In recent years, with the increasing market demand, plastic packaging has become widely used across various industries.
Among them, packaging injection molding, as a primary manufacturing technology, is extensively employed in the packaging of fast-moving consumer goods.
It provides efficient and reliable packaging solutions for industries such as food, beverages, tea, and cosmetics.
So, what exactly is packaging injection molding? In the following content, we will delve into this process, analyzing its components, characteristics, and application areas in detail to help readers better understand this crucial technology.
Basic Of Packaging Injection Molding
Packaging injection molding typically refers to the production of plastic packaging using injection molding technology.
This process can efficiently produce packaging products with complex shapes and precise dimensions.
These products span multiple fields, including food containers, beverage bottles, cosmetic packaging, and pharmaceutical packaging, meeting the high standards required by various industries for packaging materials.
The injection molding process involves heating and melting plastic raw materials, which are then injected under high pressure into molds.
Once cooled and solidified, the material forms the desired packaging shape.
This method not only ensures high precision and consistency in packaging but also allows for the incorporation of innovative techniques such as multi-material injection molding and in-mold labeling (IML).
These advancements further enhance the functionality and aesthetics of the packaging, providing the plastic packaging industry with diverse and high-value packaging solutions.
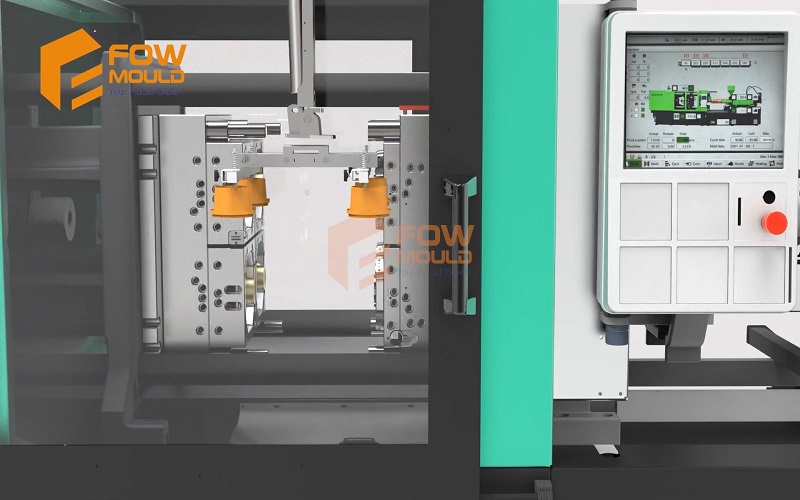
Types Of Packaging Injection Molding
Packaging injection molding is not just a single manufacturing technology.
To meet the packaging needs of various industries, plastic molding manufacturers use different types of injection molding processes.
Here are some common types of plastic packaging injection molding technologies:
Injection Molding
This is the most common type of packaging injection molding. It involves injecting molten plastic into a mold, which then cools and forms the desired shape.
This process is suitable for various thermoplastics and thermosetting materials.
It offers fast production speeds, high efficiency, and can be automated, allowing for the rapid production of large quantities of high-quality packaging products.
Thin-Wall Injection Molding
Thin-wall injection molding technology requires high flowability and cooling speeds, making it ideal for producing plastic products with thin walls.
Currently, in China, thin-wall injection molding is widely used in the production of food containers, medical boxes, cosmetics, stationery, and multimedia packaging, such as disposable lunch boxes and cosmetic bottles.
In-Mold Labeling (IML) Injection Molding
During the molding process, pre-printed film labels are placed on the inner walls of the mold.
The injection molding process then combines the label with the plastic part, creating a product surface with images and text. This technology, when combined with advanced robotic systems, enables efficient and automated production.
Products can achieve high design flexibility and diverse surface effects by using different decorative films.
Many market products, such as milk tea cups and instant noodle containers, which require immediate decoration and information labeling, utilize this technology.
These different types of packaging injection molding technologies not only improve production efficiency and product quality but also provide diverse manufacturing solutions for the plastic packaging industry.
Material Options For Packaging Injection Molding
Typically, most thermoplastic materials are suitable for packaging injection molding.
Here are some commonly used plastic packaging materials and their characteristics:
1.Polypropylene (PP)
Characteristics: Low density, high transparency, chemical resistance, and good fatigue resistance.
Uses: Lightweight food containers and pharmaceutical packaging.
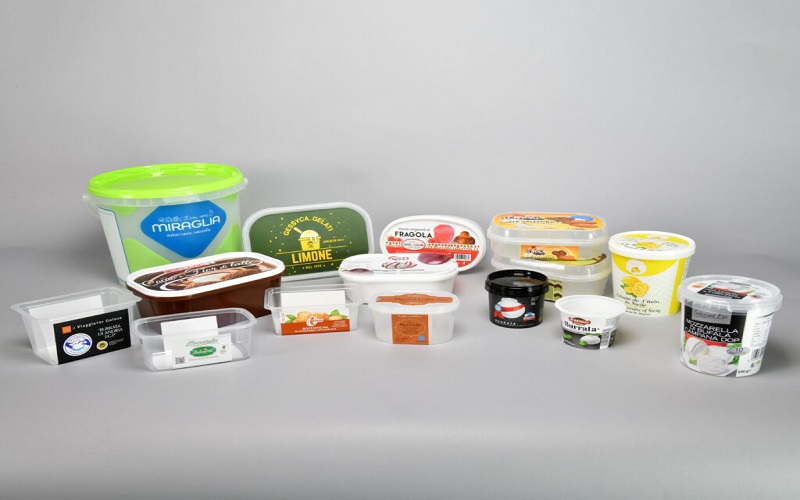
2.Polyethylene (PE)
Types: Low-Density Polyethylene (LDPE) and High-Density Polyethylene (HDPE).
Characteristics: LDPE is flexible and impact-resistant, while HDPE is hard and strong.
Uses: LDPE is used for squeeze bottles and plastic bags, while HDPE molding product is used for milk bottles and industrial containers.
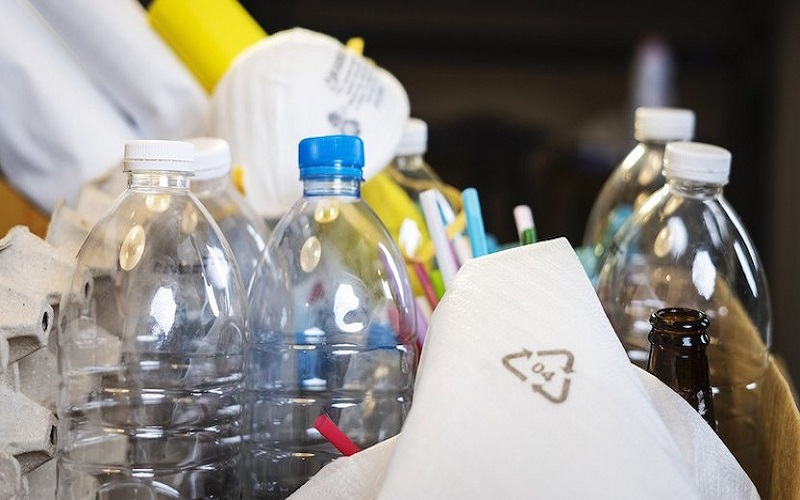
3.Polyethylene Terephthalate (PET)
Characteristics: High strength, excellent transparency, good chemical resistance, and recyclability.
Uses: PET injection molding commonly used for making beverage bottles and food containers.
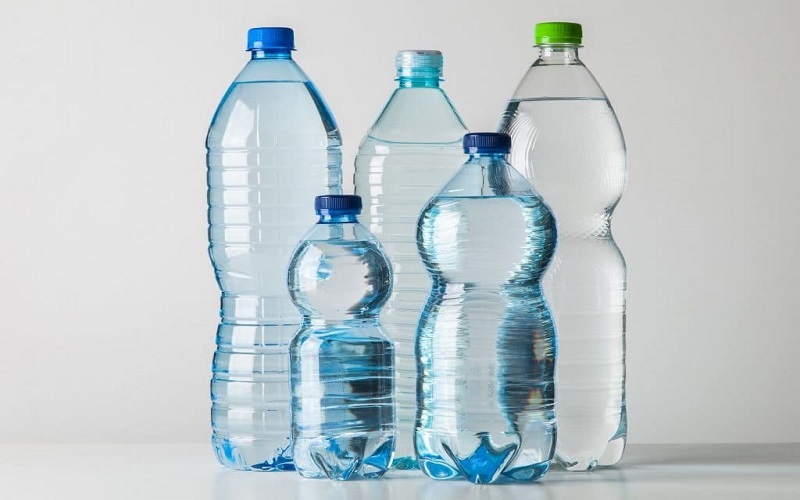
4.Polylactic Acid (PLA)
Characteristics: Biodegradable, good barrier properties, and excellent transparency.
Uses: PLA plastic Often used for eco-friendly packaging and disposable cutlery.
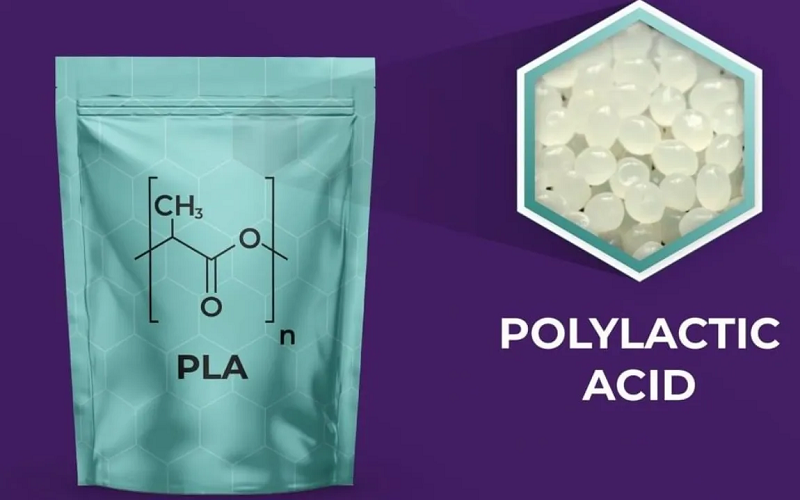
5.Polystyrene (PS)
Characteristics: Low moisture absorption, high transparency, and high rigidity and compressive strength.
Uses: PS injection molded products are widely used for disposable tableware, food packaging, and CD cases.
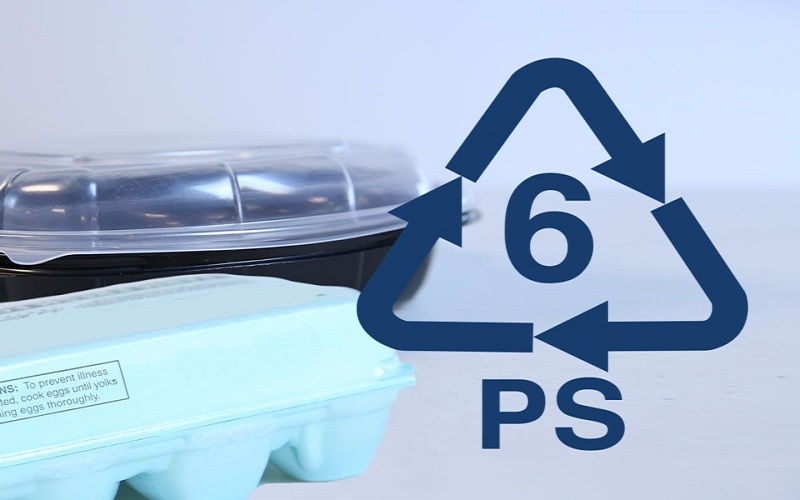
It is precisely this diverse selection of materials that allows packaging injection molding to meet the functional, cost, and environmental requirements of various products.
Characteristics Of Plastic Packaging Molding
Next, we will explore the key features of packaging injection molding in detail to understand how this process drives the development of the packaging industry.
- High Efficiency
This process can produce large quantities of high-quality packaging products in a short time.
The high level of automation reduces manual intervention and increases production efficiency.
- High Precision
Plastic injection molding can create products with precise dimensions and complex shapes, meeting strict design and functional requirements.
- Material Diversity
Injection molding is suitable for most thermoplastic materials, such as PET, PP, PE, and PS.
Injection molding companies can choose the appropriate materials based on different application needs.
- Versatility
Multi-material injection molding can combine various material properties in a single product, enhancing its functionality. For example, a packaging product can have both soft and hard areas to meet different usage requirements.
- Cost-Effectiveness
Due to its fast production speed and high level of automation, the unit production cost of the injection molding process is relatively low.
- Flexible Design
Injection molding allows designers to create complex and innovative shapes, enabling unique packaging designs and enhancing the product’s market competitiveness.
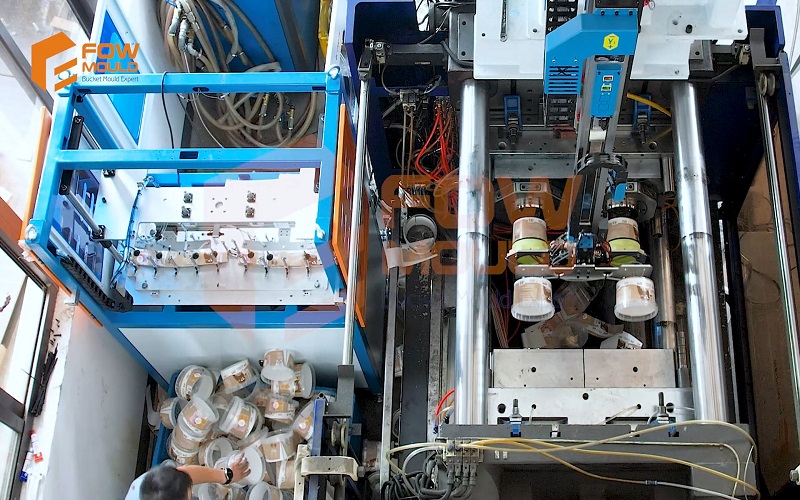
Applications Of Packaging Injection Molded Products
Leveraging the aforementioned process advantages, packaging injection molding holds a significant position in the plastic packaging industry.
Whether it is plastic bottles, plastic boxes, or plastic containers, injection molding technology provides efficient and reliable production solutions.
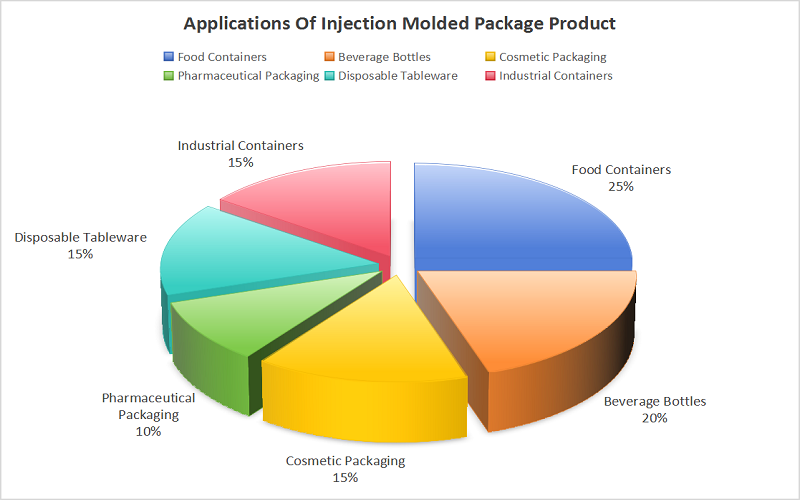
- Food and Beverage Packaging
Injection molding can use food-grade plastics to produce various food and beverage packaging containers, such as beverage bottles, storage boxes, and ready-to-eat utensils.
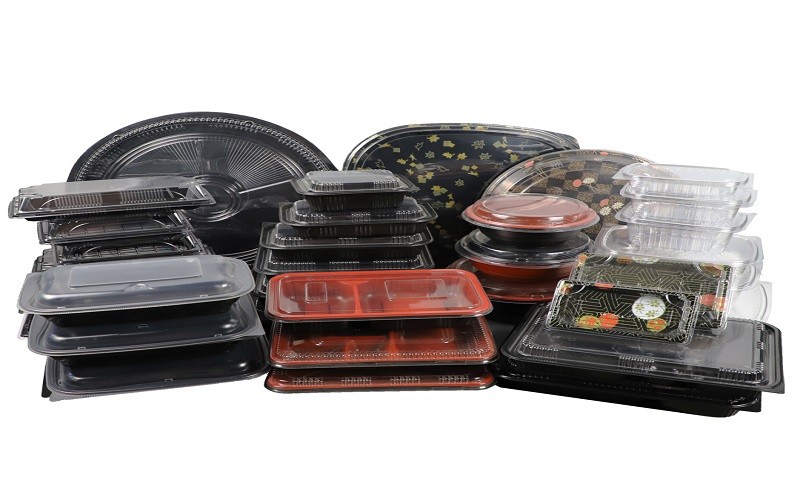
- Cosmetic Packaging
Packaging injection molding technology can produce complex shapes and high-quality surfaces for packaging, such as cosmetic bottles, cream jars, and makeup cases, meeting the market’s demand for high-end packaging.
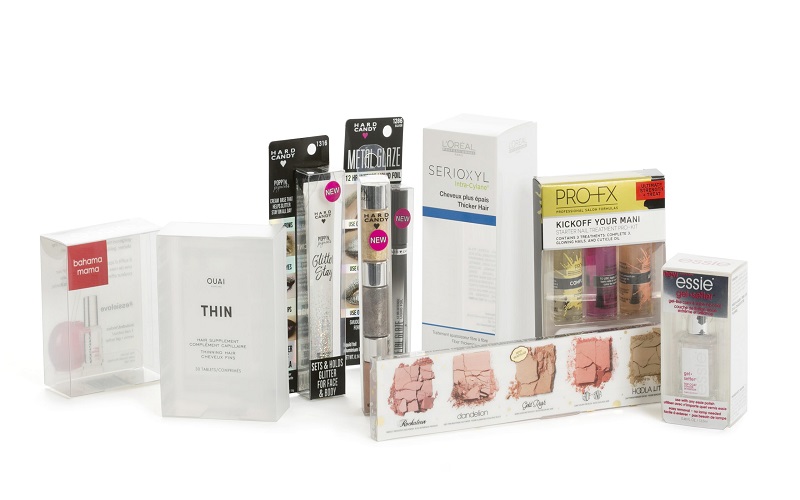
- Medical and Pharmaceutical Packaging
Plastic injection molding is commonly used for making medicine bottles, syringes, and medical device housings.
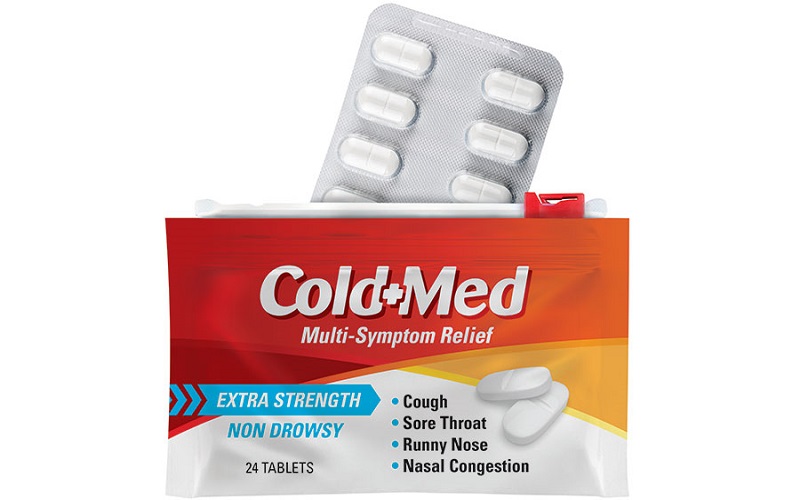
- Disposable Tableware
Utilizing the fast production and consistency of injection molding technology, it is often used for large-scale production of plastic cutlery, cups, and plates.
Especially with the use of biodegradable materials like PLA, it can meet environmental needs.
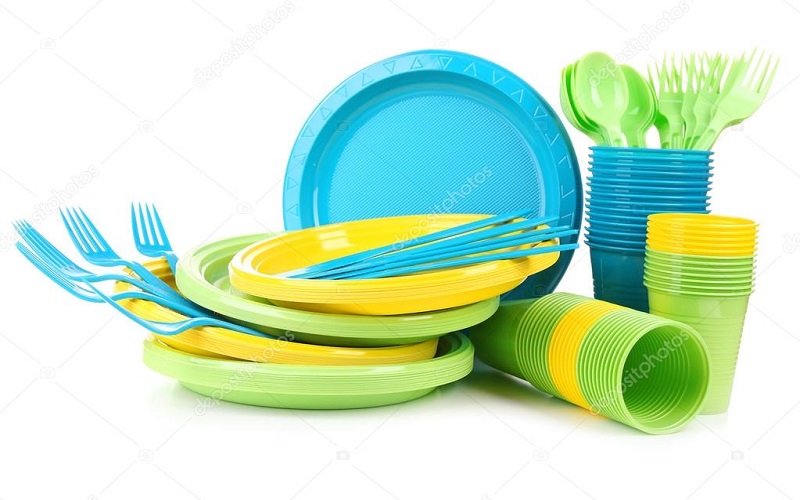
- Industrial Containers
In the industrial sector, injection molding is used to manufacture various sturdy and durable containers, such as chemical containers, storage bins, and transport packaging.
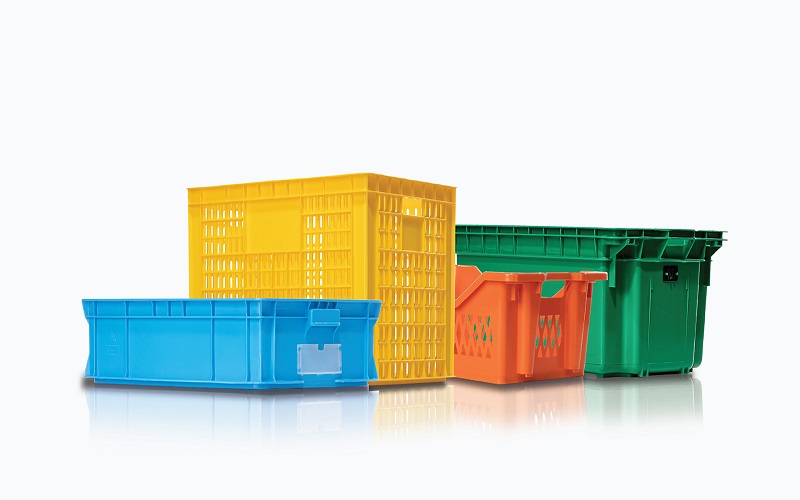
Sustainability in Packaging Injection Molding
In the context of growing environmental awareness, the sustainable development of packaging injection molding technology has become increasingly important.
Here are several key factors in how packaging injection molding promotes sustainability:
- Use of Biodegradable Materials
Materials like PLA (Polylactic Acid) and other plant-based plastics are biodegradable and can naturally decompose after use, reducing the impact of plastic waste on the environment.
- Improving Material Recycling Rates
To enhance plastic recycling efficiency, many countries are now improving recycling technologies and upgrading recycling facilities.
This effort not only reduces the consumption of virgin plastic materials but also decreases the environmental burden of plastic waste.
- Eco-friendly Packaging Solutions
Packaging injection molding designs and uses biodegradable and recyclable materials to manufacture reusable packaging containers.
These solutions meet the market’s demand for sustainable development.
Through these initiatives, packaging injection molding not only meets the market demand for efficient, high-quality packaging but also actively responds to the global call for environmental protection and sustainability.
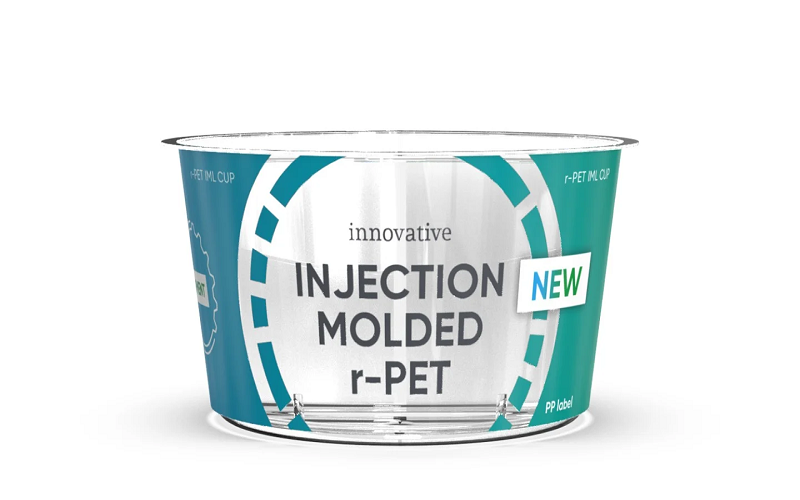
Custom Packaging Injection Molding Service
As a leader in the Chinese injection molding industry, FOWMOULD has been dedicated to providing one-stop injection molding services to meet the customized packaging needs of clients for 40 years.
FOWMOULD’s services encompass the entire process from initial design and mold making to final injection production.
With an experienced design and manufacturing team, FOWMOULD can quickly respond to customer needs and provide professional technical support and services.
Currently, FOWMOULD’s clients span various industries worldwide, including food and beverage, cosmetics, medical and pharmaceutical, and industrial sectors.
By delivering high-quality packaging injection products to many renowned companies, FOWMOULD has earned high recognition and trust from its clients.
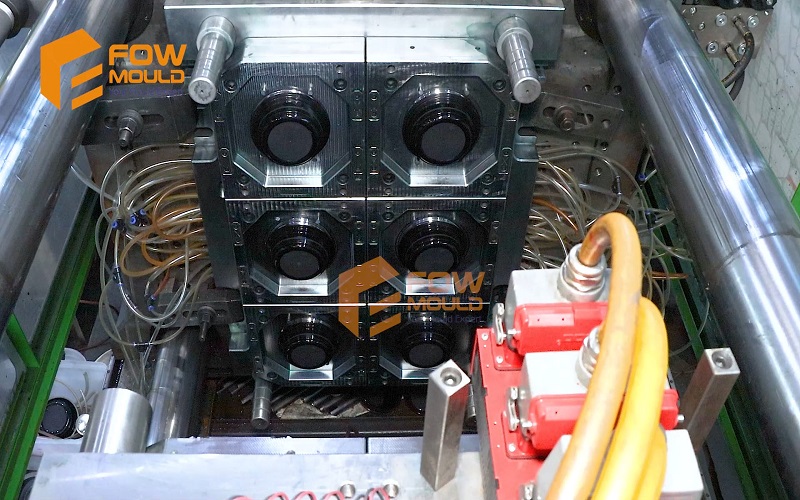
Conclusion
As a key technology in the packaging industry, packaging injection molding provides the market with reliable and cost-effective packaging solutions through its efficient production, precise control, material diversity, and design flexibility.
Additionally, with the increasing environmental awareness, injection molding processes are continually innovating by adopting more biodegradable materials and recyclable plastics, promoting the development of green packaging.
In summary, packaging injection molding not only enhances product quality and production efficiency but also expands the applications of plastic packaging, making significant contributions to the sustainable development of the industry.