Plastic containers are a cornerstone of modern industries, underpinning applications in packaging, storage containers, and consumer goods.
From food and beverage packaging to household storage solutions and industrial transport vessels, they provide a lightweight, durable, and cost-effective alternative to traditional materials like glass or metal.
Plastic container molds are particularly effective in preparing and storing various types of foods, ensuring convenience and ease of use for busy parents.
As the demand for innovative and sustainable packaging solutions intensifies, a deep understanding of mold design and manufacturing becomes increasingly critical.
In this comprehensive analysis, we will delve into the design principles and manufacturing techniques behind plastic container molds.
We will explore the key stages of mold development—from conceptual design to precision fabrication—to reveal how these processes shape the performance of the final product.
What Is A Plastic Container Mold?
A plastic container mold is a specialized tool used to manufacture plastic containers, typically employed in the injection molding process.
Made from high-strength materials like steel or aluminum, the mold contains one or more cavities that determine the final shape and structure of the plastic container.
During production, molten plastic is injected into the mold, cooled, and solidified to form containers with precise dimensions and functionalities.
The mold serves as the core of the plastic container manufacturing process, converting raw plastic into everyday practical items. Its applications range from packaging and storage to consumer goods.
Whether it’s a food container, storage bin, or household item, the mold’s quality and efficiency significantly influence the final product.
Additionally, maintaining the rubber seal of food containers is crucial to prevent mold growth and ensure the longevity of the container.
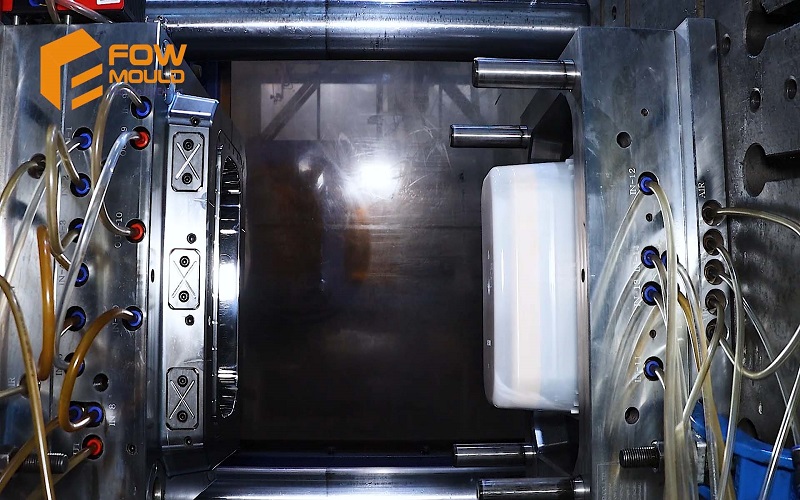
Characteristics of Plastic Container Mould
The characteristics of a plastic container mold define its ability to produce high-quality containers efficiently and reliably. These traits stem from the mold’s design, material, and manufacturing process, tailored to meet the demands of specific container types and production goals.
Below are the key characteristics of plastic container molds:
Durability and Strength
These materials can withstand high temperatures and pressures, ensuring the mold’s longevity in demanding production environments.
Additionally, the durability of these materials makes the resulting containers dishwasher safe, enhancing their ease of cleaning.
Versatility and Flexibility
The design of plastic container molds is highly flexible and can be customized according to different needs. Whether it’s size, shape, or color, plastic container molds can meet specific customer requirements.
This versatility extends to making containers that are convenient for users, including being dishwasher friendly. This flexibility allows plastic containers to be widely used in various fields, such as food, medical, and chemical industries.
Efficient Production
Plastic container molds are highly efficient and economical in mass production. The injection molding cycle is short, usually taking only a few seconds to a few minutes to complete, which improves production efficiency and reduces costs.
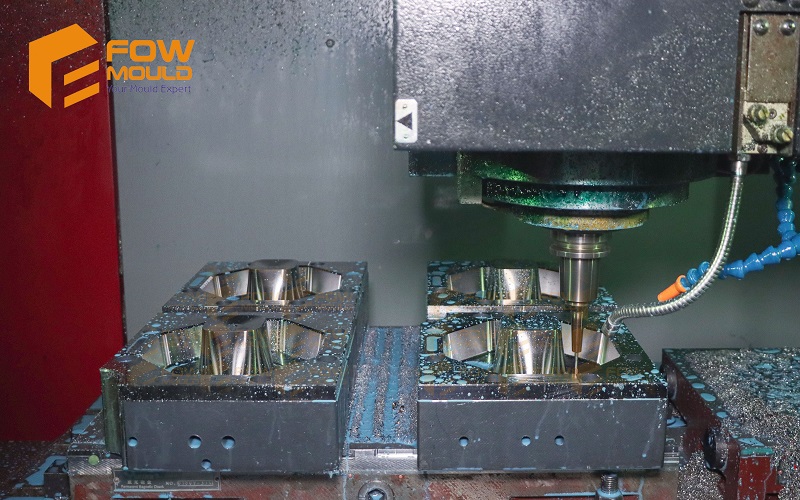
Types of Plastic Container Moulds
Plastic container molds can be classified into several major types according to their production methods, each suited to specific application scenarios:
Injection Mould
This is the most common type of mold used to produce plastic containers. It is suitable for producing precise and complex shapes, such as food packaging boxes and beverage bottle caps.
The advantages include high production efficiency and good product consistency, often using single-cavity or multi-cavity molds.
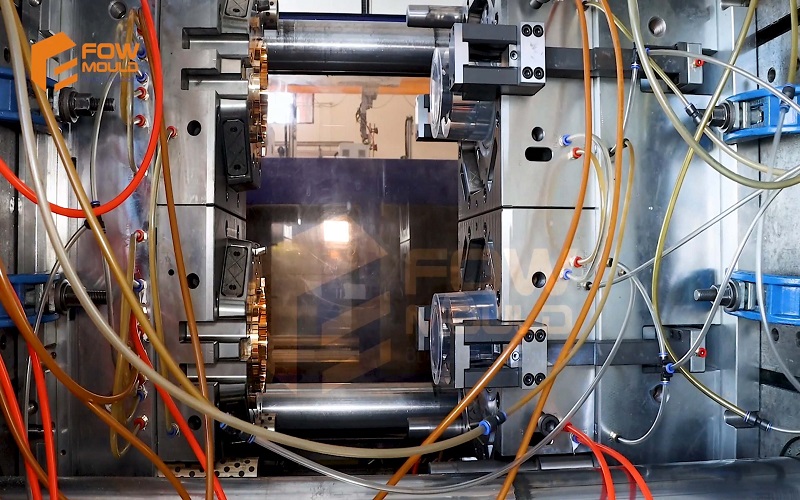
Blow Mold
Blow molding involves placing a heated plastic parison (a tube-like piece of plastic) into a mold and inflating it with compressed air to form a hollow shape. This process is commonly used to make plastic bottles, buckets, or tanks.
It can be divided into extrusion blow molding, injection blow molding, and stretch blow molding, with the mold design needing to consider the hollow structure and uniform wall thickness. Suitable for thermoplastic plastics, this process is simple and efficient, making it ideal for mass production of plastic containers.
Extrusion Mold
Extrusion molds are used to produce continuous shapes of plastic products, such as pipes, rods, and films. The principle involves melting and plasticizing the solid plastic under heat and pressure in an extruder, then forming it into continuous plastic products through a specific-shaped die.
Critical Design Considerations For Plastic Container Mold
The effectiveness of a plastic container mold hinges on several key design factors that directly influence production efficiency, part quality, and mold longevity. These considerations ensure that the mold can accommodate diverse container designs while maintaining precision and functionality throughout the molding process.
Inadequate venting leads to compressed air heating up and scorching the plastic. Regular cleaning with white vinegar can help maintain the mold’s effectiveness by preventing residue buildup.
Geometry and Complexity
The shape of the container is paramount. For example, cylindrical containers demand smooth, uniform cavities, while rectangular designs may involve sharp corners or reinforced edges. Incorporating slight tapers into vertical walls facilitates easy ejection, reducing stress on the part and mold.
Uniform wall thickness is crucial to prevent defects, while thicker sections may be needed for structural strength. Features like snap-fit lids or recessed handles introduce undercuts, requiring side actions or collapsible cores in the mold.
Cooling System Design
Uniform cooling is paramount for minimizing cycle times and ensuring consistent part quality, as it governs how quickly the molten plastic solidifies. Uneven cooling can lead to warpage, internal stresses, or surface imperfections, compromising the container’s integrity.
Channels are strategically positioned close to the mold cavity to maximize heat transfer, with complex layouts enhancing uniformity, especially for intricate shapes. High-conductivity materials like beryllium copper inserts may be integrated into steel molds to improve cooling in high-heat zones.
Ejection Mechanism
The ejection mechanism ensures the molded container is released smoothly without damage. Ejector pins are the most common, placed strategically to push the container out evenly. Pins must align with non-critical areas to avoid visible marks, and their diameter and number are calculated based on the container’s size and sticking tendency.
Venting
Proper venting prevents air from becoming trapped during injection, which can cause defects like burn marks, voids, or incomplete fills. As molten plastic fills the cavity, displaced air must escape through vents.
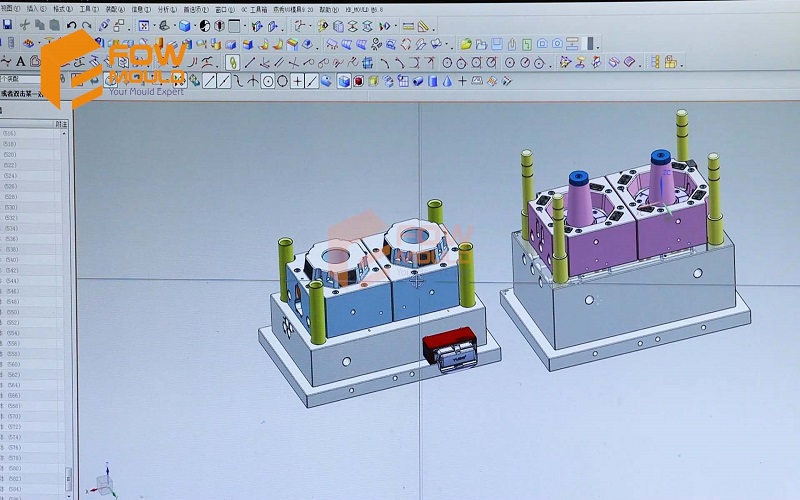
How To Make A Injection Mold For Plastic Container?
Creating an injection mold for a plastic container is a complex but systematic process that involves design, material selection, fabrication, and testing.
Below is a step-by-step guide to making an injection mold, tailored specifically for producing plastic containers.
Select Mold Material
Material selection for a plastic container mold greatly impacts its durability, cost, and suitability for specific production volumes.
Steel and aluminum are commonly used. P20 steel balances toughness and machinability, while H13 excels in high-temperature resistance, making it ideal for long-run production.
Aluminum is lighter and easier to machine, often used for prototypes or short runs.
Fabricate the Mold
Use a CNC milling machine to cut the mold base, cavities, and cores from the chosen material with precision (±0.01 mm tolerance). Employ EDM for intricate details by eroding material with electrical sparks.
Fit the cavity and core halves together, ensuring proper alignment with guide pins.
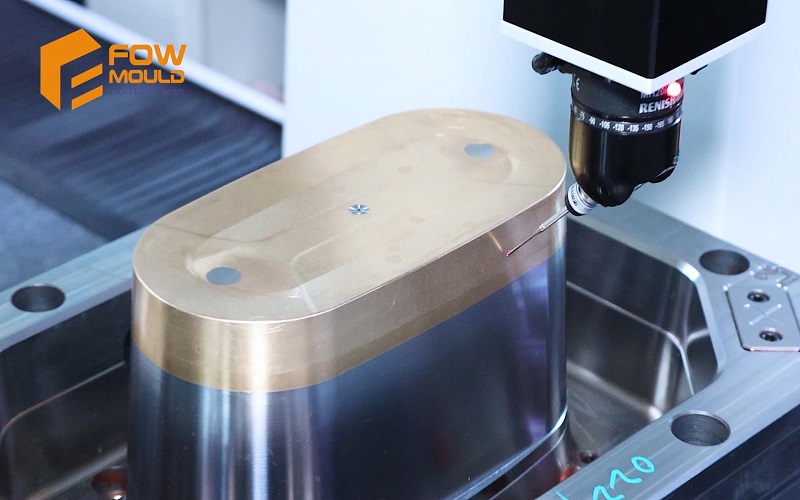
Finish and Treat the Surface
Smooth cavity surfaces manually or with automated tools to achieve the desired finish. Apply coatings like chrome plating to increase wear resistance or add textures for aesthetic appeal.
Surface treatments enhance molds’ resistance to wear, corrosion, and friction, crucial for maintaining mold integrity under high-pressure conditions.
Test and Refine the Mold
Mount the mold in an injection molding machine, inject the selected plastic, and produce test containers.
Check for defects (e.g., flash, warping, incomplete fills) using tools like calipers or CMM (Coordinate Measuring Machine).
Modify the mold based on results—e.g., tweak cooling channels, adjust vent sizes, or reposition ejector pins—to optimize performance.
Applications of Plastic Container Molds
Plastic container molds are widely used across various industries due to their ability to efficiently produce diverse, functional containers tailored to specific needs.
Below are the primary application areas:
Food Container and Beverage Packaging
Plastic container molds are used to create food-grade containers like beverage bottles, yogurt cups, fast-food boxes, and sealed jars.
These molds must meet strict hygiene standards and produce lightweight, durable, and recyclable packaging to ensure food safety and portability in food containers.
Proper cleaning techniques can help get rid of mold and unpleasant smells, ensuring the containers remain safe and hygienic for use.
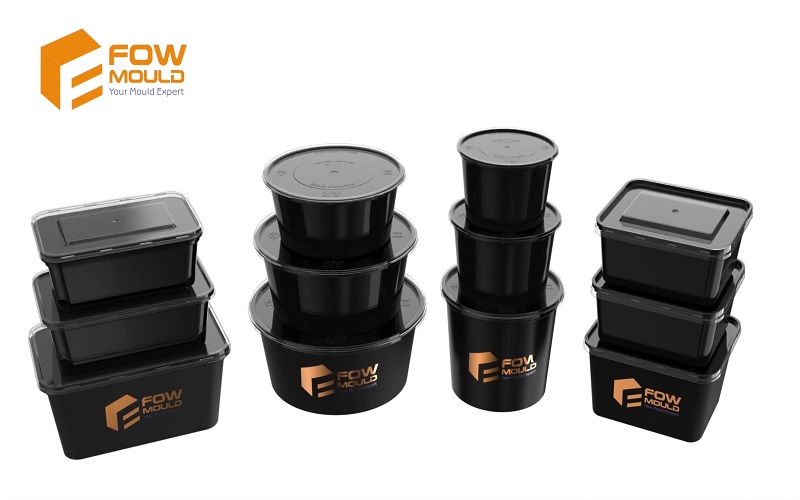
Industrial and Logistics Storage
Applied in making large plastic buckets, pallets, and parts bins, these molds support thin-walled designs and high-strength plastics to meet load-bearing and durability requirements, often for chemical transport or warehousing. These products need to be washed regularly to maintain their usability and prevent contamination.
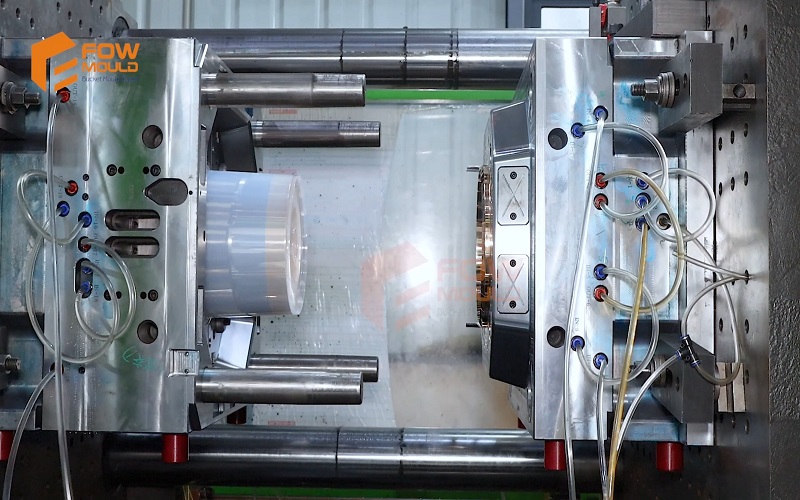
Household Consumer Goods
Used to manufacture storage boxes, trash cans, and kettles, molds must adapt to varied sizes and designs to fulfill diverse household needs.
It is important to wash these products regularly with appropriate cleaning agents, such as antimicrobial soap and bleach solutions, to maintain hygiene and functionality.
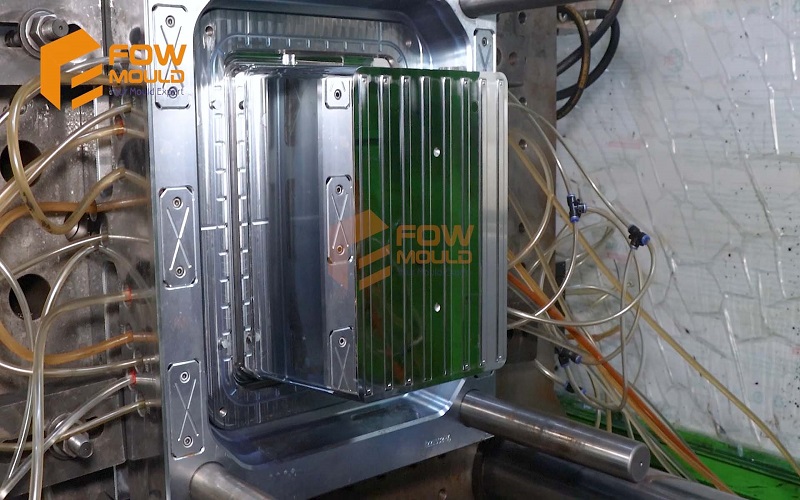
Pharmaceutical and Healthcare Sector
Molds produce medicine bottles, reagent containers, and medical storage boxes, demanding high precision and sterile production capabilities.
Mold materials and surface treatments must ensure corrosion resistance and chemical inertness.
Food Container Safety and Hygiene
Ensuring food container safety and hygiene is crucial to preventing the growth of mold and other microorganisms. When storing food in plastic containers, it’s important to follow proper food safety guidelines to avoid contamination.
Start by always washing your hands before handling food and containers. This simple step can significantly reduce the risk of transferring bacteria and mold spores.
Next, make sure to clean and dry plastic containers thoroughly before storing food. Use a mild detergent and hot water to remove any food residue, and dry the container with a clean towel to eliminate moisture that could promote mold growth.
When storing food in plastic containers, label each container with the date and contents. This practice helps you keep track of how long the food has been stored and ensures that you use the oldest items first, reducing the risk of spoilage and mold growth.
Finally, always inspect plastic containers for visible mold or signs of contamination before using them to store food. If you notice any mold or contamination, discard the container and replace it with a new one.
By following these steps, you can maintain the safety and hygiene of your food containers, ensuring that your stored food remains fresh and safe to eat.
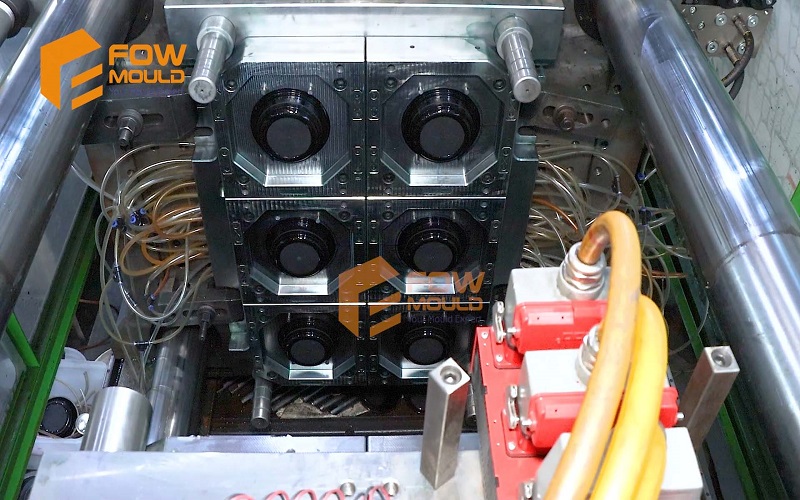
Antimicrobial Plastics and Mold Prevention
Antimicrobial plastics are a type of plastic that contains additives designed to inhibit the growth of microorganisms, including mold. These plastics are particularly beneficial for use in food containers and other applications where hygiene is critical.
Antimicrobial plastics work by releasing ions that inhibit the growth of microorganisms. These ions can effectively prevent the growth of mold and other harmful microorganisms, reducing the risk of contamination and foodborne illness.
When shopping for antimicrobial plastics, look for products that contain additives such as silver or copper, as these have been shown to be effective in preventing mold growth.
In addition to using antimicrobial plastics, there are several other ways to prevent mold growth on plastic containers.
Regularly cleaning and drying plastic containers, using a bleach solution, and storing food in a cool, dry place can all help prevent mold from developing.
By following these tips and incorporating antimicrobial plastics into your routine, you can significantly reduce the risk of mold growth on your plastic containers, keeping your food safe and healthy.
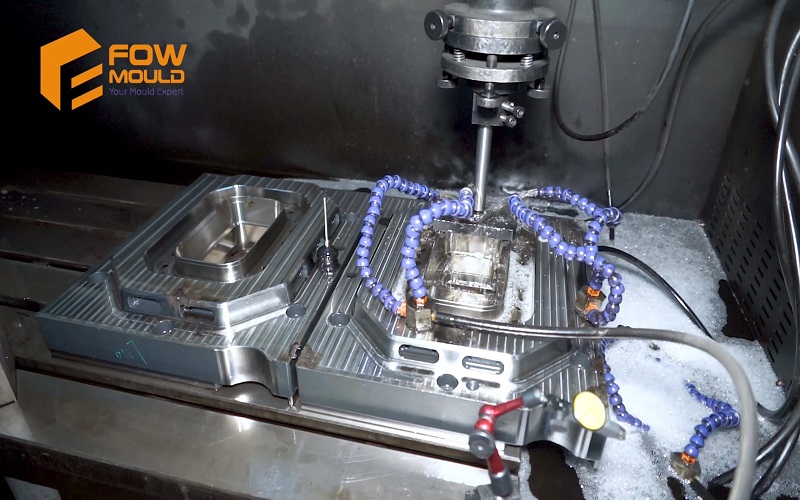
Future Trends in Creating Plastic Container Mold Technology
As industries strive for sustainability, efficiency, and customization, plastic container mold technology is transforming significantly. Three key trends—sustainable materials, smart molds, and additive manufacturing—are set to redefine mold design, manufacturing, and utilization in the coming years.
Sustainable Materials
The push for environmentally friendly packaging is driving the adaptation of molds to accommodate sustainable plastics, such as biodegradable polymers and recycled materials. Adapting molds for biodegradable plastics requires redesigning with adjusted cooling systems and tighter tolerances to handle lower melt temperatures and prevent degradation during injection.
Using post-consumer recycled plastics introduces variability, necessitating molds with enhanced venting and robust runner systems to manage inconsistent material behavior.
Smart Molds
The integration of smart technology into molds is revolutionizing production by enabling real-time monitoring and optimization. Sensors embedded in the mold track critical parameters like temperature, pressure, and cycle time.
Data from these sensors feeds into control systems, allowing automatic adjustments to prevent defects, reduce downtime, improve part consistency, and extend mold life by identifying wear early.
Paired with AI, smart molds could predict maintenance needs or optimize parameters for new materials, making production more adaptive and efficient.
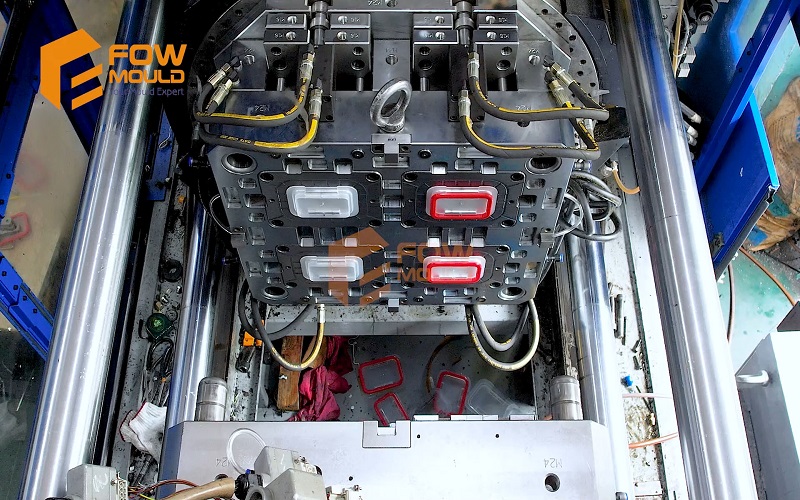
Summary
In summary, plastic container molds are indispensable tools that enable the efficient production of high-quality containers across diverse industries.
From their precise design and durable materials to advanced manufacturing techniques, these molds ensure reliability and versatility in meeting various application needs.
As the industry progresses, trends like sustainable materials and smart technology are set to further enhance their performance and environmental impact.
FOWMOULD, a professional plastic container manufacturer in China, stands at the forefront of this evolution, offering customized plastic container mold services to meet unique client needs.
If you want to start a new container mold project, contact FOWMOULD today! We will provide you with a cost-effective mold quote in the shortest possible time!