PBT (polybutylene terephthalate), as a high performance engineering plastic, holds a significant position in modern industry due to its excellent mechanical properties, heat resistance, and chemical resistance.
Since its introduction, PBT has gradually become an indispensable material in fields such as electronic components, automotive parts, and mechanical equipment, thanks to its excellent machining characteristics and wide-ranging applications.
With advancements in technology and the growing demand for enhanced material performance, the research and application of PBT plastic continue to expand, providing robust support for the design and production of high-precision, durable plastic parts.
This article will explore the properties, processing methods, and application areas of PBT plastic, aiming to offer readers a comprehensive and in-depth understanding.
What is Polybutylene Terephthalate (PBT)?
Polybutylene terephthalate (commonly abbreviated as PBT) is a synthetic, semi crystalline thermoplastic with similar properties and composition to polyethylene terephthalate ,belongs to the polyester family of thermoplastics.It was first synthesized by German scientist P. Schlack in 1942.
This material is formed by a process called polycondensation, which uses terephthalic acid. It can also be formed using dimethyl terephthalate and 1,4-butanediol.
The chemical formula of PBT is (C12H12O4)n, with a relative molecular weight ranging from 30,000 to 40,000. It appears milky white or pale yellow with a glossy surface and has a density of 1.31 to 1.55 g/cm³.
Its highly crystalline structure results in excellent dimensional stability and low creep. PBT also exhibits good resistance to chemicals, oils, and solvents, making it suitable for various applications.
It is widely used in various industries such as electrical and electronic components, automotive components, mechanical equipment, and optical cable and fiber optic coatings.
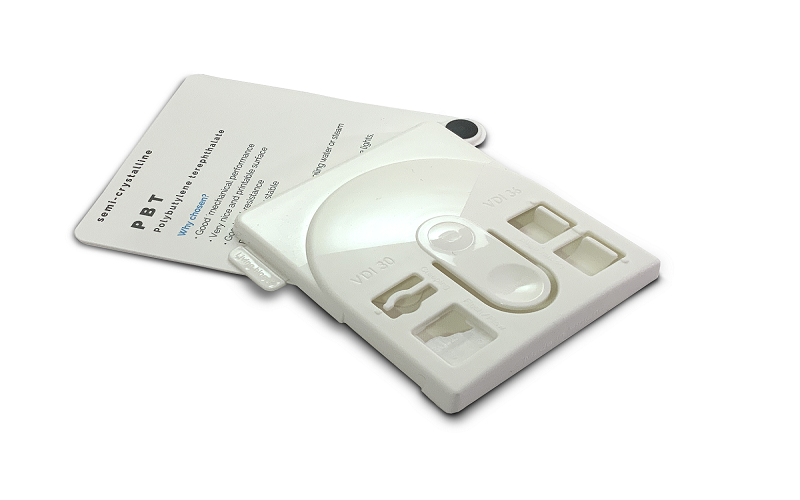
PBT Material Properties
PBT polymer offer high strength, dimensional stability, and excellent properties —including strong chemical resistance, desirable electrical properties, and high suitability for molding and other industrial processes.
Below is a detailed introduction to the properties of PBT:
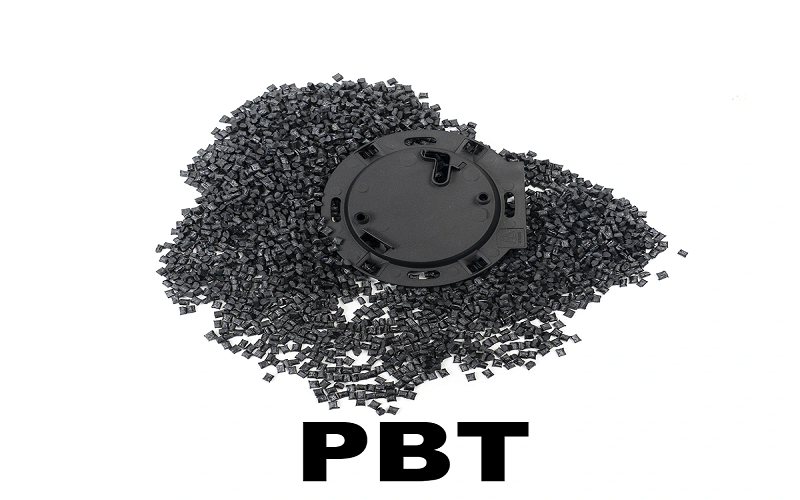
Physical Properties
PBT appears milky white or pale yellow with a high gloss surface and a density ranging from 1.31 to 1.55 g/cm³, depending on the formulation and additives.
It has a high crystallinity (typically 30-40%), which provides the material with good dimensional stability and low moisture absorption (water absorption rate is only about 0.08-0.2%).
Additionally, it has a low molding shrinkage rate (about 1.5-2.0%), resulting in high precision of the processed products.
Mechanical Properties
PBT has slightly lower strength and rigidity, slightly better impact resistance, and a slightly lower glass transition temperature.. It provides good creep resistance over steady and elevated temperatures.
Moreover, PBT’s wear properties and fatigue resistance are also prominent, making it suitable for components that need to withstand repeated mechanical stress, such as gears and connectors.
When reinforced with materials like glass fibers, its mechanical strength and rigidity can be further significantly enhanced.
Electrical Properties
PBT exhibits outstanding electrical insulation properties, with high dielectric strength (approximately 20-30 kV/mm), and high volume and surface resistivity (>10^15 Ω·cm), maintaining stable insulation even in humid environments.
This makes it an ideal material for manufacturing insulating components, sockets, and connectors in the electronics and electrical fields. Additionally, PBT has low dielectric loss, making it suitable for high-frequency applications.
Thermal Properties
PBT has excellent heat resistance, with a melting point usually between 225-235°C, and a heat deflection temperature (HDT) of about 60-70°C when not reinforced, which can be increased to over 200°C with glass fiber reinforcement.
The long-term usage temperature range of PBT is 120-140°C, allowing it to operate in high-temperature environments without significant loss of performance.
Meanwhile, it has good thermal stability, is not easily decomposed during processing, and is suitable for high-temperature molding processes such as injection molding applications.
Chemical Properties
PBT has excellent chemical resistance to a wide range of various chemicals. These include diluted acids, alcohols, aromatic hydrocarbons, ketones, solvents, oils, and greases. Suitable to produce plastic parts exposed to organic solvents, gasoline, and oils.
PBT Properties | |
Property | Value |
Density(g/cm³) | 1.31 – 1.55 |
Melting Point(°C) | 233 |
Tensile Strength(MPa) | 50 – 60 |
Elongation at Break(%) | 50 – 300 |
Glass Transition Temperature(°C) | 60 – 70 |
Water Absorption(%) | 0.2–0.5 |
Mold Shrinkage(%) | 1.5 – 2.0 |
Why Use PBT For Injection Molding?
Owing to its exceptional resistance, PBT is widely favored in injection molding, establishing itself as a standout among high performance material.
Firstly, PBT exhibits excellent machining characteristics. As a crystalline polymer with a distinct melting point range, PBT can achieve a crystallinity of up to 40%. Its high crystallinity and rapid crystallization rate allow it to solidify quickly during injection molding, significantly shortening processing cycles and enhancing production efficiency.
During the PBT injection molding process , the viscosity of its melt is less sensitive to temperature changes than to shear stress, making injection pressure a critical factor in controlling melt flowability.
Additionally, PBT demonstrates good fluidity in its molten state, with a viscosity lower than that of nylon, making it suitable for filling complex molds, though it is prone to “flash” phenomena.
The molded products exhibit anisotropy due to their crystalline nature and are susceptible to hydrolytic degradation under high-temperature, high-humidity conditions.
To optimize molding quality, the mold temperature is typically controlled between 60-100°C to ensure uniform crystallization and minimize deformation.
Prior to processing, PBT raw material must be thoroughly dried to reduce its moisture content below 0.02%. This step is essential to prevent molecular chain scission and performance degradation caused by moisture during processing, thereby ensuring the reliability and stability of the final products.
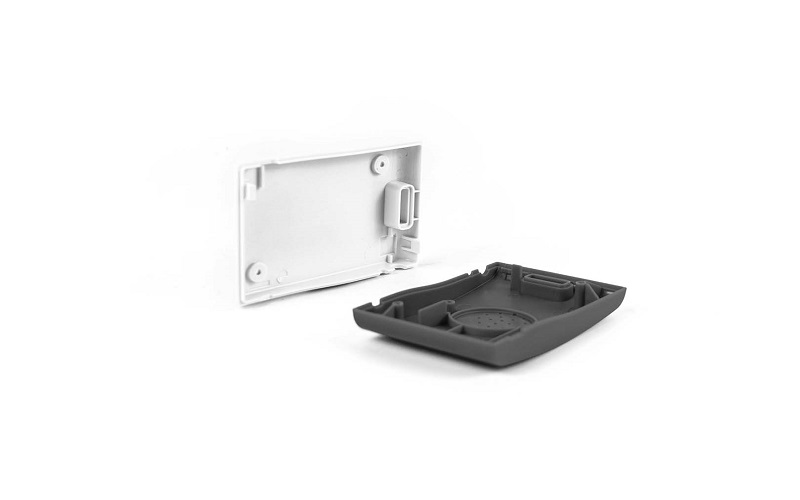
Advantages Of PBT Plastic
Superior Mechanical Properties: PBT materials offer high strength and rigidity, with tensile strength typically ranging between 50-60 MPa and flexural strength reaching up to 80-90 MPa, allowing them to withstand significant external forces without noticeable deformation.
Outstanding Electrical Insulation:PBT is highly valued for its electrical properties, offering a dielectric strength of 20-30 kV/mm and a volume resistivity exceeding 10^15 Ω·cm. These characteristics, along with low dielectric loss and stable performance in humid conditions, make it an excellent insulator for electrical and electronic applications.
Chemical and Environmental Resistance:PBT exhibits robust resistance to a wide range of chemicals, including oils, greases, solvents, and weak acids, enhancing its suitability for harsh industrial environments. Its low moisture absorption (0.08-0.2%) minimizes the risk of swelling or degradation in humid conditions, a critical advantage over materials like nylon. This stability ensures that PBT components maintain their performance and appearance over time, even when exposed to challenging surroundings.
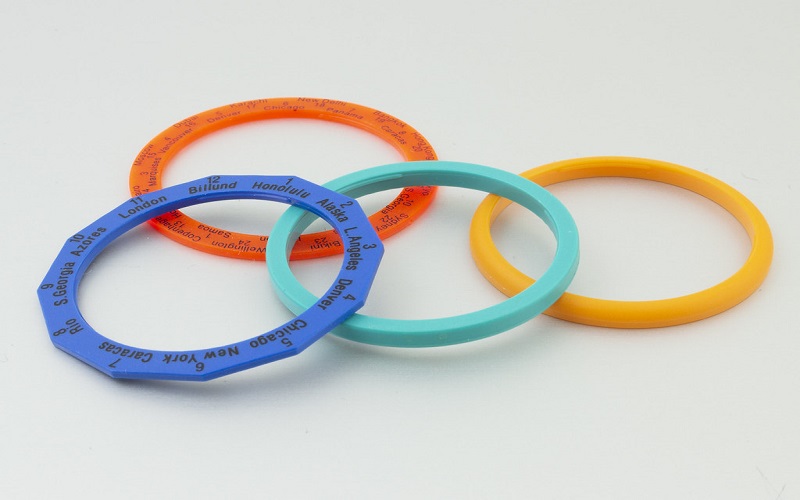
Disadvantages Of PBT Plastic
Limited Impact Resistance:Despite its good mechanical strength, unreinforced PBT has relatively modest impact resistance, with notched Izod impact strength typically ranging from 3-6 kJ/m². This makes it prone to cracking or breaking under sudden, high-impact loads, especially at lower temperatures where it can become brittle. While reinforcement with glass fibers improved performance
, it often further reduces toughness, limiting PBT’s use in applications requiring high impact durability, such as heavy-duty protective casings.
Susceptibility to Hydrolysis:PBT is sensitive to hydrolytic degradation when exposed to water or high humidity at elevated temperatures. Although its moisture absorption is low (0.08-0.2%), prolonged exposure to hot, wet conditions can cause molecular chain scission, reducing mechanical properties and leading to premature failure. This vulnerability restricts its use in environments with constant moisture exposure, such as underwater components or steam-exposed parts, unless properly stabilized or coated.
Moderate Heat Resistance:While PBT offers good thermal stability with a melting point of 225-235°C, its heat resistance is moderate compared to high-performance plastics like PEEK or PPS. Its heat deflection temperature (HDT) in unreinforced form is only 60-70°C under load (1.8 MPa), which can limit its use in applications requiring sustained performance above 140°C without reinforcement.
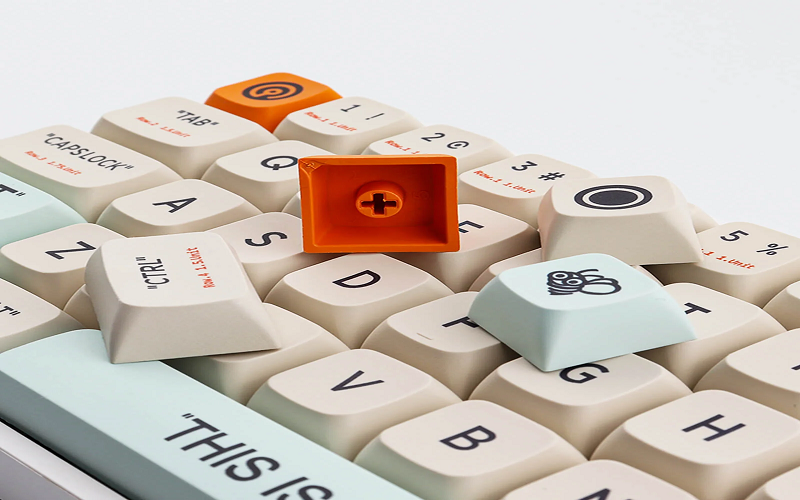
Applications Of Polybutylene Terephthalate
Automotive Industry
In the automotive industry, half of the PBT used is alloyed with PC to form PBT/PC blends, which can be used for car bumpers . Additionally, PBT is utilized in window motor housings, locomotive motor parts, automotive transmission gearboxes, radiator grilles, tailgate outer panels, wheel covers, and door and window components.
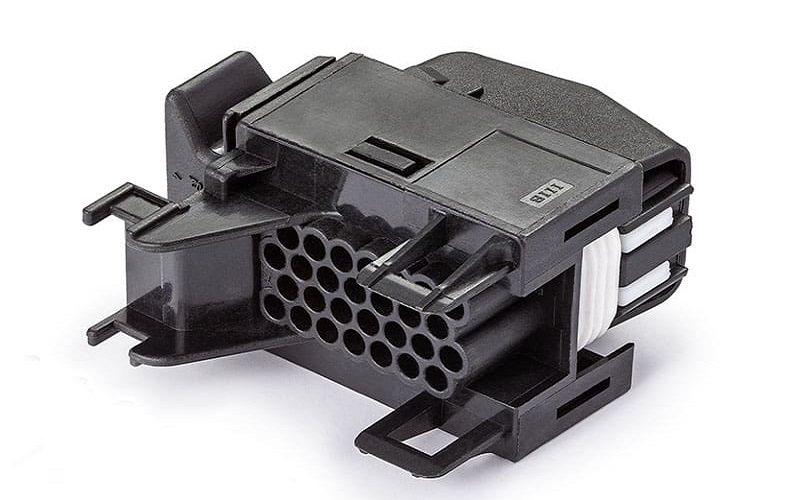
Electronics and Electrical Systems
Thanks to its outstanding electrical insulation properties—featuring a dielectric strength of 20-30 kV/mm and high resistivity (>10^15 Ω·cm)—PBT is a staple in the electronics sector.
It is widely used to produce connectors, sockets, switches, and circuit breaker housings that require reliable insulation and resistance to heat and humidity. Flame-retardant PBT variants meet stringent safety standards, making them ideal for power tool components and appliance wiring systems.
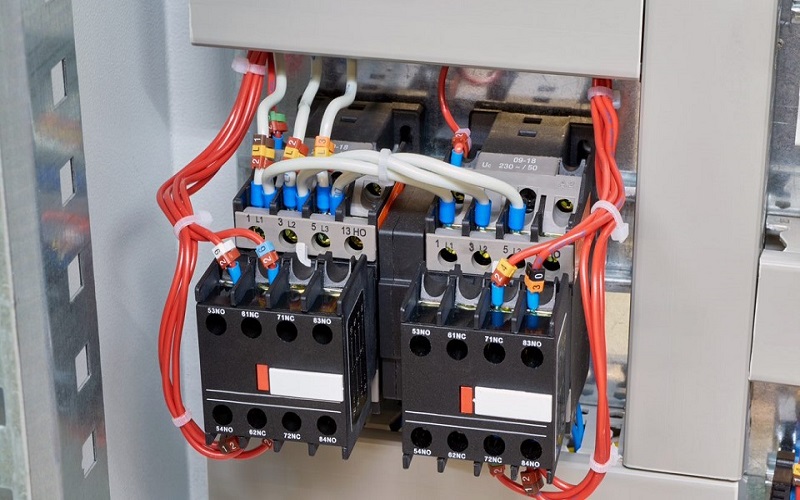
Consumer Goods
This material is heat resistant and tough, makes it a popular choice for consumer products. It is used in power tool housings, kitchen appliance parts (e.g., blender bases), and personal care devices like electric toothbrush handles.
Its low moisture absorption and resistance to wear ensure long-lasting performance, while its glossy surface appeals to design-conscious manufacturers.
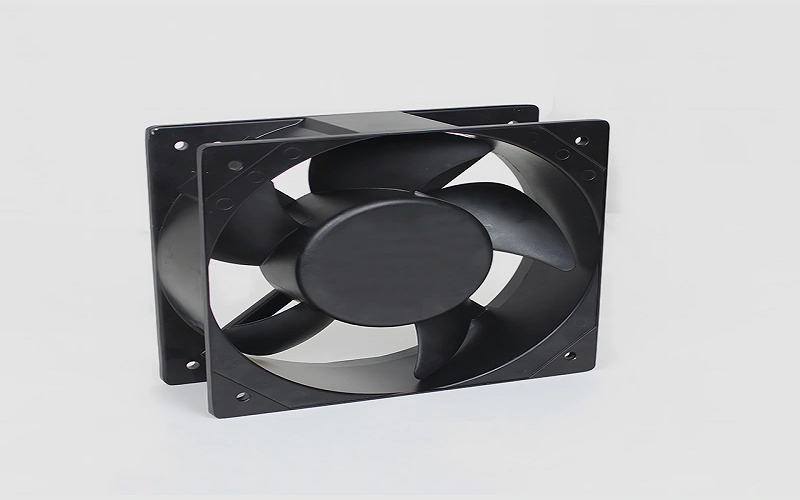
Industrial and Mechanical Components
In industrial settings, PBT serves in applications requiring mechanical reliability and precision. Its fast crystallization and low shrinkage enable the production of high-tolerance parts like gears, bearings, and valve components . PBT’s resistance to fatigue and abrasion supports its use in moving parts, while its chemical stability suits it for machinery exposed to lubricants or solvents.
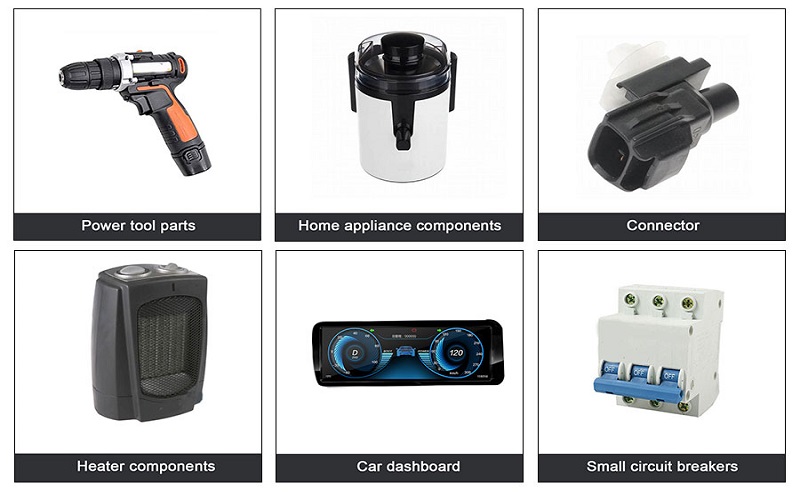
PBT vs Other Materials
Polybutylene terephthalate is a high-performance thermoplastic polyester frequently chosen for demanding applications due to its unique combination of properties.
However, its performance must be evaluated against alternatives like nylon (polyamide), polycarbonate PC, PET, and PEEK to understand its competitive edge and limitations.
PBT vs Nylon (Polyamide)
Both PBT and nylon two materials excel in applications requiring toughness and flexibility, but they differ significantly. PBT offers good resistance to oils, solvents, and heat (melting point 225-235°C), with lower moisture absorption (0.08-0.2%) compared to nylon (2-8%).
This makes PBT more dimensionally stable in humid environments, ideal for automotive connectors or electrical housings. However, nylon typically surpasses PBT in impact resistance and elasticity, making it better suited for high-wear parts like gears or belts.
PBT fibers, used in textiles or cable cladding, provide durability but lack the softness and flexibility of nylon fibers.
PBT vs PET
As fellow polyesters, PBT and PET share similarities but serve distinct roles. PET, with a higher melting point (250-260°C) and greater stiffness, dominates in packaging (e.g., bottles) and high-strength fibers for textiles. PBT, however, offers faster crystallization and better processability, making it ideal for injection-molded parts in applications like automotive sensors.
PBT fibers provide highly resistant to environmental stress in optical cable cladding, whereas PET fibers prioritize tensile strength. PBT’s lower moisture sensitivity also gives it an edge in humid conditions over PET.
PBT vs PEEK
PEEK is a premium engineering plastic with exceptional heat resistance (HDT >300°C) and mechanical performance, far exceeding PBT in extreme demanding applications like aerospace or medical implants. PBT’s advantages lie in its cost-effectiveness and ease of processing, with excellent resistance to chemicals and good electrical insulation for less extreme uses (e.g., connectors, housings).
While PBT fibers serve well in telecommunications, PEEK’s superior durability suits harsher environments. PBT is thus a practical choice where high performance meets budget constraints, but it cannot match PEEK’s elite capabilities.
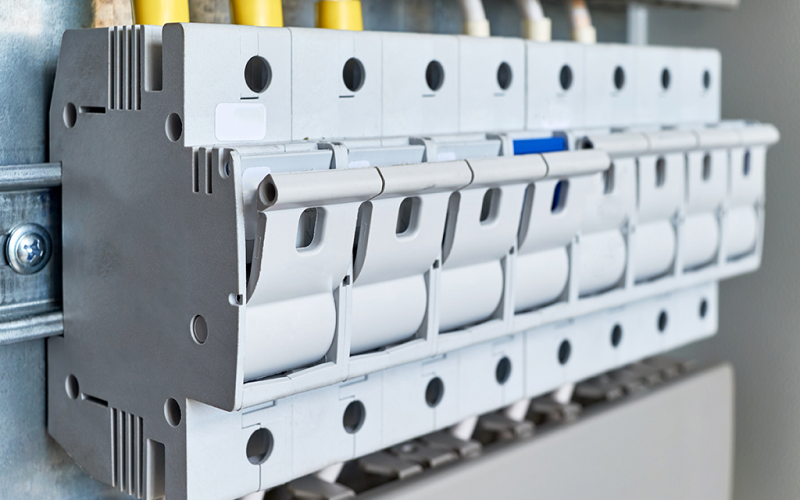
Conclusion
PBT is a high-performance thermoplastic polyester renowned for its excellent mechanical strength, heat resistance, electrical insulation, and chemical stability.
Its rapid crystallization and low moisture absorption make it highly effective in injection molding, finding widespread use in automotive components, electronic parts, optical cable cladding, and consumer goods.
As an efficient plastic solutions option, PBT excels in meeting demanding environmental requirements, though it has limited impact resistance and is susceptible to hydrolysis at high temperatures.
Through additives and process enhancements, PBT continues to offer reliable, durable material choices for modern industry, with promising future potential.