Polycarbonate (PC) and Nylon are two widely used engineering plastics, each with unique properties that suit various industrial applications.
Polycarbonate is celebrated for its superb heat resistance and clarity, ideal for applications requiring optical precision and high temperature resilience.
Conversely, Nylon, known for its durability and chemical stability, is prone to aging under high temperatures and is commonly used in textiles, automotive components, and medical devices.
This article delivers an in-depth analysis of “Polycarbonate vs Nylon” highlighting their respective strengths and limitations in diverse applications and discussing their environmental impacts and safety profiles.
What Is Polycarbonate?
Polycarbonate (PC), synthesized from Bisphenol A and phosgene (COCl2), is an almost colorless, glass-like amorphous polymer with excellent optical properties.
Generally, PC plastics are transparent, heat-resistant, impact-resistant, and have a flame retardant BI rating, maintaining good mechanical performance within typical operating temperatures.
However, PC is susceptible to environmental stress cracking and highly sensitive to notches, which complicates the molding of parts with metal inserts.
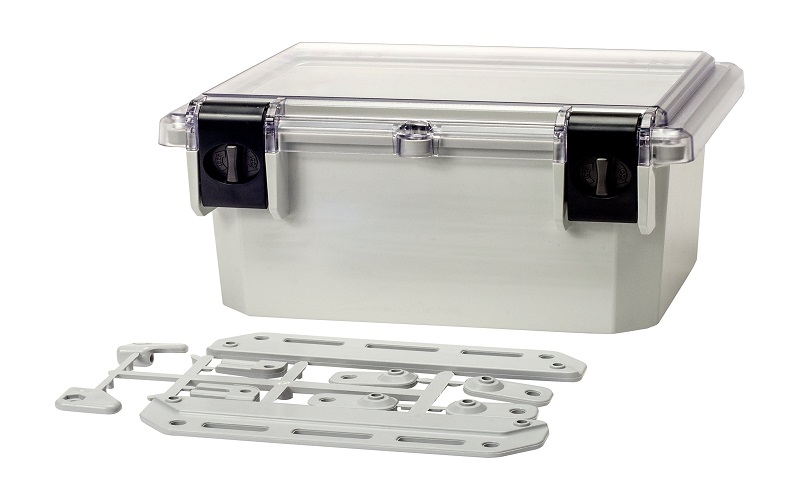
What Is Nylon?
Nylon is a member of the polyamide family and a condensation polymer, obtained either through the polymerization of dibasic acids with diamines or from amino acids, often referred to as nylon or polyamide fiber.
Among the various types of nylon, Nylon 6 and Nylon 66 are the most frequently used.
It features excellent overall properties, a low friction coefficient, and is easy to process.
It is suitable for enhancement and broadening of applications through reinforcement with glass fibers and other fillers.
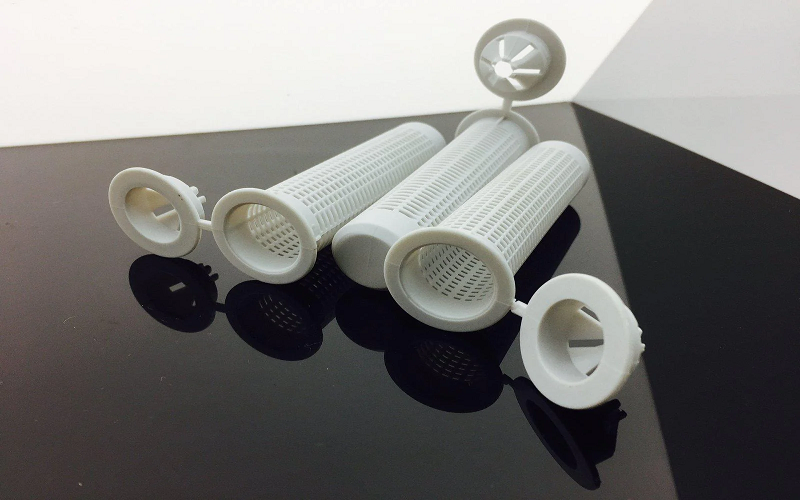
Polycarbonate vs Nylon:Properties
This table below shows data on the properties comparison between polycarbonate and nylon:
Properties | Polycarbonate | Nylon |
Density(g/cm3) | 1.18-1.22 | 1.13-1.15 |
Melting Point(℃) | 220-230 | 220 (Nylon 6), 260 (Nylon 66) |
Tensile Strength(MPa) | 50 | 50-80 |
Flexural Modulus(MP) | 2400 | 1700-3700 |
Water Absorption(%) | 0.15-0.24 | 0.1-10 |
Shrinkage(%) | 0.5-0.7 | 1-2 |
Impact Strength (J/m) | 600~900 | 100-160 |
Heat Deflection Temp (℃) | 135 | 65 (Nylon 6), 75 (Nylon 66) |
Polycarbonate vs Nylon:Manufacturing Process
Polycarbonate and Nylon can both be processed using techniques such as injection molding, extrusion, and 3D printing.
Injection Molding
Polycarbonate has a higher melt viscosity compared to Nylon, so the polycarbonate injection molding process typically requires higher temperatures to reduce viscosity and ensure smooth filling of the mold.
In contrast, Nylon injection molding sometimes involves adding a certain percentage of glass fibers to enhance the tensile strength of the Nylon. For example, plastic hooks made using with more than 40% glass fibers Nylon.
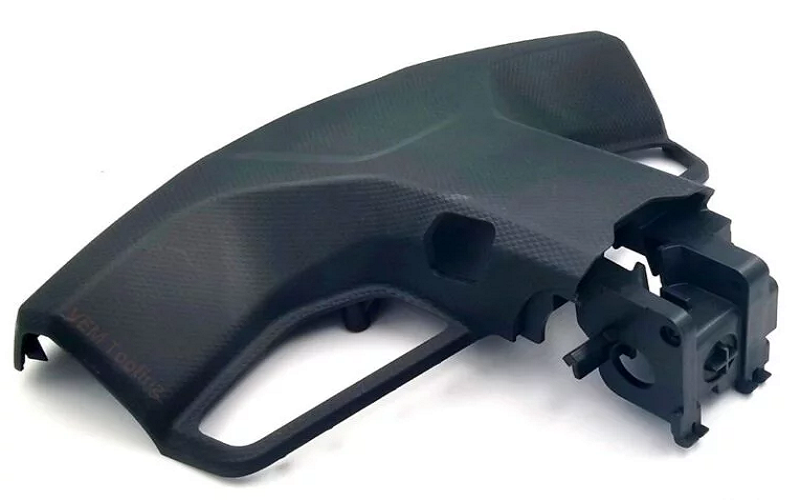
Extrusion Molding
PC sheets, profiles, and long tubes are typically manufactured using extrusion processes. Nylon extrusion products are generally used to make Nylon pipes, Nylon films, and Nylon threads.
3D Printing
In 3D printing, PC is commonly used with Fused Deposition Modeling (FDM) technology, where the material is extruded layer by layer to form the desired three-dimensional object.
Nylon is favored in the 3D printing industry for its high strength, good toughness, and heat resistance, making it particularly suitable for creating prototypes and complex craft items.
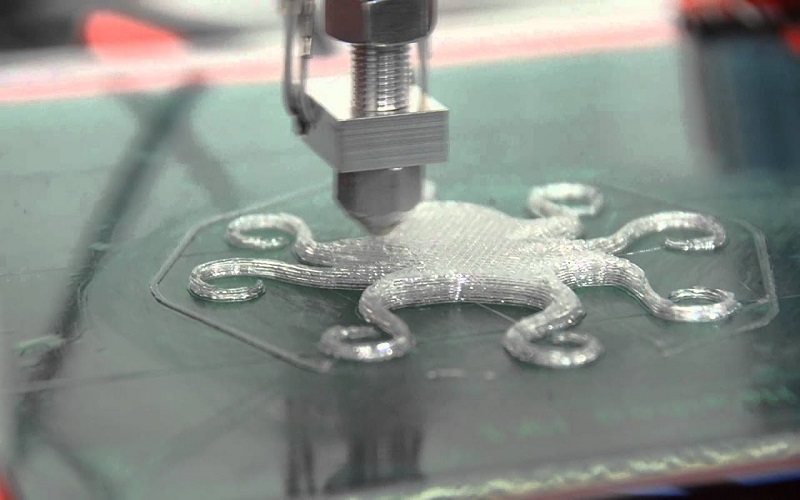
Polycarbonate vs Nylon:Advantage And Disadvantage
As two of the main materials in the field of engineering plastics, PC and Nylon each have their unique advantages but also come with certain limitations.
Advantages of Polycarbonate
- High toughness
- Strong impact resistance
- Good electrical insulation
- Superior heat resistance
- Low water absorption
Disadvantages of Polycarbonate
- Low hydrolysis resistance
- Low fatigue strength
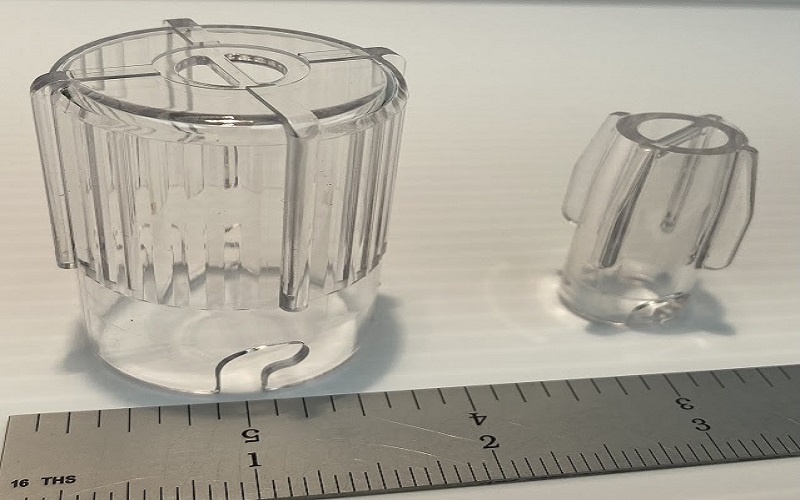
Advantages of Nylon
- Lightweight
- Strong wear resistance
- High elasticity
- Corrosion resistance
- Low coefficient of friction
Disadvantages of Nylon
- Prone to water absorption
- Poor resistance to light
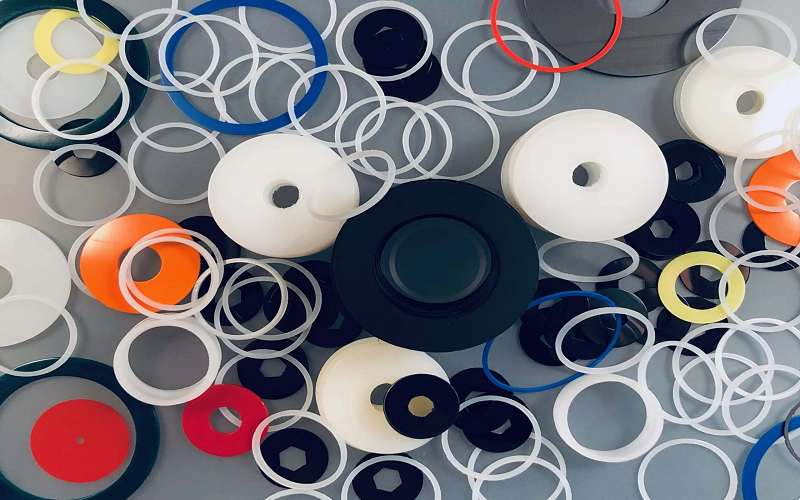
Polycarbonate offers high toughness and heat resistance ideal for durable and high-impact applications, while Nylon provides lightweight, wear-resistant, and flexible solutions, though both materials face challenges with environmental sensitivity such as hydrolysis and UV exposure.
Polycarbonate vs Nylon:Applications And Uses
Due to their unique advantages and limitations, PC and Nylon play crucial roles across various industries.
Applications of Polycarbonate
Optical Applications: Due to its high transparency and excellent light transmission, PC is commonly used for eyeglasses, optical discs, and transparent protective equipment.
Automotive Parts: PC’s impact resistance and thermal stability make it ideal for car headlights, bumpers, and dashboard components.
Electronic Housings: Its good electrical insulation and durability make it the preferred material for housings of smartphones, laptops, and televisions.
Medical Devices: PC is widely used in the medical field for its strength, clarity, and sterilizability, including in laboratory equipment and medical storage containers.
Safety Equipment: The toughness of PC makes it suitable for bulletproof glass, riot shields, and other protective gear.
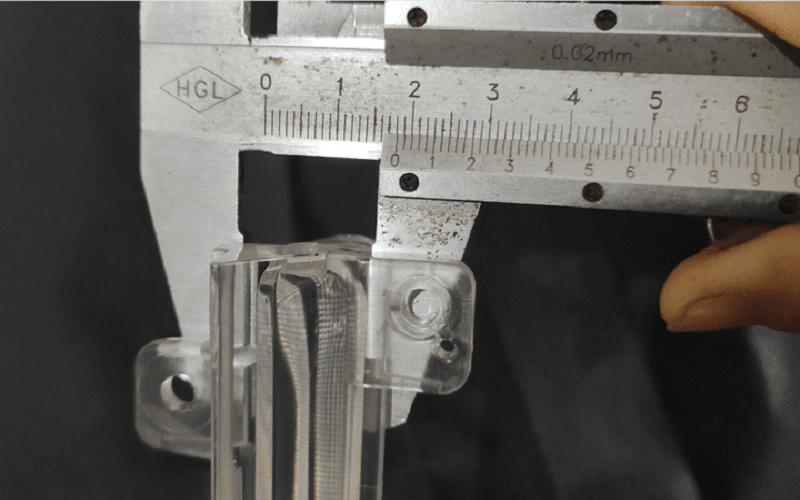
Applications of Nylon
Textile Fibers: Nylon’s elasticity and wear resistance make it ideal for producing socks, ropes, and thread.
Automotive Parts: Nylon’s good thermal and chemical stability allows it to be used for manufacturing under-hood components like radiator fans and timing belts.
Mechanical Components: Its strength and lubricity make it suitable for gears, bearings, and other wear-resistant mechanical parts.
Sporting Goods: Due to Nylon’s toughness and lightweight, it is used in climbing equipment, fishing lines, and racket strings.
Consumer Goods: Its flexibility and durability make it common in kitchen utensils, toothbrush bristles, and other everyday items.
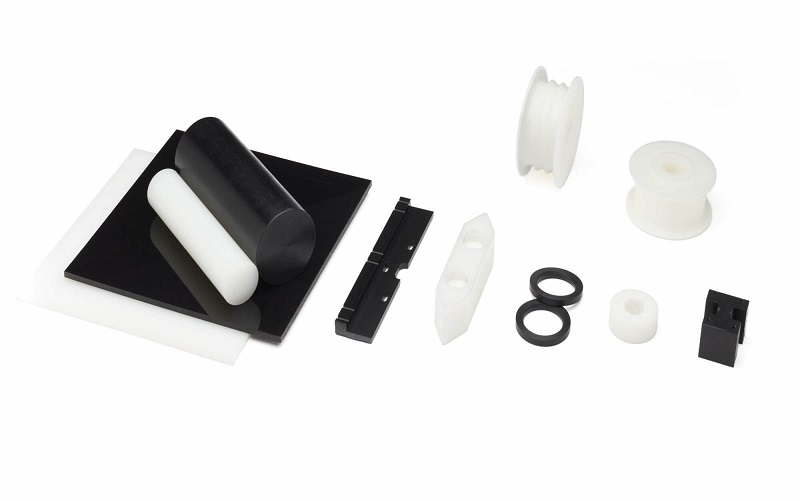
These diverse applications demonstrate the effectiveness and versatility of PC and Nylon in meeting specific performance requirements and functionalities in different sectors.
Polycarbonate vs Nylon:Recyclability and Sustainability
As the concept of sustainable development deepens, plastic recycling has become a crucial issue for both injection molding companies and consumers.
Therefore, the recycling of Polycarbonate and Nylon products cannot be overlooked.
In theory, polycarbonate plastics can be recycled and are marked with the plastic recycling code “7”.
One effective method is chemical recycling, where waste PC is reacted with phenol to produce monomers, which are then purified and re-polymerized.
However, due to its chemical structure and the presence of additives such as Bisphenol A, the recycling of PC is not only costly but often results in degraded material quality.
Nylon recycling faces similar challenges due to its diverse formulations and the degradation of properties with each recycling cycle, making effective recycling more difficult.
Like PC, the mechanical properties of recycled Nylon typically decline, limiting its reuse in high-performance applications.
To address these issues, manufacturers are currently developing bio-based alternatives for both PC and Nylon to reduce resource consumption and carbon footprint while continuously improving recycling technologies to enhance the sustainability of these materials.
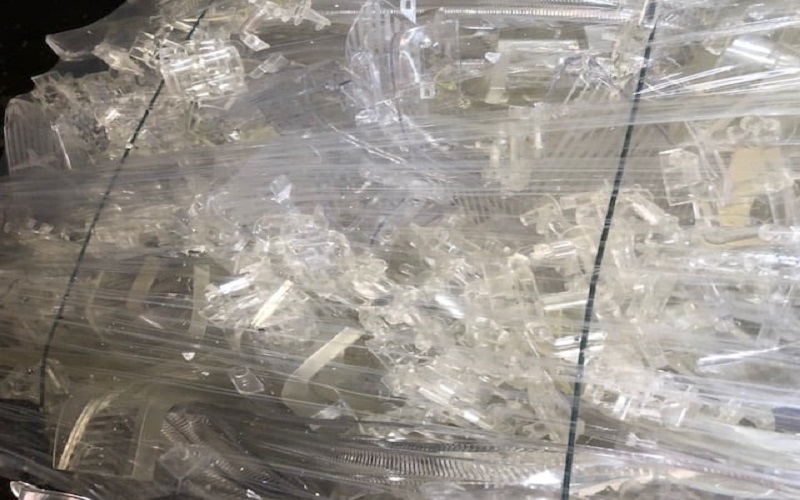
Which Is Safer, PC Plastic Or Nylon?
Polycarbonate plastic is widely utilized in manufacturing baby bottles, straw cups, and various other containers for food and beverages.
However, the presence of Bisphenol A has raised significant concerns about polycarbonate safety.
In fact, the potential exposure to BPA from polycarbonate products that come into contact with food and beverages is extremely low, presenting no known health risks to humans.
On the other hand, nylon materials are relatively safe in normal use.
Nylon, recognized for its wear resistance and mechanical strength, is broadly employed in products that require stringent safety standards, such as medical devices and children’s toys.
However, it’s important to note that during the production of nylon products, certain additives may be used, which should not be ingested as they can be hard to digest and may lead to symptoms such as diarrhea and abdominal pain.
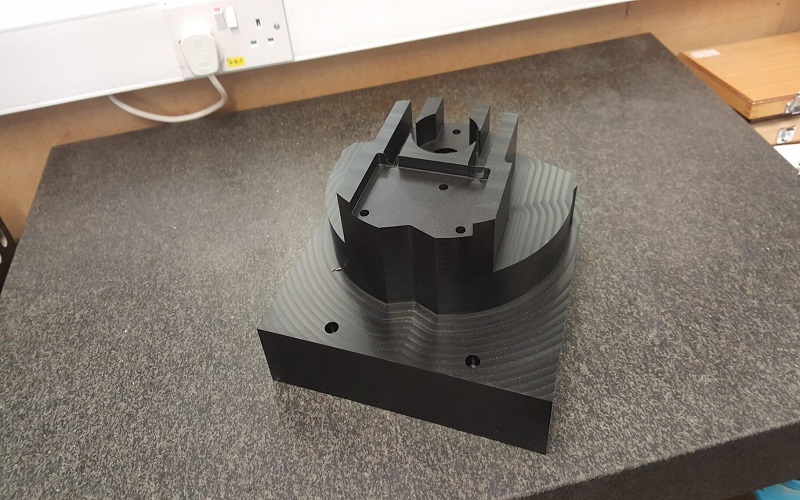
Conclusion
In conclusion, both polycarbonate and nylon have their advantages and disadvantages, and the choice between them should be based on the specific requirements of the project.
For example, PC might be the better choice for products that require transparency and high impact resistance;
whereas nylon might be more suitable for applications that need lightweight, high wear resistance, and stronger environmental sustainability.
If you are looking to start a new project, please contact FOWMOULD for a free quote! We offer a one-stop injection molding service from drawings to finished products.