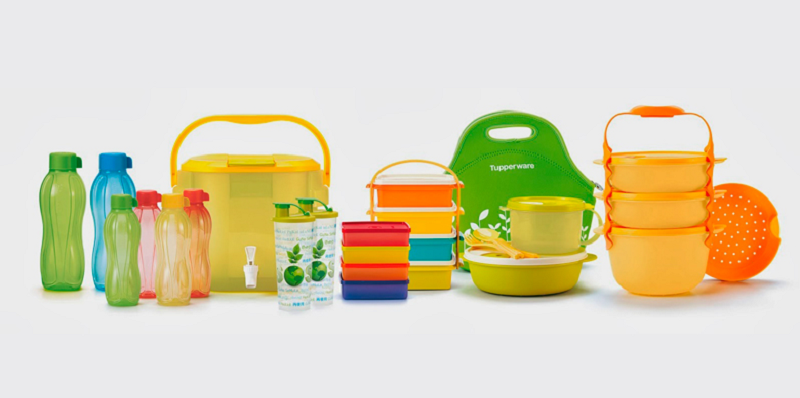
What are the advantages of plastics?
Plastics have numerous advantages in manufacturing, including their versatility, durability, and cost-effectiveness. Plastics can be molded into various shapes and sizes, are resistant to corrosion and chemicals, and often require less energy to produce compared to other materials.
Introduction to Plastic Parts Manufacturing: A Comprehensive Overview
Plastic parts manufacturing is a nuanced methodology that merges artistry with intricate mechanical engineering. This multifaceted industry extends from the manufacturing plants all the way to your local stores, providing countless objects we use daily. It refers to the production process involved in transforming plastic materials into a wide range of plastic parts, including different types of plastics.
The transformation happens in various ways, each tailored to produce high-quality goods with distinct characteristics and applications. Processes like injection molding, extrusion manufacturing process, fabrication, and CNC machining are some of the core techniques in plastic parts manufacturing. The production process involved in manufacturing complex parts made of thermosetting plastics is a careful blend of technology, material science, and craftsmanship.
A critical factor in the manufacturing process is the type of plastic material used. Thermoplastics such as polyethylene, polypropylene, and polystyrene are commonly used in the industry. Nylon is another thermoplastic that is widely used due to its high strength, durability, and resistance to abrasion. Additionally, polymers called thermosets are another type of plastic material that are used in manufacturing due to their ability to withstand high temperatures and resist deformation. Each plastic processing method also directly relates to the produced part’s complexity, mechanical properties, and cost-effective large quantities manufacturing.
Exploring the Concept of Plastic Component Manufacturing
Diving deeper into plastic component manufacturing reveals a multi-step process. This involves plastic selection, mold design, production, and finishing processes. After deciding on a product design, manufacturers select the right manufacturing process, which offers a unique balance between manufacturing speed, product detail, plastic type, and cost.
Details in every step of the plastic component manufacturing process are incredibly important. The selection of materials (plastic) for manufacturing depends on the products’ final application. For example, sturdy plastics used in manufacturing deposits thin layers of plastic to produce a finished product. The design process for plastic component manufacturing also finds its applications in various industries such as automotive, healthcare, aerospace, and consumer goods, with the use of dfm techniques to ensure high-quality and efficient production.
Mastering the Art of Plastic Part Fabrication: Techniques and Tools
The next layer of plastic parts manufacturing lies in the distinct skills required for plastic part fabrication, including the plastic manufacturing process. The sophistication of the part dictates the manufacturing method, with some techniques tailored for simple shapes and others aimed at creating complex ones, paying attention to even the smallest details.
Companies like custom plastic part manufacturing specialize in making intricate designs that suit their client’s specifications. For example, plastic injection parts factories are adept at producing large quantities of a product quickly and cheaply, adhering to the tight tolerance requirements. In the manufacturing process, the mechanical properties of a plastic part are directly impacted by the method of fabrication, such as plastic injection molding.
Various industries use machinery and many plastic part fabrication methods, including the use of acrylic, to achieve different goals, including creating prototypes, manufacturing deposits, thin layers of plastic to produce finished products, and even massive-scale manufacturing.
Highlighting Different Methods in Plastic Part Fabrication
There are numerous methods used in plastic part fabrication, each with its unique advantages, each offering unique benefits depending on the type of plastic part being produced.
●Injection Molding: This is one of the most common methods used in plastic part fabrication. It involves melting plastic pellets and injecting the molten plastic into a mold under high pressure. The plastic then cools and hardens into the shape of the mold. This method is ideal for mass production due to its high speed and precision. It can produce complex shapes with excellent surface finish.
●Extrusion: This process involves heating a plastic material and pushing it through a die, a specially shaped orifice. The plastic that emerges from the die takes on its shape, forming a long continuous product, such as pipes, rods, or sheets. The extruded plastic is then cooled. This method is commonly used for creating plastic parts with a consistent cross-section.
●Blow Molding: This method is used to create hollow plastic parts. It starts with a molten plastic tube, known as a parison, which is placed between two mold halves. The mold then closes, and air is blown into the parison, inflating it into the shape of the hollow part. Once cooled and hardened, the mold opens to eject the part. This method is commonly used for making bottles, containers, and other hollow items.
●Rotational Molding: Also known as rotomolding, this process is used to create large, hollow plastic products. A measured quantity of plastic powder is placed in a mold, which is then heated and slowly rotated on two axes. The plastic melts and coats the interior of the mold, creating a hollow part. Once cooled, the part can be removed from the mold. This method is ideal for creating large, hollow objects like tanks and bins.
●Thermoforming: This involves heating a plastic sheet until it becomes pliable, then forming it into a specific shape using a mold. The plastic is held against the mold by applying a vacuum between the mold surface and the plastic sheet. Once cooled, the plastic retains the molded shape. This process is commonly used for packaging, automotive parts, and other plastic products.
●Vacuum Forming: This is a type of thermoforming where a plastic sheet is heated to a forming temperature, stretched onto a mold, and forced against the mold by a vacuum. This process is used for making product packaging, speaker casings, and car dashboards, among other items.
Harnessing 3D Printing Technology in Plastic Parts Manufacturing
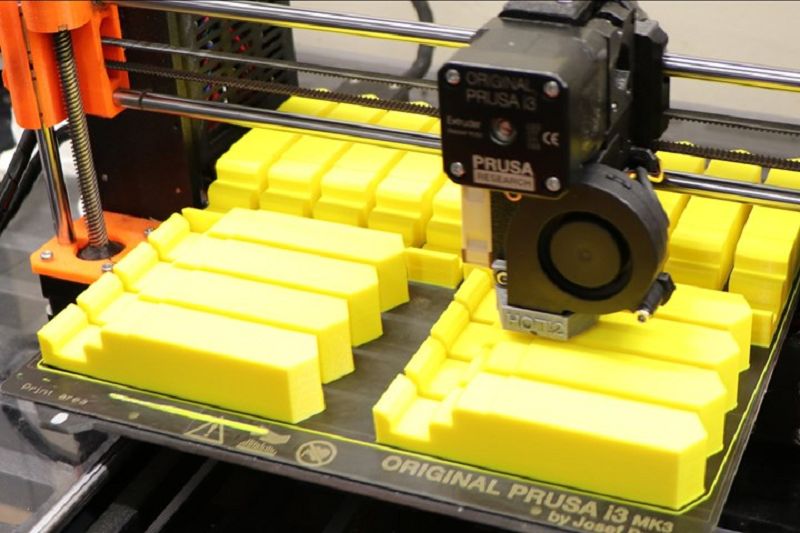
With technology continually advancing, plastic parts manufacturing has also seen a radical shift. The rise of 3D printing has introduced a new era in plastic parts manufacturing. This application has made the process of making large quantities of a product quicker, cheaper, and more efficient.
3D printing brings forth the concept of additive manufacturing, where layers of material are progressively added to form the desired final product. This technology has not only amplified the speed of production but also the scale and the ability to handle part complexity. It provides an economical approach for both mass and custom production. Another option for custom production is urethane casting, which offers a cost-effective and efficient way to produce small to medium-sized batches of parts with high-quality finishes. Polyurethane is a common material used in urethane casting, providing durability and flexibility to the final product. Another option for custom production is using a silicone mold, which can create intricate shapes and designs with high precision.
Injection Molding: A Mainstay in Plastic Parts Manufacturing
Injection molding is arguably the most common method in plastic parts manufacturing. It’s a versatile process that can produce a range of products with complex geometries. The process involves injecting molten plastic into a mold, where it cools and solidifies into the desired shape.
The advantages of injection molding include high production rates, repeatable high tolerances, the ability to use a wide range of materials, low labor costs, minimal scrap losses, and little need for finishing parts after molding. However, the initial setup cost and lead time can be high due to the design, testing, and tooling requirements, especially when using specialized materials such as polycarbonate.
Types of Injection Molding
INSERT MOLDING | OVERMOLDING | |
Function | ●Increase the weight of the part ●Achieve threads on a plastic part ●Add cosmetic or functional value ●Improve the IP rating of the part | ●Strengthen the structure of the original part ●Add flexibility to rigid areas ●Add functional features like grip ●Blend colors ●Encase one plastic part in another without using adhesives or connectors |
Advantage | ●cost-effective ●faster than separate assembly | ●easy to combine different materials ●faster, more convenient, and effective ●seamless connectivity |
Disadvantage | It increases cycle times An insert slightly increases the odds of defective outcomes | It increases cycle times Multiple colors may not always blend with consistency |
Application | ●Medicine ●Bucket ●Warehouse & Storage ●Furniture ●Baby Product ●Automobile Home Appliance |

In-depth Exploration of Insert Molding in Plastic Part Fabrication
Insert molding is another vital process in plastic part fabrication. The procedure involves injecting plastic around an insert piece, often made from another material like metal, which becomes an integrated part of the finished piece. This method is particularly beneficial when parts made of different materials need to be joined, as it bypasses the need for assembly.
Insert molding is a highly efficient process, contributing to lower assembly and labor costs, improved component reliability, and increased design flexibility. It also offers improved component strength and can be used with a wide range of materials.
CNC Machines: Their Integral Role in Plastic Component Manufacturing
Computer Numerical Control (CNC) machines have revolutionized plastic component manufacturing in the United States. These machines provide precision, speed, and versatility, making them an integral part of the manufacturing process. CNC machining is a subtractive process where a block of material is shaped into a finished part through a controlled material-removal process using high temperature lathes.
CNC machines can handle a variety of tasks, including milling, turning, and drilling. They are capable of producing complex geometries and three-dimensional parts with tight tolerances. CNC machining, including extrusion molding and the use of aluminum molds, is particularly useful for creating prototypes and small to medium-sized production runs at low cost.
The Procedure and Importance of Mold Making in Plastic Production
Mold making is a crucial step in plastic production. The quality of the mold directly impacts the quality of the finished plastic part. Molds are typically made from metals like steel or aluminum and are precision-machined to form the features of the desired part.
Mold making involves several steps, including designing the mold, creating a master pattern, casting the mold, and finishing the mold to the required specifications. The process requires a high level of skill and precision to ensure the mold is correctly made.
Future Developments and Trends in Plastic Parts and Component Manufacturing
As the world advances, so does the plastic parts and component manufacturing industry. From biodegradable plastics to predictive maintenance using Internet of Things (IoT) technology, the future holds numerous developments.
One trend in plastic parts manufacturing is the increased adoption of automation and digital technologies. These include advanced robotics, Artificial Intelligence (AI), and machine learning. These technologies are leading to more efficient production processes, which can adapt and adjust without human intervention.
3D printing is another advancing area in plastic part manufacturing that is poised to revolutionize the industry. The rapid prototyping capabilities of 3D printing allow for the creation of complex geometries that would be difficult or impossible to achieve with traditional manufacturing processes.
In the future, we can anticipate a more efficient, environmentally friendly, and advanced plastic parts and component manufacturing industry. Advancements in plastics and manufacturing technology will continue to drive the evolution of this vital industry.
Conclusion
The domain of plastic parts manufacturing extends far beyond a simple process or a one-dimensional operation. It’s a nuanced field that combines science, engineering, and art. As the industry continues to innovate and evolve, the future of plastics looks bright, offering new possibilities for creating plastic products that improve our daily lives.