In modern life, from food containers to plastic bags, a lightweight, durable material is everywhere—polypropylene plastic.
As one of the most widely used plastics globally, polypropylene stands out with its excellent chemical resistance, low cost, and high versatility, quietly transforming our daily lives. But what exactly is it? What makes it so remarkable?
This article will take you into the world of polypropylene, unveiling the science and applications behind this fascinating material.
What Is Polypropylene(PP)?
Polypropylene (PP), a semi crystalline solid form thermoplastic polymer, is produced through the addition polymerization of propylene monomers and belongs to the polyolefin family.
Its molecular chain consisting of propylene units linked by carbon-carbon single bonds, creating a linear chain structure.
The chemical formula for this linear hydrocarbon resin is (C3H6)n,with a density of 0.89 to 0.92 g/cm³, making it the thermoplastic resin with the lowest density.
Renowned for its lightweight nature, high mechanical strength, excellent heat resistance, and chemical resistance, it stands out as a versatile material.
In the mid-1950s, Italian scientist Natta first synthesized polypropylene using an aluminum-titanium chloride catalyst, establishing it as the second most widely used plastic after polyethylene.
Polypropylene finds extensive applications in both daily life and industry, appearing in products like plastic containers, textile fibers, pipes, and automotive components.
Its low cost, strong recyclability, and processing flexibility make it an ideal choice for packaging material, medical devices, and even plastic furniture manufacturing.
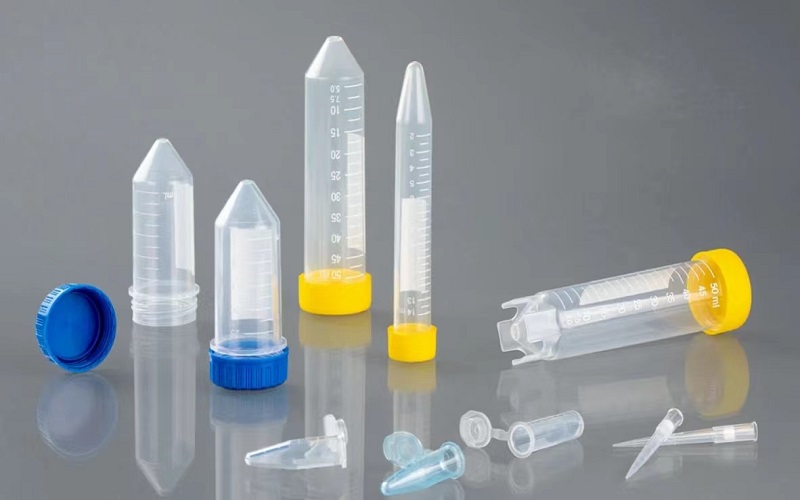
Types Of Polypropylene
Polypropylene can be categorized into different types based on its molecular structure and composition, primarily including homopolymer and copolymer.Each type offers unique characteristics suited to specific applications.
Polypropylene Homopolymer
Polypropylene homopolymer (PPH) contains only propylene monomer in a semi-crystalline solid form. It has a high strength-to-weight ratio, and is stiffer and stronger than copolymers.
It features a highly ordered molecular structure, typically exhibiting strong isotacticity, which results in high crystallinity and a relatively high melting point ranging from 164°C to 176°C.
Known for its excellent stiffness, tensile strength, and heat resistance, this general-purpose grade is widely used in medical devices, automotive components, packaging containers, piping systems, and electrical insulation parts, valued for its cost-effectiveness and balanced performance.
Polypropylene Copolymer
Polypropylene copolymer is created by incorporating small amounts of other monomers (such as ethylene) into the propylene chain and can be further divided into random copolymers and block copolymers based on the distribution of comonomers.
Random Copolymer: The comonomers are randomly distributed along the polymer chain, enhancing flexibility, transparency, and low-temperature impact resistance. This type is ideal for flexible packaging films, transparent containers, and household storage boxes.
Block Copolymer: The comonomers are integrated as distinct blocks within the chain, improving toughness and stress resistance. It is commonly used in automotive bumpers, durable consumer goods, and industrial components requiring greater durability.
Polypropylene copolymer, by adjusting the type and proportion of comonomers, significantly improves the low-temperature brittleness and impact properties of homopolymers, broadening its application scope.
These three types of polypropylene, produced through varying catalysts and polymerization processes, cater to a broad spectrum of needs—from rigidity to flexibility and from high strength to elasticity—making polypropylene an exceptionally versatile material.
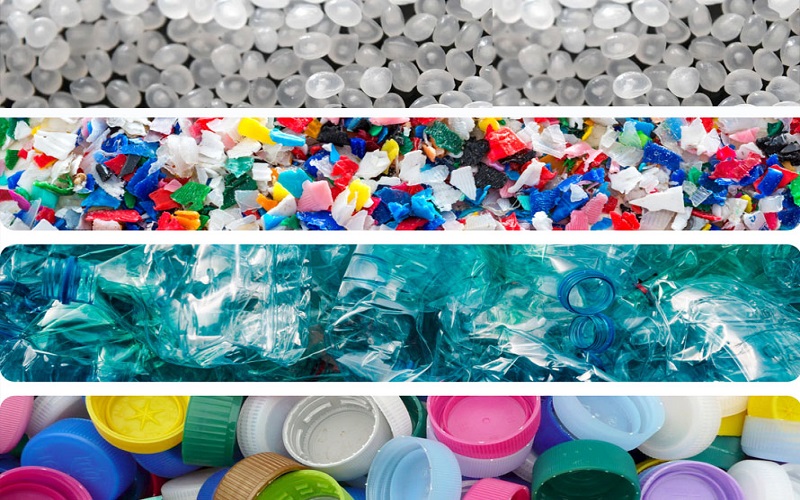
How To Produce Polypropylene?
The preparation of polypropylene is primarily achieved through the polymerization of propylene. Specifically, this process typically employs an addition polymerization reaction, where under the influence of a catalyst, the carbon-carbon double bonds of the propylene monomers open and link together to form long and stable polymer chains.
Depending on the production conditions and the catalyst used, the structure of the polymer chain can be isotactic, syndiotactic, or atactic, which determines the final properties of polypropylene.
Industrially, polypropylene is mainly manufactured through two methods: solution polymerization and gas-phase polymerization.
In the mid-1950s, Italian scientist Natta first achieved efficient polymerization of propylene using a Ziegler-Natta catalyst (usually aluminum-titanium chloride), laying the foundation for modern polypropylene production.
Today, metallocene catalysts are also widely used, especially for producing syndiotactic polypropylene, as they allow for more precise control over the stereoregularity of polymer chains.
Polypropylene polymerization is often performed at temperatures between 140 – 176°F (60 – 80°C), at pressures from 30 – 40 atm (440 – 588 psi), where propylene gas gradually polymerizes into polymer chains within the reactor and is eventually extruded, cooled, and cut into polypropylene pellets.
These pellets can then be used for injection molding, blow molding, or extrusion to create various plastic products.
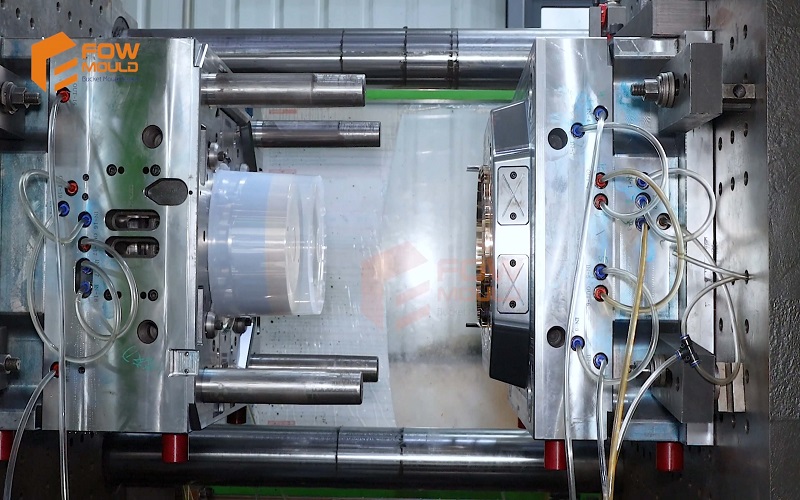
Chemical And Physical Properties Of Polypropylene
The material properties of polypropylene are influenced by several critical factors, including molecular weight distribution, crystallinity, the type and proportion of comonomer (if used), and isotacticity. These elements collectively determine its versatility and effectiveness across a wide range of applications.
With a density ranging from 0.89-0.92 g/cm³, polypropylene stands out as one of the lightest thermoplastic resins, a feature that makes it a preferred choice in industries like packaging and automotive where weight reduction is essential.
Mechanical Properties
Polypropylene exhibits a balanced combination of toughness and rigidity, offering good tensile strength, impact resistance, and exceptional fatigue resistance under bending stress.
However, its impact strength is highly temperature-dependent: it performs well above room temperature but becomes brittle and less impact-resistant at lower temperatures.
Thermal Properties
The melting point of polypropylene ranges from 164°C to 176°C, and its service temperature spans from -30°C to 140°C, reflecting excellent heat resistance. It withstands boiling water and steam effectively, making it particularly suitable for producing medical-grade items that require high-pressure sterilization.
Chemical Properties
Polypropylene is chemically inert to most substances, except strong oxidizing agents. At room temperature, solvents cannot dissolve PP, though certain halogenated compounds, aromatic hydrocarbons, and high-boiling aliphatic hydrocarbons may cause it to swell.
At elevated temperatures, it becomes soluble in solvents such as tetrahydronaphthalene, decahydronaphthalene, and 1,2,4-trichlorobenzene, showcasing its selective chemical interactions.
Electrical Properties
Polypropylene boasts excellent electrical insulation properties, which remain stable despite changes in environmental conditions or electric field frequency.
This reliability makes it an outstanding dielectric and insulating material, particularly well-suited for high-frequency insulation applications.
PP Properties Table | |
Properties | Reference Value |
Density(g/cm³) | 0.89-0.92 |
Melting Point(°C) | 164-176 |
Tensile Strength(MPa) | 21-39 |
Elongation at Break(%) | 200-400 |
Rockwell Hardness(R Scale) | 95-105 |
Water Absorption(%) | < 0.01 – 0.03 |
Shrinkage(%) | 1.0 – 2.5 |
Manufacturing Process Of Polypropylene Products
Polypropylene plastic, thanks to its excellent thermoplasticity and processing versatility, can be transformed into a wide variety of products through multiple methods.
Below are the commonly used processing techniques for polypropylene:
Injection Molding
Polypropylene injection molding is one of the most prevalent processing methods for polypropylene plastic. This technique produces lightweight, compact parts with low material costs and short molding cycles.
With its low melt viscosity and minimal shrinkage, polypropylene is an ideal material for the injection molding process, particularly for thin wall injection molded applications, making it a preferred plastic raw material in this field.
Extrusion
Extrusion is employed to create continuous-length polypropylene products. Molten polypropylene is extruded through a die in an extruder, shaped, and cooled to form items such as pipes, sheets, films, and fibers.
For instance, polypropylene pipes are widely used in water supply and drainage systems, while extruded polypropylene films play a key role in the packaging industry.
Blow Molding
Blow molding, encompassing both extrusion blow molding and injection blow molding, is primarily used to manufacture hollow products. Polypropylene is heated to a molten state, inflated to conform to the mold’s interior, and cooled to take shape.
This method is commonly applied to produce bottles, storage tanks, and hollow containers, where polypropylene’s high chemical resistance and lightweight properties shine.
What Is PP Plastic Used for?
Polypropylene plastic, known for its versatility, durability, and cost-effectiveness, is widely used across numerous industries due to its excellent chemical and physical properties. Below are some of the primary applications of PP plastic:
Automotive parts
Used extensively in the automotive industry for the production of various components, such as interior and exterior trims, bumpers, and instrument panels. Its low density helps to improve fuel efficiency.
Medical Devices
Polypropylene combined with good chemical resistance make it ideal for the medical industry.So, it’s very popular for medical applications, including syringes, food trays, bed pans, Petri dishes, and pill containers.
Packaging material
Packaging industry uses polypropylene as a substitute for paper and cellophane, mostly due to its low cost and flexibility.
Pallets, bottles, jars, yogurt containers, hot beverage cups, and food packaging are some of the products made with this material.
Household Appliances
Polypropylene plastic, due to its excellent insulation properties and chemical stability, is commonly used to manufacture the casings and electronic components of household appliances such as refrigerators, washing machines, air conditioners, and televisions.
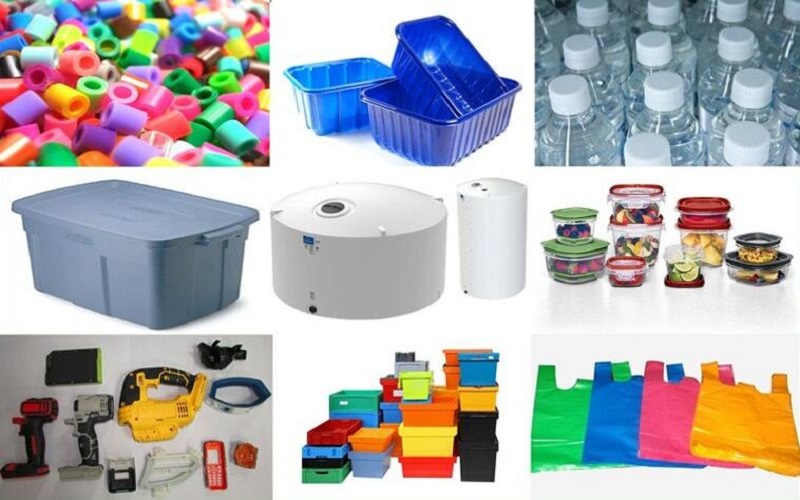
Advantage of Polypropylene
Light Weight: Polypropylene plastic boasts a lightweight characteristic, ranking among the lightest types of plastics. This low-density property makes polypropylene products more convenient to carry and transport while also reducing production costs.
Excellent Chemical Stability: Polypropylene exhibits outstanding chemical stability, remaining inert to most acids, bases, salts, and oxidants. Only a few strong oxidizing agents, such as fuming sulfuric acid, can cause any noticeable changes.
High Heat Resistance: Polypropylene products can withstand prolonged exposure to temperatures of 100°C without issue and remain undeformed even at 150°C, far surpassing the heat resistant of many other plastic materials.
Strong Mechanical Properties:Polypropylene combines toughness and rigidity, with isotactic polypropylene offering high tensile strength and resistance to bending fatigue. Copolymers enhance low-temperature impact resistance through modification, meeting a wide range of mechanical demands.
Electrical Insulation:Polypropylene offers outstanding electrical insulation properties, unaffected by humidity or changes in electric field frequency.This makes it an excellent choice for high-frequency insulation materials and dielectrics in cables and electronic components.
Cost Effectiveness:Polypropylene is relatively inexpensive to produce, with abundant raw material availability and scalability in manufacturing. Its recyclability further reduces long-term costs, aligning with sustainability goals.
Disadvantage Of Polypropylene
Although polypropylene (PP) boasts numerous advantages, it also has inherent shortcomings that limit its performance in certain applications. Below are the primary disadvantages of polypropylene:
Low-Temperature Brittleness
Polypropylene becomes brittle at low temperatures (especially below 0°C), with a significant drop in impact resistance.
This is particularly pronounced in homopolymer polypropylene, restricting its use in cold environments. While copolymer variants offer some improvement, their low-temperature performance still lags behind certain plastics like polyethylene.
Poor Weather Resistance
Polypropylene is sensitive to ultraviolet (UV) light and oxygen, leading to oxidative degradation when exposed to sunlight or air over time. This causes yellowing, brittleness, and loss of mechanical strength. Without UV stabilizers or antioxidants, its lifespan in outdoor applications is considerably reduced.
Flammability
Polypropylene is highly flammable, burning with dripping and producing thick smoke. Unmodified polypropylene can exacerbate fire spread in a blaze, necessitating additional flame-retardant treatments for applications requiring high fire resistance, such as building materials.
Is Polypropylene Safe?
When discussing whether “is polypropylene safe“, its safety in terms of food contact has always been a focal point of public concern.
Overall, polypropylene is generally regarded as food-safe, primarily due to its exceptional chemical stability. Polypropylene exhibits excellent inertness to acids, bases, fats, and most food components, showing minimal reactivity under typical usage conditions (such as room-temperature storage or sterilization in boiling water below 100°C) and releasing no harmful substances into food.
To ensure safety, food-grade polypropylene undergoes rigorous testing and must comply with stringent international standards, such as the regulations of the U.S. Food and Drug Administration (FDA) and the European Union’s (EU) No 10/2011 regulation on food contact materials.
These certifications guarantee that PP products—such as food containers, bottle caps, and microwaveable meal trays—are safe for food packaging applications.
In terms of physical properties, polypropylene boasts a high melting point (164–176°C), enabling it to withstand boiling water at 100°C and making it suitable for microwave heating, provided the product is clearly labeled as “microwave-safe.” Nevertheless, it should not be exposed to extreme heat or direct flames, as this could lead to material degradation and potential risks.
It’s worth noting that while polypropylene resin itself is safe, the safety of the final product may be influenced by additives used during processing, such as certain plasticizers or colorants. Therefore, consumers should prioritize products labeled as “food-grade” and certified accordingly.
Additionally, for long-term storage of high-fat or strongly acidic foods, adhering to product usage guidelines is recommended to minimize any potential migration of trace substances.
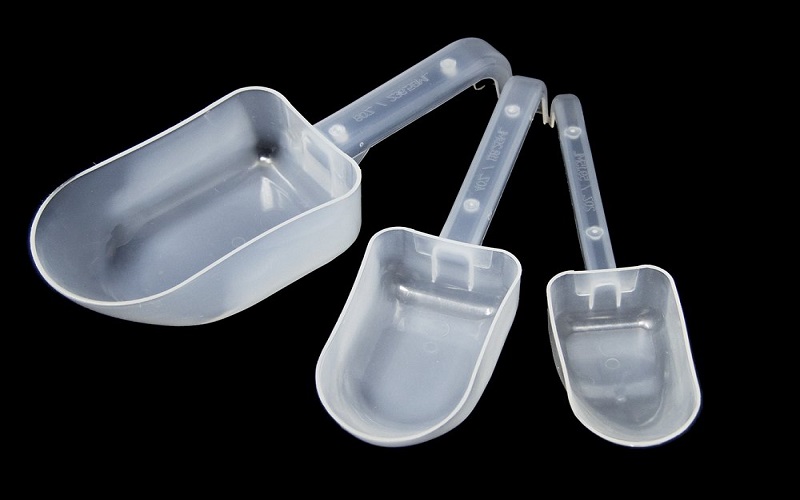
Is Polypropylene Plastic Recyclable?
The recycle code for polypropylene is the number “5”. When you see a plastic product with a label or marking on the bottom that has a recycle symbol with the number “5” inside, it indicates that the primary material of the item is PP.
Polypropylene is technically fully recyclable. Recycled PP can be processed into recycled plastic pellets, which are used to manufacture new products such as automotive parts (bumpers, battery cases), storage boxes, gardening supplies, fibers, and non-food packaging containers.
Although technically feasible, the actual recycling rate and the availability of recycling channels for PP may vary by region.
Compared to plastics with codes “1” (polyethylene terephthalate) and “2” (High density polyethylene), plastics with code “5” (polypropylene) may have less developed recycling infrastructure in certain areas.
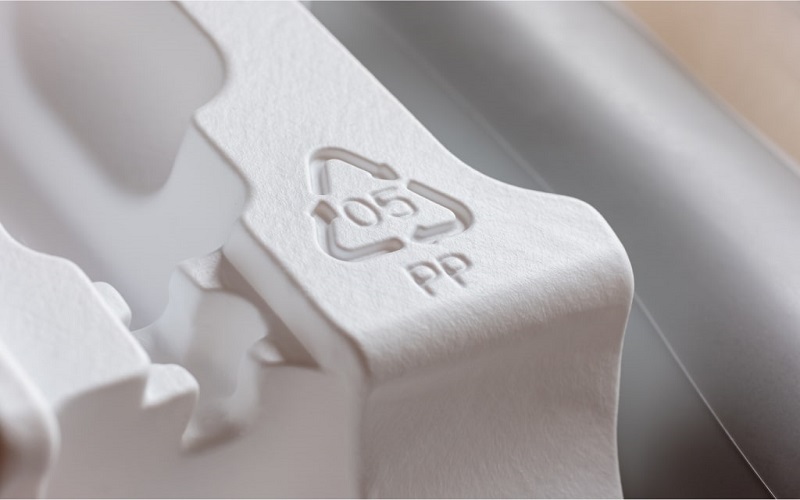
Conclusion
From the content above, we understand that polypropylene is a lightweight, durable, and versatile thermoplastic known for its low density, heat resistance, and processing flexibility. It is categorized into homopolymers and copolymers, with extensive applications in packaging, automotive, medical, piping, and textiles.
Despite drawbacks such as low-temperature brittleness and poor weather resistance, these can be effectively mitigated through modifications and additives. Additionally, polypropylene excels in food safety and recyclability, making it an ideal choice for sustainable development.
FOWMOULD, as a professional injection molding service provider, offers high-quality polypropylene injection molding services to meet diverse needs ranging from precision parts to everyday items, ensuring the best balance of product performance and cost-effectiveness.