PA66, or Polyamide 66, is a high-performance engineering thermoplastic materials renowned for its strength, heat resistance, and versatility.
Since its development by DuPont in the 1930s, this synthetic polymer has become indispensable in industries like automotive, textiles, and manufacturing.
This article aims to provide a clear and comprehensive introduction to PA66, exploring its key properties, production process, diverse applications, and enduring significance.
From its molecular structure to its role in modern innovation, we’ll uncover why PA66 remains a vital material in today’s world.
What Is Polyamide 66?
Polyhexamethylene adipamide, commonly known as olyamide 66 or nylon 66, is a major type of polyamide plastic, typically produced through the condensation polymerization of adipic acid and hexamethylenediamine.
As a synthetic polymer, polyamide 6 is insoluble in common solvents, dissolving only in specific substances like m-cresol. It boasts high mechanical strength, hardness, and rigidity, making it an ideal engineering plastic.
It is widely used to manufacture mechanical components such as gears and lubricated bearings, as well as to replace non-ferrous metals in machine casings and automotive engine blades. Additionally, PA66 can be processed into synthetic fibers for textiles and ropes.
The history of PA66 dates back to the 1930s. In 1937, W.H. Carothers of the DuPont Company in the United States published the first patent, successfully producing a sample of nylon fiber. A pilot plant was established in 1938, followed by the launch of industrial production in 1939.
Initially, PA66 was primarily used to create fibers, ropes, and coating materials, establishing its foundational role in material science.
Today, it is one of the most commonly used materials in the textile and plastic industries.
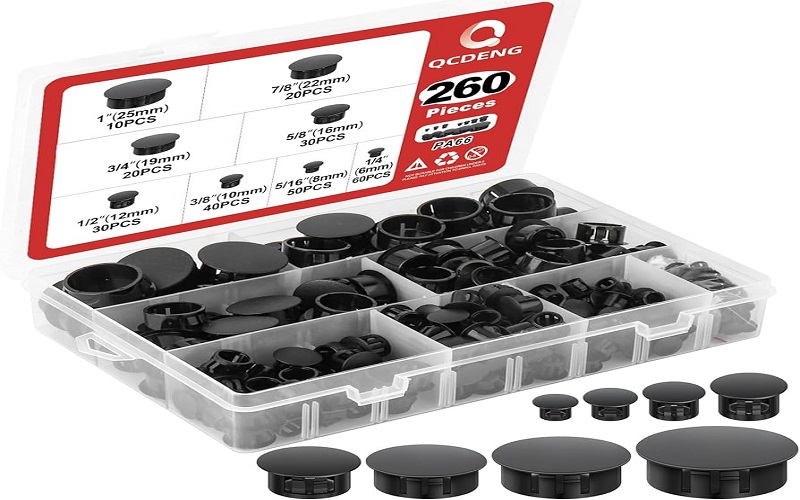
Key Properties of PA 66 Material
Nylon 66, a prominent member of the nylon material, owes its widespread use in industries such as automotive, electronics, and mechanical manufacturing to its exceptional overall performance.
This includes high strength, excellent wear resistance, chemical corrosion resistance, and ease of processing.
Synthesized through the condensation polymerization of adipic acid and hexamethylenediamine, it exhibits the characteristic structure of an aliphatic polyamide.
Below are the primary performance characteristics of Nylon 66:
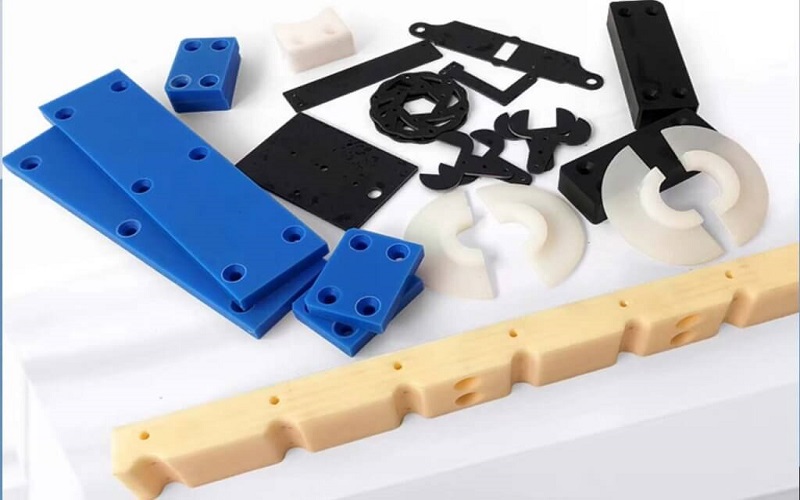
Excellent Mechanical Properties
Polyamide 66 demonstrates outstanding mechanical strength, stiffness, hardness and toughness, enabling it to maintain excellent shape stability under heavy loads and high-stress conditions.
This allows PA66 compounds to withstand heavy loads, impacts, and vibrations, making them ideal for automotive components, industrial machinery, and structural parts.
Good Wear Resistance
With exceptional wear resistance and a low friction coefficient, Nylon 66 excels in applications involving prolonged friction and abrasion, such as bearings, gears, and pulleys.
However, its creep resistance is influenced by moisture absorption and temperature; in humid or high-temperature environments, the molecular chains may relax, leading to increased creep.
Chemical Resistance
The material effectively resists corrosion from various chemicals, including greases, oils, and other substances. However, it shows limited resistance to strong acids, bases, and certain solvents.
Self-Lubricating Property
The internal structure of nylon 66 imparts a degree of self-lubrication, reducing the need for additional lubricants and extending its service life.
Moisture Absorption
Nylon 66 has a notable tendency to absorb moisture, which can affect its dimensional stability and electrical properties. While this enhances its toughness, designers must account for potential dimensional changes in product development.
Heat Resistance
With a melting point ranging from 220°C to 260°C, polyamide 66 exhibits excellent heat resistance, retaining its strength and rigidity even in elevated temperature environments.
This high melting point enables nylon 66 to withstand elevated temperatures without losing its structural integrity.
Electrical Insulating Properties
Nylon 66 exhibits exceptional electrical insulation properties in its dry state, with a volume resistivity of 10¹²–10¹³ Ω·cm, a dielectric strength of 20–25 kV/mm under dry conditions, and a dielectric constant of 3.6–4.0 (at 1 MHz, dry state). These attributes make it a reliable choice for applications in the electronics and electrical industries.
However, its moisture absorption significantly impacts its electrical performance, necessitating special caution when used in humid environments.
Nylon 66 Properties Data Sheet | |
Properties | Value |
Density(g/cm3) | 1.13–1.15 |
Melting Point(℃) | 255–265 |
Heat Deflection Temperature(℃) | 70-90 |
Water Absorption(%) | 2.5–3.0 |
Impact Strength (J/m) | 50–60 |
Tensile Strength(MPa) | 80–85 |
Friction Coefficient | 0.2–0.4 |
Processing Techniques Of Nylon66 Plastic
Polyamide 66,thanks to its excellent thermal and mechanical properties, is highly versatile in manufacturing, lending itself to a variety of processing techniques, including injection molding and extrusion.
Injection Molding
Nylon injection molding is the most widely used technique for shaping PA66 into intricate molded parts. Molten PA66 is injected into a injection mold under high pressure, cooled, and then ejected as a solid component.
PA66 must be dried (e.g., at 80°C for 4–6 hours) to a moisture content below 0.2% to prevent defects like bubbles or hydrolysis during processing.
This method makes it possible to produce large quantities of products with complex shapes and high dimensional accuracy in a short period of time.
Extrusion Molding
Extrusion involves forcing molten PA66 through a die to create continuous profiles such as tubes, rods, or films. The material is then cooled and cut to desired lengths.
At this stage, Nylon66 can either be extruded and granulated into pellets for later use or directly spun into fibers by extrusion through a spinneret—a small metal plate with fine holes—followed by cooling to form filaments.
It is ideal for producing long, uniform shapes or continuous fibers, with flexibility in downstream processing (granulation or spinning).
Additive Manufacturing
PA66 filaments are increasingly utilized in nylon 3D printing, capitalizing on the material’s impressive strength and flexibility to enable rapid prototyping and small-batch production with reliable performance.
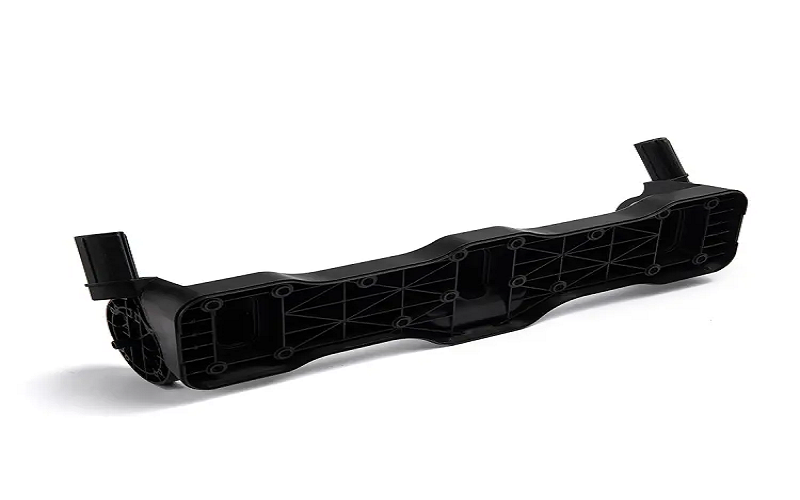
Modified Method Of Polyamide 66
The modification methods of Polyamide 66 primarily include chemical and physical modifications. Chemical modifications encompass reactions such as copolymerization, grafting, and crosslinking, whereas physical modifications rely on forces like hydrogen bonding and adsorption.
Specific methods include filler modification, polymer blending modification, and the addition of additives.
Chemical Modification
Copolymerization Modification: By selecting appropriate monomers, new structural units, polymer chains, or functional groups are introduced into the polyamide 66 molecular chain, thereby altering its properties. This method can enhance the strength and processability of polyamide 66 while reducing its moisture absorption, and it can even impart flame retardancy or other special properties.
Grafting Modification: Other molecules are grafted onto the polyamide 66 molecules through chemical reactions to improve its performance. For instance, grafting pa 66 short fibers with methacrylic acid (MAA) significantly enhances their mechanical properties.
Crosslinking Modification: Crosslinking reactions increase the crosslinking points between molecules, enhancing the material’s heat resistance and mechanical strength.
Physical Modification
Filler Modification:Adding inorganic or organic fillers such as glass fibers and carbon fibers to PA66 can enhance its mechanical properties and thermal stability. For example, the tensile strength of PA66/CF composites can exceed 200 MPa.
Polymer Blending Modification: Blending with other polymers (such as MXD6) optimizes the mechanical and crystallization properties of nylon 66.
Addition of Additives: Adding toughening agents (such as POE-g-MAH), flame retardants (such as MDCP and ZDCP), etc., to improve specific properties of PA66.
Examples
PA66/6T Copolymer: Synthesized through melt polycondensation, the PA66/6T copolymer containing benzene rings shows slightly improved tensile strength but significantly enhanced notched impact strength compared to the original material.
PA66/12T Copolymer: Compared to pure nylon, the PA66/12T copolymer has a lower melting point and relative viscosity, which is beneficial for product molding and processing.
Dimer Acid-Based Copolyamide: The copolyamide material prepared from PA66 salt, dimer acid, and hexamethylenediamine exhibits lower moisture absorption and good resistance to high and low temperatures.
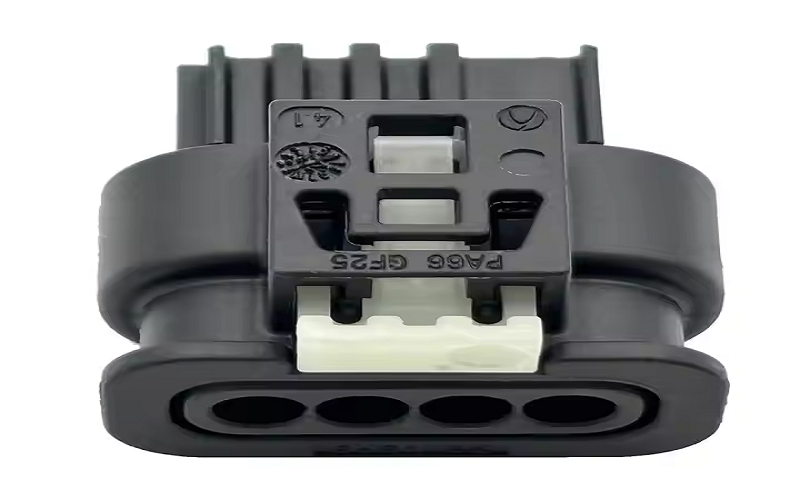
Is PA66 Safe?
Nylon 66 is generally considered safe under normal usage conditions, owing to its chemical stability, which prevents the release of harmful substances in consumer products (such as clothing and ropes) and engineering applications, posing no significant toxicity risk to humans and exhibiting low environmental toxicity.
However, nylon 66 may release certain hazardous substances during processing and use. Research from the German Federal Institute for Risk Assessment indicates that nylon 6 and nylon 66 can emit cyclic monomers and oligomers during high-temperature processing, substances that may possess neurotoxic and carcinogenic properties.
Additionally, nylon 66 is not widely certified as food-grade; unmodified versions may degrade under high temperatures or acidic conditions, and combustion can produce smoke and toxic gases (such as carbon monoxide).
Therefore, when using nylon 66 products, prolonged contact or consumption of items containing PA66 should be avoided, while ensuring proper ventilation during processing and prioritizing flame-retardant or specially modified variants to enhance safety.
To learn more about the safety of nylon, click here to read the article “Is Nylon safe”.
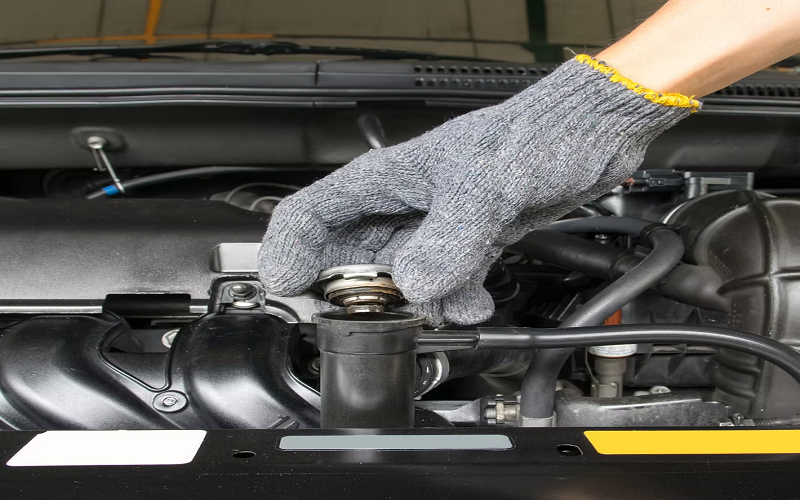
Various Applications Of Nylon 66 Products
Nylon 66 is a versatile material whose exceptional strength, wear resistance, heat tolerance, and processability make it a cornerstone in numerous industries.
From industrial components to everyday consumer goods, many applications showcase its adaptability and reliability.
Below are the primary areas where Nylon 66 products excel:
Industrial Uses
Mechanical Components: Nylon 66’s high strength, rigidity, and wear resistance make it ideal for manufacturing gears, bearings, bushings, and rollers. Its self-lubricating property reduces maintenance needs in machinery.
Automotive Parts: Widely used in engine components like intake manifolds, radiator end tanks, and fuel system parts, Nylon 66 withstands heat and chemical exposure. Its lightweight nature also aids in improving fuel efficiency.
Machine Housings: As a replacement for metals, Nylon 66 is molded into durable casings for tools and equipment, offering corrosion resistance and cost-effectiveness.
Consumer Products
Textiles and Fibers: Spun into filaments, Nylon 66 is a staple in clothing (e.g., stockings, sportswear), ropes, and fishing lines, valued for its toughness and elasticity.
Household Items: From kitchen utensils (e.g., spatulas) to toothbrush bristles, Nylon 66’s durability and ease of molding make it a practical choice for daily use products.
Sporting Goods: Used in items like tennis racket strings and ski bindings, leveraging its flexibility and impact resistance.
Emerging Applications
3D Printing: Nylon 66 filaments are increasingly utilized in additive manufacturing, capitalizing on the material’s impressive strength and flexibility to enable rapid prototyping and small-batch production with reliable performance.
Electronics: Its electrical insulation properties suit it for connectors, cable ties, and switch housings, though moisture sensitivity requires careful design in humid environments.
Lightweight Engineering: Reinforced variants (e.g., with glass fiber) are used in aerospace and structural applications, balancing strength with reduced weight.
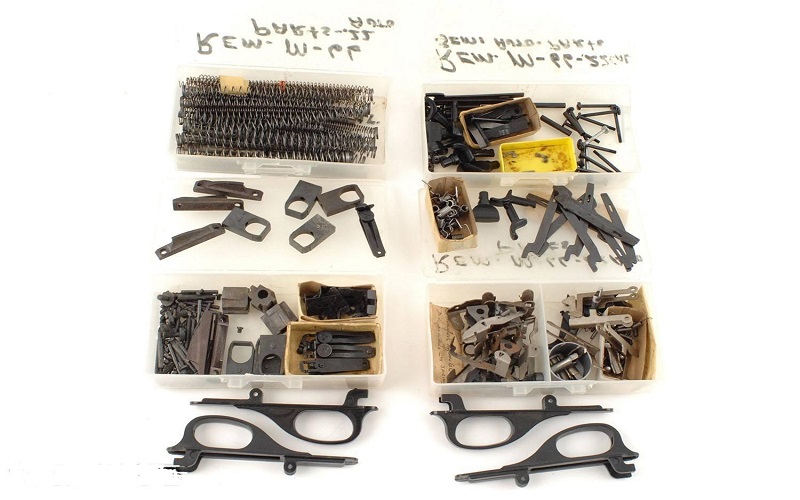
PA 6 vs PA66
PA6 and PA66 are two of the most widely used polyamides, sharing similarities as engineering plastics and fibers but differing in composition, performance, and suitability for specific applications. Below is a breakdown of their key distinctions:
1. Chemical Structure
PA6: Formed by the polymerization of caprolactam, a single monomer, resulting in a repeating unit with 6 carbon atoms.
PA66: Synthesized via condensation of hexamethylenediamine and adipic acid, featuring a dual-monomer structure with 6+6 carbon atoms.
PA66’s symmetrical structure leads to tighter molecular packing and higher crystallinity than PA6.
2. Key Properties
Property | PA6 | PA66 |
---|---|---|
Melting Point | 220–225°C | 255–265°C |
Tensile Strength | 70–80 MPa (dry) | 80–85 MPa (dry) |
Flexibility | Higher (more elastic) | Lower (more rigid) |
Moisture Absorption | 9–10% (saturated) | 8–9% (saturated) |
Wear Resistance | Good | Excellent |
Heat Resistance | Moderate | Superior |
Impact Resistance | Better in cold conditions | Slightly lower |
PA6: Offers greater flexibility and toughness, especially at low temperatures, but absorbs slightly more moisture, impacting dimensional stability.
PA66: Excels in strength, rigidity, and heat resistance due to its higher melting point and crystallinity, making it more durable under thermal stress.
3. Processing
PA6: Easier to process due to lower melting point and better flowability, often preferred for complex molds or extrusion into films.
PA66: Requires higher processing temperatures (260–300°C vs. 240–270°C for PA6), but its superior strength suits precision parts via injection molding.
4. Applications
PA6:
Textiles (carpets, clothing) due to flexibility and dyeability.
Automotive parts (e.g., air intake ducts) where toughness is key.
Films and packaging, leveraging its processability.
PA66:
High-heat automotive components (e.g., radiator tanks, engine covers).
Mechanical parts (gears, bearings) needing wear resistance and rigidity.
3D printing filaments for stronger prototypes.
5. Cost and Availability
PA6: Generally less expensive and more widely available, as its single-monomer production is simpler.
PA66: Slightly costlier due to dual-monomer synthesis and higher performance, often chosen for premium applications.
While PA6 and PA66 share polyamide traits like durability and versatility, their differences in structure and properties cater to distinct needs.
PA6 shines in flexibility and ease of processing, while PA66 stands out for its superior strength and thermal stability, making each a valuable choice depending on the specific demands of the application.
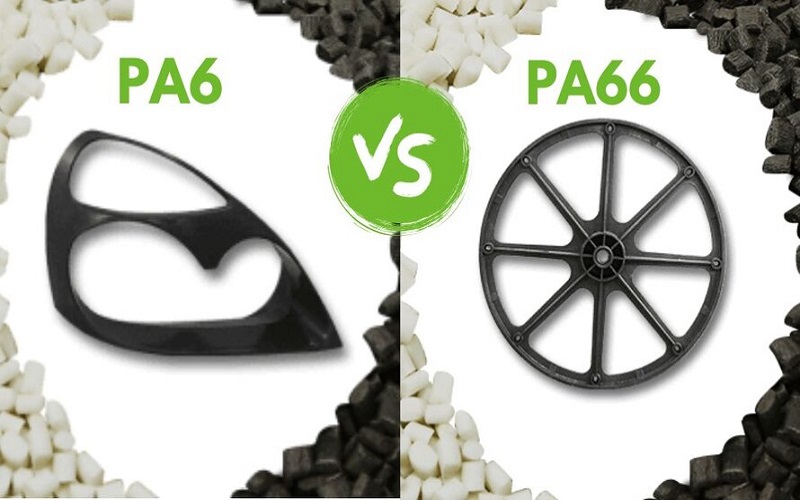
Conclusion
Polyamide 66 stands as a versatile engineering material, its high strength, wear resistance, and heat tolerance (melting at 255–265°C) making it indispensable in automotive, mechanical, and consumer applications, from engine parts to textiles, while its processability via injection molding, extrusion, and 3D printing enhances its adaptability.
Despite challenges like moisture absorption and potential emissions of cyclic monomers during processing—as noted by the German Federal Institute for Risk Assessment—its chemical stability and ability to replace metals underscore its significance.
In today’s world of innovation and sustainability, understanding PA66 is vital, as its role in lightweight design and emerging technologies grows, tempered by the need to manage its limitations through informed design and recycling efforts, ensuring it remains a cornerstone of modern engineering.