In the world of manufacturing, achieving the perfect blend of precision and efficiency is essential, especially for industries where detail and consistency are paramount.
Motion control technology has become a cornerstone in modern injection molding, allowing manufacturers to produce high-quality, repeatable parts with minimal waste.
This article delves into the crucial role motion control plays in injection molding, exploring its benefits, components, types, and how it elevates quality standards across production lines.
Why is Motion Control Critical in Injection Molding?
In injection molding, motion control systems are integral to achieving consistent product quality and operational efficiency.
This technology allows manufacturers to execute precise movements in various stages of the molding process, ensuring each cycle produces parts that meet strict dimensional tolerances and aesthetic standards.
Without motion control, maintaining consistency and meeting the demands of high-quality production would be challenging.
Benefits of Motion Control in Injection Molding:
- Precision in part dimensions: Ensures each product meets exact specifications, reducing the likelihood of defects.
- Reduced waste: Minimizes material waste by optimizing movements and reducing trial-and-error during production.
- Enhanced production speed: Increases cycle efficiency, allowing for faster production without compromising quality.
- Improved repeatability: Maintains consistency across multiple cycles, ensuring every part produced aligns with the initial design specifications.
What is Motion Control in the Context of Injection Molding?
Motion control in injection molding refers to the use of automated technology that manages and optimizes the movements within a molding machine.
It encompasses a range of components and processes, such as positioning, velocity, and pressure control, which all contribute to accurate and repeatable movements essential for high-quality production.
Primary Aspects of Motion Control in Injection Molding:
- Positioning accuracy: Controls precise movements, ensuring molds close and open at exact points.
- Velocity control: Regulates speed to optimize cycle times and maintain consistent flow rates.
- Pressure management: Ensures correct pressure is applied during different phases, critical for achieving uniform part density and surface finish.
What are the Main Components of Motion Control Systems in Injection Molding Machines?
Motion control systems in injection molding machines rely on various components that work together to regulate movements accurately.
These components play specific roles in achieving precision and are essential for the overall performance and reliability of the molding process.
Key Components of Motion Control Systems:
- Servo motors: Drive the movements with precision, controlling the mold’s position, speed, and torque. Servo motor drives by Advanced Motion Controlsoffer industry-leading accuracy and responsiveness, ensuring consistent performance and fine control in even the most demanding molding applications.
- Sensors: Monitor real-time parameters, providing feedback on pressure, position, and speed for adjustments.
- Controllers: Act as the brain of the system, coordinating inputs from sensors and directing the actuators and servo motors.
- Actuators: Execute controlled movements, translating signals from controllers into mechanical actions.
- Feedback mechanisms: Continuously collect data to ensure the system is functioning within specified tolerances and make real-time adjustments.
How Does Motion Control Enhance Precision in Injection Molding?
Precision is essential in injection molding, where even minor deviations can lead to defects or wasted material.
Motion control systems enhance precision by regulating movements, ensuring every part of the mold operates within a narrow range of tolerance.
Through precise control over positioning and velocity, manufacturers can create components that meet exact specifications.
What Are Positioning and Velocity Tolerances in Motion Control?
Motion control systems enable high positioning and velocity tolerances, which are crucial for the integrity and quality of molded parts.
Typical Tolerances Achieved with Motion Control:
- Positioning tolerance: Often within ±0.01 mm, depending on the application and machine specifications.
- Velocity tolerance: Controlled to ensure uniform filling and minimize defects in the final product, with tolerances tailored to specific cycle requirements.
What Role Does Motion Control Play in Consistency and Repeatability?
Consistency and repeatability are crucial factors in injection molding, as they ensure that every product in a batch meets the same quality standards.
Motion control systems excel in maintaining these parameters by executing precisely controlled movements in every cycle.
This control over movement not only improves product uniformity but also minimizes variations that could lead to quality issues.
Enhanced repeatability means fewer rejected parts and a more reliable manufacturing process.
In recent years, data from manufacturers implementing motion control have shown significant improvements in repeatability.
For instance, studies indicate that injection molding machines equipped with advanced motion control can achieve repeatability levels within ±0.01% in part dimensions across thousands of cycles.
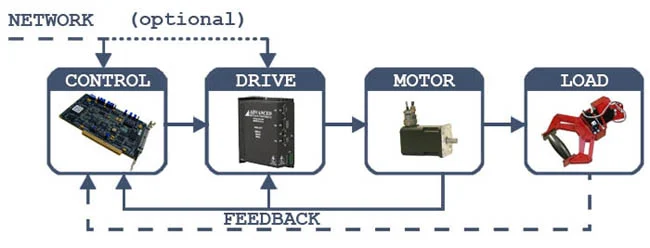
How Does Motion Control Improve Efficiency in Injection Molding?
Beyond quality and consistency, motion control systems greatly enhance the efficiency of injection molding processes.
By optimizing movements and cycle times, these systems reduce overall production costs and enable faster throughput without compromising on quality.
This combination of precision and speed is essential in industries where time and cost-efficiency are paramount.
Main Efficiency Factors Enhanced by Motion Control:
- Energy savings: By reducing unnecessary movements, motion control systems contribute to significant energy savings in high-volume production.
- Cycle time reduction: Faster, more efficient movements lead to shorter cycles, which allows for a higher output rate.
- Reduced material usage: With precise control, material waste is minimized, as fewer defective parts are produced, and less trial-and-error is required during production setup.
What are the Types of Motion Control Technologies Used in Injection Molding?
Motion control technologies can vary in complexity and application, each offering distinct advantages and limitations.
The choice of technology depends on the specific requirements of the injection molding process and the desired balance between cost, precision, and speed.
Electric Motion Control
Electric motion control systems rely on electric servo drives and motors to manage movements with high accuracy.
This type of motion control is especially favored for its precision, clean operation, and energy efficiency.
Pros of Electric Motion Control:
- High positioning accuracy, ideal for complex or delicate parts.
- Reduced energy consumption, as motors only run during active movements.
- Cleaner and quieter operation, beneficial in industries like medical and electronics manufacturing.
Cons of Electric Motion Control:
- Higher initial cost compared to hydraulic systems.
- Limited in terms of force output, which can be restrictive for certain high-force applications.
Hydraulic Motion Control
Hydraulic systems use fluid pressure to control movements and are widely known for their powerful performance and reliability in heavy-duty applications.
Pros of Hydraulic Motion Control:
- High force capability, making it suitable for large or complex molds.
- Robust performance under demanding operating conditions.
- Lower initial costs compared to electric systems.
Cons of Hydraulic Motion Control:
- Higher energy consumption due to continuous running.
- Requires more maintenance, including regular oil changes and monitoring of seals.
Hybrid Motion Control
Hybrid systems combine electric and hydraulic motion control, capitalizing on the strengths of each technology while mitigating their respective limitations. This system is often chosen for applications that require both high precision and high force.
Advantages of Hybrid Motion Control:
- Optimized energy efficiency, as electric drives are used for precision while hydraulics provide force.
- Versatile, accommodating a broader range of production requirements.
- Balance between cost-effectiveness and functionality.
Limitations of Hybrid Motion Control:
- More complex maintenance due to the integration of both electric and hydraulic components.
- Higher cost than purely hydraulic systems.
How Does Closed-Loop Control Enhance Injection Molding Precision?
Closed-loop control systems take motion control to the next level by constantly monitoring performance and making real-time adjustments to maintain precision.
Unlike open-loop systems, which operate without feedback, closed-loop control allows for immediate correction of any deviation, ensuring high accuracy in each cycle.
Advantages of Closed-Loop Control:
- Real-time error correction: Detects and corrects deviations instantly, enhancing part accuracy.
- Enhanced precision: Consistently meets tight tolerances, reducing defects.
- Improved part quality: Ensures consistent output with minimal variation, ideal for high-precision applications.
What are the Different Phases of Injection Molding Affected by Motion Control?
Motion control impacts several critical phases of the injection molding process, with each phase requiring specific movement control for optimal outcomes.
Phases of Injection Molding and Motion Control’s Role:
- Injection: Controls the material flow and filling speed, critical for avoiding defects.
- Packing: Manages pressure to maintain density and reduce shrinkage, ensuring dimensional stability.
- Cooling: Ensures consistent cooling rates to prevent warping or dimensional changes.
- Ejection: Facilitates smooth removal of parts from the mold without causing damage.
Injection Phase
During the injection phase, motion control systems precisely regulate the material flow into the mold cavity. This level of control is crucial for achieving a uniform fill, which minimizes the risk of voids or surface defects.
Packing Phase
In the packing phase, pressure control is vital. Motion control systems maintain consistent pressure to compact the material, enhancing part density and minimizing shrinkage, which is essential for maintaining tight dimensional tolerances.
Cooling Phase
Motion control’s role in cooling involves maintaining a steady rate of temperature decrease. Consistent cooling prevents warping and ensures dimensional stability, which is especially important for parts with complex geometries.
Ejection Phase
Precision in the ejection phase prevents deformation or damage as parts are removed from the mold. Motion control systems guide the ejection pins with care, ensuring each piece retains its intended shape and surface quality.
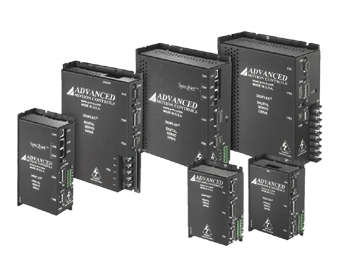
How Does Motion Control Contribute to Quality Control in Injection Molding?
Quality control is a top priority in injection molding, and motion control systems contribute significantly by monitoring and adjusting production parameters in real-time.
This monitoring capability ensures each part produced aligns with the quality standards set for the application.
Quality Indicators Monitored by Motion Control Systems:
- Part dimensions: Maintains tight tolerances to meet dimensional specifications.
- Surface finish: Ensures smooth, defect-free surfaces.
- Weight consistency: Monitors material usage to prevent variations in part weight, which is critical for applications requiring precise dosing.
What are the Challenges of Implementing Motion Control in Injection Molding?
Despite its advantages, implementing motion control in injection molding can pose several challenges.
These obstacles often arise due to the initial costs, the technical complexity of the systems, and the specialized knowledge required for operation and maintenance.
However, understanding these challenges allows manufacturers to plan more effectively and realize the benefits of motion control with fewer setbacks.
Common Challenges in Implementing Motion Control:
- Initial cost and investment: High-quality motion control systems require a significant upfront investment, especially for advanced electric and hybrid technologies.
- Maintenance requirements: Regular maintenance is necessary to keep systems operating smoothly, which adds to long-term costs.
- Need for specialized training: Operators and maintenance staff require specialized training to operate motion control systems effectively, which can add time and expense during implementation.
How Can These Challenges Be Overcome?
Manufacturers can address these challenges through targeted strategies.
For instance, exploring leasing or financing options can reduce the initial cost barrier, making high-end systems more accessible.
Furthermore, investing in comprehensive training programs not only improves system operation but also reduces the frequency of errors and downtime.
Regular, optimized maintenance schedules can help maximize the system’s lifespan and performance.
What Industries Benefit Most from Precision Motion Control in Injection Molding?
Several industries rely heavily on precision motion control in injection molding, each with unique requirements that make the technology indispensable.
Precision, repeatability, and high-quality standards are critical in these sectors, driving demand for advanced motion control systems.
Industries That Benefit from Motion Control in Injection Molding:
- Automotive: Produces components with complex geometries and tight tolerances, essential for vehicle safety and performance.
- Medical devices: Requires high precision and consistency to meet strict regulatory standards for medical-grade products.
- Consumer electronics: Demands miniature, detailed components with minimal defects to ensure reliability in high-tech products.
- Packaging: Requires efficient, high-speed production with consistent quality, especially for food-grade or pharmaceutical packaging.
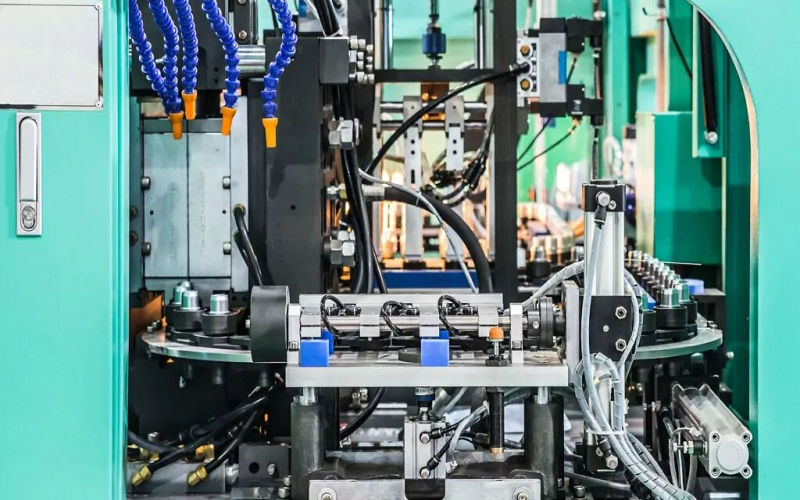
How to Choose the Right Motion Control System for Injection Molding?
Selecting the right motion control system is crucial for achieving desired outcomes in injection molding.
The choice largely depends on the specific production requirements, budget constraints, and precision needs of the application.
By carefully considering these factors, manufacturers can identify the motion control system that best aligns with their operational goals.
Key Considerations When Choosing a Motion Control System:
- Part complexity: More intricate parts often require systems with higher precision capabilities, such as electric or hybrid systems.
- Cycle time requirements: For applications demanding rapid production, motion control systems that optimize cycle times are essential.
- Budget constraints: Balancing initial investment with long-term benefits helps manufacturers choose the most cost-effective solution.
How Important is Precision for Your Application?
Determining the level of precision needed is a fundamental step in selecting a motion control system.
Applications with strict dimensional tolerances, such as medical or automotive parts, benefit from high-precision electric or hybrid systems, while less demanding applications may find hydraulic systems adequate.
Should You Opt for an Electric or Hydraulic System?
Electric systems provide superior precision and energy efficiency, making them ideal for applications requiring tight control over part dimensions.
However, hydraulic systems are more cost-effective for applications that prioritize force over precision. Hybrid systems offer a compromise, delivering both high force and accuracy, suited for complex, high-volume production environments.
What are the Advantages of Using Motion Control in Injection Molding?
The integration of motion control technology in injection molding brings numerous advantages that positively impact production quality, efficiency, and sustainability.
By automating and optimizing movements, these systems enhance both product quality and operational productivity.
Primary Benefits of Motion Control in Injection Molding:
- Reduced cycle times: Faster movements translate to shorter production cycles, which can lead to significant cost savings.
- Enhanced part quality: Precision control reduces defects, resulting in higher-quality products.
- Lower defect rates: Real-time adjustments minimize deviations, reducing the likelihood of rejects.
- Improved energy efficiency: Optimized movements reduce energy consumption, contributing to sustainable production practices.
How to Maintain and Troubleshoot Motion Control Systems in Injection Molding Machines?
Regular maintenance and troubleshooting in injection molding machines are vital to ensure the longevity and performance of motion control systems.
Preventive maintenance routines help identify and resolve potential issues before they cause downtime, while effective troubleshooting techniques allow for quick recovery from unexpected issues.
Key Maintenance Tasks for Motion Control Systems:
- Regular calibration: Ensures that all components function within specified tolerances, maintaining accuracy.
- Lubrication checks: Keeps moving parts operating smoothly, reducing wear and tear.
- Sensor alignment: Ensures sensors are properly positioned to provide accurate feedback for real-time adjustments.
Common Issues in Motion Control Systems
Several issues can arise within motion control systems, including motor overheating, sensor misalignment, and inconsistent feedback.
Overheating may indicate excessive load or inadequate cooling, while sensor misalignment can lead to inaccurate data, impacting control precision.
Step-by-Step Guide for Troubleshooting
For efficient troubleshooting, begin by isolating the issue—check sensors, motors, and controllers individually to identify faults.
Ensure all components are properly aligned, and if overheating persists, reduce load or improve cooling measures.
Regularly inspecting system connections can also prevent communication errors that may lead to system malfunctions.
Are There Alternative Technologies to Motion Control in Injection Molding?
While motion control is a popular choice, other technologies are sometimes used in specific applications.
These alternatives can be viable depending on the operational requirements and cost constraints of a production facility.
Alternative Technologies in Injection Molding:
- Hydraulic-only systems: Offer high force capabilities but lack the precision of modern motion control.
- Pneumatic systems: Useful for smaller, less complex parts but may lack the control needed for high-precision applications.
- Manual control systems: Rarely used in large-scale production, these systems are more suited for small-batch or prototyping environments where flexibility is prioritized over efficiency.
What are the Future Trends in Motion Control for Injection Molding?
The field of motion control is continually evolving, with innovations poised to make injection molding even more precise, efficient, and reliable.
These emerging trends leverage advancements in artificial intelligence, machine learning, and the Internet of Things (IoT) to push the boundaries of what’s possible in modern manufacturing.
Key Innovations to Watch in Motion Control:
- AI-driven motion control: Uses machine learning algorithms to optimize movement patterns and enhance precision automatically.
- Predictive maintenance: Analyzes data to predict component failures before they occur, reducing downtime.
- IoT integration: Connects machines to a centralized network, allowing for real-time monitoring and remote control, which is especially beneficial for large production facilities.
Conclusion
Motion control technology has become a fundamental asset in the injection molding industry, driving advancements in precision, consistency, and efficiency.
Through the integration of electric, hydraulic, and hybrid systems, manufacturers can produce high-quality parts with minimal waste and maximum repeatability.
As new innovations like AI-driven control and IoT integration continue to develop, the role of motion control in injection molding will only become more essential.
For manufacturers aiming to stay competitive in a fast-paced industry, adopting advanced motion control technologies is not just beneficial—it’s necessary.