For over a century and a half, injection molding has been the go-to process for manufacturers around the world. The traditional methods of injection molding have with time, metamorphosed into several modern practices that arose as a result of the need to fill in the gaps in areas where the former fell short.
In this article, we will take a clear, concise, and close examination of one of these modern injection molding practices called the over-mold process. Read on to get a complete understanding of what it entails.
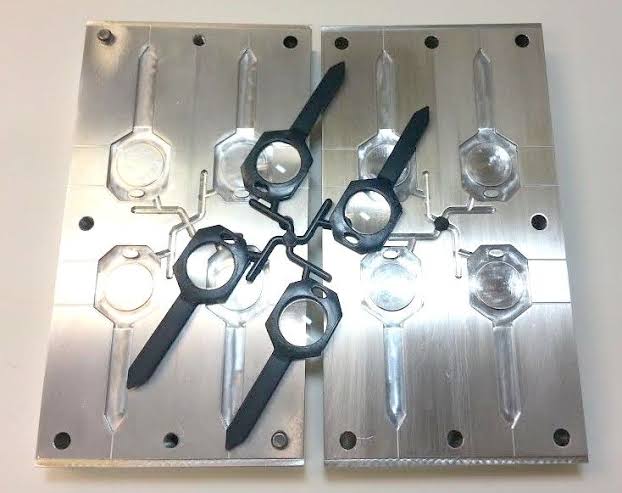
Brief Overview of the Overmolding Process
As a manufacturer, you might be faced with dilemmas like deciding whether to glue or screw parts together to create a single piece, or to employ the over-molding process. In this section, we detail the over-molding process and its benefits.
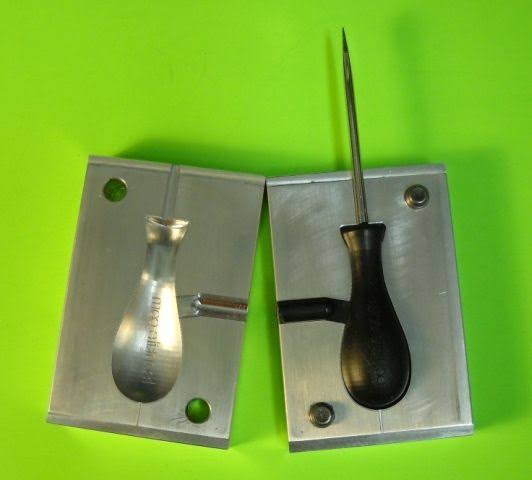
What is Overmolding?
Overmolding is commonly referred to as one of the most user-efficient and reliable injection molding processes in manufacturing. It involves the formation of single-piece parts from two or more components.
Often also called “in-mold assembly,” over-molding is used to mold plastics such as TPE over another substrate. This injection over-molding process involves the use of both plastic and non-plastic material.
The over-molding process encapsulates two other methods, these are:
- Insert Molding
- Two-Shot (also multiple shot or double shot) molding
Insert molding involves the introduction of a metal material to plastic parts during the injection molding process. On the other hand, two-shot molding is the process of creating plastic components from different materials.
Benefits of the Overmolding Process
The over-molding process is an industry favorite for several reasons, as it presents manufacturers with multiple benefits. Some pros of the over-molding process are highlighted below:
- Improve Product Functions and Performances
Overmolding gives you the advantage to enjoy some features that might not be present in other processes. Some of these special functions and performances include waterproofing, protection from corrosive chemicals, anti-UV, and electrical insulation for adequate protection against the discharge of electricity.
Overmolding is also ideal as it enables noise elimination and reduction of vibration.
- Add Multiple Colors or Textures
One major benefit of the over-molding process is that it allows manufacturers to join two uniquely distinct plastic resins to make a single part. This results in a rigid plastic part that soft silicone grips can be over-molded on, allowing end users to have a handle to hold on to.
Plastic over-molding gives you the ability to join two different textures and colors of plastic resin to give the product an even more aesthetic look. It also lets you get creative and make relevant products for your prospective customers.
- Increased Durability with a Protective Layer
Using two or more materials to form a single part helps to increase the durability of the end product as the extra components serve as a protective layer.
Overmolding helps to create a resilient product with enhanced fortification techniques, which protects it against wear and tear. The advanced blend of precision engineering in the over-molding process gives manufactured goods increased durability.
What is the Process of Overmolding?
Having discussed over-molding and its benefits to the manufacturing industry, it is pertinent to look at the processes involved in the over-molding technique.
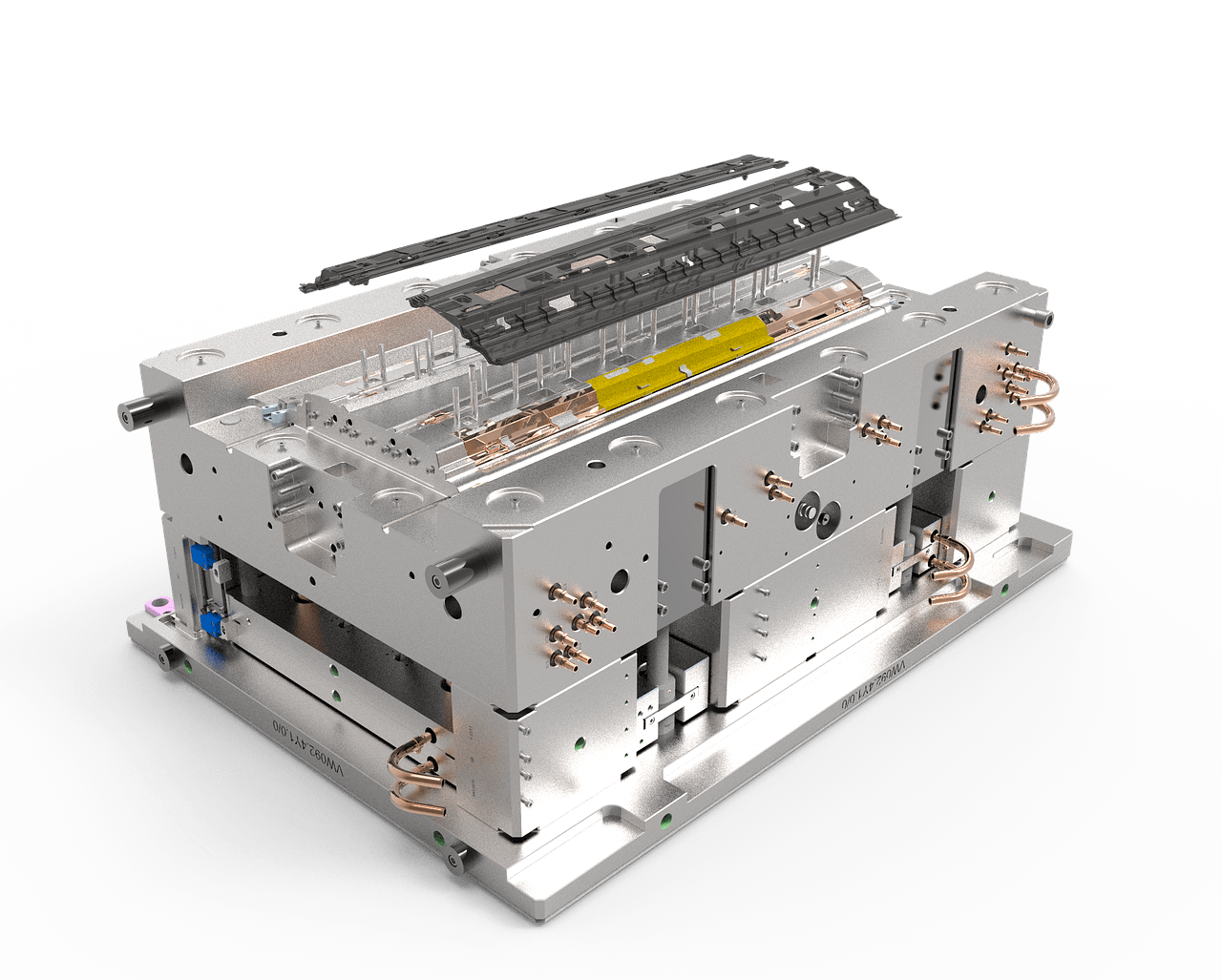
Design the Mold and Product
The first step of the over-mold process is mold and product design. The intended product should first of all be designed with emphasis on both the base and the secondary materials that are being overmolded.
Looking at how complex over-molded parts can be, several factors will also need to be put into consideration before designing. Some of these factors include functionality, compatibility of materials, and more importantly, the entire aesthetics of the end product.
It is recommended to make CAD designs or 3D models that would serve as guides for the process of over-molding.
Pre-Molding
The next over-molding process is pre-molding. Pre-molding is the procedure during over-molding that involves using a preformed insert to create the end over the mold part. The pre-mold insert step happens even before the main over-molding techniques are executed.
Usually, the pre-mold is made from the same (or almost the same) material as the secondary material. During pre-molding, a separate process of molding like compression molding and injection molding is used to form the desired end product shape.
Select Compatible Materials
There are numerous materials that can be explored for plastic over-molding, such as HDPE, acetal, TPE, Ionomer, PVC, CPVC, TPV, and so on. However, due to their difference in components, these materials typically have different features and benefits.
Highlighted below are some other factors that should be considered when selecting compatible materials:
- The thickness of the Materials: It is not unusual for the thickness properties of a material to affect how effective the material is. When using TPE with a thick wall section, its properties have the ability to take in more vibration, therefore, giving it a softer feel.
- Bonding: An important compatibility check to look out for is the bonding capabilities of the materials. When over-molded, some materials tend to bond together more than others, while some materials like PVDF, PP, and PE are difficult to bond together.
- Compression Properties: TPE plastic is one of the most used materials due to how flexible it is. It is necessary to use an adjoining material that can be compressed as much as TPE without causing any permanent damage to it.
- Temperature: The substrate material that will be introduced should be able to withstand as much pressure as the over-molded plastic. It should not lose its form or get damaged when placed under the heat.
Overmolding Process
It involves placing the pre-molded base part which was already molded separately, back into the mold. Inject the over mold material into the surrounding cavity. Apply high pressure for proper adhesion and bonding.
Cooling, Ejection, and Post-Processing
Following the over-molding process, the next step is cooling, ejection, and post-processing.
The time it takes to cool a mold varies from material to material and also the size of the parts. Using a controlled cooling process is ideal as it ensures accurate dimensions.
For ejecting the over-molded part, manual extraction is used, or automated ejection systems to make the removal faster and easier. And the post-processing steps include sanding rough edges and trimming excess material. Post-processing is necessary to give the product the ideal aesthetics and functionality.
What is Overmolding Used for?
Overmolding is embraced by almost every industry as the process offers quite a number of advantages.
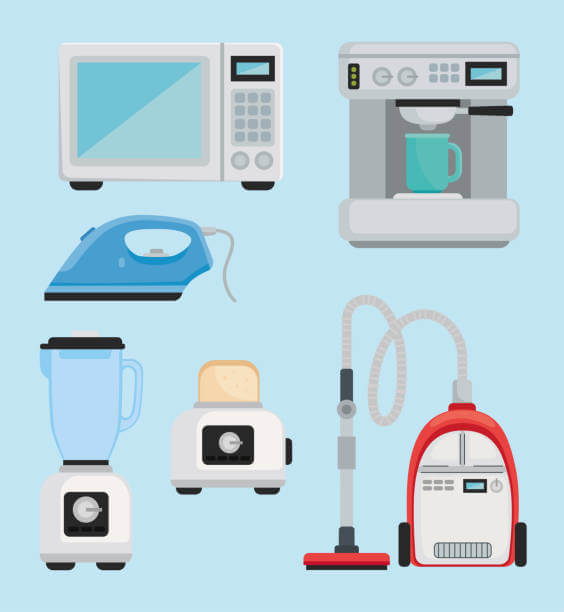
Produce Automotive Components
Overmolding is used to produce components for car parts. Manufacturers in the automotive industry employ this process to eliminate the need for adhesives in assembling components together.
Examples of automotive components that over-molding is used to produce include plastic over-molding engine parts, dashboards, card door locks, etc.
Manufacture Medical Devices
Overmolding helps to simplify the production of medical devices, no matter how sophisticated they might be.
Common medical devices made with this process include defibrillators, insulin pens, infusion pumps, blood pressure monitors, etc.
Make Protective Casing
One of the best measures to take in the protection of electrical and electronic devices is over-molding. The over-molding process makes functionality its primary advantage while not ignoring aesthetics and reliability, which makes it suitable for protective casing.
Protective casing made with over-molding is very beneficial to the end users as it gives the products increased grip, ensuring that users can hold and handle the objects or equipment securely.
Leading Provider of Overmolding Manufacturing
When in need of over-molding services, whatever the use application is, it is most important to pick out a reputable manufacturer that offers prototyping and cost-effective services. FOW Mould is an industry leader and innovator in the manufacturing of over molds.
Rapid Prototyping
FOW Mould uses rapid prototyping to quickly carry out the initial design of your choice product during the development process.
Rapid prototyping gives you a very realistic depiction of the mold, allowing for it to be tested and analyzed, then improved upon, before mass production. This process helps to save cost, and time, and ensure only the best quality is produced.
Cost-Effectiveness
With FOW Mould’s top-of-the-line 3D printers, CNC machines, and an expert team of engineers, you get your molded parts fast at low costs.
Also, you would have access to a broad range of injection over-molding procedures at highly competitive prices, which are not offered anywhere else for that same quality and price.
Conclusion
To sum everything up, we can conclude that over-molding injection molding bears numerous advantages for different user applications. Overmolding provides features such as electrical insulation, waterproofing, and noise reduction, and improves product performance.
Reach out to us at FOW Mould for every of your molding needs. Our professional team of expert engineers will see that you get the best quality products and efficient production processes.