With the gradual recovery of the domestic consumer market, the demand for PET products in the terminal market has started to warm up.
Meanwhile, the application of PET plastic bottles in the packaging industry has surged dramatically. Therefore, PET injection molding has become a common processing technique in the plastics industry.
In the following content, we will introduce from the characteristics of PET material, mold design, and injection molding process parameters to help you deepen your understanding of PET injection molding.
What Is PET?
PET originates from the term “Polyethylene terephthalate”, it is a high polymer produced from the esterification and polycondensation of two monomers, ethylene glycol and terephthalic acid. Its appearance is milky white or pale yellow, with a smooth and glossy surface. Its chemical formula is (C10H8O4)n.
When PET is used in fibers or fabrics, it is usually referred to as “polyester”; when used in container and packaging applications, it is commonly termed “PET” or “PET resin”.
PET is the most significant type among thermoplastic polyesters, with a repeating unit having a molar mass of 192g/mol. It is a condensation product of terephthalic acid and ethylene glycol. Together with PBT, they are collectively known as thermoplastic polyesters or saturated polyesters.
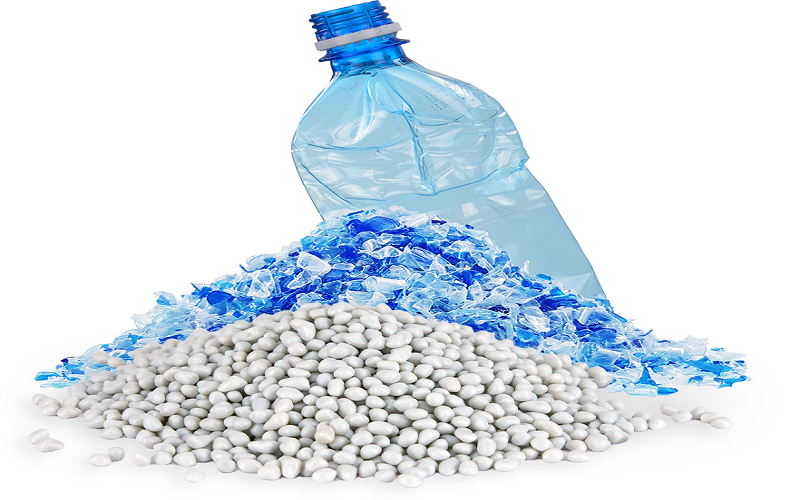
Properties Of The Plastic PET
PET polymer is a milky white translucent or colorless transparent body.
The relative density is 1.38, and the light transmittance is 90%.
PET belongs to medium barrier materials, the transmission coefficient of O2 is 50~90cm3-mm/(m2-d-MPa), and the transmission coefficient of CO2 is 180cm3-mm/(m2-d-MPa).
The water absorption rate of PET is 0.6%, and the water absorption is large
It has excellent physical and mechanical properties in a wide range of temperatures, and its long-term use temperature can reach 120℃.
Excellent electrical insulation, even at high temperatures and high frequencies, its electrical properties are still good, but poor corona resistance, creep resistance, fatigue resistance, friction resistance, dimensional stability are very good.
PET has ester bond, decomposition occurs under the action of strong acid, strong alkali and water vapor, resistance to organic solvents, good weather resistance.
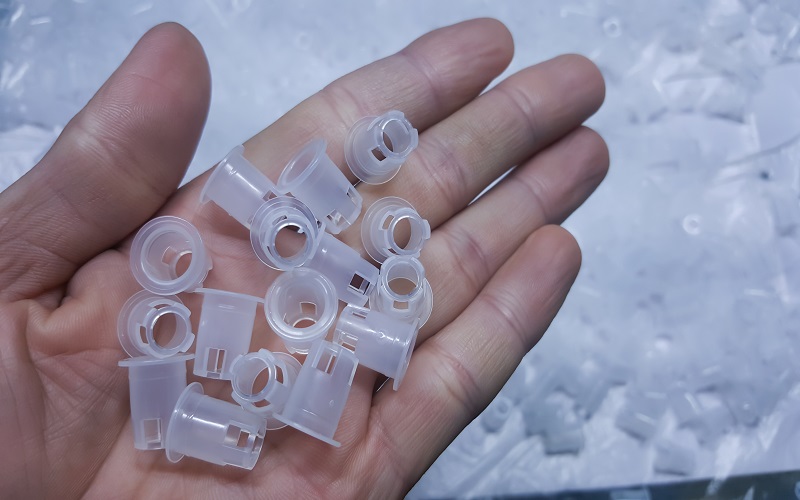
How To Design a PET Mold ?
In order to obtain high quality PET products, PET injection molds play a key role. The design of PET mould determines the final shape, size and weight of the plastic product.
PET Mold preforms are generally molded with hot runner molds, molds and injection molding machine templates are installed between the heat insulation plate, the thickness of the heat insulation plate 12mm is appropriate, while the heat insulation plate must be able to withstand high pressure.
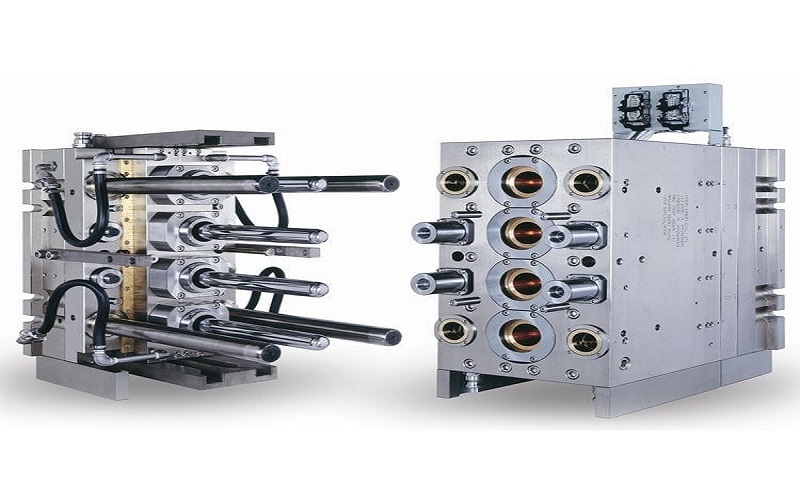
The exhaust must be sufficient to avoid localized overheating or shattering, but the depth of its exhaust port must not be more than 0.03mm, otherwise it is easy to produce flying edge.
In addition, under the premise of avoiding melt injection, the mold gate should be opened at the thick PET parts, which can avoid the shortcomings of high flow resistance and fast cooling, and ensure that it fills the mold cavity.
At the same time, the opening orientation of the mold gate can be directly opposite to the cavity wall or thick core, which can change the flow direction, reduce the flow rate, so that the melt can fill the cavity uniformly and avoid surface defects.
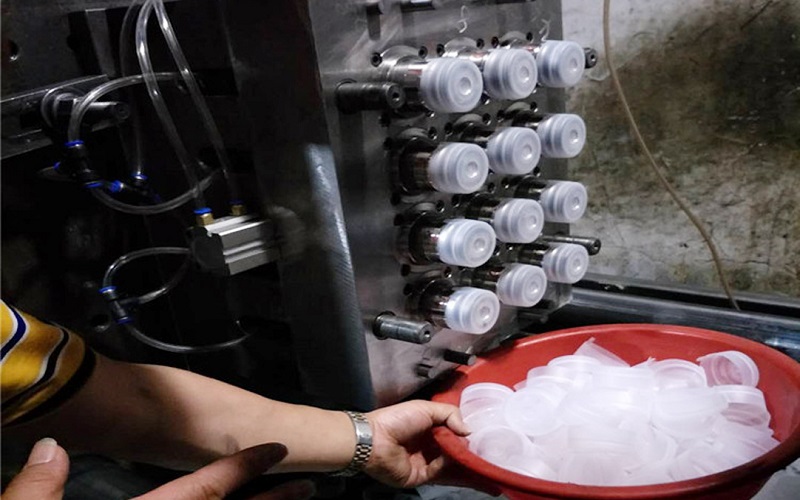
Conditions for PET Injection Molding Process
As a common technology in plastics manufacturing, optimal results in PET injection molding depend on adherence to specific process conditions.
Drying treatment
As PET macromolecule contains lipid group, it has certain hydrophilicity, the pellet is sensitive to water at high temperature, when the moisture content exceeds the limit, the molecular weight decreases in the injection molding process, and the injection molded products will be discolored or become brittle.
Therefore, before PET plastic injection molding, the pellets must be dried, its drying temperature is 100-120 ° C, drying time 3-4 hours. Note that PET recycled material must not exceed 25%.
Injection Molding machine
PET due to the melting point after the stability of a short period of time, and melt higher, so the choice of temperature-controlled segments more, less self-friction heat generation during plasticization of the injection system.
And the actual weight of the injection molded PET product + spouting material can not be less than the machine injection volume of 2 / 3.
Cylinder temperature
PET molding temperature range is narrow, the temperature will directly affect the performance of the product.
Cylinder temperature control at 240 ~ 280 ℃, glass fiber reinforced PET cylinder temperature of 250 ~ 290 ℃, shall not exceed 300 ℃, the nozzle temperature is generally lower than the cylinder temperature 10 ~ 20 ℃.
Mold temperature
Mold temperature directly affects the cooling rate of the melt and crystallinity, crystallinity is different, the performance of pet plastic parts is different. Usually, the mold temperature control in 100 ~ 140 ℃, when molding thin-walled plastic parts, can take a small value; molding thick-walled plastic parts, can take a large value.
Injection pressure
PET melt fluidity is good, easy to mold, usually using medium pressure, pressure of 80 ~ 140MPa, glass fiber reinforced PET injection pressure of 90 ~ 150MPa.
PET Injection Molding Parameters | |||
Drying Temperature(℃) | 100~120 | Drying Time(hr) | 3~4 |
Mold Temperature(℃) | 100~140 | Residual Material Amount (mm) | 3~8 |
Melt Temperature (℃) | 260~295 | Back Pressure (MPa) | 5~10 |
Injection Pressure(MPa) | 80~140 | Locking Force (ton/in2) | 3~4 |
Injection Speed | High Speed | Screw Rotation Speed (rpm) | 60~90 |
Screw Type | Standard Screw (Direct-feed nozzle) | ||
Shutdown Treatment | The barrel needs to be cleaned with PE or PP material | Reuse of Scrap Material (%) | 10~20 |
What Is The PET Plastic For Injection Molding?
The PET injection molding process is widely used in a variety of fields, including beverage containers, electronic appliances, and automotive parts. Since PET plastic has good transparency, heat resistance and impact resistance, it is widely used to manufacture a variety of products that require these characteristics.
Electronic and electrical appliances
PET injection molded parts are characterized by fire and water resistance, corrosion and pressure resistance, etc. They are commonly used to manufacture electrical components such as motor housings, electrical couplings, relays, switches, microwave oven internals, and so on.
Automobile parts
Using PET material good resistance to acids and oils, modified with high strength and high temperature characteristics, in some parts can replace nylon, and in the cost has a great advantage.
Therefore, it is commonly used in the automotive industry to manufacture structural devices such as reflector boxes and electrical components such as headlight reflectors.
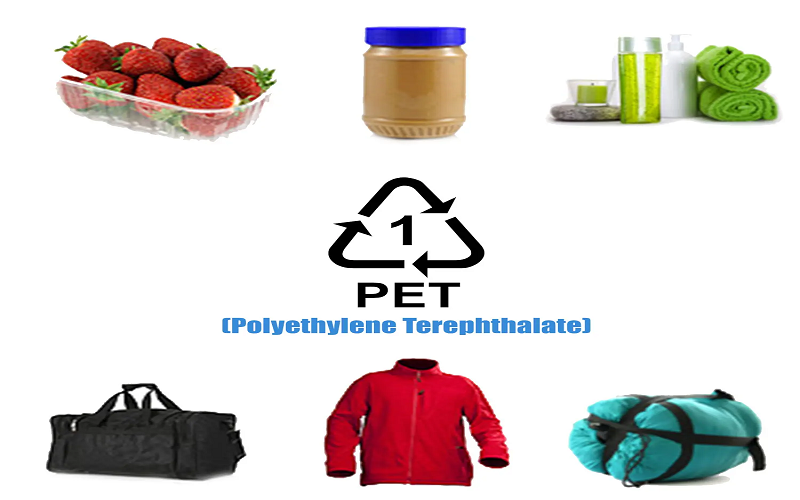
What is the difference between PET and PETG?
PETG sheet is easy to produce products with complex shapes and high tensile ratios. Also, unlike PC sheet and impact-modified acrylic, this sheet does not require pre-drying before thermoforming processing.
Compared with PC sheet or acrylic, the molding cycle is shorter, the temperature is lower, and the yield is higher.
PET plastic molecular structure is highly symmetric, with a certain crystalline orientation ability, so it has a high film-forming and into the nature of the PET plastic has very good optical properties and weather resistance, amorphous PET plastic has good optical transparency.
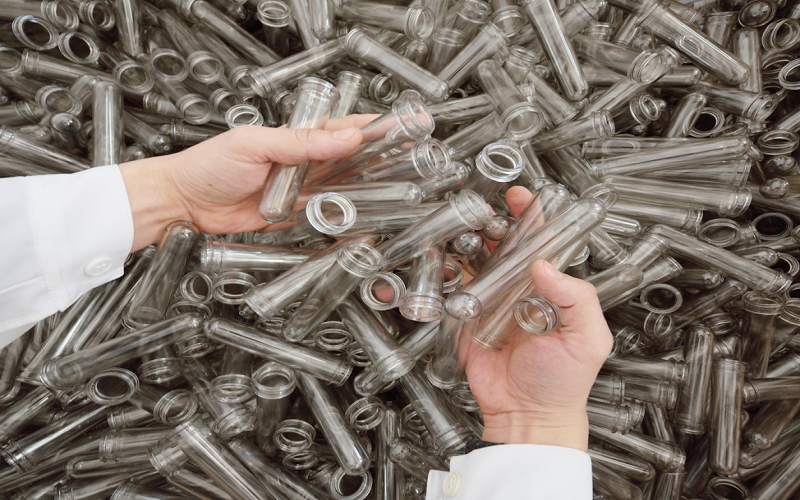
Conclusion
The PET injection molding process is an efficient and flexible plastics processing technology that is used in a wide variety of applications. If you would like to start a new project for PBT injection molding, request a quote from FOWMOULD and we will respond in the shortest possible time.