Nylon 12, also known as Polyamide 12 (abbreviated as PA 12), is a robust thermoplastic polymer prepared through the polymerization of dodecanedioic acid and decanediamine.
As an important member of the nylon family, PA 12 began to emerge in the industrial sector in the mid-20th century. Its unique molecular structure endows it with excellent physical and chemical properties.
Compared to other common nylon materials (such as Nylon 6 and Nylon 66), Nylon 12 has a longer carbon chain, which makes it particularly outstanding in terms of water absorption, flexibility, and chemical resistance.
Since its inception, PA 12 has gradually become a key material in the field of engineering plastics due to its superior performance. It is widely used in various industries, including automotive manufacturing, medical devices, and consumer goods.
This article aims to provide a comprehensive introduction to this high-performance polymer, delving into its chemical and physical characteristics, production processes, broad application areas, and potential value.
Characteristics Of Nylon 12
Chemical Structure and Fundamental Properties
Nylon 12 is a semi-crystalline thermoplastic material synthesized through the linear polymerization of butadiene.
Its molecular structure is characterized by long-chain twelve-carbon units, which result in performance similarities to PA 11, though the two differ in their crystalline structures.
These differences in crystalline arrangement directly influence PA 12’s mechanical properties and processing behavior, providing it with distinct advantages in specific applications.
As an outstanding electrical insulator, PA 12 exhibits stable insulation performance even in humid conditions—a trait shared with most polyamides, attributable to the chemical stability of the amide groups within its molecular chain.
Mechanical Properties and Chemical Resistance
PA 12 boasts impressive mechanical properties, including good impact resistance, which enables it to withstand physical stress effectively.
PA 12 provides good chemical resistance to oils, greases, aliphatic hydrocarbons, and alkalies and is the optimal material for complex assemblies, housings, enclosures, and watertight applications. This makes PA 12 an excellent choice for producing final parts that require high durability and performance.
However, PA 12 is less chemical resistant to strong oxidizing acids, a limitation that requires careful consideration during material selection and application design.
Compared to widely used polyamides like PA 6 and PA 66, PA 12 offers a lower melting point and density, positioning it as an ideal candidate for lightweight design applications where weight reduction is a priority.
Nylon12 Properties Table | |
---|---|
Properties | Value |
Density(g/cm³) | 1.08 |
Melting Point(°C) | 175 – 180 |
Tensile Strength(MPa) | 40-50 |
Elongation at Break(%) | 200-300 |
Shrinkage(%) | 0.9 |
Water Absorption(%) | 0.7 – 1.5 |
Notched Impact Strength(kJ/m²) | 5-15 |
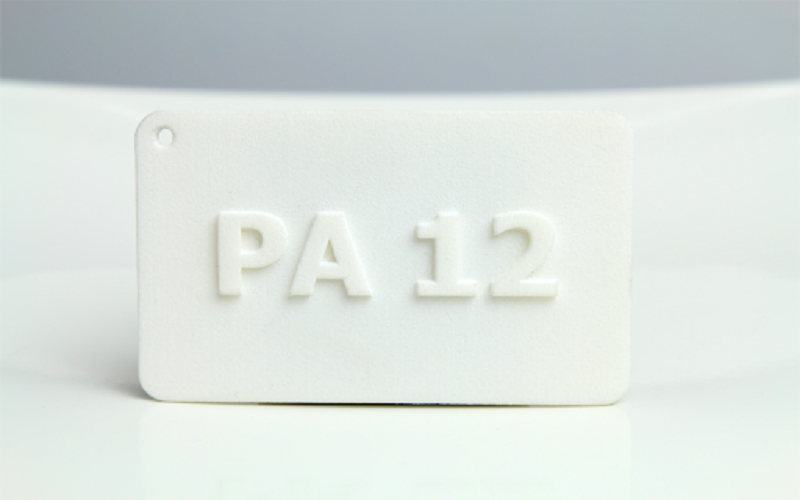
Different Applications Of Polyamide 12
PA 12 is a good general-use plastic with broad additive applications and is known for its toughness, tensile strength, impact strength and ability to flex without fracture.
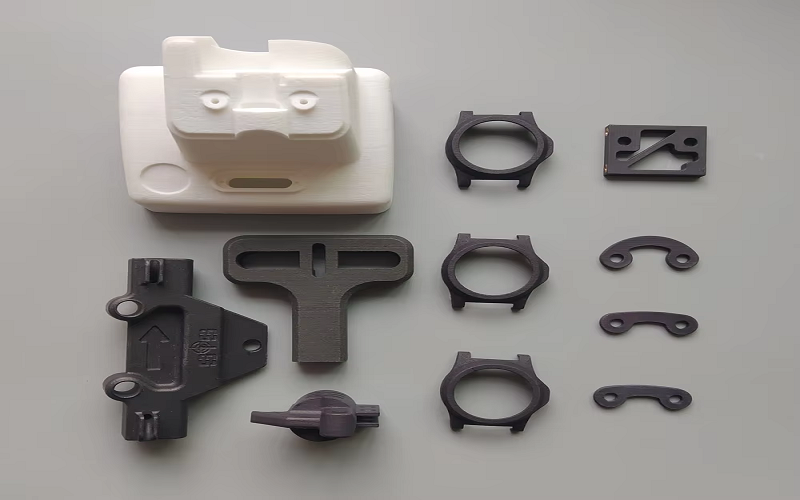
Industrial Manufacturing
Nylon 12 plays a crucial role in the field of industrial manufacturing, particularly excelling in the mechanical manufacturing and automotive industries.
Its low density and excellent chemical stability make it an ideal material for producing automotive components such as fuel lines, oil circuit connectors, and gears.
These parts need to withstand long-term exposure to fuels and lubricants, and the good chemical resistance of Nylon 12 ensures its reliability in harsh environments.
Additionally, the high toughness and impact resistance of Nylon 12 make it suitable for manufacturing mechanical components and tools, such as bearings, washers, and transmission parts, which must maintain stable performance under high loads and frequent use conditions.
Consumer Goods
In the consumer goods sector, Nylon 12 is widely used in sports equipment and household products due to its flexibility, durability, and low water absorption. For instance, in sports equipment, Nylon 12 is commonly employed in the production of ski boot liners and fishing lines.
The former leverages its flexibility and low-temperature resistance to provide comfort and durability, while the latter relies on its high tensile strength and wear resistance to withstand complex outdoor environments.
Additionally, PA 12 is utilized as a material for the casings of household appliances, such as vacuum cleaners or power tool shells. Its low water absorption ensures that the casings remain resistant to deformation in humid conditions, while its good surface finish and processing characteristics meet consumer demands for both aesthetics and practicality.
Medical Devices
In medical devices, PA 12 is frequently used to manufacture catheters and other flexible medical components.
Its softness and chemical resistance fulfill stringent hygiene and durability requirements, while its low water absorption minimizes performance changes due to moisture, ensuring the stability of medical equipment.
Additive Manufacturing For PA 12
More recently, PA 12 powder has been adopted as a common 3D printing material for creating functional parts and prototypes.
PA 12 is known for its fine feature resolution, which allows for the production of high-quality surface finishes and consistent mechanical properties.
Its excellent flowability and thermal stability make it highly suitable for nylon 3D printing manufacturing technologies such as selective laser sintering (SLS), where it excels in producing complex prototypes and complex parts, widely applied in research, development, and customized production.
Designs with thin walls can be achieved using PA 12, but it is important to maintain appropriate wall thickness to ensure structural integrity and avoid warping.
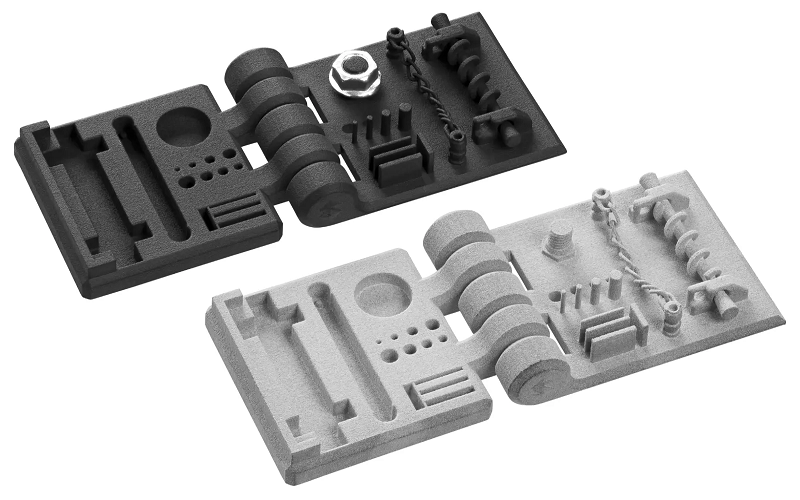
Cost Analysis For PA 12
From a raw material cost perspective, PA 12 incurs a significant expense due to its core components, phthalic acid and 12-aminododecanoic acid, which are prone to price volatility and demand complex synthesis processes.
This directly elevates the overall cost of PA 12. The raw material supply chain is closely tied to the global chemical market, where crude oil price fluctuations further amplify cost variability.
Moreover, PA 12’s production is both intricate and energy-intensive, involving multiple stages such as polymerization, spinning, and stretching. These processes necessitate specialized equipment, like high-temperature, high-pressure reactors, and precise control technologies.
Energy costs (e.g., electricity and steam) combined with labor expenses contribute over 30% to the total cost, with the need for meticulous process control adding further complexity.
Recent market data indicates that unreinforced PA 12 typically costs between $5 and $10 per kilogram in bulk, while reinforced grades (e.g., glass fiber-enhanced) or specialty variants (e.g., for 3D printing) range from $10 to over $20 per kilogram. High-purity or small-batch grades for medical applications can exceed $50 per kilogram.
Compared to PA 6 ($2-4/kg) and PA 66 ($3-5/kg), PA 12’s higher price reflects its longer carbon chain, lower production volume, and premium properties, such as low moisture absorption and flexibility—attributes that justify the cost in performance-critical applications.
Thus, we recommend manufacturers opt for polyamide 12 in high-volume applications where dimensional accuracy and low cost per part are priorities, leveraging its superior properties to achieve cost-effective outcomes.
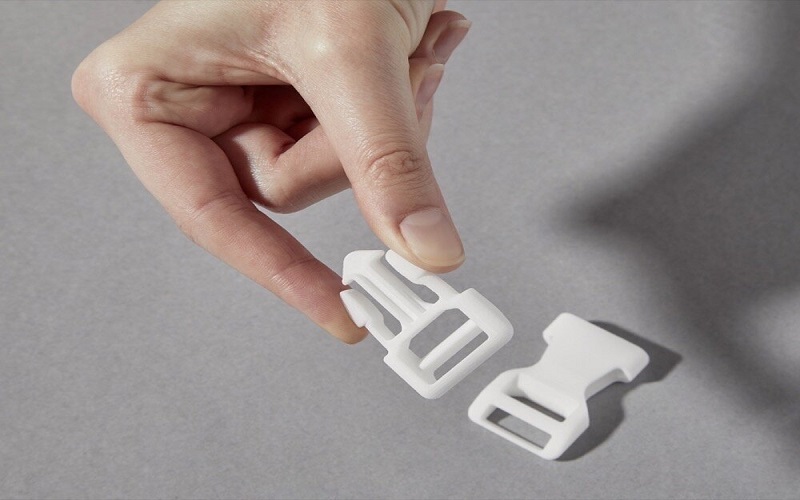
How To Choose Between PA 11 And PA 12?
In practical applications, the choice between PA 11 and PA 12 depends on the specific requirements of the application and the desired material properties.
Both are high-performance polyamides with similar characteristics, such as low water absorption and excellent chemical resistance, but they differ in key aspects.
PA 11, derived from renewable castor oil, offers superior flexibility and impact resistance, making it ideal for applications like flexible tubing or sports equipment where elasticity is critical.
In contrast, PA 12, typically synthesized from petrochemical sources, provides slightly better dimensional stability and lower moisture sensitivity due to its distinct crystalline structure, which suits high quality components like automotive fuel lines or 3D-printed parts.
Cost also plays a role—PA 11 often carries a premium due to its bio-based origin, while PA 12 may be reduce production costs for large-scale production.
Ultimately, the decision hinges on balancing performance needs, environmental considerations, and budget constraints specific to each use case.
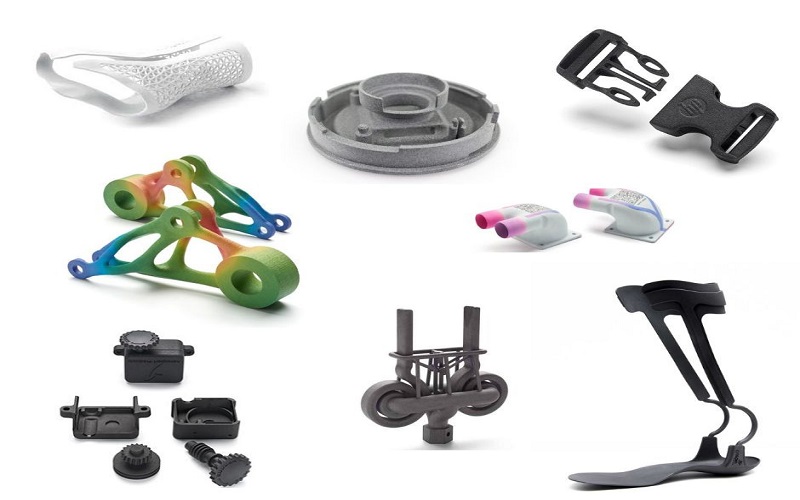
Conclusion
PA 12 is the most widely used long-chain nylon, combining the general properties of typical nylons with distinctive advantages such as low water absorption, high dimensional stability, resistance to high temperatures and corrosion, excellent toughness, and ease of processing.
Compared to another long-chain nylon-PA 11, PA 12 benefits from a significant cost advantage—its raw material, butadiene, costs only one-third as much as PA 11’s castor oil—allowing it to replace PA 11 in most applications, including automotive fuel lines, pneumatic brake hoses, underwater cables, and 3D printing.
Furthermore, PA 12 powder offers exceptional characteristics like high flowability, low static electricity, moderate melting point, and high dimensional accuracy in finished products, while its fatigue resistance and toughness meet the demands of components requiring superior mechanical performance.
As a result, Nylon 12 has emerged as an ideal material for 3D printing in engineering plastics, underscoring its outstanding versatility and value across industrial and cutting-edge technological applications.