The Polycarbonate molding technique is mainly used to mold complex designs and shapes. Polycarbonate is thermoplastic used in many ways to form tough materials and re-process the material for further usage and production. Its effortlessly flexible property allows them to be used for many heavy and intricate projects where the use of Polycarbonate is unavoidable.
Polycarbonate is a world-class plastic that is extremely easy to relieve from one to another object because it is exceedingly pliable. The excellent properties make Polycarbonate become useful in many industries. It is not only good for carving new products but also has enriched the trust of its users.
This high-quality plastic fiber is impressively solid, resistant proof, and easy to clean. When molding, Polycarbonates exhibit the utmost endurance and undergo a lot of pressure and high temperature without having any effect on their durability.
What Is Polycarbonate And What Are Its Properties?
It’s essential to understand what Polycarbonate is and its essential properties before getting to know about the molding service. In the next section, we discuss some of the key properties of this material.
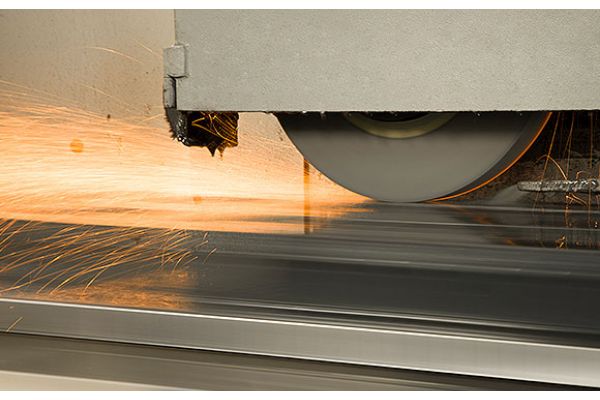
The Usages of Polycarbonate Injection Molding
Polycarbonate is the first choice of industries because of its multifunctional properties. They are tough, solid, and flexible to fulfill the requirements.
Polycarbonates are gaining their market remarkably and are the best-selling material in the clan of thermoplastics, they are realized as the best alternative possible for plastic with even better quality and longer brawn.
Polycarbonate is profoundly used in engineering and manufacturing sectors where their extensive utilization is likely to be possible. Its ideal translucency and finish make it a popular fiber to use in machinery, face shields handle, guards, and skylights.
Unlike other fibers, Polycarbonate does not react easily to any disruption, and it sustains its quality throughout the product journey. Its products are also easy-to-maintain ones that don’t compel additional care.
Various Properties Of Polycarbonate
Polycarbonate is a heavy-duty fiber that fulfills many requirements of industries. In addition to being a favorable material in injection molding, Polycarbonate also has many other beneficial properties.
In the following part, all those material characteristics of Polycarbonate will be introduced one by one and it will be easy for people to know if Polycarbonate is the best choice for their needs.
1. General Properties
- Elasticity
Polycarbonate materials are very elastic and stretchable. Once they are melted down to a precise consistency, one can shape anything out of them. It is ingenious for molding things, and once the object is rested, it turns into solid and retains high-impact toughness—molding Polycarbonate functions in two ways: elastic enough to be modulus and tough enough to retain the shape.
- Hardness
Polycarbonates are known for their stiffness and ability to uphold and conserve the shape and size in which it is melted down. When it comes to performing on the surface, Polycarbonates ace the job there too.
All thanks to the high density of Polycarbonate fibers, this material can be hard enough to cater to different needs. The density of Polycarbonate is marked up to 1200 kg/m³, which is adequate for fibers to serve the purpose.
2. Mechanical Property
- Compressive Strength
Compressive strength is a test of material to undergo pressure to its fullest extent and resistance of the material to not break down.
It is assumed that the higher the compressive strength of the material is, the better its functions and alternative usages are. A compressive string of Polycarbonate is 6.683 MPa.m½ which is good to endure the combustion pressure.
- Dielectric Strength
Another determining property of Polycarbonate is its dielectric strength. In other words, this material can insulate the currents and ebbs. This is a really helpful property in many ways. For example, this material can be used to produce shells of some electronic products.
Due to its high dielectric strength and heat resistance, it is a good source to insulate electricity. Furthermore, it ensures the flow of production without any hindrances.
3. Thermal Property
Polycarbonate is capable of withstanding extreme temperatures up to 270 degrees for prolonged periods and up to 1166 degrees in short bursts without it breaking, distorting, or absorbing any heat. This makes it an excellent material to use in construction, making molds, and other industries that employ high temperatures.
Polycarbonate is also a remarkable insulator and provides much better insulation as compared to other building materials like glass. The material’s thermal efficiency helps stabilize and create a uniform temperature across a space.
4. Optical Properties
Polycarbonate is capable of providing UV protection, allowing soft light to pass through but deflecting harsh light. Optical grade polycarbonate allows total transmittance of visible light with no haze in vision while also offering protection from harmful UV rays.
Due to it being light as well as sturdy, it is used to make optical glasses, sunglasses, and contact lenses. Since it also offers impact resistance, it is used to make protective eye gear in labs and construction sites.
Advantages Of Polycarbonate In Injection Molding
Polycarbonate infolds so many properties in them, and these properties enable the worldwide use of Polycarbonates in different manners. And the process by which Polycarbonate becomes this strong is called Polycarbonate injection molding.
Polycarbonate is always regarded as an ideal type of material for injection molding because of its various advantages. This part will introduce some of its major advantages in injection molding and help people choose the most suitable injection molding material for their needs.
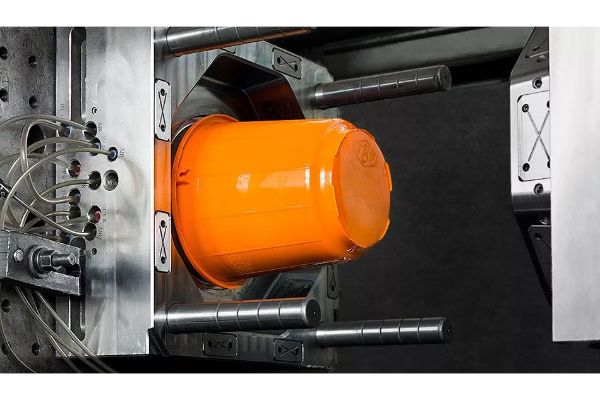
- Maintain Good Performance In Heat
Polycarbonate, with its high degree of compressibility and the ability to withstand frequent heat treatment, works well under fire and high temperatures. This is one of the reasons why industries prefer Polycarbonates over any fiber.
When using injection molding and thermoforming to manufacture automotive parts, electrical components, and lab equipment, polycarbonate proves to be the choice of material due to its ability to withstand high temperatures for long as well short periods of time.
- Good Stiffness And Toughness
Polycarbonate is a tough and stiff material. It has high-density molecules that keep the material integrated into the injection molding process. They are made tough because those products are going to be used for distinct experimental purposes too.
Polycarbonate is tough enough to maintain the existing shape up to 120° Celsius. Till the Polycarbonate is under this temperature its quality won’t get affected a bit and this quality remains the same for long periods.
- Capability Of Transmitting
It is said that Polycarbonates are a good source of green light. Its sheets are very thin and flimsy. They facilitate the photosynthesis process and also play a role in the greenhouse.
The greenhouse requires a lot of sunlight but not direct because direct sunlight may harm the plants kept in the greenhouse. Hence, Polycarbonate is a good source because it transmits 80% of sunlight to the greenhouse and protects plants from ultraviolet rays.
- The Deformation is Low
Polycarbonate is rigid once it settles into its shape. Plates of Polycarbonate are rigorous in forming and involve a lot of injection molding.
Deformation becomes a challenge here because a plate can undergo much of the injection process. Once the products have been cooled down, it takes extensive force to break down. Because of this characteristic, Polycarbonate can be considered a great choice for producing some products with fine details and precise shapes using the injection molding technique.
- Moisture Resistant
Often when things come in contact with moisture, it gets ruined. Moisture depreciates the product and can further lead to its complete damage just by a few drops of water and moisture.
But Polycarbonate is moisture resistant. This material has a greater level of density which results in the insulation of moisture that may degrade the quality of Polycarbonate. This is why Polycarbonates don’t react with moisture in atmospheres and their performance improves.
- Impact Resistant
Renowned toughness and longer lasting Polycarbonates are possible because they are impact resistant. The toughness of Polycarbonate works as a shield and protects from environmental particles.
Contact lenses and glasses are made from Polycarbonate to ensure safer use. Same as a protective shield worn by a welding man. Since it has a maximum tensile strength of 9500 psi and yield strength of 9000 psi, polycarbonate is able to withstand enormous pressure and high-strength impacts. The fundamental element that protects them against fire blazes is Polycarbonate face shields.
- Electric Insulation
Polycarbonate is a great insulating material. Charging plugs, adapters and batteries are coated in Polycarbonate pieces, and wires are molded in Polycarbonate wires to prevent leakage of electric current and secure the smooth flow of current inside.
Polycarbonate molding is heat resistant, waterproof, and flame retardant, which makes it the first choice for hardware products and outer covering or protective covering for electrical appliances, for instance, Toasters, mixer grinders, juicers, and handles for knives.
Some Disadvantages of Polycarbonates
Everything great comes with a little drawback. The same goes with Polycarbonates there are very few shortcomings in Polycarbonate molding too. Let’s check out some of them.
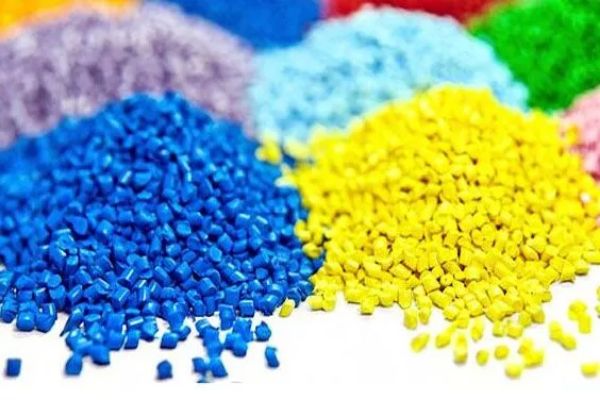
Sensitivity to Scratches
Polycarbonate molding is very rigid and strong, but there are a few things that they are sensitive to. Polycarbonates are sensitive to scratches because they increase the chances of tarnishing the material inside. It is important to note that Polycarbonate products must be stored with caution. They are not high maintenance but require a little attention and care.
Polycarbonate Sheets Can Expand
Polycarbonate is a thermoplastic, and thermoplastics tend to become elastic when they are in constant touch with heat.
Furthermore, warm weather can expand the size of a sheet continuously. And this becomes a hardship when Polycarbonates cannot bear the environment. This is a disadvantage because expansion in size might result in thinning of Polycarbonate sheets which depletes their quality and ability to ensure pressure.
In cold weather, Polycarbonate sheets dwindle after more than a couple of years so they may fail in playing their role when there is a definite requirement for the size of the Polycarbonate sheet.
The Process Of Polycarbonate Injection Molding
In nutshell, the process of converting Polycarbonate sheets into any desirable shape involves many steps, such as melting the Polycarbonate at 120° C and filling the Polycarbonate liquid in the mold to set them to freeze. Once they are set in the desired shape, the material is demould and the finished product is obtained.
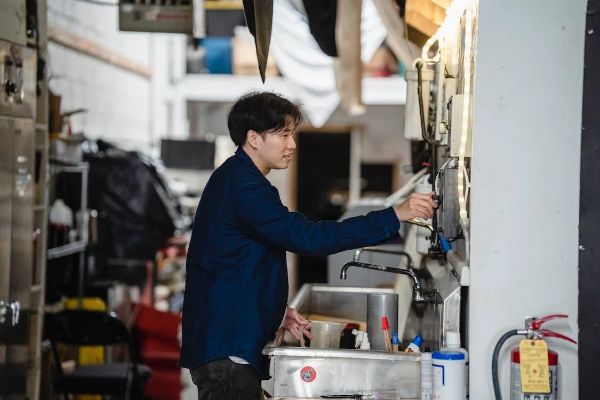
- Prepare Polycarbonate Injection Mold
To procure Polycarbonate into a suitable shape the mold needs to be perfect. Selecting a mold that can tolerate the heat and warmth of the liquid material is significant. These thermoplastic mold helps to give Polycarbonate the desired shape.
Polycarbonate injection molds are usually made from hardened or pre-hardened steel, beryllium-copper alloy, or aluminum. Typically, one of two main methods is used in making molds- Standard Machining and Electrical Discharge Machining.
In Standard Machining, CNC machining has gained predominance since it can be used to make more complex molds more accurately. Designing and manufacturing the mold has become highly automated with Computer Aided Design (CAD) software being used to define the mold’s mechanical dimensions. This is then translated into manufacturing instructions using Computer-aided manufacturing software. These instructions are transformed into specific commands for each machine using post-processor software which is then loaded into the CNC machine and constructed using 3D printing.
In the EDM method, the desired mold shape is achieved by using an electrode that is constructed out of copper or graphite. This is placed in an EDM machine and using a controlled source of electricity, is used to shape the workpiece.
- Feed Polycarbonate Material and Start the Molding Process
Polycarbonate fibers are dissolved into liquid from un-uniform chunks in a forge, and they are melted at a very hot temperature which is approximately 120° C. Then, the fluid of Polycarbonate is poured into the mold where it settles once.
This process ensures that only smooth fluid is settled and, blurting all the bubbles & removing all the unwanted elements from the liquid. Once this is analyzed, then the mixture is poured into the mold and left to get set for the final step. The settling process varies from product to product and the time and temperature to be settled are customized according to the product.
- Eject the Polycarbonate Part and Finish it
Ejection is the last step and a very delicate one because this is the final stage for determining the quality and efficiency of the product. It’s the result of the above two steps. In ejecting, mold is desolated from the set Polycarbonate material and made ready for the next insertion into them.
In case a mold gets stuck to the product, then it is carefully carved with the help of sharp objects such as carving knives. This process continues till the final product is obtained. Furthermore, the finished and approved product is stored with care in warehouses.
The Appliance Of Polycarbonate
There are so many things that can be made from molten Polycarbonate, from daily household stuff to industrial products. Polycarbonate molds are used worldwide. Polycarbonate products can be spotted almost anywhere, in any sector.
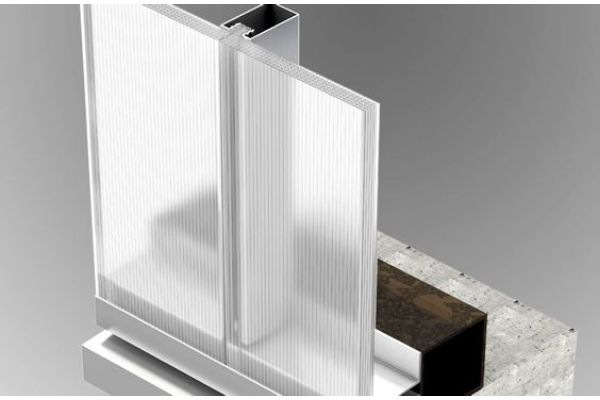
Here are some common Polycarbonate appliances used for daily purposes and some industrial products.
1. Automotive Components
- Helmets and Other Automobile Accessories
Helmets made to safeguard people and protect others must be very solid to endure any accident or condition. Hence, Polycarbonates are a trusted material for its creation. It proves to be durable in road mishaps.
Other automobile accessories such as mudguards, knee pads, and shoulder pads are also made from Polycarbonate since it is also going to be used for the safety o others.
- Brackets and Road Signs
Brackets and sign boards on roads are also made from Polycarbonate. These brackets and signs are reiterated in nature. Hence, their quality must be better than the best to survive on roads.
2. Optical Components
Contact lenses may seem surprising but they are definitely made of Polycarbonate. These contact lenses are available in various colors and sizes as colorful lenses also emerge as a fashion trend. Owing to the excellent properties of this material, the lens can protect eyeballs from some cases, including from catching dust particles outdoors.
3. Electrical Conductors and Insulators
Lighting and fixtures require a lot of care because the flow of current is very dangerous. Furthermore, one must ensure that the cover of the wiring and cables is made of good material.
Polycarbonate is trusted in this, too; its electric insulation property makes them trustworthy for making the cover of wiring and cables. Moreover, these Polycarbonates are also used for decorating ceiling lights. All in all, as Polycarbonate is non-conductive, it’s a great choice for producing items in the electrical industry.
4. Medical Components
The medical industry requires a lot of resources to get things done. These contain equipment such as pipes, cans, injection, oxygen cylinder lids, machine covers, water bottles, plates, and so many more.
These medical equipment are mostly for one-time use hence they require generous quality products which should not be hazardous to any patient or workers. Thus, Polycarbonate makes sure that the substance from the source won’t get leaked into the course of action.
5. Basic Component
Water bottles and lunch boxes are two daily necessities for students and working people. And people always tend to choose products that have advantages in both price and quality.
Hence, Polycarbonate helps manufacturers to achieve the desired quality at a minimum price. Water bottles, especially the lids, are made of Polycarbonate, so even when the bottle is dropped accidentally, it will not make the bottle leak for the rest of the day.
Why Polycarbonate Injection molding Is A Good Choice?
Injection Molding is an easy yet so efficient & effective method to transform Polycarbonate. The injection molding method facilitates quick production for maintaining the demand and supply constraints and ensures high output production with a steady flow.
Without a doubt, it can be said that injection molding guarantees the enhanced quality of products and production cycles.
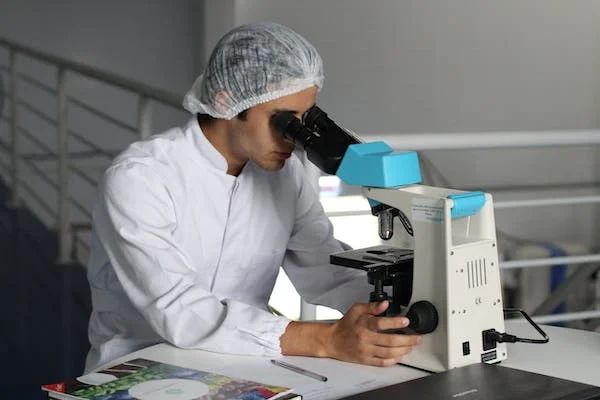
Scalability in Polycarbonate
It can be easily melted down and transformed into any int shape or size. Its high scalability function makes Polycarbonate an appropriate choice for injection molding.
Low-Cost Labour
The Injection molding method does not require a lot of labor because a lot of work has to be done by machinery. That’s how this molding process facilitates the producer to reduce manpower and increase production speed and consistency with machinery.
Therefore, Polycarbonate injection molding is a wonderful choice for manufacturers who want to produce Polycarbonate products at a relatively low price.
Design Flexibility
Injection molding provides the freedom to modify the design of the product as desired. The industry can create customized designs to create unique and innovative products.
Whatever shape of Polycarbonate products you want, it can be easily done. All you need to do is to find a reliable injection molding service provider who enables you to customize the products.
Low Scrape Rates
Injection molding is just a threefold process which is quite economical for manufacturers. It has a very definite list of resources to be required and the industry can easily repeat the process with residual molten Polycarbonate for the next batch of injection molding.
Good Colour Control
Since it can withstand temperature extremities, precipitation, sunlight as well as the physical impact, polycarbonate can last for several years without fading or getting discolored. The color fastness of polycarbonate is remarkable and with the injection molding process, these properties can be enhanced in order to increase its longevity.
A Trustworthy Injection Molding Service Provider: FOW Mould
FOW Mould in China has been in the business of making injection mold for more than 40 years. They have specialized knowledge of how things are done with mold making and these skills make them overseas representatives in 3 countries, the USA, Russia, and Egypt.
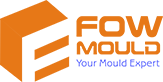
FOW Mould claims their product as the best because of the following reasons: good quality, lifelong free repair, technical efficiency, reasonable prices, and most importantly prompt response. These qualities altogether made FOW Mould an ideal supplier and partner for your business.
FOW Mould not only makes the best company in the domain of Polycarbonate molding but also guides their customers on matters such as cost saving by minimizing the unnecessary burden from the offering while still preserving the quality.
Products & Services They Offer:
- Polycarbonate Molding for buckets
- Polycarbonate Molding for containers
- Polycarbonate Molding for Toys & baby products
- Polycarbonate Molding for chairs
Mold Designs They Offer:
- Unique Polycarbonate molding for toys
- Pet products and molds for pet supplies
- Various designed boxes
- Crate molds and storage boxes
- Design and provide injection molding service for solar panel parts
Conclusion
Polycarbonate products are gaining an extensive market for their wide usage. With help of an injection molding technique, manufacturing units now have a more creative outlook and turn their imaginary products into reality.
It is considered that thermoplastic is harmful to nature but it is important to understand the minor difference between one-time use of plastic and plastic which can be recycled very easily. Polycarbonate can be recycled very easily with injection molding technology and it continues to serve many other needs. Contact FOW Mould now to get a quote for your business.