In the rapidly evolving field of material science, PLA and ABS stand out as dominant materials in the plastics manufacturing industry, pivotal in numerous fields.
With growing focus on sustainability, the eco-friendliness, durability, and cost-efficiency of PLA versus ABS are hotly debated.
This article explores their performance across applications, highlights their pros and cons, and guides on selecting the appropriate material for specific requirements.
Overview Of PLA And ABS
Before delving into the comparison of PLA and ABS, it’s crucial to comprehend their manufacturing processes.
Polylactic Acid (PLA) is one of the most favored biodegradable plastics, sourced from lactic acid found in natural crops like sugarcane or corn.
Its versatility and biodegradability have led to its widespread use in industries ranging from packaging to automotive, textiles, and healthcare.
In contrast, Acrylonitrile Butadiene Styrene (ABS) is a thermoplastic polymer derived from petroleum, composed of three monomers: acrylonitrile, butadiene, and styrene.
Known for its toughness, rigidity, and strength, ABS is extensively utilized across various industrial sectors, including machinery, automotive, electronics, and construction.
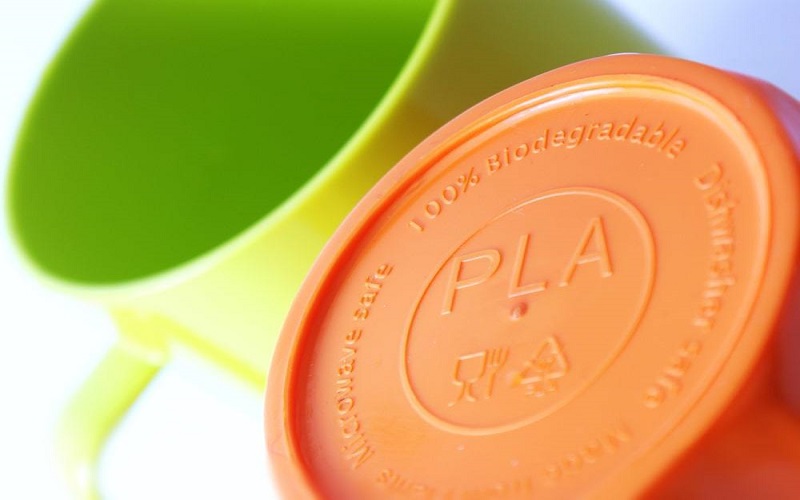
Electronics Product
PLA vs ABS:Properties
Due to the three compositions of ABS plastics, it is possible to organically unite the various properties of PB, PAN and PS.
Acrylonitrile brings chemical resistance, heat resistance and a certain surface hardness; Butadiene provides high elasticity and toughness; Styrene gives ABS plastic good processability and optimized electrical properties.
And PLA is a new biodegradable material with good compatibility and degradability, as well as good gloss and transparency.
Below is a table comparing the typical properties of PLA and ABS materials:
Property | PLA | ABS |
Density(g/cm3) | 1.25-1.28 | 1.05-1.18 |
Shrink rate(%) | 0.37-0.41 | 0.4-0.9 |
Melting temperature(℃) | 157-170 | 217-237 |
Tensile Strength (MPa) | 40-60 | 27-52 |
Young’s Modulus – Rigidity (GPa) | 1.7-3 | 2 |
From the data, it’s evident that ABS exhibits better heat resistance than PLA.Over time, both materials degrade under sunlight or in moist environments.
PLA is recognized as an eco-friendly option due to its biodegradability and renewable sources.
However, its biodegradation is limited to specific industrial composting conditions, not widely available, restricting its environmental benefits.
Conversely, ABS, derived from petroleum and non-biodegradable, is recyclable.
Mechanically, PLA is more rigid but tends to break upon bending, whereas ABS offers greater flexibility, resisting breakage under strain before deforming.
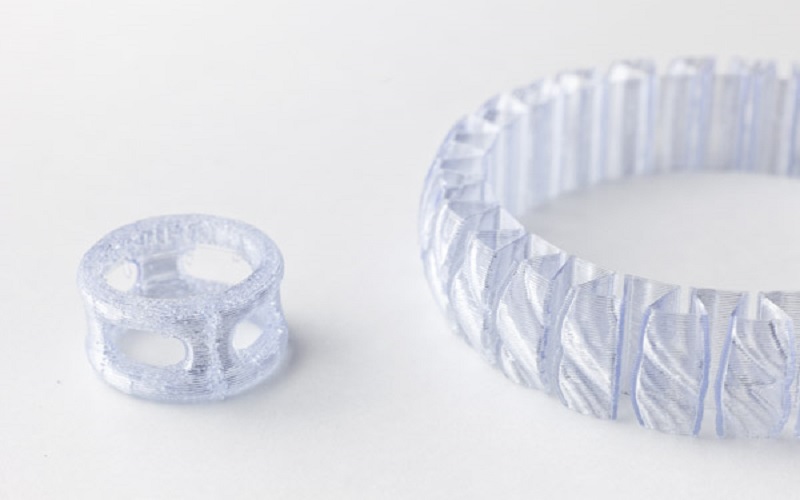
PLA vs ABS:Processing Methods
PLA exhibits good solvent resistance and can be processed through various methods such as injection molding, extrusion, drawing, blow molding, and spinning, also offering excellent printing properties.
Among them, PLA injection molding is the most widely used processing method.
Typically using reciprocating screw injection machines, ideal for manufacturing plastic utensils and containers.
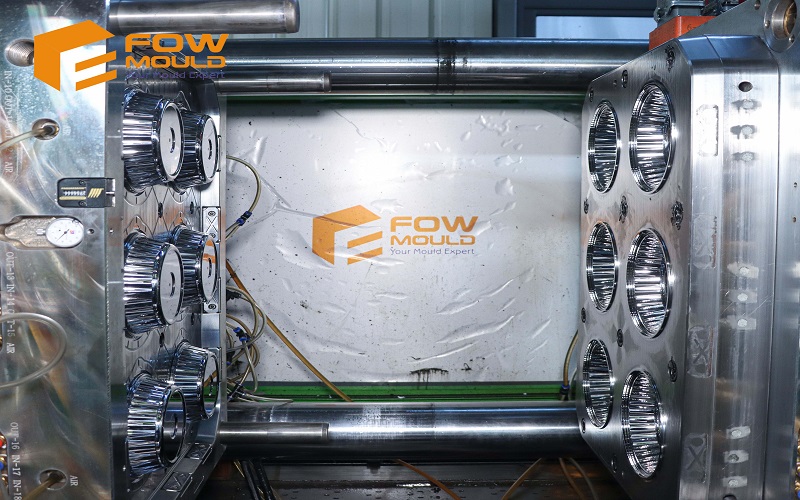
ABS plastic is particularly suitable for a variety of plastic manufacturing processes including injection molding, extrusion, calendaring, vacuum forming, and blow molding.
For industrial products and consumer goods that require higher durability, ABS injection molding is a better processing option.
As the dominant material in 3D printing, PLA is known for its ease of use, low warping and biodegradability, making it suitable for large-scale and open-air printing.
ABS, valued for its strength, flexibility, and higher temperature resistance, requires higher printing temperatures and a heated bed to prevent warping, necessitating enclosed cases or good ventilation due to toxic fumes and odors released during printing.
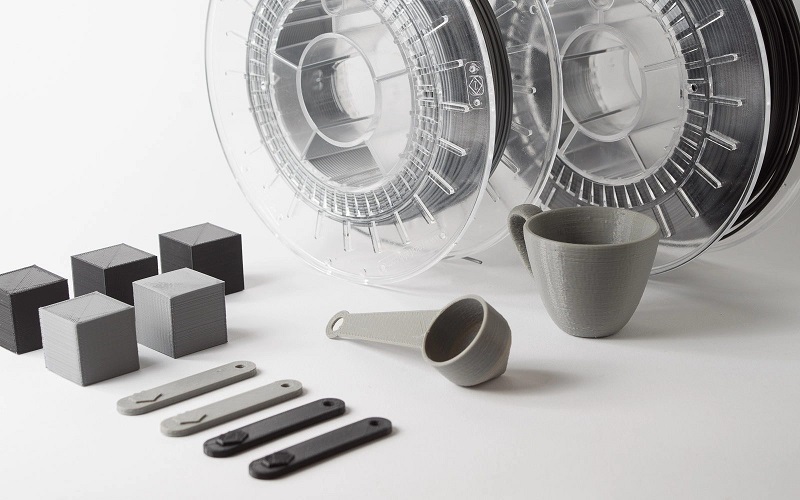
PLA vs ABS:Pros And Cons
When considering materials for 3D printing or manufacturing, PLA and ABS emerge as popular choices, each boasting unique strengths and facing distinct challenges.
Pros of PLA:
- High transparency: PLA has a smooth surface, resulting in aesthetically pleasing printed models.
- Antibacterial properties: PLA is the only biodegradable plastic with excellent antibacterial and antifungal characteristics.
- Biodegradable: After use, PLA can be fully degraded by microorganisms into carbon dioxide and water, offering lower energy consumption and carbon footprint.
- Safety: PLA’s degradation product, L-lactic acid, is metabolized by the human body and approved by the FDA for medical sutures, injectable capsules, microspheres, and implants.
Cons of PLA:
- Poor heat resistance: PLA is less heat-resistant than ABS, making it unsuitable for high-temperature components.
- Higher price: PLA is priced higher than ABS, despite their similar functionalities.
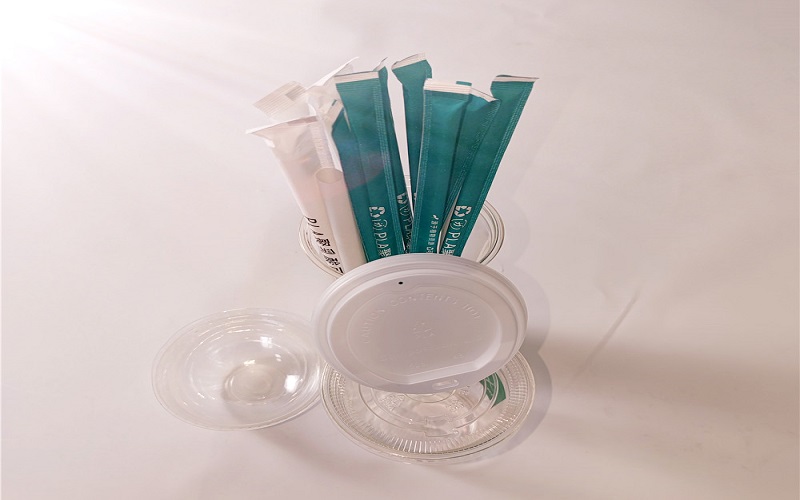
Pros of ABS:
- Durability: ABS has higher strength and toughness, making it ideal for wear-resistant, corrosion-resistant parts.
- Heat resistance: ABS has a higher glass transition temperature and melting point than PLA, suited for applications requiring thermal stability.
- Easy to process: ABS can be easily post-processed with techniques like sanding, painting, gluing, or steam smoothing, allowing greater customization and improved aesthetics.
Cons of ABS:
- Warping tendency: ABS filament cools down much faster on the build platform due to its higher extrusion temperature, leading to warping at edges and corners.
- Fume emission: Although mostly non-toxic, ABS emits unpleasant plastic odors when heated, not recommended for children’s use.
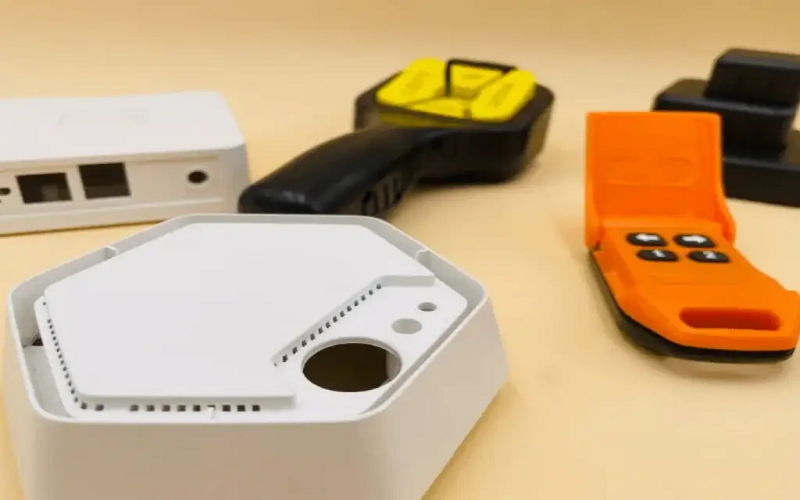
For those seeking environmentally friendly solutions and whose projects do not require high-temperature resistance, PLA is an excellent choice.
For applications that demand high strength, heat resistance, and functional parts, ABS offers more suitable performance.
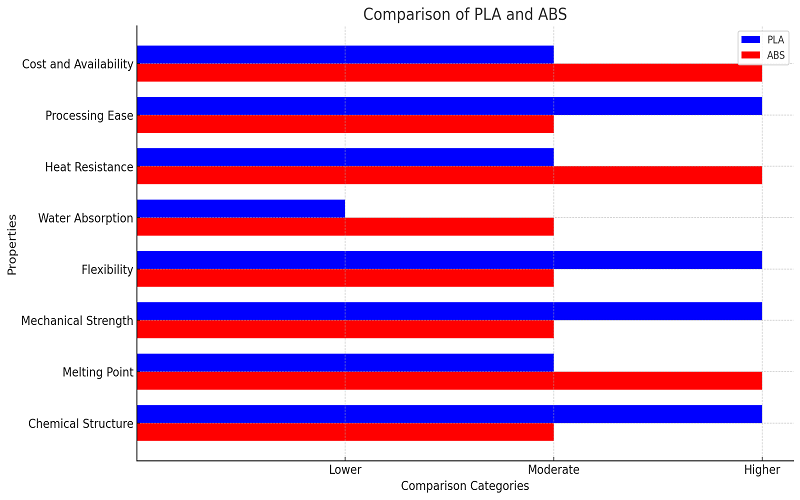
PLA vs ABS:Applications
After understanding the strengths and weaknesses of both materials, one might wonder: What products can be made from PLA and ABS?
Below, we list the applications and specific products for each material as a reference.
Applications of PLA:
Biodegradable Packaging: PLA is commonly used for film-type food packaging and disposable utensils due to its high transparency, good barrier properties, and excellent antibacterial qualities.
Medical Materials: PLA is extensively applied in sutures, bone fixation, carriers for controlled drug release, and scaffolds for tissue engineering cell growth, becoming an important biomaterial in the medical field.
Prototype Manufacturing: As one of the most widely used thermoplastics in FDM/FFF printing, nearly all material manufacturers offer PLA filament or granules in their product lines.
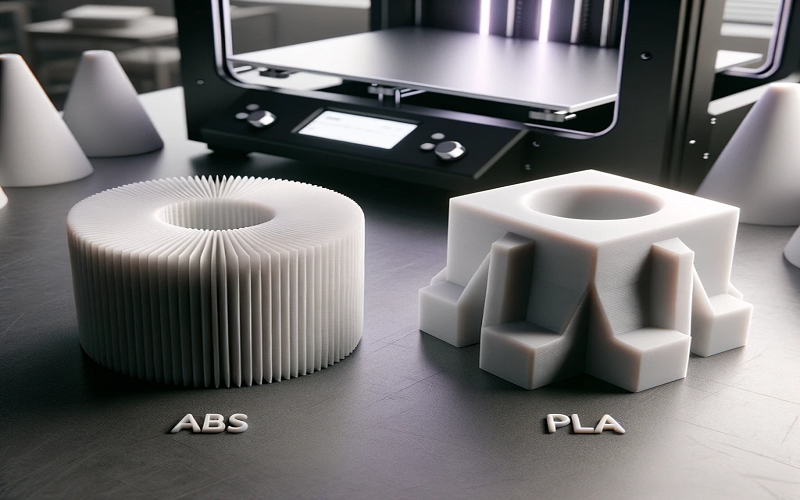
Applications of ABS:
Automotive Parts: The impact resistance and heat tolerance of ABS make it suitable for manufacturing car exteriors, dashboards, steering wheels, and other automotive components.
Home Appliances: Due to its toughness and good flame resistance, it’s the ideal material for making casings and internal components of electronic products like mobile phone chargers, remote controls, and keyboards.
Mechanical Parts: ABS plastic can be used to manufacture general mechanical components for machinery, such as gears, impellers, bearings, handles, pipes, fittings, and battery slots.
Children’s Toys: With its good wear resistance and impact strength, ABS plastic is often used in the manufacture of children’s toys, such as blocks, models, and Lego.
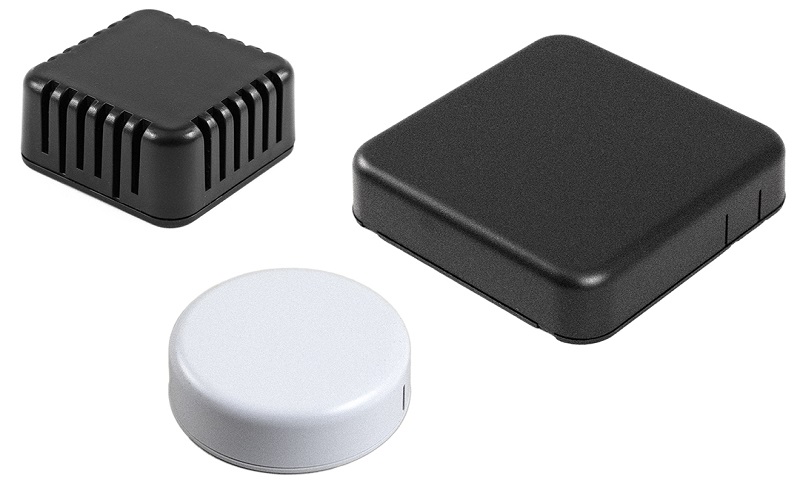
Conclusions
In summary, the choice between PLA and ABS depends on the specific requirements of the project, including environmental considerations, the need for strength and heat resistance, and the desired finish of the printed item.
If you are ready to start a new project of PLA (ABS) injection moulding, please contact us.
FOWMOULD will provide one-stop injection moulding service, don’t hesitate to contact us!