyphenylene ether b in Chinese, is one of the world’s top five general-purpose engineering plastics.
PPO has one of the smallest dielectric constants and dielectric losses among engineering plastics, and is virtually unaffected by temperature and humidity.
PPO is a linear polymer made of 2,6-dimethylphenol through oxygen and oxidative condensation reaction under the action of catalyst. It is usually in the form of earthy yellow powder.
Commonly used is polyphenylene ether synthesized from 2,6-dimethylphenol, with excellent comprehensive performance, the most important feature is that under long-term load.
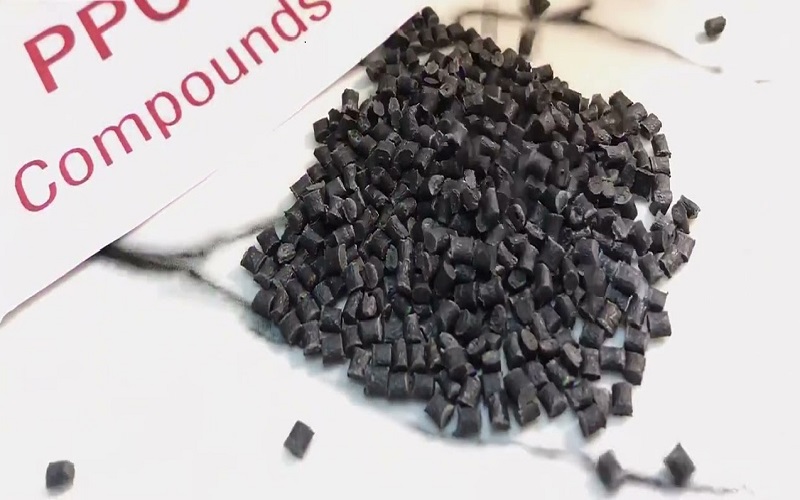
What Are The Properties Of PPO Material?
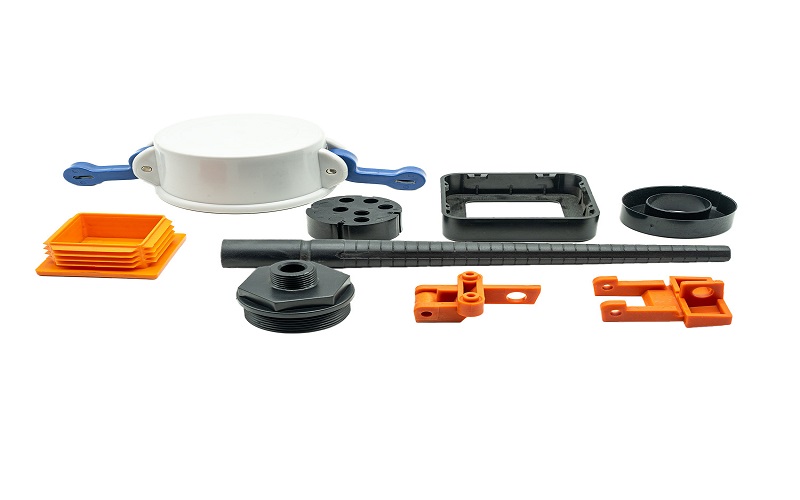
- The appearance is typically in the form of white granules.
- Good electrical properties in a wide range of temperature and frequency change, not hydrolyzed,
- PPO materialcan be used in steam at 120 degrees Celsius, has low water absorption, but tends to crack under stress.
- The load deflection temperature of PPO can be up to 190℃ or more, and the embrittlement temperature is -170℃.
- PPO plastic raw materials dielectric constant and dielectric loss in the engineering plastics is one of the smallest varieties, almost unaffected by temperature, humidity.
Properties of PPO Plastic | |
Density | 1.08g/cm³ |
Shrinkage | 0.5-0.8% |
Melting point | 268℃ |
Oxygen index | 29 |
Heat deflection temperature | 190℃ |
What Are The Advantages And Disadvantages Of PPO Materials?
Polyphenylene Oxide (PPO) is a high-performance engineering plastic with various properties that make it suitable for a wide range of applications. Below are some of the advantages and disadvantages associated with PPO materials:
Advantages
- Excellent electrical properties
- High rigidity and strength
- Flame retardant, high heat resistance
- Non-toxic, transparent, low relative density
Disadvantages
The main shortcomings of PPO are high melt viscosity, poor fluidity, molding processing is more difficult.
In addition, the internal stress of the molded part is large, the molded part is easy to crack, the fatigue resistance is not good, and there is a tendency to change into thermosetting plastic in the long-term storage process.
In order to overcome these shortcomings, PPO can be modified, that is, in which to add an appropriate amount of HIPS blended into, that is, into the MPPO.
On the basis of which can also be added to the short glass fibers and become reinforced MPPO and its performance is more superior.
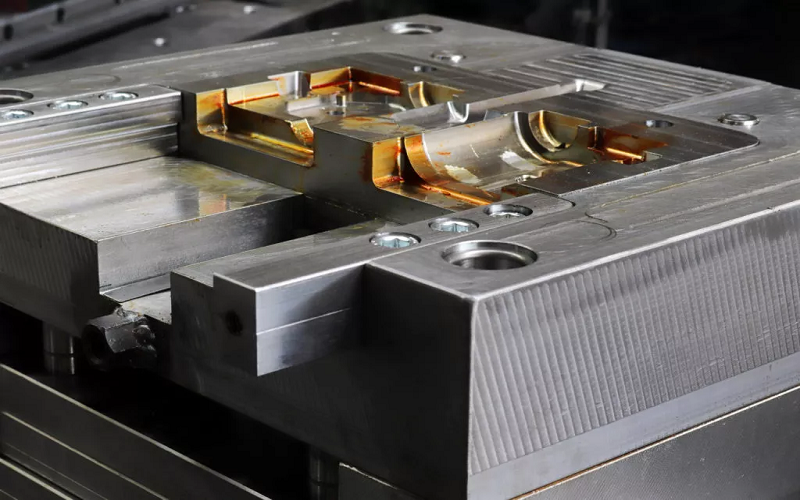
Conditions For PPO Injection Molding
In order to produce high-quality injection molded PPO parts, specific conditions need to be followed to achieve optimal molding results.
Below are the key conditions and considerations for PPO plastic injection molding:
Drying process
PPO is a non-crystalline polymer with a low water absorption rate. However, moisture can lead to defects such as silver streaks and bubbles on the surface of the product.
Therefore, it is recommended to place the raw material in an oven at 80-100℃ for drying for 1-2 hours before use.
Selection of Injection Molding Machine
A screw-type injection molding machine is suitable for molding PPO melt. A straight-through nozzle is preferable, with a diameter of 3-6mm. For the mold’s sprue, a larger taper or a pull-hook is recommended, and the runner should be short and thick.
Injection Temperature
The injection melt temperature of PPO is usually controlled within the range of 270-290℃. PPO has high heat resistance with a thermal decomposition temperature reaching 350℃, and no significant thermal degradation occurs below 300℃. Additionally, the barrel temperature should be controlled at 260-290℃, and the nozzle temperature should be about 10℃ lower than the barrel temperature.
Since PPO melt has a high viscosity, a higher mold temperature should be adopted during injection molding.
Mold Temperature
Generally, the mold temperature is controlled at 100-150℃. If the mold temperature is below 100℃, thin-walled plastic parts may have insufficient filling and delamination issues.
On the other hand, temperatures above 150℃ may lead to defects such as bubbles, silver streaks, and warping.
Injection Pressure
Due to the high viscosity of the PPO melt, high pressure and high-speed injection should be used during molding, and the holding pressure and cooling time should not be too long.
Increasing the injection pressure helps with mold filling.
The general injection pressure is controlled at 100-140 MPa, and the holding pressure is controlled at 40-80 MPa. Adjustments should be made based on specific circumstances.
Injection Speed
Products with long flow paths require rapid injection. However, under such conditions, ensure that the mold has adequate venting.
By carefully controlling these conditions, manufacturers can optimize the injection molding process for PPO, achieving high-quality parts with excellent performance characteristics.
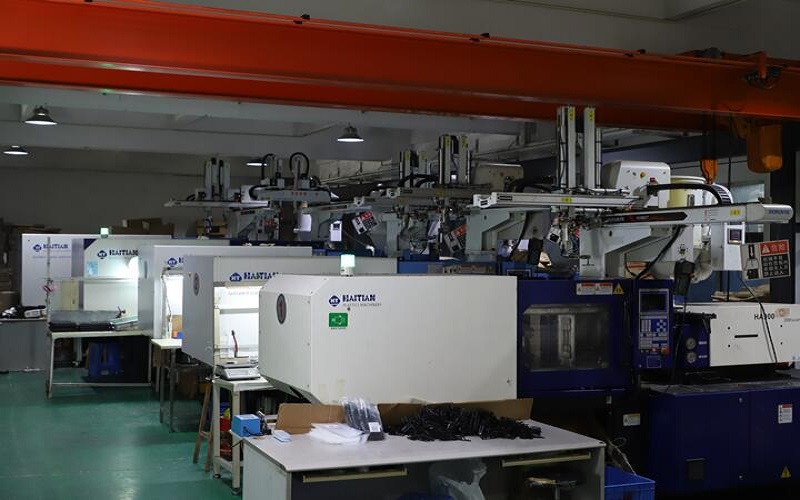
Applications of PPO Plastic Injection Molding
PPO plastic injection molding is used in various industries to produce parts that require a combination of strength, thermal stability, electrical insulation, and chemical resistance.
Its versatility and high-performance characteristics make PPO a preferred material for many demanding applications.
Electronics and Electrical Industry
PPO materials play a crucial role in the electronics and electrical industry. PPO plastic components maintain excellent electrical insulation under conditions of humidity, load, and high temperature.
Therefore, they are commonly used to manufacture connectors, various high-voltage electronic components, and other parts.
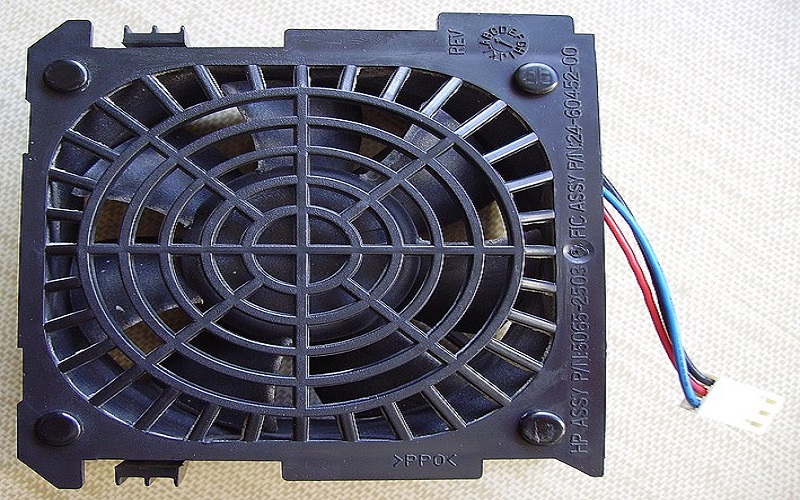
Automotive Industry
Thanks to its impressive impact resistance, wide operating temperature range, paintability, and resistance to stress cracking, PPO material is suitable for various applications.
These include instrument panel components, window frames, shock absorbers, pump filters, and more.
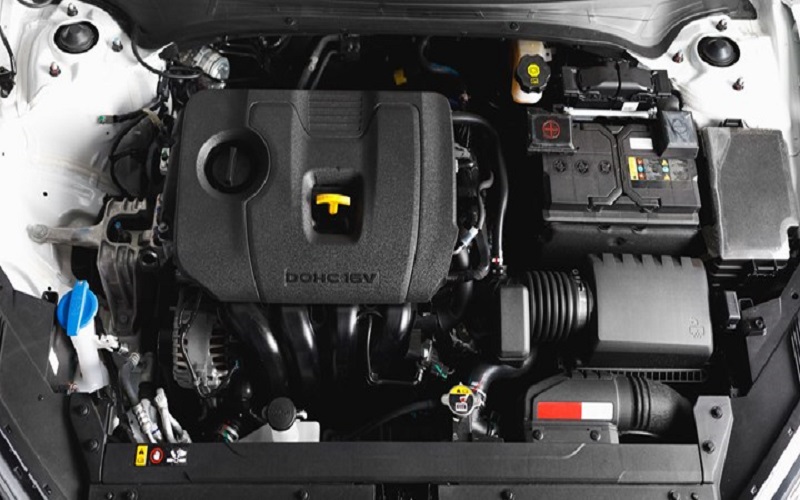
Household Appliances
PPO plastic is often used to process ultra-high frequency electronic components in household products.
For instance, it is utilized in manufacturing parts for televisions, computers, cameras, video tapes, recorders, air conditioners, heaters, rice cookers, and other devices.
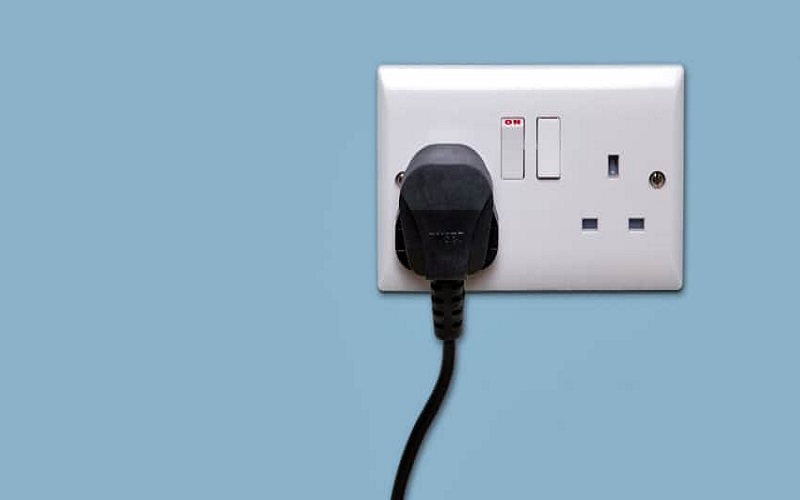
FOWMOULD — PPO Injection Molding Services
With years of experience in PPO injection molding, FOWMOULD leverages advanced injection molding machinery and a professional technical team to provide clients with high-quality PPO plastic parts production services.
FOWMOULD’s one-stop injection molding services encompass the entire process from product design and mold manufacturing to mass production.
In addition, FOWMOULD implements a strict quality control system. Every stage, from raw material inspection to final product shipment, undergoes rigorous testing to ensure the delivery of top-quality products to our clients.
Choosing FOWMOULD for your PPO injection molding services means you will receive high-quality, reliable, and cost-effective plastic components.
We look forward to collaborating with you and achieving success together.
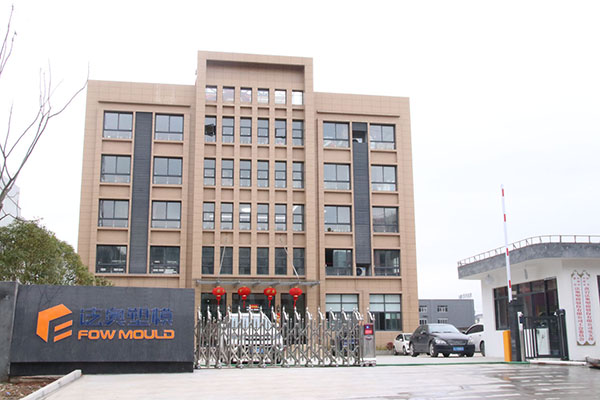
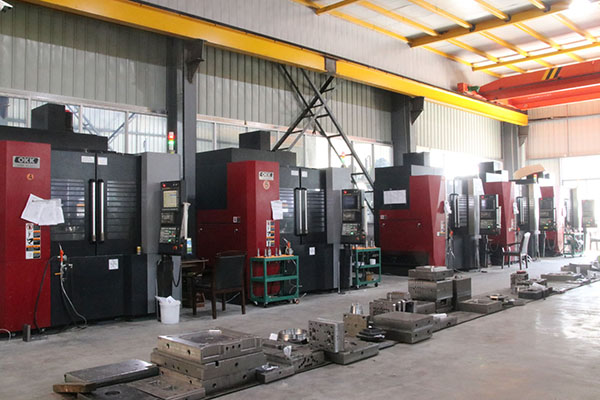