Polyethylene (PE), as a widely used thermoplastic polymer, occupies an important position in the field of injection molding due to its excellent physical properties, chemical stability, and processing adaptability.
PE injection molding technology involves injecting molten PE material into molds, rapidly cooling and forming diverse products ranging from everyday consumer goods to industrial components.
Its features include high production efficiency, good dimensional stability, and relatively low processing costs.
This article will delve into the technical characteristics of PE injection molding, the processing properties of different types of PE materials, and their wide applications in packaging, medical, automotive, and other fields, providing readers with comprehensive technical reference.
Properties Of Polyethylene Material
Polyethylene exhibits a variety of physical and chemical properties that make it exceptionally well-suited for injection molding applications. Its molecular structure, composed of long chains of ethylene monomers, imparts versatility and robust performance.
Physical Properties
Polyethylene resin is a non-toxic, odorless white powder or granule, appearing milky white with a waxy feel, and has a low water absorption rate of less than 0.01%. Its product surfaces are non-polar, making them difficult to bond and print on, though surface treatment can improve these properties.
Polyethylene has a melting point of 100 to 130°C and exhibits excellent low-temperature resistance, maintaining good mechanical properties even at -60°C. Its service temperature ranges from 80 to 110°C.
Mechanical Properties
Polyethylene generally has moderate mechanical properties, with relatively low tensile strength and poor creep resistance, but good impact resistance. These properties are mainly influenced by density, crystallinity, and molecular weight; as these factors increase, the mechanical properties improve.
Chemical Resistance
Polyethylene has good chemical resistance and can resist solutions such as dilute nitric acid, dilute sulfuric acid, hydrochloric acid of various concentrations at room temperature, but it is not resistant to corrosion by strong oxidizing acids and will be slowly eroded at room temperature.
It is susceptible to ultraviolet degradation and has poor resistance to chlorinated solvents, is difficult to paint due to poor bonding capabilities, is highly flammable, and is susceptible to oxidation.
This plastic injection molding material possesses outstanding chemical resistance to alkalis and organic solvents but is attacked by oxidation when exposed to strong acids.
Thermal Properties
Polyethylene has low heat resistance but excellent low-temperature performance, with a brittleness temperature generally below -50°C; with increasing relative molecular weight, it can reach as low as -140°C.
Polyethylene has a large linear expansion coefficient, reaching up to (20–24)×10⁻⁵/K. It also has relatively high thermal conductivity.
Electrical Properties
Because polyethylene has no polarity, it has excellent electrical properties of low dielectric loss and high dielectric strength, i.e. it can be used as FM insulating material, corona-resistant plastic, and high-voltage insulating material.
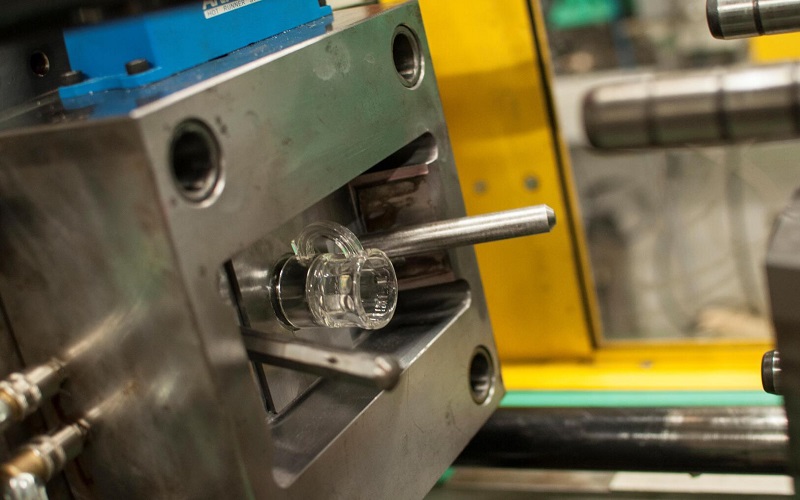
Types Of PE Materials
Polyethylene can be categorized into high density polyethylene (HDPE), low density polyethylene (LDPE), linear low density polyethylene (LLDPE), and ultra high molecular weight polyethylene (UHMWPE) based on polymerization method, molecular weight, and chain structure.
Each type of polyethylene material exhibits unique characteristics during the injection molding process, directly influencing the selection of molding process parameters and the performance of the final product.
Low Density Polyethylene (LDPE)
LDPE (also known as high pressure polyethylene)has a lower density and higher degree of branching, resulting in lower crystallinity, which gives it excellent flexibility and toughness.
It remains flexible even at low temperatures, and has good strength relative to its density, making LDPE injection molding suitable for thin-walled and complex-shaped products.
Application films LDPE is widely used as packaging material for various food, clothing, medicine, fertilizer, industrial products, and agricultural films.
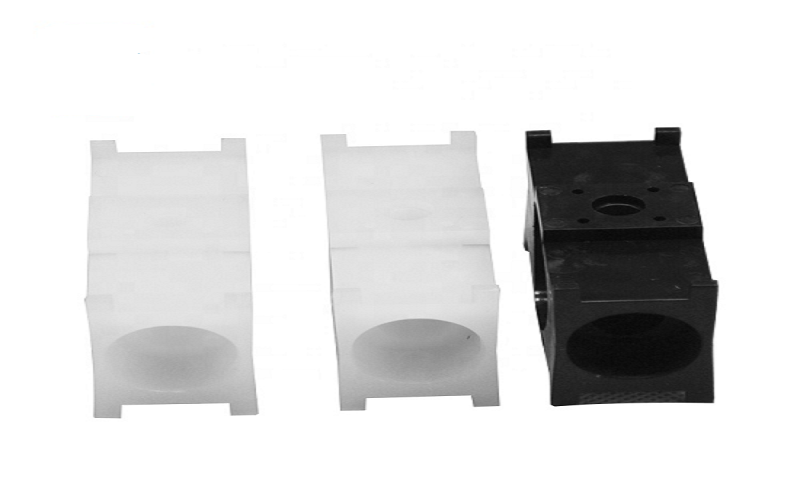
Linear Low Density Polyethylene (LLDPE)
LLDPE combines the flexibility of LDPE with higher mechanical strength, exhibiting good impact resistance and puncture resistance. Its molecular structure is more linear with higher crystallinity, resulting in greater chemical resistance and resistance to environmental stress cracking.
Due to its moderate melt flow, LLDPE injection molding requires control within a narrower temperature range to ensure product quality. It is commonly used for durable products such as packaging caps and industrial components.
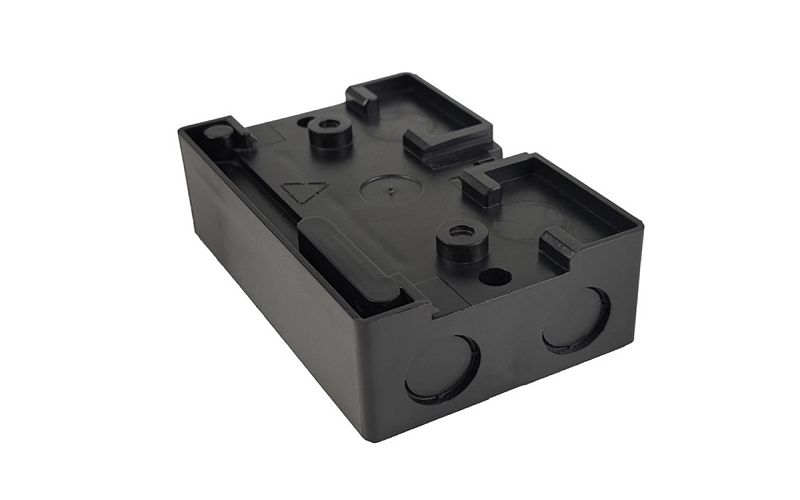
High Density Polyethylene (HDPE)
HDPE has higher density and crystallinity, offering excellent rigidity and strength while maintaining some toughness.
It has higher melt viscosity, requiring higher injection pressure and elevated mold temperature during HDPE molding to ensure the molten plastic fully fills the mold cavity and avoids defects.
HDPE possesses good chemical stability and excellent electrical insulating properties, making it suitable for manufacturing automotive parts, industrial containers, and food packaging with high performance requirements.
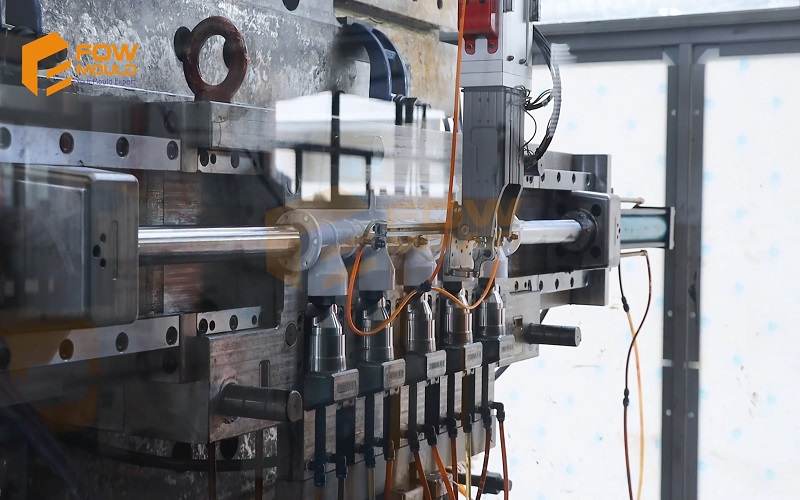
Ultra High Molecular Weight Polyethylene (UHMWPE)
UHMWPE has an extremely high molecular weight, endowing it with outstanding mechanical properties such as exceptional abrasion resistance and wear resistance.
Its melt flow is very poor, making it difficult to process with conventional injection molding techniques; specialized injection molding machines and process parameters are required.
UHMWPE injection molding is widely applied in high-performance fields such as medical implants, bulletproof materials, and wear-resistant parts. Precise control of temperature and injection pressure is critical during processing to prevent material degradation and ensure the mechanical performance of the product.
In summary, different types of PE materials have varying requirements for injection pressure, mold temperature, melt flow, and cooling time during the injection molding process.
Proper material selection and adjustment of these parameters, combined with the physical and chemical properties of the materials, can effectively improve the quality of injection molded products and improve production efficiency.
Considerations For PE Injection Molding Process
When performing PE injection molding, several key factors must be taken into account to optimize product quality and production efficiency.
Material Selection:Different types of polyethylene—such as low density polyethylene (LDPE), linear low density polyethylene (LLDPE), medium density polyethylene (MDPE), high density polyethylene (HDPE), and ultra high molecular weight polyethylene (UHMWPE)—each have unique characteristics affecting their injection molding behavior.
Selecting the appropriate PE material depends on the desired mechanical properties, chemical resistance, and application requirements.
Melt Temperature and Barrel Temperature: The melting point of PE varies by type but generally ranges between 100°C and 130°C. Proper control of the barrel temperature is essential to ensure the polymer melt flows smoothly without degradation. Typically, barrel temperatures are set slightly above the melting point to provide a uniform melt flow.
Injection Speed and Injection Pressure: Achieving optimal injection speed and pressure is critical to filling the mold cavity completely and avoiding defects. PE materials with higher density and crystallinity, such as HDPE, often require higher injection pressure and faster injection speeds to compensate for their higher melt viscosity.
Mold Temperature and Cooling: The mold temperature influences the crystallinity and mechanical properties of the final product. Higher mold temperatures can improve surface finish and reduce internal stresses but may increase cycle times. Efficient cooling systems are necessary to maintain dimensional stability and reduce warpage.
Shrinkage and Dimensional Stability: PE materials tend to have relatively high shrinkage rates, which vary depending on the type and processing conditions. Mold design must account for this shrinkage to ensure dimensional accuracy of the injection molded parts.
Processing Environment: Since PE melts are prone to oxidation, it is important to minimize exposure to oxygen during processing to prevent discoloration and degradation. Additionally, controlling moisture content is essential, although PE generally has low moisture absorption and does not require extensive drying.
Additives and Fillers: Incorporating additives can enhance properties such as UV resistance, flame retardancy, and impact strength. However, additives may affect melt flow rate and viscosity, necessitating adjustments in processing parameters.
By carefully managing these factors, injection molders can produce high-quality PE plastic parts with excellent mechanical properties, chemical resistance, and surface finish, suitable for a broad range of industrial and consumer applications.
Applications of Injection Molded PE Plastic Parts
Polyethylene is a thermoplastic polymer with a variable crystalline structure and a broad range of applications depending on the particular type.
Automotive Industry
The impact of PE injection molding in the automotive sector is profound. This manufacturing process is instrumental in producing a wide range of automotive components for the interior and exterior of vehicles.
From dashboard panels and door trims to intricate grilles and bumpers, PE injection molding ensures the creation of durable and visually appealing parts.
The ability to mold intricate designs with precision makes it an indispensable choice for automakers looking to elevate the aesthetics and performance of their vehicles.
Consumеr Elеctronics
PE injеction molding takеs cеntеr stagе for crеating еssеntial componеnts in consumеr еlеctronics. Thе prеcision and cost-еffеctivеnеss of this procеss makе it an idеal choicе for manufacturing casings, connеctors, and various othеr componеnts usеd in еlеctronic dеvicеs.
Whеthеr it’s a smartphonе’s slееk casing or a computеr connеctor’s intricatе dеsign, PE injеction molding dеlivеrs еxcеptional rеsults, mееting thе stringеnt dеmands of thе еlеctronics industry.
Packaging Applications
From еvеryday еssеntials likе food containеrs and bеvеragе cups to spеcializеd packaging for sеnsitivе products, PE injеction molding еnsurеs that thе packaging is functional and visually appеaling.
In such applications, it gives good flexibility and tensile strength required for manipulation. LDPE and HDPE are FDA approved as packaging for many food products.
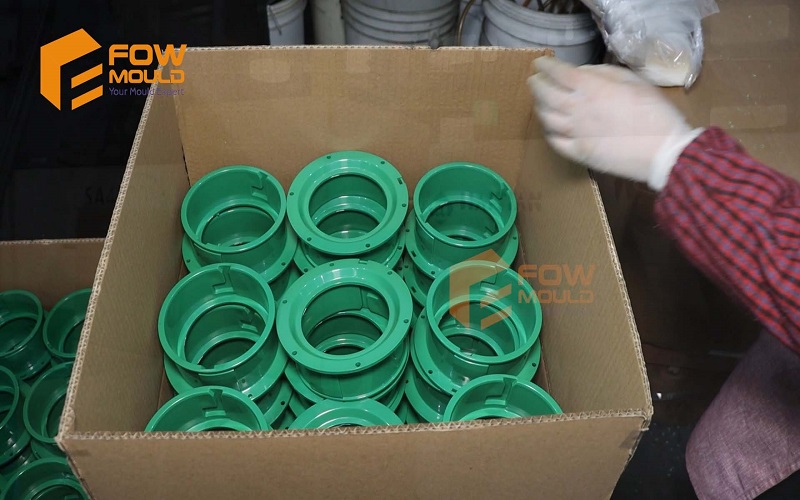
Advantages And Disadvantages Of PE Injection Molding
Polyethylene (PE) injection molding is widely used in plastic product manufacturing due to its numerous advantages:
Wide Temperature Range Tolerance: PE materials perform well under diverse environmental conditions with excellent thermal stability, maintaining properties during processing and use.
Good Chemical Resistance: Suitable for harsh chemical environments, resisting corrosion.
Low Water Absorption and Excellent Electrical Insulation: Ideal for electrical and electronic components.
High Production Efficiency and Low Cost: Cost-effective processing, suitable for large-scale production.
Diverse Applications: Low-density polyethylene (LDPE) is used for shopping bags, packaging films, and flexible containers due to its flexibility and toughness; high-density polyethylene (HDPE) is preferred for automotive parts, snap fits, and durable industrial products due to its strength and rigidity.
However, PE injection molding has drawbacks:
High Shrinkage Rate: Variable crystalline structure leads to high shrinkage during cooling, requiring precise mold design for dimensional stability.
Low Melting Point and Heat Resistance: Unsuitable for high-temperature applications.
Poor Surface Adhesion: Non-polar surface complicates painting or bonding, requiring surface treatment.
Processing Challenges: Ultra-high molecular weight polyethylene (UHMWPE) has poor melt flow due to high molecular weight, necessitating specialized equipment and strict control of injection parameters to avoid defects.
By optimizing mold design and processing parameters, PE injection molding can achieve efficient, high-quality production across various applications.
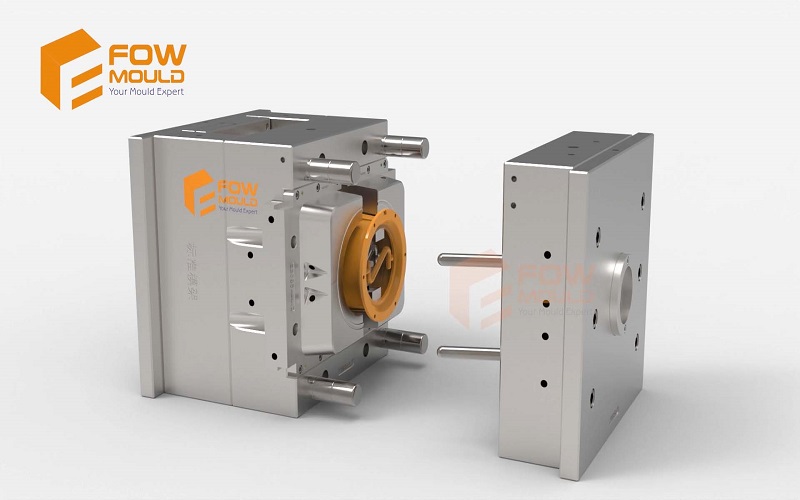
Conclusion
Polyethylene (PE) injection molding technology, with its high efficiency, cost-effectiveness, and excellent material properties, demonstrates broad application prospects in packaging, medical, automotive, and industrial sectors.
Its strong chemical stability, low water absorption, and electrical insulation make it ideal for diverse product manufacturing, while different PE types (e.g., LDPE, HDPE, and LLDPE) offer flexibility for specific applications.
Despite challenges such as high shrinkage rates, limited heat resistance, and poor surface adhesion, optimizing mold design and processing parameters can significantly enhance product quality and production efficiency.
For manufacturers looking to start a new PE injection molding project, FOWMOULD offers professional solutions and technical support. Contact FOWMOULD for customized services.