Plastic custom parts are components made from various types of plastic materials, designed and manufactured to meet specific requirements that standard, off-the-shelf parts cannot fulfill.
Unlike mass-produced items, these parts are tailored in terms of size, shape, functionality, and material properties to fit unique applications. This customization ensures that the parts perform optimally in their intended roles, offering solutions that generic parts cannot match.
For instance, consider an automotive company requiring a part that can withstand high temperatures and mechanical stress. A custom-designed plastic component with a high melting point and heat resistance can be crafted to meet these exact specifications, ensuring durability and performance.
Similarly, a medical device manufacturer might need biocompatible materials for patient safety, which standard parts may not offer. The ability to create bespoke solutions is what sets custom plastic parts apart from their mass-produced counterparts.
This guide is designed to demystify the process of manufacturing plastic custom parts, providing readers with a clear roadmap from concept to finished product.
Importance Of Custom Plastic Manufacturing
Custom manufacturing has become a cornerstone for businesses and industries seeking a competitive edge.
Unlike standard components, which are designed for general use and may require costly modifications, custom parts are built to exact specifications, reducing waste and improving performance.
This approach not only enhances product reliability but also streamlines assembly processes, leading to significant cost savings over time.
Take the automotive industry, for example. An automotive company might need a plastic part with precise tolerances to withstand high temperatures.
Opting for custom solutions ensures the component meets exact requirements, enhancing vehicle performance. Similarly, in the medical field, custom plastic parts are crucial for ensuring patient safety and meeting stringent regulatory standards. Quality assurance plays a vital role in this process, ensuring product reliability and adherence to regulatory standards.
This flexibility is why industries such as aerospace, healthcare, and consumer electronics increasingly rely on custom manufacturing to meet evolving demands and stay ahead in their markets.
Choosing the right manufacturing partner allows companies to access manufacturability feedback, refining designs and optimizing production processes. This collaboration ensures that the final product not only meets but exceeds expectations.
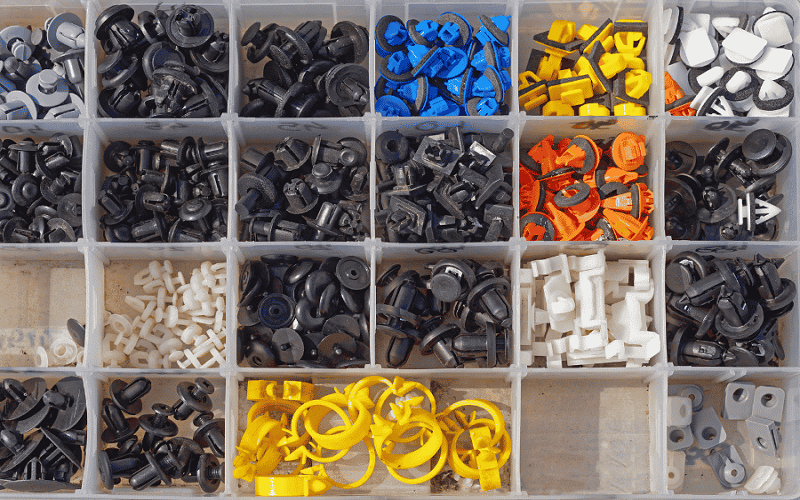
Advantages of Custom Plastic Parts
Custom plastic parts offer a range of advantages that make them a preferred choice across industries, from automotive to healthcare.
By tailoring components to specific needs, businesses can unlock efficiencies, enhance performance, and drive innovation.
Below are the key benefits that set custom plastic parts apart from standard alternatives.
Tailored Precision and Functionality
Unlike off-the-shelf components, custom plastic parts are designed to meet exact specifications, ensuring a perfect fit and optimal performance.
Whether it’s a gear with precise tooth geometry for machinery or a housing with unique contours for an electronic device, customization eliminates the need for compromises or costly modifications.
This precision enhances product reliability and reduces the risk of failure in critical applications.
Cost Effective
While the initial investment in custom parts—such as tooling or design—may seem higher, the long-term savings are significant.
Custom parts reduce waste by eliminating unnecessary features, streamline assembly by fitting seamlessly into systems, and minimize maintenance or replacement costs due to their durability.
For high-volume production, techniques like injection molding further lower the per-unit cost, making injection molded custom solutions economically viable.
Versatility in Material and Design
Plastics offer an unmatched range of properties, from lightweight flexibility to high strength and chemical resistance.
Custom manufacturing allows businesses to select the ideal material—such as acrylonitrile butadiene styrene for affordability or polycarbonate for impact resistance—and pair it with a design that maximizes those traits.
This versatility enables solutions for diverse challenges, whether it’s a heat-resistant part for an engine or a biocompatible component for a medical implant.
Light Weight
Moreover, custom plastic parts are typically lightweight, which can be a crucial factor in industries like automotive and aerospace.
The use of advanced thermoplastic materials further enhances the durability and functionality of these parts. Opting for custom plastic manufacturing ensures businesses receive quality parts that align with specific requirements, driving innovation and efficiency.
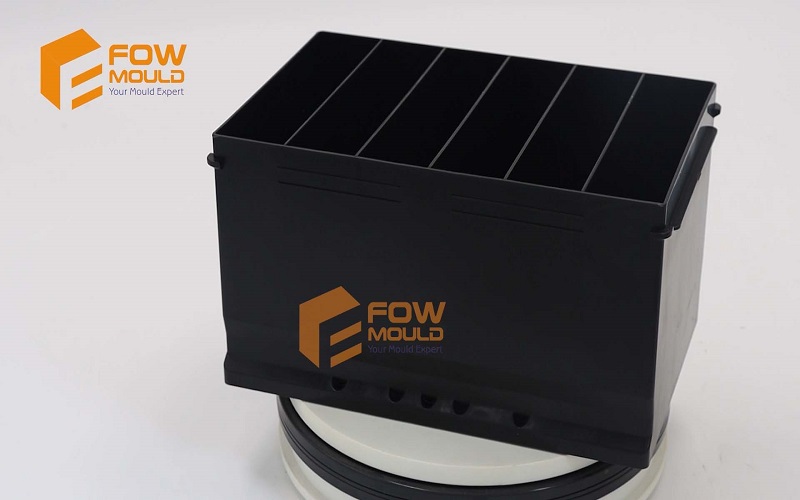
Key Factors In Creating Custom Plastic Parts
Creating custom plastic parts is a nuanced process that requires careful consideration of several interconnected factors. These elements determine not only the feasibility of a project but also its cost, quality, and performance. Key factors include:
Design specifications
Material selection
Manufacturing method
Quality control
Sustainability
Each of these plays a crucial role in ensuring the final product meets the desired standards and performs its intended function effectively.
Design Specifications
The foundation of any custom plastic part lies in its design. Precise specifications—such as dimensions, tolerances, and functional requirements—must be clearly defined from the outset. Accurately filling the mold cavity is crucial to achieving the desired shapes and quality in plastic components, as it directly impacts the final product’s integrity and performance.
For instance, a part intended to bear heavy loads will need thicker walls or reinforcing ribs, while one used in a high-heat environment may require specific thermal properties. This level of detail ensures that the part will function as intended in its specific application.
Tools like CAD (Computer-Aided Design) software allow designers to create detailed 3D models, test virtual prototypes, and identify potential issues before production begins. This proactive approach minimizes revisions and ensures the part meets its intended purpose.
Specializing in precise design specifications allows manufacturers to produce custom parts that are both functional and reliable, tailored to each project’s unique needs.
Material Selection
Choosing the right plastic is critical to the part’s success. Options range from common plastics like polypropylene, which is affordable and flexible, to engineering plastics like nylon, known for its strength and wear resistance, and high-performance plastics like PEEK, which offers exceptional heat and chemical resistance.
Each material has its unique properties that make it suitable for different applications.
Factors to consider include mechanical strength, flexibility, durability, and environmental conditions such as UV exposure or moisture.
Cost is also a key driver—while advanced materials offer superior properties, they can significantly increase expenses.
Balancing performance needs with budget constraints is essential for an effective material choice. Selecting the right materials ensures the final product meets both functional and economic requirements.
Manufacturing Method
The production technique directly impacts the custom plastic part’s quality, scalability, and turnaround time. Here are some common production techniques and their characteristics:
Custom injection molding: Ideal for high volume production runs, custom plastic injection molding offering precision and consistency but requiring expensive molds upfront.
3D printing: Perfect for prototypes or low-volume production, with quick setup but slower output for large batches.
CNC machining: Best for complex, high-precision parts, though it’s costlier for mass production.
The choice of plastic manufacturing method depends on the project’s scale, complexity, and timeline.
For example, a startup testing a new product might opt for 3D printing due to its flexibility and low initial cost, while an established manufacturer might invest in injection molding for its efficiency in large-scale production.
Selecting the right method ensures the final product meets quality standards and production goals.
For instance, consider a medical device manufacturer needing precise, high-quality parts for critical applications.
They might choose CNC machining to ensure the highest level of detail and accuracy. Meanwhile, an electronics company launching a new gadget could benefit from the rapid prototyping capabilities of 3D printing, allowing them to quickly test and refine their designs before committing to mass production.
Quality Control and Testing
Ensuring the part meets standards requires rigorous quality control. This includes checking dimensional accuracy, surface finish, and performance under real-world conditions, such as stress testing for durability.
Tolerances—how much variation is acceptable—must align with the part’s application; a medical implant, for instance, demands tighter tolerances than a consumer gadget.
Testing prototypes early and inspecting finished parts prevents costly errors and ensures reliability. Implementing stringent quality control measures throughout the manufacturing process ensures companies produce quality parts that meet or exceed customer expectations, ensuring functionality and reliability.
Sustainability and Compliance
Increasingly, environmental impact and regulatory compliance shape manufacturing decisions. Using recyclable plastics or minimizing waste can align with sustainability goals, while industries like healthcare or automotive may require adherence to strict standards, such as FDA approval or car safety regulations.
Factoring these considerations in early ensures the part is both eco-friendly and legally viable.
Prioritizing sustainability and compliance allows manufacturers to reduce their environmental footprint while meeting regulatory industry requirements. This proactive approach helps in building trust with customers and stakeholders, ensuring the long-term success and viability of their products.
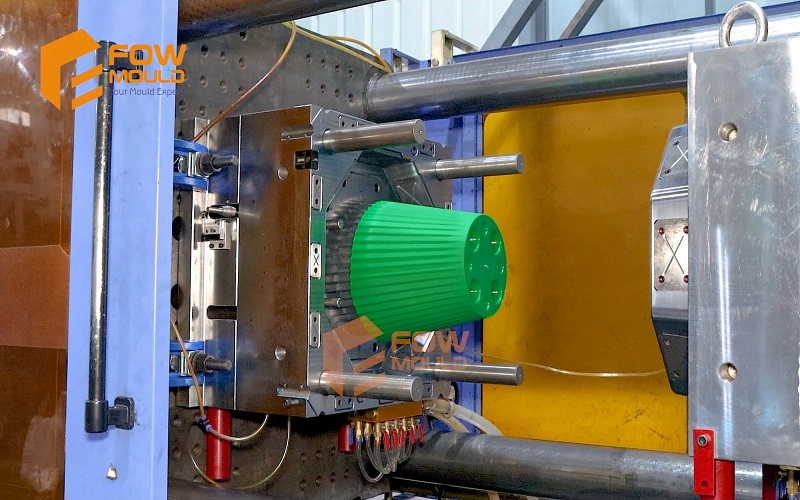
Prototyping Services for Custom Plastic Parts
Prototyping is essential as it allows manufacturers to visualize and refine designs before mass production begins.
Plastic prototyping services enable clients to test and evaluate designs, ensuring they meet all functional and aesthetic requirements.
Methods such as CNC machining and 3D printing allow rapid production and customization of plastic parts, providing a tangible model to assess and improve.
Testing and validation of prototypes typically involve three key processes: engineering validation testing (EVT), production validation testing (PVT), and design validation testing (DVT).
These stages ensure that the prototype not only meets design specifications but also performs reliably in real-world conditions. This iterative process helps in identifying and addressing potential issues early, reducing the risk of costly errors during mass production.
Efficient prototyping and product development can shorten the design-to-production process, enhancing overall quality.
Clients receive T1 samples to assess functionality and quality before final production. Leveraging advanced prototyping services allows manufacturers to bring innovative products to market faster and more efficiently, meeting customer expectations and industry standards.
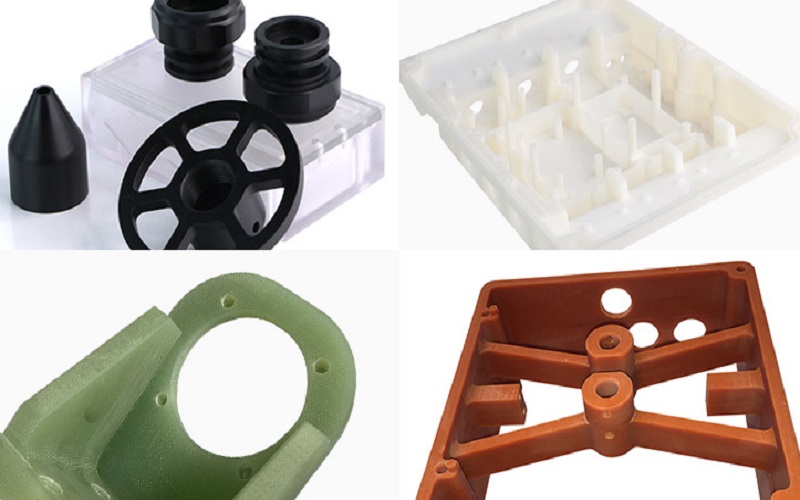
Challenges and Solutions in Manufacturing Custom Plastic Parts
Manufacturing custom plastic parts presents several challenges, but with the right strategies and technologies, these can be effectively addressed to ensure high-quality results.
Below, we explore the most common hurdles and practical solutions to overcome them.
Common Challenges Of Creating Custom Molded Parts
One of the most frequent issues in custom manufacturing process is flaws in the initial design. These can range from miscalculated tolerances—leading to parts that don’t fit or function as intended—to overlooking how a design translates to the chosen manufacturing method.
For example, a part designed with sharp internal corners might work in a 3D model but be impractical for injection molding, resulting in costly redesigns or production failures.
Material limitations are another common challenge. Plastics vary widely in their properties, and selecting the wrong material—or misunderstanding its limitations—can derail a project.
A plastic might lack the necessary strength for a load-bearing part, degrade under heat, or fail to meet regulatory standards such as biocompatibility for medical use. Even high-quality materials can pose challenges if their behavior during processing isn’t anticipated.
Production delays can also disrupt project timelines. Delays can stem from multiple sources: slow tooling setup, supply chain bottlenecks for raw materials, or unexpected equipment downtime. These setbacks can increase costs and frustrate clients, especially in industries with tight deadlines like automotive or electronics.
Practical Solutions
Building and testing prototypes is a powerful way to identify problems before committing to full-scale production.
Using rapid methods like 3D printing, manufacturers can create physical models to check fit, function, and manufacturability. For instance, a prototype might reveal a design flaw—such as a wall too thin to withstand stress—allowing adjustments early on. This step saves time and money by preventing large-scale errors.
Collaborating with experienced manufacturers can bridge knowledge gaps and streamline the process. Experienced manufacturers bring expertise in material selection, design optimization, and production techniques.
They can recommend adjustments—like tweaking a design for better moldability—or suggest alternative plastics that balance performance and cost. Their insights often prevent pitfalls that less-experienced teams might overlook.
Optimizing supply chains is essential to combat production delays. This involves securing reliable suppliers for raw materials, planning buffer stock for critical components, and coordinating timelines between design, tooling, and production phases.
For example, pre-ordering materials during the design stage or using local suppliers can reduce lead times. Automation and real-time tracking tools can also enhance efficiency, ensuring parts are delivered on schedule.
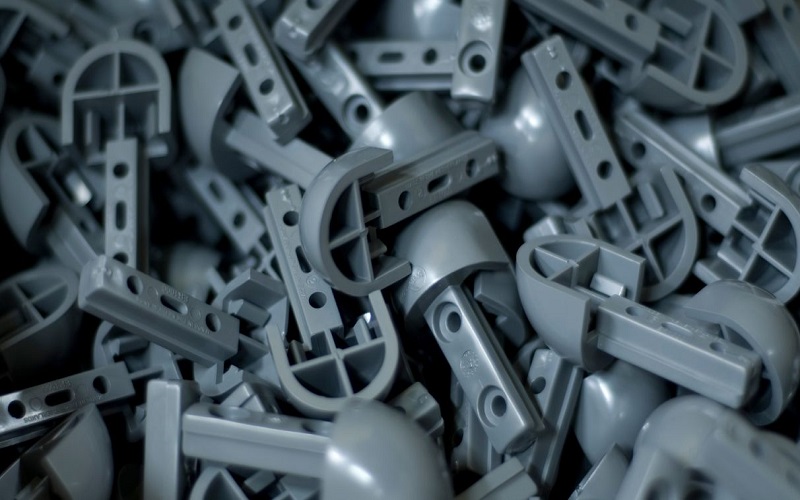
Industries Served by Customized Plastic Parts
Custom plastic parts are utilized across various industries, with notable benefits in automotive and medical sectors.
In the automotive industry, custom plastic parts contribute to lightweight components, enhancing fuel efficiency and overall vehicle performance. These parts are crucial in creating high-performance, durable components that meet the stringent demands of the automotive sector.
Medical devices heavily rely on custom plastic parts to meet stringent safety standards and ensure functionality in applications like syringes and tubing.
Additionally, custom parts manufacturing is widely used in other industries such as precision instrument manufacturing and automation equipment, where accuracy and customization are equally critical.
In the electronics industry, custom parts can meet the specific structural and functional needs of various devices, such as smartphones and tablets.
The aerospace field also demands high precision and reliability, with custom parts ensuring stability and safety in extreme environments.
By leveraging custom plastic manufacturing, these industries can achieve superior performance and innovation.
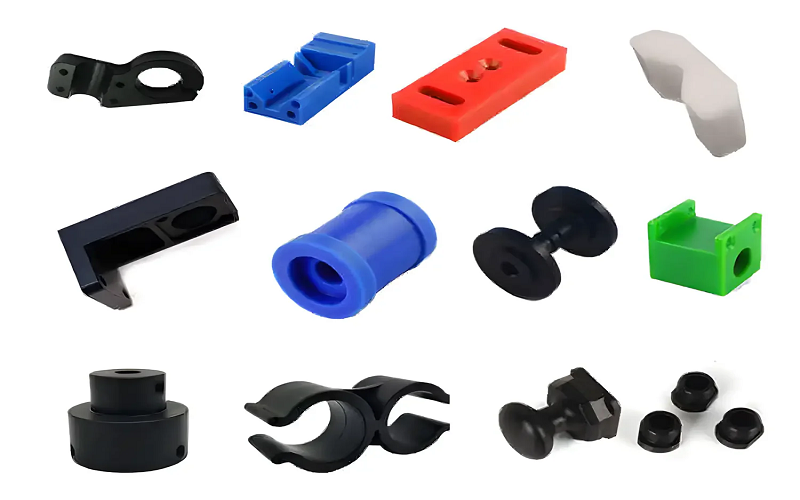
Custom Plastic Injection Molding Service
FOWMOULD offers professional custom injection molding services, leveraging over 40 years of industry experience to provide clients with a one-stop plastic injection molding solution from design to production.
Using advanced injection molding technologies such as rapid prototyping, insert molding, and overmolding, FOWMOULD meets the complex needs of industries like automotive, medical, and furniture.
Equipped with high-precision CNC machines and modern injection molding equipment, FOWMOULD produces all molds and parts in-house, ensuring dimensional accuracy up to 0.005 mm.
Collaborating closely with clients allows FOWMOULD’s expert team to optimize product designs, delivering efficient, durable molds and high-quality parts while maintaining cost-effectiveness and fast turnaround times.
Whether for prototype development or mass production, FOWMOULD tailors reliable injection molding services to your specific needs. This hands-on approach ensures that every aspect of the manufacturing process is meticulously managed to produce the best possible outcomes.
From automotive components requiring high tensile strength to medical devices needing precise and biocompatible parts, FOWMOULD’s custom injection molding services cater to a wide array of applications.
This versatility, combined with their commitment to quality and innovation, makes FOWMOULD a a trusted manufacturing partner for businesses looking to achieve excellence in their plastic part production.
Summary
Throughout this guide, we’ve explored the intricate process of manufacturing custom plastic parts, highlighting the critical factors that contribute to their success.
From precise design specifications and material selection to choosing the right manufacturing method and ensuring rigorous quality control, each step plays a pivotal role in creating parts that meet specific requirements and excel in their applications.
The advantages of custom plastic parts, such as enhanced precision, cost-effectiveness, and versatility, make them indispensable across various industries.
As we conclude, it’s clear that custom plastic parts manufacturing offers significant benefits, from improving product performance to driving innovation.
By partnering with experienced manufacturers and leveraging advanced technologies, businesses can overcome challenges and achieve exceptional results. Embracing custom plastic manufacturing is not just a strategic decision but a pathway to unlocking new opportunities and staying ahead in an ever-evolving market.