PA plastic, known as Polyamide, commonly referred to as nylon, is a type of engineering plastic widely used in both industrial and everyday applications.
Since its development in the early 20th century, PA plastic has become a crucial component of modern material science due to its excellent properties and diverse applications.
This article will delve into the composition, properties, processing methods, and application areas of PA plastic, providing an in-depth exploration of its characteristics.
Moreover, it will analyze its performance in terms of safety and environmental impact to help readers gain a comprehensive understanding of this material.
What Is Polyamide (PA)?
Polyamide or commonly called nylon, is a semi crystalline thermoplastic with low density and high thermal stability by the presence of repeating amide groups —[NHCO]— in its main molecular chain.These materials are named based on the number of carbon atoms in their synthetic monomers.
The development of PA plastics can be traced back to the 1930s when DuPont first commercialized nylon for use in fibers.
Polyamides can be synthesized using various methods, including the polycondensation of dicarboxylic acids and diamines, or through the polymerization of lactams.
This versatility in synthesis allows for a wide range of PA materials, each with unique properties tailored to specific applications. For instance, both nylon 6 and nylon 66 are popular types of nylon used extensively in industries.
From a molecular standpoint, polyamides contain repeating units of amide linkages, which contribute to their excellent mechanical properties and thermal stability. Whether it’s aliphatic, semi-aromatic, or fully aromatic, each type of polyamide brings something unique to the table.
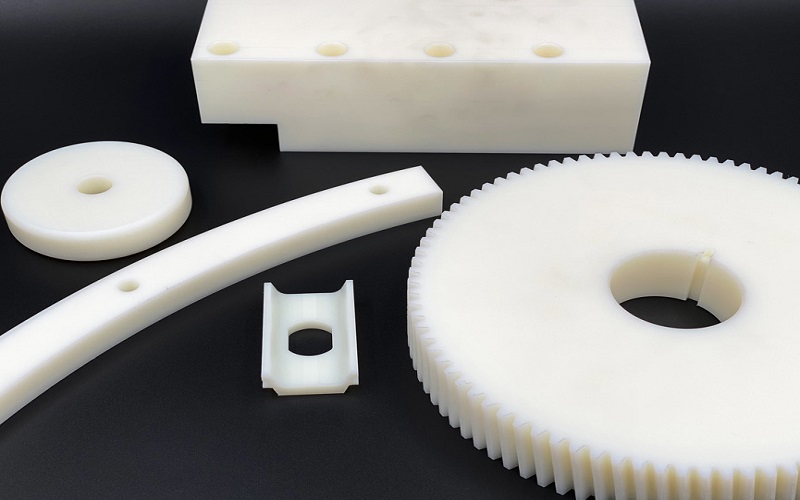
Key Properties Of Polyamide Material
The polyamide molecular structure consists of repeating amide linkages (-CONH-), which endow the material with high strength, heat resistance, and chemical stability, while also introducing specific traits like moisture absorption and processing characteristics.
Below is a detailed exploration of how these polyamide properties enable PA to excel in a wide range of applications.
Excellent Mechanical Properties
PA plastic exhibits high strength, toughness, and exceptional wear resistance. Its tensile strength and impact resistance are impressive, particularly for PA66 and glass-fiber-reinforced variants, enabling it to withstand significant loads and making it suitable for structural components.
Its wear resistance makes it an ideal choice for friction parts like bearings and gears.
High Thermal Resistance
PA plastic demonstrates good heat resistance. PA6 has a melting point of around 223°C, while PA66 reaches up to 255°C. Certain modified grades can endure prolonged use above 150°C, making them suitable for high-temperature environments such as automotive engine components.
Chemical Resistance
PA plastic offers good chemical resistance to oils, fuels, lubricants, and various organic solvents. However, it may degrade under exposure to strong acids, alkalis, or oxidizing agents, so it should be avoided in extreme chemical conditions.
Moisture Absorption
PA plastic is hygroscopic, particularly PA6 and PA66, which can lead to dimensional expansion or performance changes after absorbing water. In contrast, PA11 and PA12, with longer molecular chains, have lower moisture absorption and better dimensional stability.
Electrical Insulation
In dry conditions, PA plastic provides excellent electrical insulation, making it widely used in electrical components. However, its insulation properties decrease after moisture absorption, requiring special consideration in humid environments.
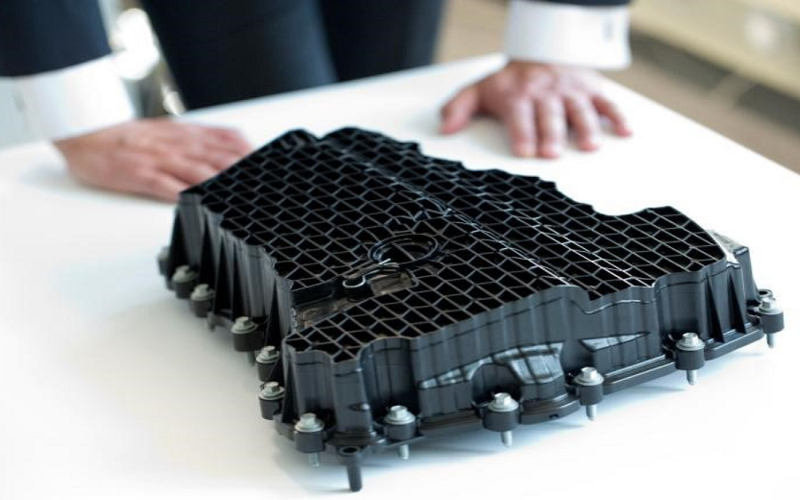
Types of Polyamides
Polyamides are a family of synthetic polymers characterized by repeating amide linkages (-CONH-) in their molecular structure.
They are classified based on the number of carbon atoms in their monomer units and the method of synthesis, leading to a variety of types with distinct properties and applications. Below is an overview of the main types of polyamides:
Aliphatic Polyamides
These are the most common types, derived from aliphatic (straight-chain) monomers. They are further divided based on whether they are synthesized from a single monomer or two different monomers.
PA 6(Nylon 6)
Synthesis: Made by the ring-opening polymerization of caprolactam, a single monomer with 6 carbon atoms.
Properties: Good toughness, wear resistance, and moderate strength; melting point around 223°C; relatively high moisture absorption.
Applications: Fibers (e.g., textiles, carpets), injection-molded parts (e.g., gears, housings).
PA66 (Nylon 6,6)
Synthesis: Formed by the condensation polymerization of hexamethylenediamine (6 carbons) and adipic acid (6 carbons).
Properties: Higher strength, stiffness, and thermal stability than PA6 (melting point ~255°C); excellent mechanical performance.
Applications: Automotive parts (e.g., engine components), electrical connectors, ropes.
PA11 (Nylon 11)
Synthesis: Produced from 11-aminoundecanoic acid, derived from castor oil (a bio-based source).
Properties: Lower moisture absorption, greater flexibility, and better chemical resistance; melting point ~185°C.
Applications: Flexible tubing (e.g., fuel lines), medical devices, powder coatings.
PA12 (Nylon 12)
Synthesis: Made from laurolactam or 12-aminododecanoic acid.
Properties: Similar to PA11 but with even lower water absorption and excellent dimensional stability; melting point ~178°C.
Applications: 3D printing filaments, cables, precision parts.
PA46 (Nylon 4,6)
Synthesis: Synthesized from tetramethylenediamine (4 carbons) and adipic acid (6 carbons).
Properties: Exceptional heat resistance (melting point ~295°C) and mechanical strength; low creep under load.
Applications: High-temperature automotive and electrical components (e.g., under-hood parts).
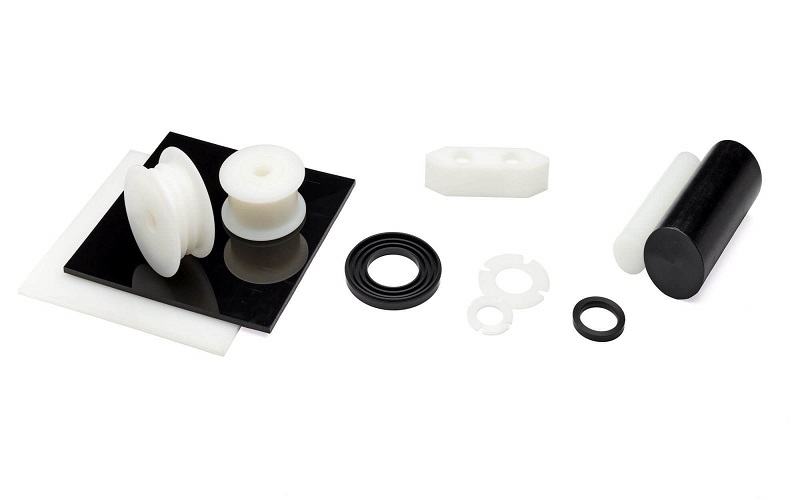
Semi-Aromatic Polyamides
These incorporate aromatic groups into the polymer chain, enhancing thermal and mechanical properties.
PA6T (Nylon 6T)
Synthesis: Combines hexamethylenediamine with terephthalic acid (an aromatic acid).
Properties: High melting point (~310°C), excellent heat resistance, and rigidity; less moisture-sensitive than aliphatic types.
Applications: Electronics (e.g., surface-mount components), high-performance engineering parts.
PA9T (Nylon 9T)
Synthesis: Made from nonanediamine (9 carbons) and terephthalic acid.
Properties: Superior heat and chemical resistance, low water absorption; melting point ~308°C.
Applications: Automotive fuel systems, electrical housings.
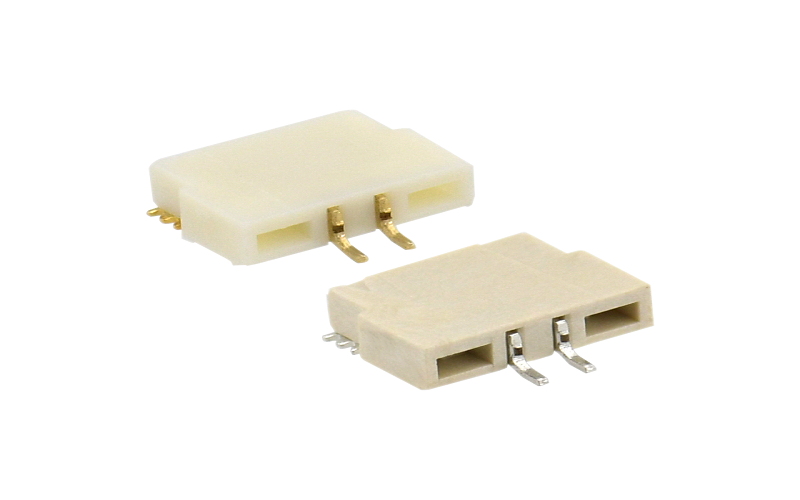
Aromatic Polyamides (Aramids)
Fully aromatic polyamides, distinct from typical nylons, are known for extreme strength and heat resistance.
Poly(p-phenylene terephthalamide) (e.g., Kevlar)
Synthesis: Derived from p-phenylenediamine and terephthalic acid.
Properties: Exceptional tensile strength, flame resistance, and thermal stability (decomposes above 500°C); not melt-processable.
Applications: Bulletproof vests, aerospace composites, protective gear.
Poly(m-phenylene isophthalamide) (e.g., Nomex)
Synthesis: Made from m-phenylenediamine and isophthalic acid.
Properties: Excellent flame and heat resistance, good chemical stability; not melt-processable.
Applications: Firefighter suits, insulation paper, aerospace materials.
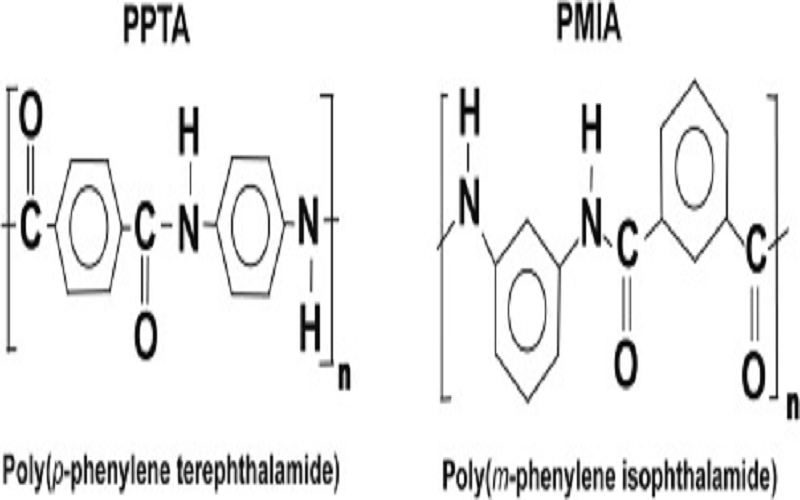
Modifying Polyamides
Modified nylon is a class of engineering plastics, is based on nylon raw materials in order to change its physical properties and the formation of granular products. The output of such products is modified according to the different needs of some manufacturers.
Reinforced PA
By adding 30% glass fiber to PA, the mechanical properties, dimensional stability, heat resistance, and aging resistance of PA are significantly improved.
The enhanced mechanical properties make it ideal for high-stress applications in the automotive and industrial sectors.
However, the molding process for glass filled nylon requires higher injection molded pressure and temperature. Due to the orientation of glass fibers during molding, the shrinkage rate and mechanical properties vary, necessitating careful mold design.
Weather-resistant PA
UV-absorbing additives such as carbon black are added to PA, and these greatly enhance the self-lubricating properties of PA and wear on metal.
These additives improve the material’s ability to withstand harsh weather conditions, making it suitable for outdoor applications.
The addition of these UV-absorbing agents requires specific processing equipment to handle the enhanced abrasion resistance and impact resistance. This ensures that the final product maintains its integrity and performance over time.
Flame-retardant PA
Due to the addition of flame retardants in PA, most flame retardants tend to decompose at high temperatures, releasing acidic substances that have a corrosive effect on metals.To mitigate this, the processing equipment must be specially treated to resist corrosion.
In terms of processing, it is advisable to control the barrel temperature to avoid excessive heat and to ensure that the injection speed is not too fast.This careful control prevents degradation and ensures the mechanical properties of the final product remain intact.
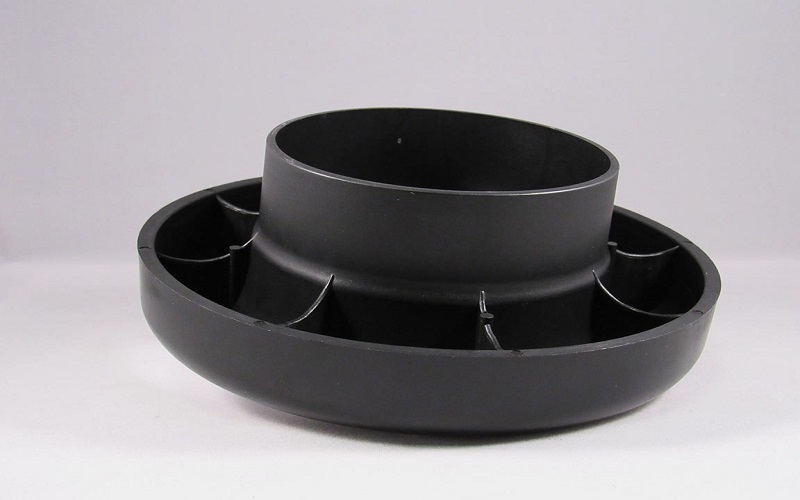
Processing Method Of PA Plastics
The processing methods for PA plastics are critical to shaping them into functional products. From automotive parts to textiles, the choice of processing technique can significantly impact the performance of the final product.
Below is an overview of the primary processing methods used for PA plastics, along with key considerations for each.
Injection Molding
Nylon injection molding is a major method of processing polyamide plastics by melting nylon resin, injecting it into a mold, and cooling and curing it into shape to make high-precision parts.
This method is widely used to manufacture automotive parts, electronic connectors, and everyday items due to its high precision and efficiency.
However, due to nylon’s hygroscopic nature, the resin must be dried before injection molding to prevent defects like bubbles or compromised strength. Proper drying and precise temperature control are essential to ensure high-quality products.
Extrusion
The extrusion process maintains uniformity in the cross-section of polyamide products, crucial for performance consistency。
This method is ideal for producing items like pipes, rods, and sheets, which require consistent dimensions and properties.
The extrusion process ensures that the material properties are evenly distributed across the product’s cross-section.
Considerations In PA Plastic Processing
Moisture control is crucial in PA plastic processing. PA plastics absorb moisture from the air, which can lead to hydrolysis during processing, causing defects like splay marks or reduced strength. Low moisture absorption is essential, and drying before processing is non-negotiable.
Thermal degradation is another concern. Excessive heat or prolonged exposure to high temperatures can degrade PA, reducing its molecular weight and mechanical properties. Precise temperature control is vital. Additionally, incorporating additives like glass fibers or flame retardants can alter processing conditions, requiring adjustments to equipment settings.
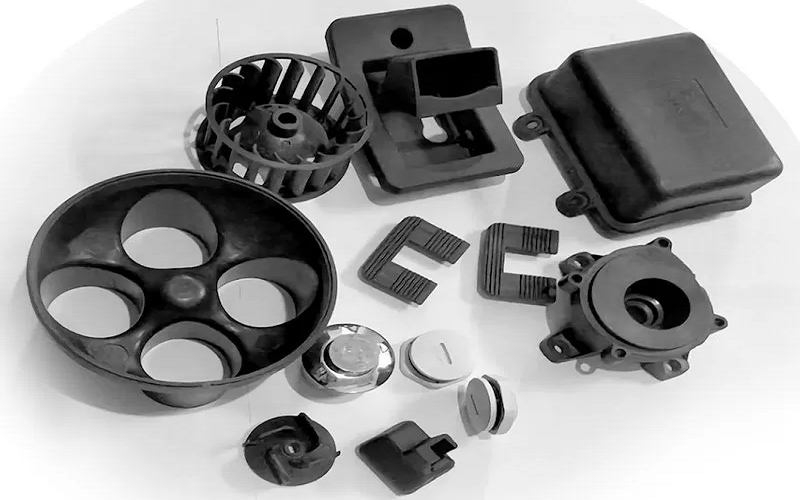
Is Nylon Safe?
PA plastic, commonly known as nylon, is inherently non-toxic. As a polymer material, its finished products are harmless to humans under normal usage conditions, making it widely applicable in both daily life and industrial settings.
So, Is Nylon safe? The answer largely depends on production and usage conditions. During the manufacturing process, small amounts of monomers (such as caprolactam) may remain.
If not fully removed, these residues could slowly release under high temperatures or prolonged use, potentially affecting human health by irritating the respiratory system or causing mild allergic reactions.
Therefore, producing high-quality PA products requires strict process controls to ensure residual monomer levels are reduced below safety thresholds, typically achieved through post-processing steps like thorough drying and extraction.
Additionally, to enhance safety, PA plastics are often formulated with flame retardants and stabilizers to improve fire resistance, which is particularly crucial in fields like electronics and automotive applications.
However, certain traditional additives (e.g., halogenated flame retardants) while effective at suppressing flames, may release toxic gases such as hydrogen chloride or dioxins during combustion, posing risks to both the environment and human health.
To address this, careful selection of eco-friendly formulations—such as halogen-free flame retardants or green additives based on phosphorus or nitrogen—is necessary to balance safety and environmental friendliness.
Through these measures, PA plastic can maximize performance while minimizing health risks, ensuring that the conclusion Nylon is safe holds true in practical applications.
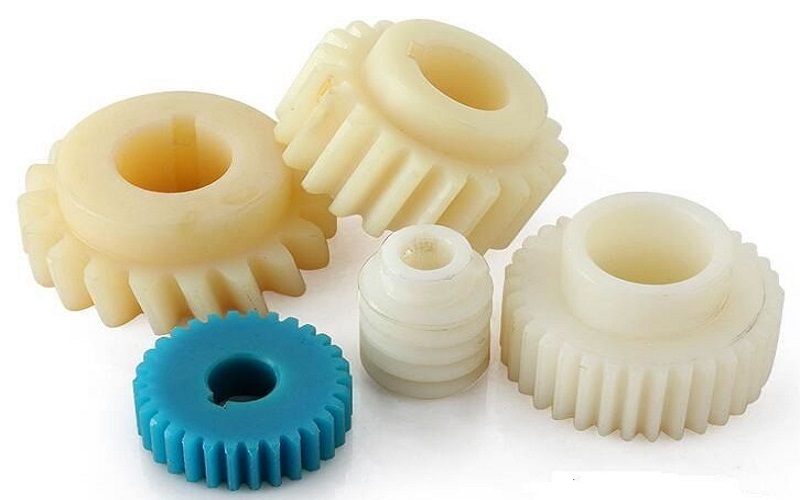
Recycling and Environmental Impact Of Polyamide Material
The production of PA plastics relies on petrochemical raw materials, which are non-renewable resources, and their manufacturing process generates a certain amount of carbon emissions and wastewater.
Additionally, PA plastics are not easily biodegradable, posing long-term environmental challenges if not properly managed.
However, recent advancements in recyclable PA and bio-based PA, such as PA11 derived from castor oil, have significantly improved their environmental footprint. Mechanical and chemical recycling methods allow PA plastics to be reprocessed into new products, reducing waste and conserving resources.
Designing products with disassembly and recyclability in mind can further minimize their ecological impact. As industries adopt more sustainable practices, the environmental benefits of PA plastics will continue to grow.
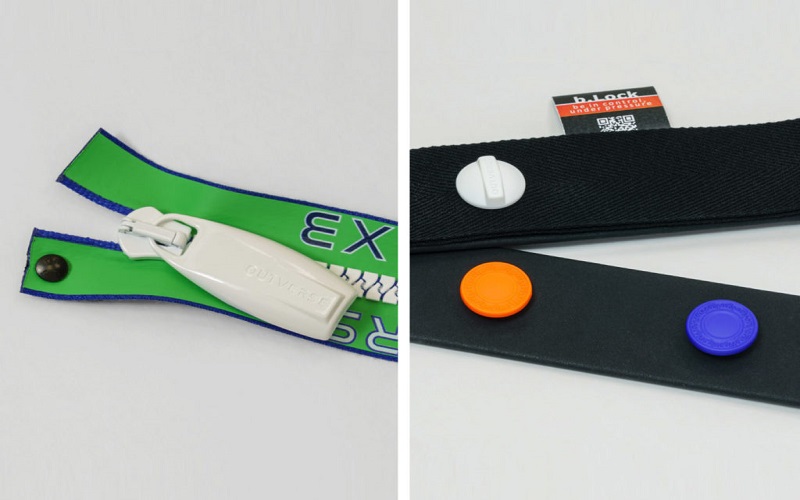
Applications of Polyamide Plastic Products
Below is an overview of the key applications of PA plastic products:
Automotive Industry
PA plastics are widely used for under-the-hood parts such as intake manifolds, engine covers, gears, bearings, and fuel system components (e.g., fuel lines and connectors).
High strength, heat resistance (up to 255°C for PA66), and resistance to oils and chemicals make them ideal for replacing metals, reducing vehicle weight and improving fuel efficiency.
Electrical and Electronics Industry
PA plastics are used in electrical connectors, cable ties, insulators, switches, and housings for electronic devices.
The material’s excellent electrical resistance and stability make it a go-to choice for insulating and protecting sensitive electrical components.
Industrial Machinery
Due to the non-toxic nature, lightweight, excellent mechanical strength, wear resistance, and good corrosion resistance of polyamides, they are widely used to replace metals like copper in the manufacturing of bearings, gears, pump blades, and other components in industries such as machinery, chemical, instrumentation, and automotive.
Textiles and Consumer Goods
Polyamide is widely utilized in consumer goods, showcasing its versatility through various applications. Common applications of polyamide in consumer products include textiles and sports equipment.
In the textile industry, polyamide is specifically used for producing a wide range of clothing and accessories. Its durability, flexibility, and comfort make it a preferred material for manufacturers and consumers alike.
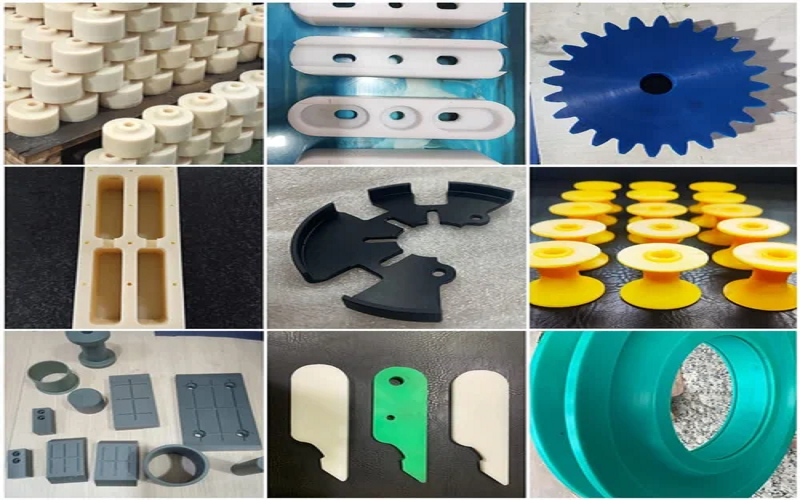
Future Trends and Innovations
Polyamides contribute significantly to microplastic pollution, accounting for a large percentage in various water bodies and sewage treatment plants. The lifecycle of polyamide materials indicates that they can persist in landfills for decades, leading to long-term environmental consequences.
There is increasing pressure to improve the recyclability and reduce the environmental impact of polyamides. Advancements in recycling technologies are influencing the future of polyamide development, emphasizing sustainability.
The shift towards lightweight materials in the automotive sector is intensifying the demand for advanced polyamides to enhance vehicle efficiency and performance. Despite challenges like high production costs and competition from alternative materials, continued innovation is essential for the growth of polyamide markets.
Summary
PA plastic, with its outstanding mechanical properties, thermal stability, and processing flexibility, plays an indispensable role in both industrial and daily life applications.
From automotive to textiles, electronics to medical fields, its wide range of uses is truly impressive. In terms of safety, PA plastic performs well under standardized production conditions, though attention must be paid to the health impacts of additive selection.
Regarding environmental impact, while it faces challenges due to its non-biodegradable nature, advancements in recycling technologies and bio-based materials offer new pathways for sustainable development.
Looking ahead, with the push toward green manufacturing and a circular economy, PA plastic is poised to achieve a better balance between performance and environmental responsibility, evolving into a safer, more eco-friendly high-performance material.
Through this introduction, it is believed that readers have gained a comprehensive understanding of PA plastic, enabling them to better grasp its advantages and limitations and make informed choices in practical applications.