As materials that are omnipresent in modern life, plastics are given considerable attention due to their diverse characteristics and wide range of applications.
Among the many types of plastics, Polycarbonate (PC) and Polypropylene (PP) are undoubtedly two of the most common and important plastic materials.
They exhibit unique advantages in their respective fields, but also have some limitations.
This article will provide a detailed comparative analysis of PC and PP plastics from multiple aspects,to help you make an informed decision in material selection for your project.
What Is Polypropylene?
Polypropylene is a polymer formed through the polymerization reaction of propylene, making it a semi-crystalline thermoplastic plastic.
PP appears as a white, waxy substance that is non-toxic and odorless, lighter and more transparent than PE plastic, making it the lightest of the commonly used resins.
Based on the spatial position of the -CH3 group in the polypropylene molecule, it can be classified into isotactic polypropylene, syndiotactic polypropylene, and atactic polypropylene.
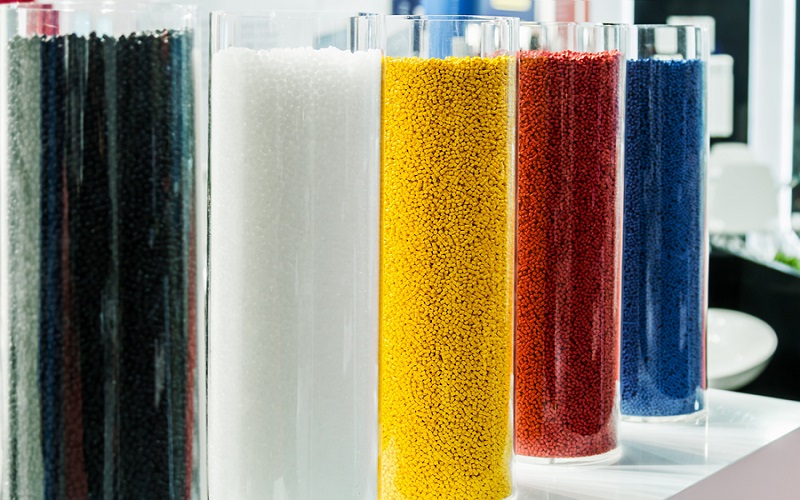
What Is Polycarbonate?
Polycarbonate (abbreviated as PC) is a high molecular polymer that contains carbonate groups in its molecular chain, also known as PC plastic.
Based on the structure of the ester group, it can be divided into several types, including aliphatic, aromatic, and aliphatic-aromatic.
Among these, due to the lower mechanical properties of aliphatic and aliphatic-aromatic polycarbonates, only aromatic polycarbonate has achieved industrial production.
Due to the unique structure of polycarbonate, it has become the fastest-growing general engineering plastic among the five major engineering plastics.
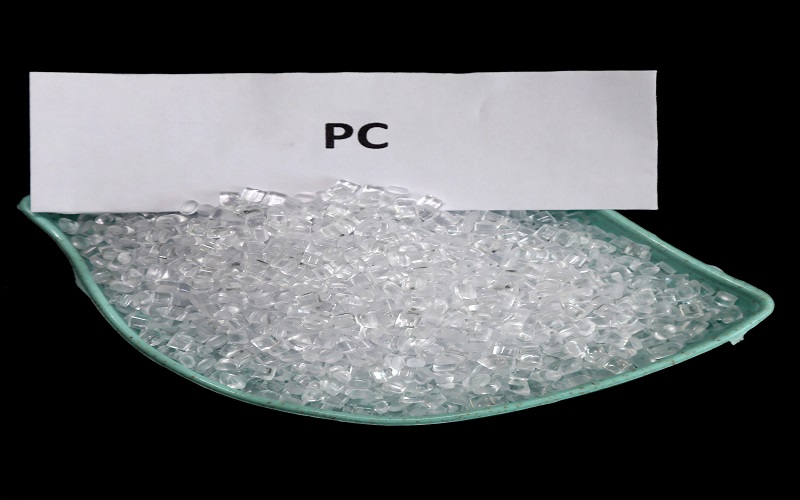
Polypropylene vs Polycarbonate:Properties
Here’s a summary of the key properties for both materials:
Mechanical Properties
PP has good tensile strength and rigidity, but poor impact strength, especially at low temperatures where its resistance to impact is particularly low.
PC, while possessing certain toughness, also has a degree of rigidity, good dimensional stability in formed products, but the downside is poor fatigue and wear resistance.
Chemical Resistance
PP exhibits excellent chemical stability, showing inertness to most acids, bases, salts, and oxidizers.
Its resistance to water is particularly noteworthy, with only a few strong oxidizers such as fuming sulfuric acid causing it to change.
PC can withstand weak acids, weak bases, neutral oils, and some organic chemical solvents.
However, it has insufficient hydrolysis stability and will turn yellow upon prolonged exposure to ultraviolet light.
Thermal Performance
Polypropylene has good heat resistance, with a continuous use temperature range of 110-120°C. It does not deform at 150°C without external force applied, but becomes brittle at temperatures below -35°C.
The thermal decomposition temperature of polycarbonate is above 300°C, with a long-term working temperature up to 120°C, and a heat distortion temperature of 135~145°C.
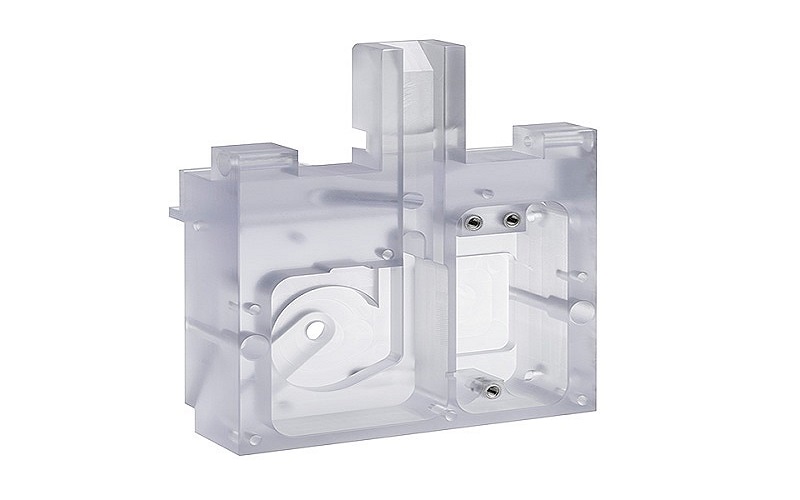
In the table below, we have listed the comparative physical properties of polypropylene and polycarbonate:
Properties | Polypropylene | Polycarbonate |
Density (g/cm³) | 0.89-0.91 | 1.18-1.22 |
Water Absorption (%) | <0.01 | 0.15-0.35 |
Tensile Strength (MPa) | 30-40 | 60-70 |
Flexural Strength (MPa) | 42.0-56.0 | 80-90 |
Heat Distortion Temperature (℃) | 100-116 | 126-135 |
Impact Strength (kJ/m²) | 2.2-2.5 | 50 |
Polypropylene vs Polycarbonate:Applications
Since both PP and PC have their own unique properties, they are also suitable for different industry sectors.
Main Application Areas Of Polypropylene
Packaging
Polypropylene is favored for food packaging like containers and caps, thanks to its light weight and chemical resistance.
Consumer Goods
Injection molding polypropylene parts known for its heat and chemical resistance, is widely used in creating durable household items like kitchenware and appliances.
In addition, the manufacturing of plastic water cups often favors PP plastic .
Automotive Components
Polypropylene, with its low cost, good mechanical properties, and corrosion resistance, is used in the manufacture of automotive parts, including bumpers, interiors, dashboards, and battery boxes.
Fiber Products
PP fibers can be used to make fiber products for decoration, industrial, and clothing fields, such as carpets and ropes.
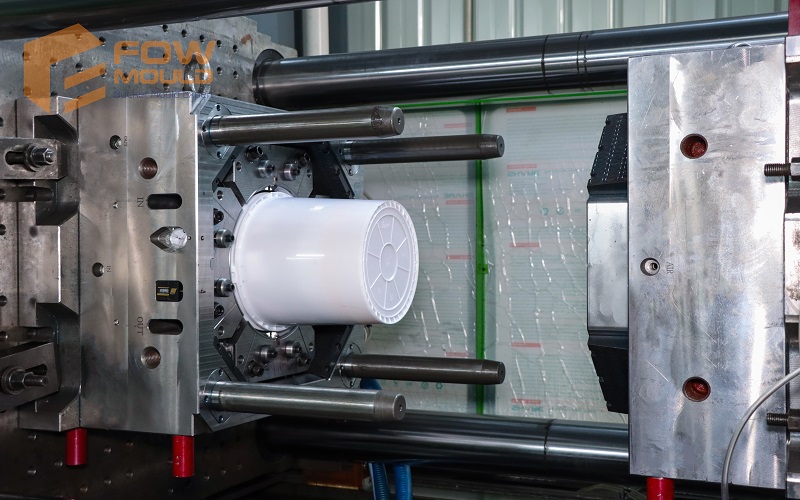
Main Application Areas Of Polycarbonate
Electronics
Polycarbonate is used for insulating parts, such as connectors and battery casings, due to its excellent insulation properties.
Optical Lenses
PC lenses are extensively used in automotive lighting and commercial lighting, thanks to their clarity and durability.
Automotive
With its high impact resistance, polycarbonate molding part is ideal for making various car parts like dashboards and bumpers.
Medical Devices
PC’s resistance to sterilization processes makes it suitable for medical containers and surgical instruments.
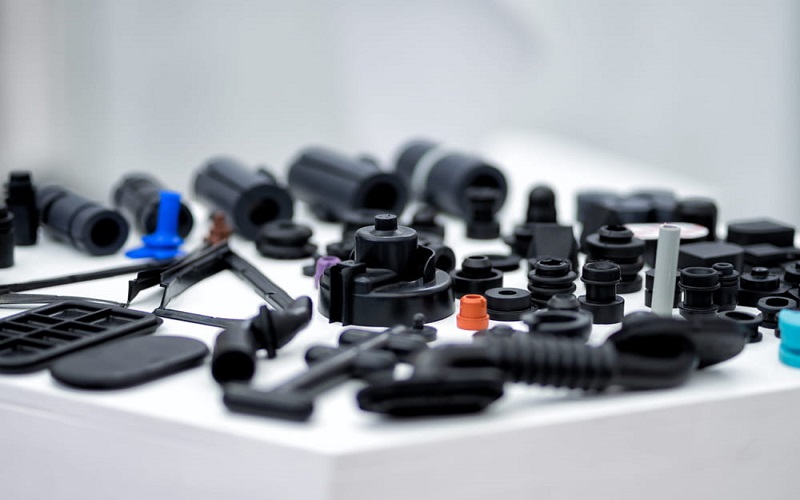
Polypropylene vs Polycarbonate:Safety Competition
With the widespread use of PP plastics, concerns about the safety of its products have emerged: Is polypropylene safe?
In reality, the safety of polypropylene has been widely recognized, especially in applications involving direct contact with food and use in medical facilities.
In the plastic symbols, the number 5 stands for polypropylene, making it the only plastic deemed safe for microwave use.
Food-grade PP material is capable of withstanding high temperatures without releasing toxic substances, ensuring its safety for infants and the general population alike.
It’s important to note that PP plastic products are prone to aging and cracking under exposure to ultraviolet light. Therefore, it’s advisable to timely replace items made from PP material to prevent any potential impact on human health.
Polycarbonate is highly valued for its strength, transparency, and heat resistance in applications such as medical equipment and eyeglasses.
However, the potential release of Bisphenol A , especially in food contact applications, has made the safety of polycarbonate a topic of discussion.
For non-food applications, PC remains a safe choice, but for food contact, it is recommended to seek BPA-free alternatives or other materials to avoid potential risks.
However, it’s important to note that PC material may release harmful substances at high temperatures, so it is not recommended for long-term storage of hot liquids.
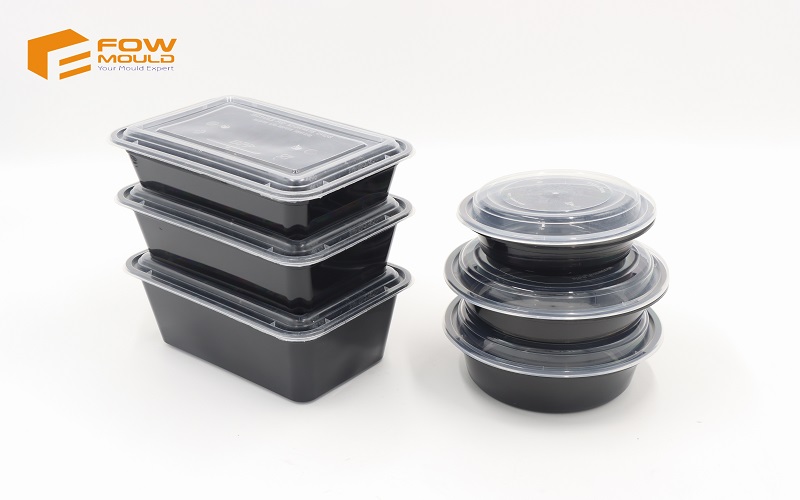
Environmental Impact Of Polypropylene And Polycarbonate
Plastic pollution is one of the most pressing environmental issues in the world today, and bothPP and PC contribute to this problem. Let’s delve into it.
The production of both Polypropylene and Polycarbonate is energy-intensive, relying on fossil fuels, which leads to significant emissions of greenhouse gases.
Moreover, these materials are not biodegradable, meaning they can persist in the environment for centuries, significantly exacerbating plastic pollution in the oceans and landfills.
Although Polypropylene can be recycled, the actual rate of recycling is lower than expected due to difficulties in sorting and issues related to white pollution.
The presence of BPA and other additives makes the recycling of PC even more complicated. Compared to other plastics, the recycling rate for PC is lower.
This results in more PC waste being landfilled or entering the environment, where improper disposal can cause soil and water contamination.
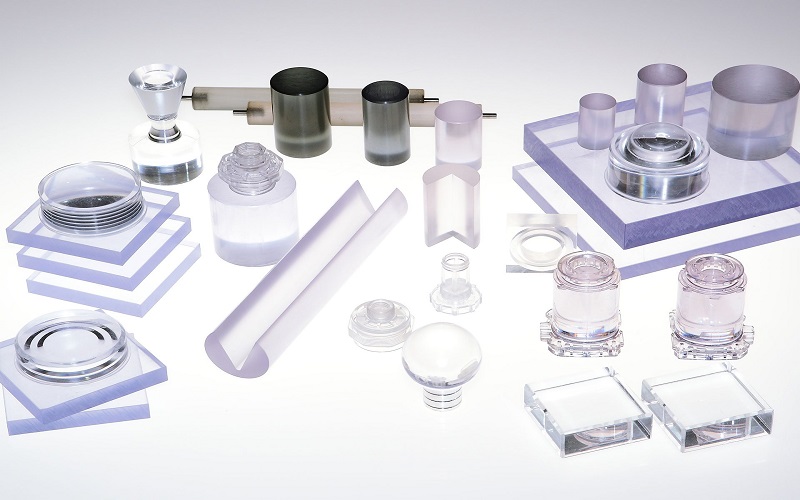
Conclusion
In general, polypropylene and polycarbonate both boast unique attributes that cater to different sectors.
PP’s light weight, durability, and superior heat resistance earn it acclaim, especially popular for medical instruments needing high-temperature sterilization and for food packaging.
On the other hand, PC’s remarkable clarity and robustness revitalize materials for optical uses and the electronics sector.
While PC may have its shortcomings concerning safety and environmental effects, it still stands as a solid choice for non-food contact applications.
For further insights into plastics, stay tuned to FOWMOULD. We’re here to bring you more related content.