Polyurethane materials, renowned for their exceptional versatility, have become a cornerstone in modern manufacturing due to their ability to be tailored into flexible foams, rigid plastics, or elastomeric components.
This adaptability stems from the chemical interplay of polyols, isocyanates, and additives, enabling PU to meet diverse performance requirements across industries.
Among the various processing techniques, polyurethane injection molding stands out as a highly efficient method for producing precise, durable parts with complex geometries.
This article introduces polyurethane injection molding, exploring its principles, processes, and critical role in delivering high-performance solutions for automotive, medical, consumer goods, and industrial applications, while highlighting its challenges and future potential.
What Is Polyurethane Injection Molding?
Polyurethane (PU) is a polymer compound characterized by repeating urethane groups (-NHCOO-) in its molecular structure.
However, polyurethane is more than light: it’s strong. Tough, durable, load bearing and impact resistant, it performs extremely well in crash tests even when compared with more “solid” materials such as metal.
Renowned for its versatility, PU can be formulated with varying raw materials and ratios to produce a wide range of products, such as polyurethane foams, elastomers, coatings, and adhesives.
Polyurethane injection molding is a manufacturing process that uses PU as the raw material, rapidly curing through chemical reactions within a mold.
It is particularly suited for producing large, structurally complex parts with uneven wall thicknesses, meeting specific material performance requirements like elasticity, rigidity, or self-skinning properties.
PU injection molding primarily encompasses two types: thermoplastic polyurethane injection molding and reaction injection molding (RIM).
Unlike plastic injection molding, the polyurethane reaction injection molding process, or RIM molding techniques , utilize low-viscosity liquid polymers in thermoset – not thermoplastic or thermoforming – processes.
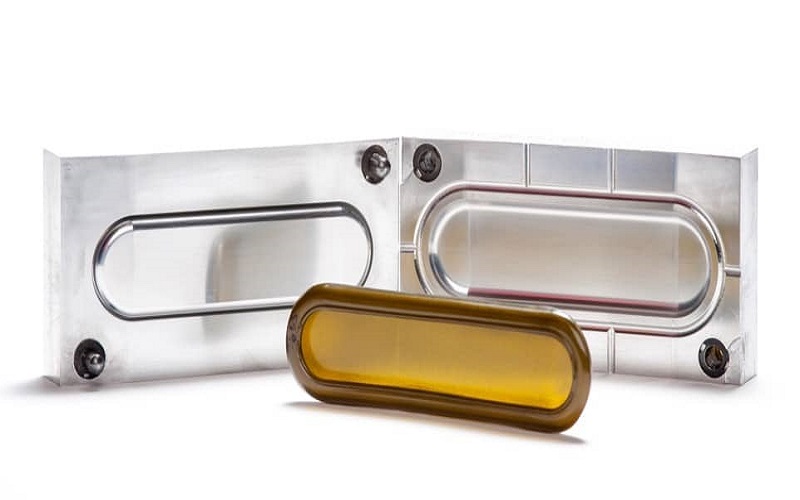
Steps Of Polyurethane Injection Molding Process
The process of polyurethane injection molding involves a series of precise steps to transform raw materials into finished parts. Below is an outline of the key steps:
Mold Crafting
In polyurethane injection molding, mold creation is a core step to ensure part precision and production efficiency. The mold design must precisely accommodate the flow and curing characteristics of PU material, commonly using metal molds and silicone molds.
Metal molds, such as those made of steel or aluminum, are suitable for high-volume TPU injection or RIM production due to their high durability and precision.
In contrast, silicone molds, which are cost-effective and flexible, are often used for low-pressure RIM prototyping or small batch production.
Material Preparation and Mixing
The components are then mixed at a high velocity in an impinging mixer.Raw materials, typically polyols, isocyanates, and additives (e.g., catalysts and stabilizers), are measured and blended.
For TPU, pellets are dried to remove moisture, ensuring optimal material performance.
In rim process, liquid components are mixed in precise ratios to initiate the chemical reaction and chemical reactions.
Maintaining the mixture at controlled temperatures is essential to ensure proper viscosity and reactivity, which are critical for producing high-quality parts.
Injection and Mold Filling
Once the materials are prepared, they are fed into the injection molding machine’s barrel or mixing head. For TPU, the molten plastic is heated to a molten state and injected under high pressure into the mold, filling the mold cavity.
In reaction injection molding, the reactive liquid mixture is injected at lower pressure, allowing the chemical reaction to begin as the mold fills.
The design of the mold ensures uniform filling, accommodating complex geometries and varying wall thicknesses to produce precise and consistent parts using reinforced reaction injection molding.
Cooling and Curing Process
The cooling and curing stages are vital to the pu injection molding process. In TPU molding, the cools and solidifies within the mold, typically using cooling channels to regulate temperature.
For RIM, the material undergoes an exothermic chemical reaction, curing into a solid or foam structure.
Cycle times can vary based on the part size, material type, and mold cooling efficiency, but this stage ensures the durability and stability of the finished part.
Demolding and Post-Processing
Once the material has cooled and cured, the closed mold opens, and the part is removed, often aided by release agents to prevent sticking.
Post-processing steps may include trimming excess material (flash), surface finishing, or painting to enhance the aesthetics and functionality of the part.
Quality checks are conducted to ensure dimensional accuracy and that the material properties meet the required specifications.
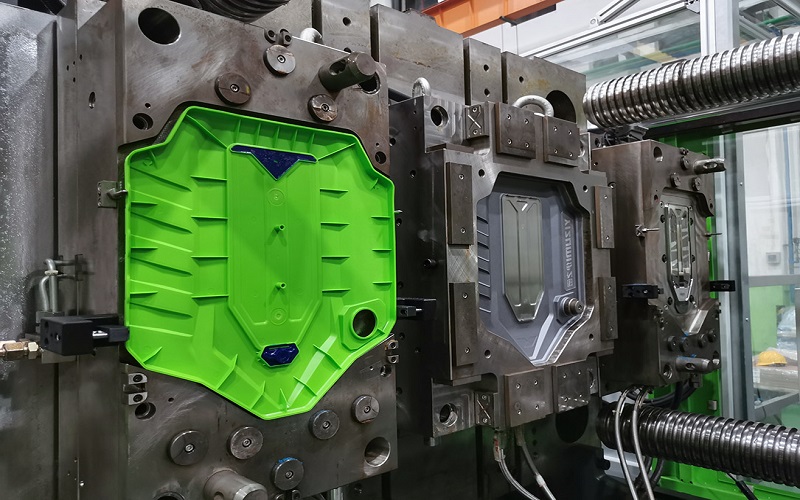
Benefits of Polyurethane Injection Molding
Polyurethane injection molding offers several significant benefits that make it an attractive option for various manufacturing needs.
Cost-Effective Tooling
Aluminum molds are commonly used due to their lower cost compared to steel, significantly reducing tooling expenses. Furthermore, the use of less aggressive material systems leads to reduced wear on molds, prolonging their life and enhancing cost-effectiveness.
Since these liquid polymers require less pressure (~100 psi) and lower temperatures (~90°) than typical ingredients, they can be injected into cost-efficient aluminum molds, lowering tooling costs.
Energy Efficiency
Energy efficiency is a crucial factor in the polyurethane molding process. Operating at low temperatures, the process consumes less energy, contributing to its overall sustainability.
The use of smaller machines further enhances energy savings by minimizing energy usage during operation.
These energy-saving practices not only reduce operational costs but also promote a more environmentally friendly manufacturing process.
Lightweight and Durable Parts
Polyurethane injection molding produces parts that are lightweight yet exhibit excellent durability and abrasion resistance. These parts often outperform those made from traditional thermoplastic materials in terms of resilience and longevity.
The ability to shape parts without drafts or undercuts offers exceptional precision, while maintaining tight tolerances ensures the production of high-quality parts suitable for demanding applications through cnc machining.
Injection-Molding.png)
Key Considerations For Polyurethane Injection Molding
When working with polyurethane injection molding, several key considerations must be taken into account to ensure successful outcomes.
These include material selection, design flexibility, and quality control. Addressing these factors can help manufacturers achieve the desired properties and performance in their finished products.
Material Selection
Selecting the right material based on application requirements is crucial for the success of the molding process.
Polyurethane resins are particularly favored for medical applications due to their exceptional biocompatibility and capacity for long-term implantation. Its impressive tensile strength and flexibility make it suitable for demanding environments, such as load-bearing implants.
This organic polymer is a highly-resistant elastomer that you can use to create some of the most intricate designs for an array of industries.
Design Flexibility
Designing for manufacturability is critical to producing parts that meet specified quality and functionality standards.
Consistent uniform wall thickness ensures part consistency, proper stress distribution, and reduces defect risks. Custom mold design and material modifications enable the creation of complex geometries and features in molded parts, providing significant design process flexibility.
Designers must also account for dimensional changes during curing, as urethanes tend to shrink, affecting the final part’s dimensions and tolerances.
Quality Control
Thorough quality checks are vital to maintaining tight tolerances throughout the polyurethane molding process. This ensures that the final product meets the required specifications and maintains high quality products standards.
Quality control measures are critical for achieving consistent results, especially in low volume production runs where precision and accuracy are paramount.
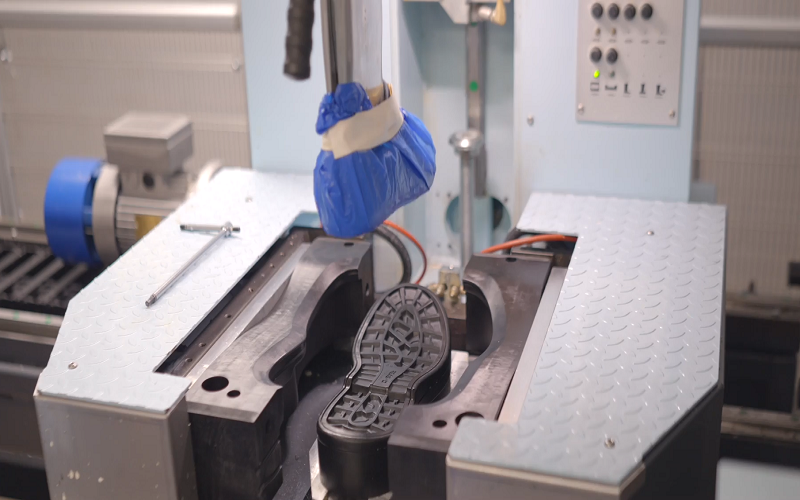
Applications of Polyurethane Injection Molding
Polyurethane injection molding is ideal for producing components that demand precision, durability, and consistency.
Here are some key applications of polyurethane injection molding :
Automotive Industry
Polyurethane injection molding is integral to manufacturing durable, lightweight parts such as bumpers, dashboards, seat cushions, and seals.
Its flexibility in producing both rigid and elastomeric components enhances vehicle safety, comfort, and fuel efficiency, with RIM often used for complex exterior panels and TPU for interior fittings.
Medical Devices
Polyurethane’s biocompatibility makes it an ideal material for medical devices. It is used to create catheters, prosthetics, and other medical components that must meet strict safety and performance standards.
The injection molding process allows for the creation of intricate geometries with high precision, ensuring that medical devices meet tight tolerances and function effectively.
Additionally, polyurethane’s chemical resistance is crucial for devices that must withstand sterilization processes.
Electronics and Consumer Goods
Polyurethane injection molding is also widely used in electronics and consumer goods. It allows for the production of complex electronic components with high precision. In consumer goods, polyurethane enhances the durability and aesthetic appeal of products such as phone cases and household appliances.
Urethane casting is often used for rapid prototyping and iterative designs, making it an ideal choice for developing new products quickly.
Industrial Parts
In industrial settings, the process manufactures robust components like conveyor belts, gaskets, rollers, and insulation panels. Polyurethane’s resistance to abrasion, chemicals, and extreme conditions ensures long-lasting performance in heavy machinery and infrastructure applications.
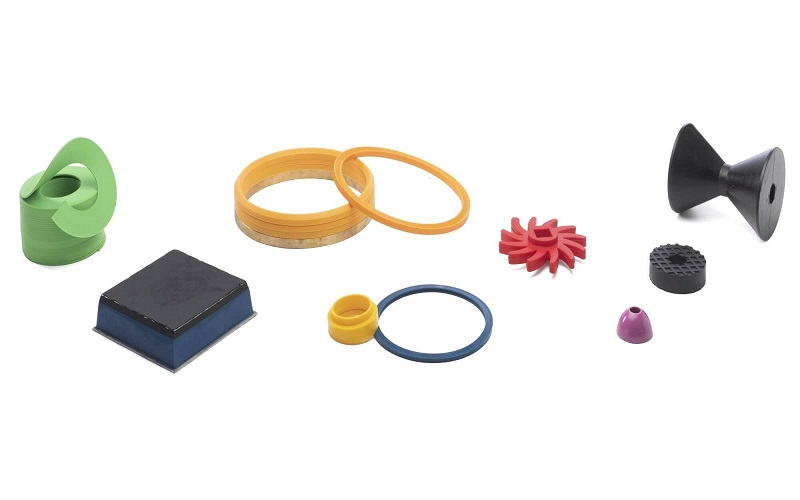
Comparing Polyurethane Injection Molding With Other Processes
Comparing polyurethane injection molding with other manufacturing processes provides valuable insights into its unique properties and limitations.
Here’s how it compares to plastic injection molding and urethane casting:
Polyurethane Injection Molding vs Plastic Injection Molding
Polyurethane injection molding surpass plastics in terms of longevity and resistance, particularly in petrochemical environments.
Unlike thermoplastic materials used in plastic injection molding, thermoset PUR used in polyurethane injection molding cannot be remelted, offering greater resilience and durability.
While both processes can achieve fine details and tight tolerances, polyurethane injection molding often has higher startup costs due to the need for hard molds.
Urethane Casting vs. Polyurethane Injection Molding
Both polyurethane injection molding and urethane casting are molding technologies used to produce plastic parts, but they follow distinct Design for Manufacturing (DFM) guidelines.
Injection molding tooling is typically more costly, often significantly higher than urethane casting tooling, which ranges from a few hundred to a few thousand dollars.
Polyurethane injection molding is well-suited for production volumes between 100 and 100,000 parts, while urethane casting excels in lower-volume runs.
Urethane casting is particularly advantageous for prototyping or small-batch production due to its soft tooling, which provides speed, flexibility, and cost-effectiveness.
However, achieving tight tolerances in urethane casting is challenging, as flexible silicone molds can deform under vacuum pressure, unlike the rigid molds used in injection molding.
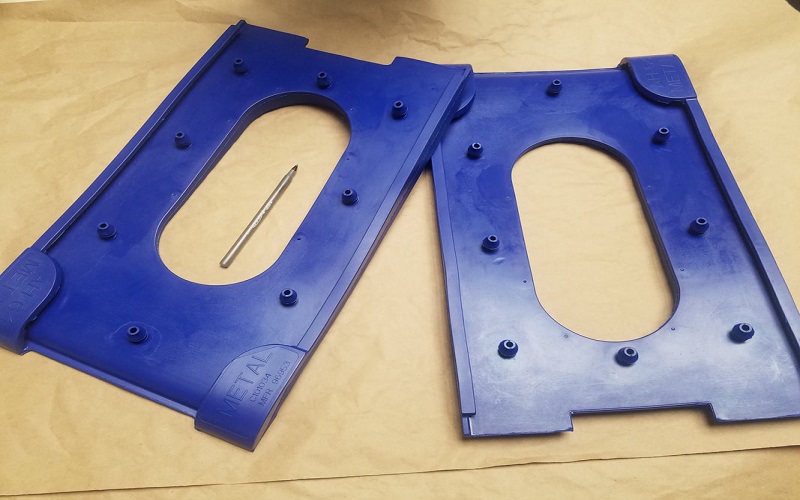
Summary
Polyurethane injection molding stands as a testament to the advancements in manufacturing technologies, offering unmatched versatility, efficiency, and performance.
By understanding the intricacies of the polyurethane molding process, from material preparation and mixing to injection, cooling, curing, and post-processing, manufacturers can harness its full potential to produce high-quality components across various industries.
The benefits of cost-effective tooling, energy efficiency, and the production of lightweight yet durable parts make this process a preferred choice for many applications.
Comparing polyurethane injection molding with other processes, such as plastic injection molding and urethane casting, further underscores its unique advantages.
As we look to the future, the continued evolution of this technology promises even greater innovations and efficiencies in manufacturing.