In the field of modern materials science and engineering, PA 11 as a unique thermoplastic polymer, has garnered significant attention due to its exceptional performance and environmentally friendly characteristics.
Unlike traditional petroleum-based nylons, nylon 11 is derived from a renewable resource—castor oil—which not only endows it with the advantage of sustainability but also enables it to exhibit excellent mechanical properties and durability across a wide range of applications.
This article will delve into the characteristics, applications, and differences between PA11 Nylon and other nylon materials.
What Is PA 11?
PA 11, also known as Polyamide 11 or Nylon 11, is a high-performance thermoplastic polymer synthesized from ω-aminoundecanoic acid.
Belonging to the nylon family, Polyamide 11 is renowned for its excellent mechanical performance, durability, and sustainability.
Unlike many other polyamide materials, PA 11 is predominantly made from renewable resources like castor oil, classifying it as a bio-based polyamide. This eco-friendly origin reduces dependency on non-renewable petroleum resources, making it a greener alternative in the world of polymers.
The unique composition of Polyamide 11 sets it apart within the nylon family. Its synthesis from castor oil not only contributes to its sustainability but also enhances its mechanical properties, including high elongation. This combination of environmental consciousness and high performance makes PA 11 a standout material in numerous industries.
Further exploration uncovers the specific properties that make nylon 11 versatile and valuable.
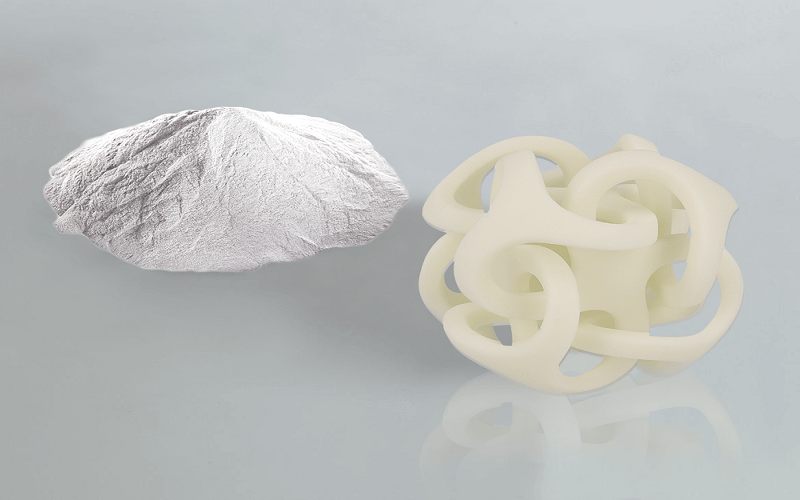
Key Properties of Nylon 11
Polyamide 11 is a semi-crystalline polymer that exhibits outstanding physical and chemical properties.
Its tensile strength ranges between 47-58 MPa, showcasing excellent toughness and impact resistance.
Compared to other types of nylon, PA 11 is notably more flexible and has lower water absorption, ensuring stable performance even in humid environments. This makes it an ideal choice for applications requiring consistent performance under varying conditions.
Another remarkable property of polyamide 11 is its resistance to chemicals, UV radiation, and extreme weather conditions. This resilience makes it suitable for outdoor applications and harsh environments. Additionally, PA 11 is lightweight, with a density of approximately 1.04 g/cm³, providing a significant advantage in applications where weight reduction is crucial.
Its thermal stability is also noteworthy, with a melting point between 185-190°C, making it suitable for various processing methods.
The combination of these properties—dimensional stability, high ductility, low water absorption, and high impact resistance—positions polyamide 11 as a durable and reliable material suited to numerous applications. Its ability to maintain performance in challenging conditions underscores its versatility and superiority within the nylon family.
Nylon11 Parameters Table | |
Properties | Value |
Density(g/cm³) | 1.04-1.05 |
Tensile Strength(MPa) | 47-58 |
Elongation at break(%) | 300 – 350 |
Melting Point(°C) | 185-190 |
Glass Transition Temp (°C) | 45-50 |
Water Absorption(%) | 1.5-1.9 |
Impact Strength(kJ/m²) | 10-15 |
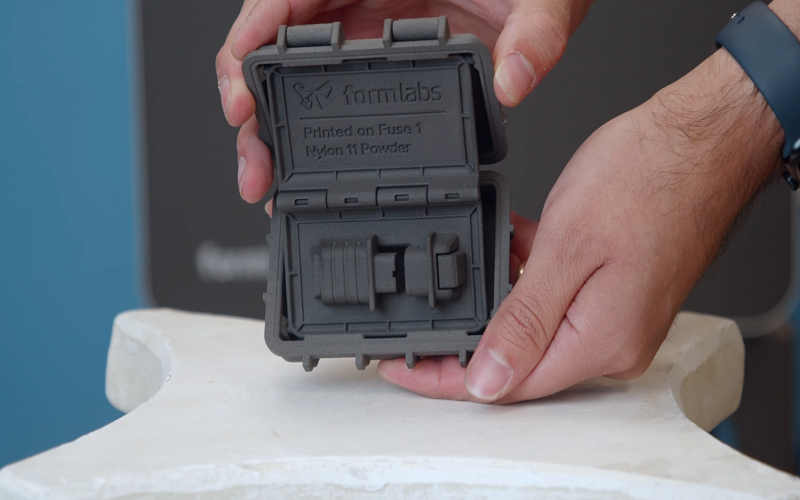
Applications Of PA 11 Products
Polyamide 11 products are gaining traction across diverse industrial applications due to their sustainable properties and durability.
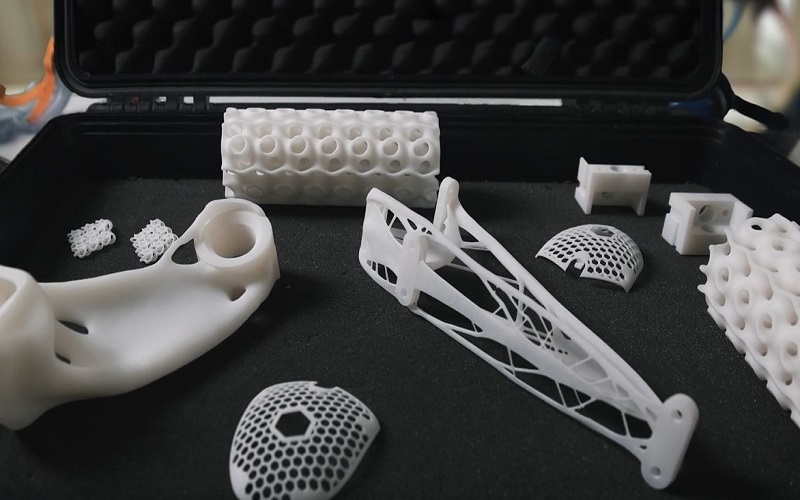
Automotive Sector
In the automotive industry, PA 11 is celebrated for its lightweight and durable characteristics. These properties are critical for manufacturing functional parts such as fuel lines and air brake tubing, which require both robustness and flexibility. The material’s resistance to corrosion and fatigue cracking ensures longevity and reliability in demanding automotive applications.
Utilizing PA 11 in automotive components allows manufacturers to achieve significant weight reduction without compromising performance. This not only enhances vehicle efficiency but also contributes to overall fuel economy. The ability to withstand harsh automotive environments, combined with its ease of processing through methods like nylon injection molding, makes PA 11 a valuable material in the automotive sector.
Electronics Industry
Nylon 11 plays a pivotal role in the electronics industry due to its excellent resistance to electric arcs and electrolytic corrosion.
These properties are essential for enhancing the reliability and lifespan of wire and cable insulation. Using Nylon 11 as an insulating material significantly reduces the risk of electrical breakdown, ensuring safer and more durable electronic systems.
Moreover, PA 11 is used in protecting submarine optical cables, reducing signal loss during transmission. This application is crucial in maintaining the integrity of communications and data transfer in underwater environments. The material’s ability to withstand harsh conditions without degrading ensures long-lasting performance in critical electronic applications.
Oil & Gas Industry
In the exploration and transportation of oil and gas, pipeline materials must withstand chemical corrosion and extreme environmental pressures. PA11 nylon, with its excellent chemical resistance and flexibility, is often the preferred material for deep-sea hoses and corrosion-resistant pipelines. It can resist the erosion of hydrocarbons and saltwater, ensuring long-term reliability, while its high strength guarantees safety in high-pressure environments.
Military Equipment
In military applications, Polyamide 11’s versatility and resilience to extreme environmental conditions make it an ideal material for various equipment. From gun stocks and grips to trigger guards and parachute covers, nylon 11 can withstand moisture, arid conditions, extreme cold (below -40°C), and high heat (up to 70°C).
The material’s ability to endure such harsh conditions without compromising performance ensures the reliability and effectiveness of military equipment. Its high impact strength and durability are crucial for the demanding requirements of military use, providing protection and reliability in the field.
Consumer Goods
PA11 powder exhibits excellent meltability, adhesion, and coating uniformity, making it a widely adopted material in the garment industry across regions such as Europe, the United States, and Japan.
Additionally, PA11 boasts superior film-forming properties, rendering it an ideal choice for sausage casings. These casings offer numerous advantages, including non-toxicity, high strength, abrasion resistance, and low breathability.
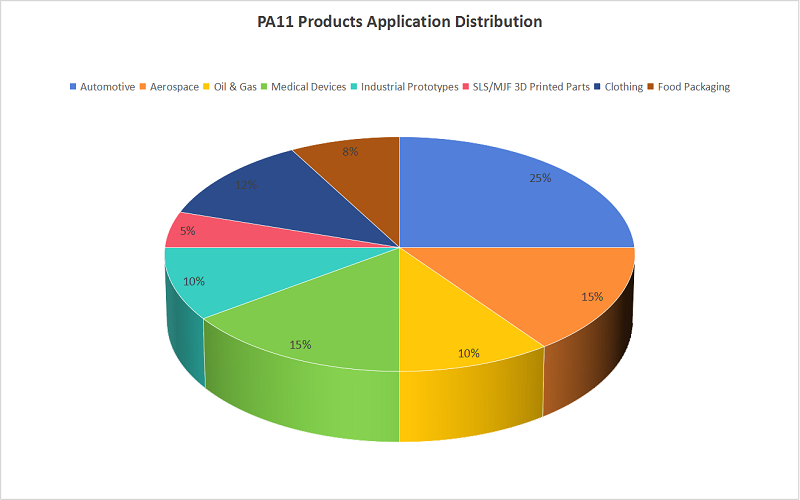
Environmental Impact Of PA 11 Material
Nylon 11’s primary raw material, castor oil, is a renewable resource, giving it a significant environmental advantage over petroleum-based alternatives. This bio-based origin reduces reliance on non-renewable resources and aligns with sustainable development goals. However, the stability of castor oil supply can impact nylon 11’s production and cost.
Nylon 11 is not only eco-friendly in its production but also in its lifecycle. The material is recyclable, allowing for recovery and reuse at the end of its lifecycle. This recyclability, combined with its high performance at elevated temperatures, makes nylon 11 a sustainable choice for various applications, contributing to a reduced carbon footprint and promoting environmental sustainability.
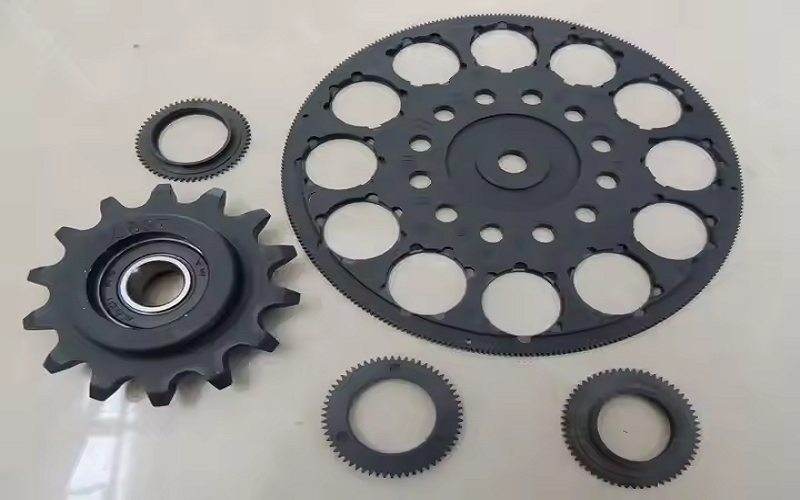
PA11 vs PA12: What Are the Differences?
When comparing PA 11 and PA 12, several distinct differences come to light. PA11, sourced from renewable castor oil, stands out as a more environmentally sustainable option than PA12, which is derived from petroleum-based materials.
This bio-based nature of PA 11, while enhancing its eco-friendliness, also results in a higher production cost compared to PA 12.
Mechanically, PA 11 delivers impressive tensile strength and impact resistance, often matching or surpassing that of traditional nylons.
In contrast, PA 12 boasts superior thermal stability, enabling it to endure higher temperatures, whereas PA 11 shines in colder environments and offers exceptional resistance to UV radiation and weathering.
Additionally, nylon 11’s smoother surface finish lends it a more polished and aesthetically appealing look, making it a preferred choice for applications where visual appeal matters.
In terms of chemical resistance, nylon 11 outperforms nylon 12 by withstanding a wider array of substances, broadening its suitability across diverse applications.
However, PA12 holds an advantage in high-stress scenarios due to its greater strength and resistance to stress cracking. Recognizing these distinctions is key to selecting the most suitable material for specific use cases.
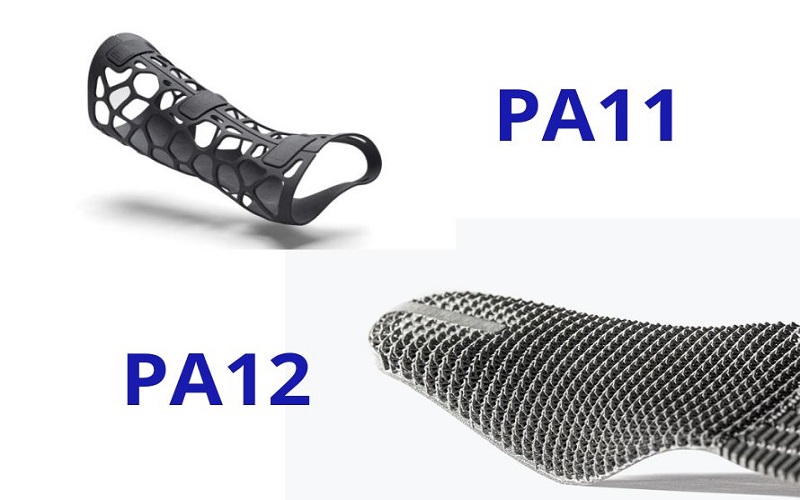
Advances Technology Of PA 11 Material
Derived from renewable castor oil, PA11 stands out as a bio-based alternative to petroleum-derived polymers like PA12. In recent years, technological advancements in PA11 have focused on enhancing its production efficiency, material performance, and applicability across cutting-edge industries.
These innovations ensure that PA11 remains a high-performing, eco-friendly material capable of meeting the evolving demands of modern engineering and manufacturing.
PA11 Polymer Powder For 3D Printing
PA11 powder excels in nylon 3D printing technology, particularly with materials like Ultrasint® PA11. This material, derived from castor oil, boasts 100% bio-based properties, making it environmentally friendly and renewable.
Products 3D printed with PA11 feature a uniform surface and a smooth texture, making them particularly suitable for manufacturing parts that endure high mechanical stress, such as hinges, automotive interior components, and external fender structures.
Additionally, Ultrasint® PA11 ESD is a PA11 powder capable of achieving electrostatic discharge, making it ideal for producing anti-static prototypes and small batch components, ensuring safety during the application process.
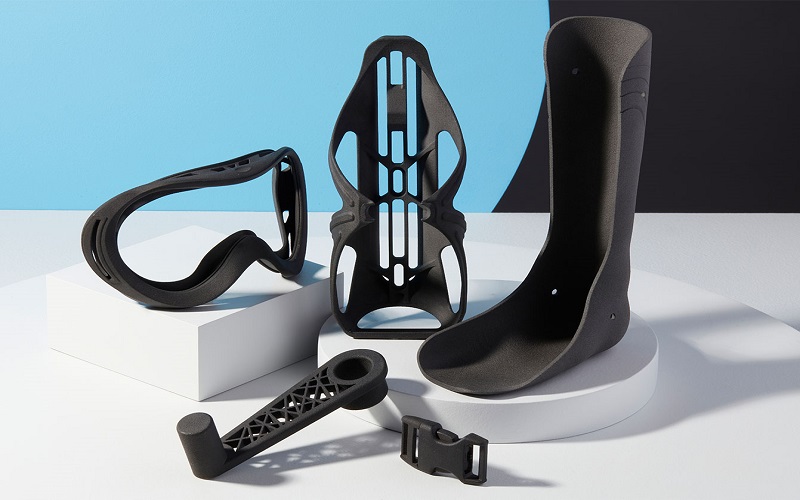
Technical Modification
Through the development of advanced compounding techniques, manufacturers have introduced reinforced PA11 variants by blending it with additives like glass fibers, carbon fibers, or nanoparticles. These reinforcements boost tensile strength, stiffness, and thermal resistance, expanding PA11’s suitability for high-performance applications.
For example, carbon-fiber-reinforced PA11 can achieve tensile strengths exceeding 70 MPa, rivaling some metal alloys while retaining its lightweight advantage.
Surface modification techniques, such as plasma treatment or chemical grafting, have further improved PA11’s chemical resistance and adhesion properties. These enhancements make it more compatible with coatings, adhesives, and composite structures, broadening its use in industries like oil and gas, where durable, corrosion-resistant materials are critical.
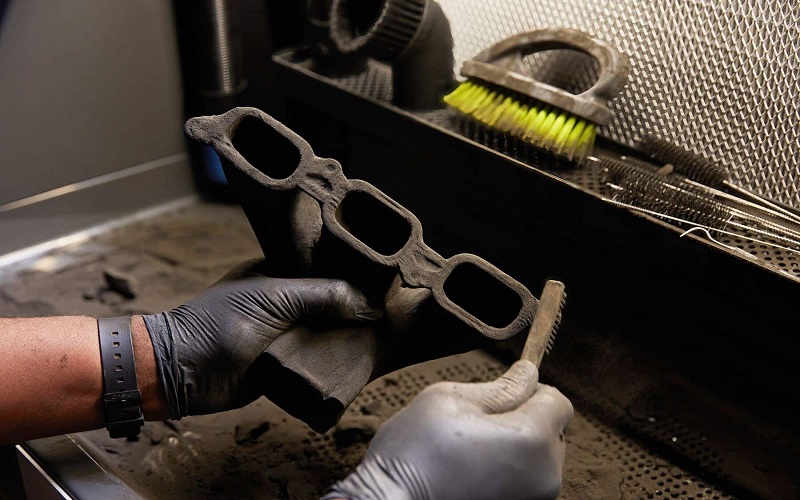
Summary
PA 11 stands out as a high-performance, sustainable material with a wide range of applications across various industries. Its unique properties, such as high tensile strength, flexibility, and chemical resistance, make it a valuable choice for demanding environments. The comparison with PA 12 highlights Polyamide 11’s environmental benefits and its suitability for specific applications.
As technology advances, nylon 11 continues to evolve, offering improved efficiency and performance. For businesses looking to incorporate sustainable and high-performing materials, PA 11 presents a compelling option. Embracing Polyamide 11 not only supports environmental sustainability but also ensures the reliability and durability of the products. The future of nylon 11 looks promising, with continued innovations and applications on the horizon.