Material selection plays a dominant role in product performance and efficiency. PA6 and PEEK are two plastics that have attracted a lot of attention in the field of engineering and manufacturing. Their excellent performance in terms of mechanical strength, abrasion resistance, and chemical resistance makes them used in a variety of industrial applications. But how do you choose the material that is more suitable for your product? This article makes your choice easier with a detailed comparison!
Introduction to PA6
PA6 is a synthetic polymer made from caprolactam monomers.
In the natural state presents milky white or translucent color, smooth surface, colorless and odorless, usually supplied in the form of granules and powder.
It has good moisture absorption, abrasion resistance and processing performance.
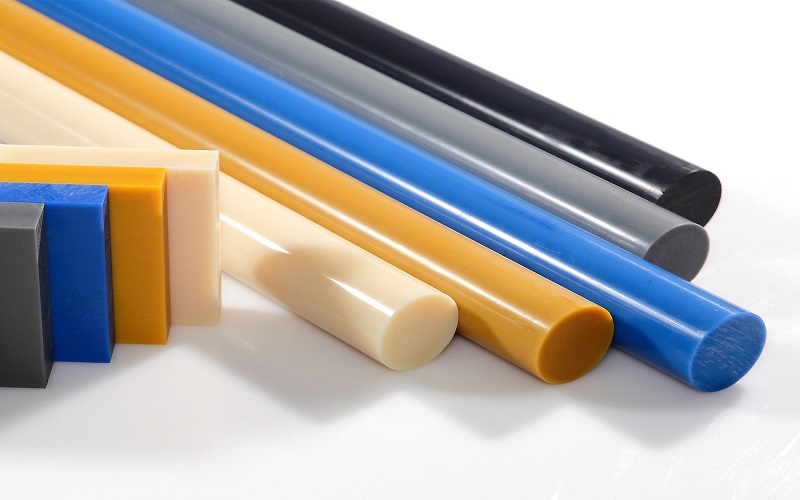
What is PEEK?
Peek is a semi-crystalline thermoplastic polymer composed of aromatic and ketone groups, generally light brown or beige in color.Its special atomic structure provides the basis for the magical effects it produces.
The aromatic ring (C6H4) gives it more rigidity and strength.
The ether bond (-O-) ensures flexibility and better chemical resistance.
The ketone group (-CO-), on the other hand, excels in strength and heat resistance.
PEEK because of its special chemical structure, heat-resistant temperature can reach 250℃, so its stability is good at high temperatures, often used in aerospace, medical equipment for the temperature requirements of the strict field.
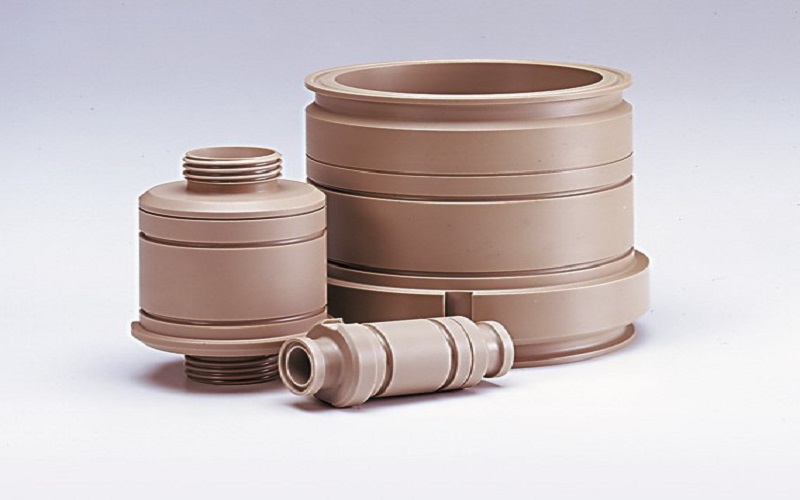
PA6 vs PEEK:Properties
PA6 and PEEK are both polyamide (nylon) materials, but they also have many differences. Here are some of the characteristics of PA6 and PEEK:
Property | PA6 | PEEK |
Tensile Strength | 70-90 MPa | 90-100 MPa |
Elongation at Break | 20-30% | 20-40% |
Elastic Modulus | 2.8 GPa | 3.6 GPa |
Heat Deflection Temperature | 180°C | 250°C |
Water Absorption | 1.3-1.9% | < 0.5% |
Coefficient of Friction | 0.3 | 0.2 |
Density | 1.14 g/cm³ | 1.30 g/cm³ |
Chemical Resistance | Good | Excellent |
Thermal Conductivity | 0.25 W/(m·K) | 0.25 W/(m·K) |
Cost | Lower | Higher |
PA6 and PEEK Injection Molding Conditions:
Due to the different characteristics of the two materials, different temperatures are required during processing to ensure the quality and performance of the final product.PA6 usually suitable processing temperature between 230°C to 280°C, mold temperature needs to be maintained at 80-100°C.Injection pressure is 70-120 MPa,holding pressure is 50-80 MPa.It needs to dry for 4-6 hours.
PEEK, on the other hand, has a significantly higher processing temperature than PA6 and needs to reach 350-400°C, with the mold temperature within 160-200°C.The injection pressure should be set in the range of 100-160 MPa, and the pressure holding pressure should be 70-100 MPa. In addition, it needs to be dried in an environment with a drying temperature of 150°C for 3-4 hours.
What Can PA6 and PEEK Materials be Used For?
When it comes to applications, PA6 and PEEK have a lot in common, but their specific uses differ.
PA6 is relatively inexpensive and economical to produce and is widely used in automotive, electrical and electronic, consumer, textile and industrial components.
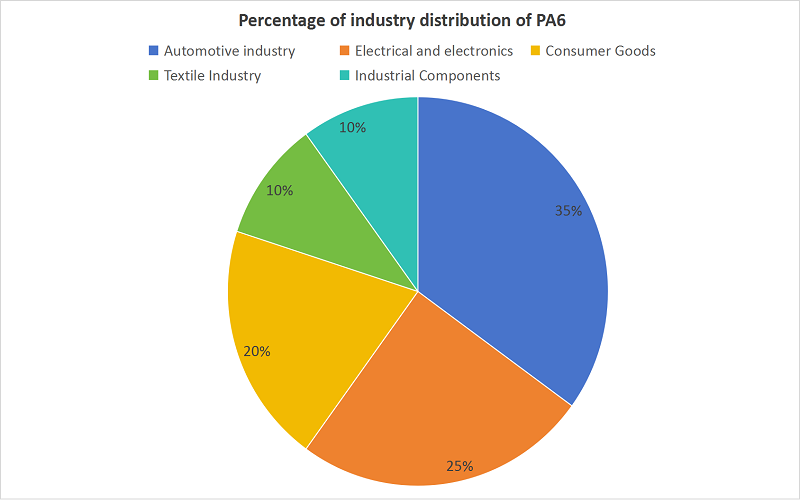
PEEK, on the other hand, With a heat distortion temperature of 250°C, it has excellent high-temperature performance and is generally used in highly demanding products.
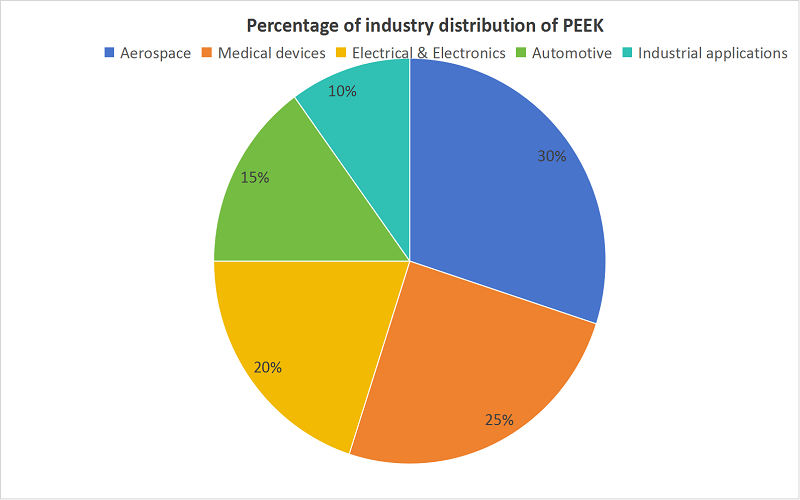
Which is Safer, PA6 Or PEEK?
This depends on their chemical properties, such as thermal stability, chemical resistance, toxicity and flammability, as well as how they are used in different application scenarios.
PA6 is safe for general everyday use, such as food contact applications. However, it can produce harmful substances at high temperatures. Thermal degradation releases harmful gases such as ammonia and caprolactam. Proper ventilation is required during processing to avoid inhalation of fumes.
PEEK has a very high melting point and is highly resistant to high temperatures. In addition, PEEK is safe for humans as it has good biocompatibility and does not cause adverse reactions in the body.
Overall, PEEK is more stable and safer. Specific applications and environments should always be considered when evaluating material safety.
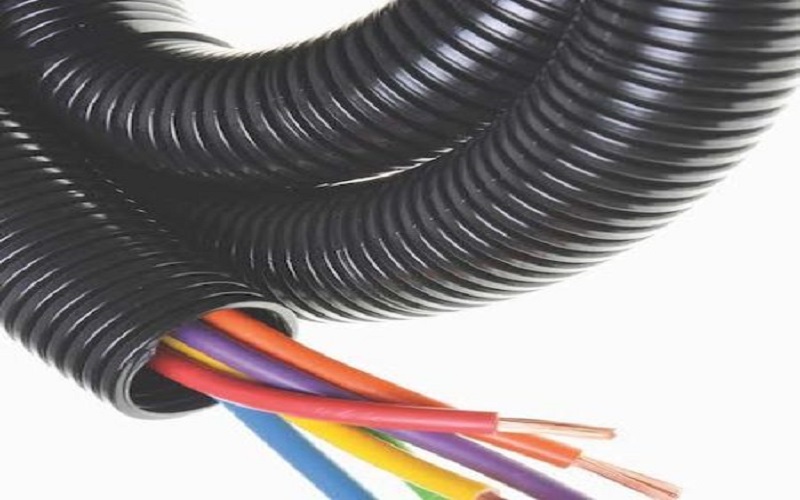
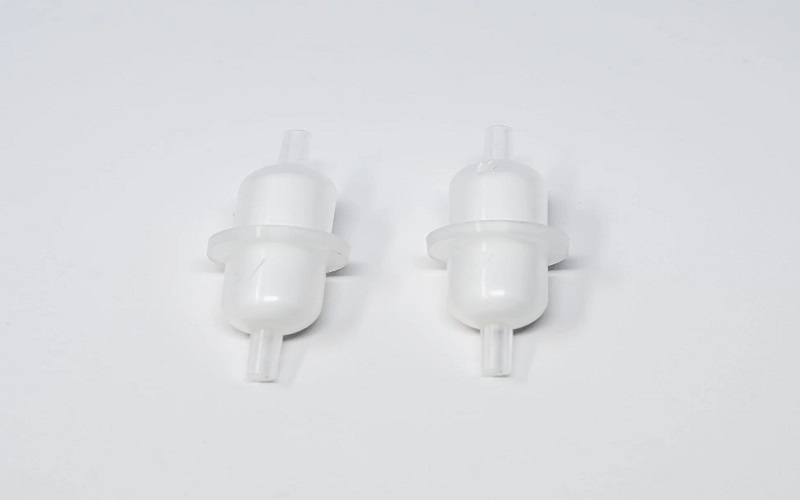
PA6 vs PEEK:Processing Type
PA6 and PEEK differ greatly in their processing methods due to their different properties.
PA6 is known for its high tensile strength and abrasion resistance, and is well suited for injection molding, extrusion molding, and blow molding.
PA6 injection molding is used for automotive parts such as gears, bearings, instrument panels, and door handles.
PA6 extrusion molding is used for conveyor belts in industrial applications.
In addition, PA6 has blown film, thermoforming, rotomolding and other processing methods.
The main processing methods for PEEK include injection molding, extrusion molding, compression molding and thermoforming. These methods take advantage of the high temperature stability of PEEK. Injection molding can produce parts with complex shapes and high precision, and is suitable for mass production. Compression molding is generally used in the aerospace and medical fields.
PA6 vs PEEK:Which is More Cost-Effective
Factors such as material cost, performance, application scenarios, service life and maintenance costs need to be considered.
In terms of cost, PA6 is mainly extracted from petroleum derivatives, with a mature production process and relatively low material costs.
However, the production process of PEEK is complex and requires a special high temperature and high pressure process, so the cost is generally higher.
In terms of service life, PA6 has a long service life, but may need to be replaced frequently in harsh environments, while PEEK has a very long service life and low maintenance costs.
If the project budget is limited and the application environment is common, PA6 is the more economical choice; if the project requires high performance and long life, PEEK is more advantageous in terms of long-term economic benefits.
Conclusion
If you still don’t know which one is more suitable for your product, PA6 or PEEK, welcome to consult FOWMOULD, we will give you a more detailed introduction. Feel free to click on the links below for more information on the subject!