Injection molding is a cornerstone of modern manufacturing, shaping everything from everyday plastic goods to advanced engineering components.
At its heart lies a delicate balance of plastic material, machinery, and process parameters, with temperature playing a pivotal role. From melting raw plastic to ensuring a polished surface finish, the right temperature settings dictate material flow, part strength, and cycle efficiency in plastic injection molding.
Yet, controlling temperature is no simple task—it demands an understanding of material behavior, machine dynamics, and practical know-how to navigate the challenges of real-world production.
This article is your practical guide to mastering injection molding temperature. Discover why temperature is a decisive factor, learn strategies to optimize settings for different materials and molds, and get actionable troubleshooting tips to address common defects.
What Is Injection Molding Temperature?
Injection molding temperature is the temperature at which plastic pellets are heated to a molten state during the injection molding process.
This involves several key temperature controls: barrel temperature, nozzle temperature, and mold temperature.
Barrel temperature refers to the heat inside the injection molding machine’s barrel, where plastic pellets are melted into a molten state, ensuring proper plasticization.
The nozzle temperature is the heat applied to the nozzle through which the molten plastic is injected into the mold. It should be slightly lower than the front barrel temperature to prevent drooling.
Mold temperature refers to the temperature of the mold cavity surface, crucial for controlling the cooling rate and the appearance of the final product.
These temperature settings must be carefully balanced based on the type of plastic, the shape and size of the product, and the mold’s structure.
Proper temperature control ensures a smooth injection molding process. Temperature fluctuations can affect product quality, so monitoring and adjusting temperatures closely during production is crucial. Understanding these temperature components and their roles helps achieve optimal results in injection molding.
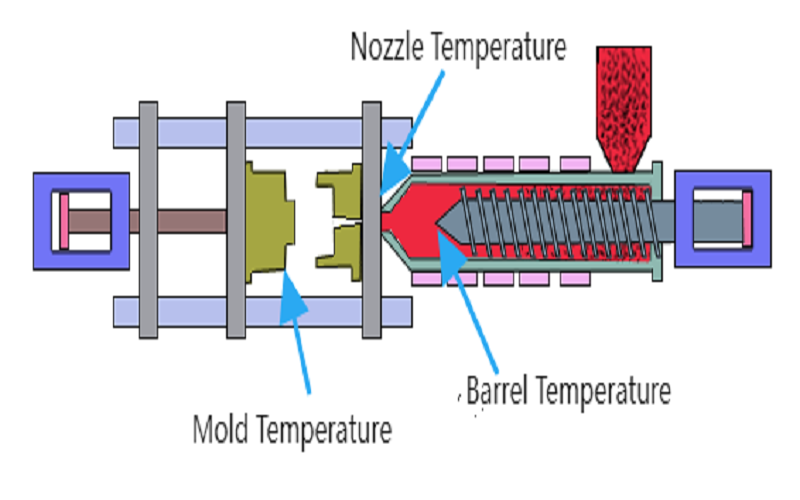
How Molding Temperature Affects the Product?
Molding temperature plays a critical role in determining product quality, production efficiency, and material performance in injection molding.
Temperature not only influences the physical properties of the molded product but also affects the overall efficiency and effectiveness of the production process.
Product Quality
Temperature directly shapes surface quality, dimensional stability, and internal stresses. An optimal melting temperature ensures uniform melting and good flow, delivering a smooth, glossy finish.
Too low a temperature leaves rough surfaces due to incomplete melting, while too high temperature can make it difficult for the product to form and be ejected from the mold. If the product is ejected at a temperature higher than its heat deflection temperature, it can deform, affecting the quality.
Excessive heat can lead to oversized parts or increase internal stresses, compromising mechanical properties.
On the other hand, insufficient heat risks inconsistent dimensions or filling defects. Thus, maintaining the right temperature is a critical factor in achieving high product quality.
Production Efficiency
The right temperature shortens molding cycles, boosting throughput. Improper settings—too high or too low—can overheat equipment or hinder material plastification, leading to downtime, faults, and higher costs. Optimizing temperature settings enhances manufacturing efficiency and reduces energy consumption.
Extended cycle times and secondary processing become necessary when temperatures are not correctly managed, impacting overall production efficiency. Therefore, maintaining the correct temperature is essential not only for product quality but also for maximizing manufacturing efficiency.
Material Performance
Temperature affects the physical properties and flow of plastic materials. Proper heat enhances density and strength by fully plasticizing the material.
Overheating may break molecular chains, reducing strength and elasticity, while underheating limits flow, weakening part integrity. Each type of plastic material has unique characteristics that require specific temperature controls to ensure optimal performance, especially when considering how plastic material melt can impact these properties.
Understanding the relationship between temperature and material performance is vital for producing high-quality, durable products. Proper temperature control can significantly improve the mechanical properties and wear resistance of the final product.
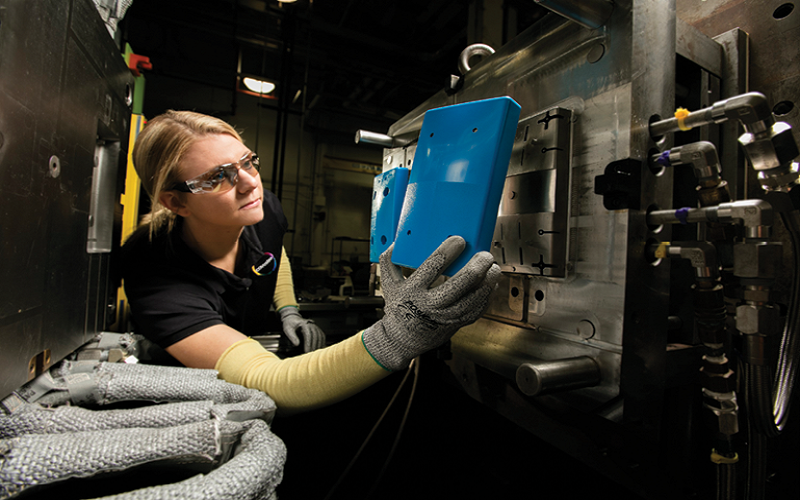
Recommended Temperature Ranges for Different Plastic Materials
Selecting the correct mold temperature is crucial for achieving high-quality products, especially for semi-crystalline plastics that should be molded close to their crystallization temperature.
Injection molding manufacturers typically provide specific temperature ranges for melting, which are crucial for optimal processing.
Here, we provide recommended molding temperatures for common plastics like various plastic materials:
Polyethylene (PE)
Polyethylene (PE) is a widely used plastic that includes two main types: Low-Density Polyethylene (LDPE) and High-Density Polyethylene (HDPE).
LDPE typically has a melting point range from 180°C to 240°C, making it more flexible. HDPE ranges from 200°C to 260°C, offering rigidity and durability. These melting points influence the unique properties and applications of LDPE and HDPE.
Polystyrene(PS)
The typical processing temperature range for Polystyrene is generally set between 180°C and 230°C. It is quite sensitive to temperature, particularly near the upper end of its processing window. If the processing temperature becomes too high, exceeding the recommended range, PS is prone to thermal degradation.
This can lead not only to scorching, yellowing, or discoloration, significantly impacting the product’s appearance, but may also decrease its flowability and degrade the physical properties and mechanical strength of the final part.
Polycarbonate(PC)
Polycarbonate is a high-performance engineering plastic with a relatively high processing temperature range, typically between 250°C and 320°C.
Despite its inherent good heat resistance, PC also exhibits sensitivity to processing temperatures, particularly when they become excessive or when exposure to heat is prolonged. If the temperature significantly exceeds the recommended upper limit, or if the material is held at high temperatures for too long (excessive residence time), Polycarbonate can undergo thermal decomposition.
This decomposition can not only release potentially harmful gases but also lead to chain scission (breaking of the polymer chains), which severely compromises its key properties such as transparency (for clear grades), impact strength, and overall mechanical performance including long-term durability.
Polypropylene (PP)
Polypropylene generally requires a mold temperature setting between 30°C and 80°C during the injection process. This temperature range, well above its glass transition temperature (typically around -10°C to 0°C), ensures optimal product quality and performance by allowing proper flow and crystallization.
Polyvinyl Chloride (PVC)
Rigid PVC requires a mold temperature around 30°C to 50°C. Flexible PVC’s temperature settings can differ significantly compared to rigid PVC. Proper temperature control for PVC maintains its chemical resistance and durability.
Principle Of Molding Temperature Control
Controlling molding temperature relies on several key aspects:
The cooling system of injection mold is crucial, as the cooling phase accounts for 60% to 80% of the injection molding process and directly impacts product quality.
The flow rate of the cooling liquid is vital.
Through cooling channels designed within the mold, the circulating coolant at a predetermined temperature removes heat, ensuring uniform mold surface temperature and preventing overheating, thus guaranteeing molding precision and stability.
Mold temperature machines achieve precise heating through internal circulation of heat transfer oil. The oil continuously circulates within the mold or hot press plate’s channels, evenly transferring heat to the molding mold or hot press plate. Once the required temperature for production is met, heating stops.
Mold temperature machines support customizable temperature settings, ensuring uniform heating of the material, effectively preventing product deformation, and enhancing molding efficiency and quality.
Understanding these principles of molding temperature control is essential for achieving consistent and high-quality products in the injection molding process.
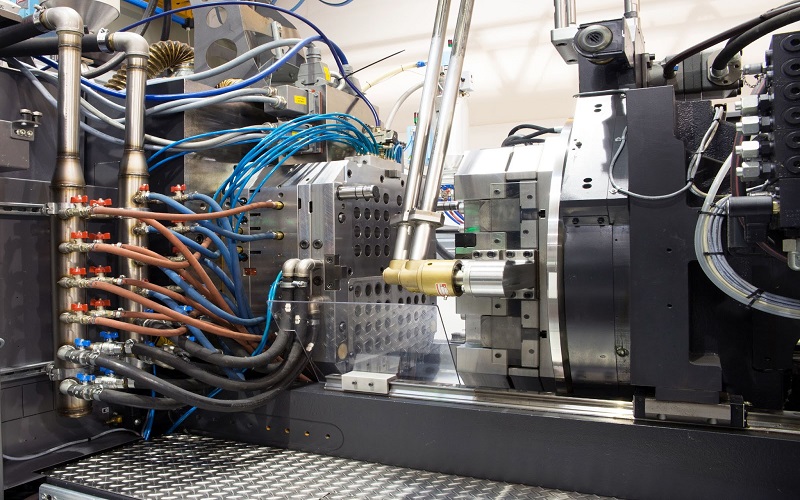
Challenges of High and Low Molding Temperatures
Incorrect temperature settings can lead to numerous challenges. High temperatures can cause plastic to decompose or lose desirable features, while low temperatures can result in incomplete filling of the mold.
High Molding Temperature Issues
Excessively high mold temperatures can cause material degradation and extended cycle times. Improper mold temperature adjustment can lead to various product quality issues.
High molding temperatures can lead to severe defects in the final product, such as warping, discoloration, and reduced mechanical properties. These defects significantly impact production efficiency and product performance.
Keeping mold temperatures within specified limits maintains the integrity and quality of the final product. Regular monitoring and adjustments prevent high-temperature issues.
Low Molding Temperature Issues
Low mold temperatures result in low smoothness of the surface finish. Higher mold temperatures increase surface gloss, while lower temperatures decrease it.
Low molding temperatures reduce product strength and make weld lines more visible. Residual internal stress can exceed the resin’s elastic limit, leading to cracks on the surface of the plastic part.
Low temperatures decrease melt flowability. This can potentially result in incomplete filling of the mold. Correct mold temperature ensures smooth, strong, and defect-free products.
Determining The Correct Temperature In Injection Molding
Determining the correct injection molding temperature is key to ensuring product quality and production efficiency. This involves a systematic approach, starting with material specifications and ending with real-time monitoring and adjustments.
Refer to Material Specifications
ABS typically requires a melt temperature of 210–250°C and a mold temperature of 50–80°C, along with melting temperature ranges that may shift due to additives (e.g., fibers or flame retardants).
Following these guidelines ensures that the material is processed under optimal conditions, enhancing product quality and performance, considering the plastic melting temperature.
Material datasheets provide critical information for setting correct temperature parameters, crucial for achieving desired results in injection molding.
Set Initial Parameters
Based on the datasheet, configure initial barrel, nozzle, and mold temperatures. Begin at the lower end of the range—e.g., set the barrel at 210°C for a 210–230°C range—to avoid degradation. Start mold temperatures low and adjust gradually. This approach helps in minimizing the risk of thermal degradation and other temperature-related issues.
Correctly setting initial parameters lays the foundation for successful injection molding. Gradual adjustments ensure optimal conditions, enhancing product quality and performance.
Test and Observe Results
Run a trial production and inspect parts for surface quality, dimensional stability, and defects. If short shots (underfilling) occur, increase melt temperature by 5–10°C; for burns or bubbles, lower nozzle temperature. Document each adjustment’s impact. Conducting tests during the injection molding process allows for observation of how temperature affects the flow and quality of the molten resin.
Analyzing temperature test results helps adjust cooling rates to ensure consistent product quality. Temperature monitoring data aids in fine-tuning mold design to mitigate heat distribution issues.
Temperature tests reveal the optimal conditions for resin flow, which can enhance production efficiency.
Monitor and Fine-Tune in Real Time
Use thermocouples or infrared thermometers to track actual barrel and mold temperatures, ensuring they match settings. Adjust dynamically based on defects—like raising mold temperature to reduce warpage—keeping changes small (e.g., 5°C) for stability. Real-time monitoring and fine-tuning are essential for maintaining dimensional accuracy and preventing defects.
Regular monitoring and small adjustments maintain optimal temperature settings throughout production, ensuring consistent product quality and reducing defects.
Utilize Simulation Tools
For complex shapes molds, employ software like Moldflow to predict temperature effects on flow and cooling, optimizing settings beforehand.
These tools provide insights into mold temperature management, helping to prevent defects caused by improper thermal conditions during the injection molding process.
Advanced simulation tools can evaluate various scenarios, including thermal cycling and material behavior, enhancing the accuracy of mold temperature settings.
Simulation tools like Moldex3D and Autodesk Moldflow enable detailed analyses of injection molding processes, optimizing mold temperature control and cooling, reducing cycle times, and minimizing warpage.
Early-stage simulation aids in troubleshooting and refining mold designs for better temperature management. Validate simulation results with production runs to refine ideal temperature settings, ensuring high-quality and efficient production.
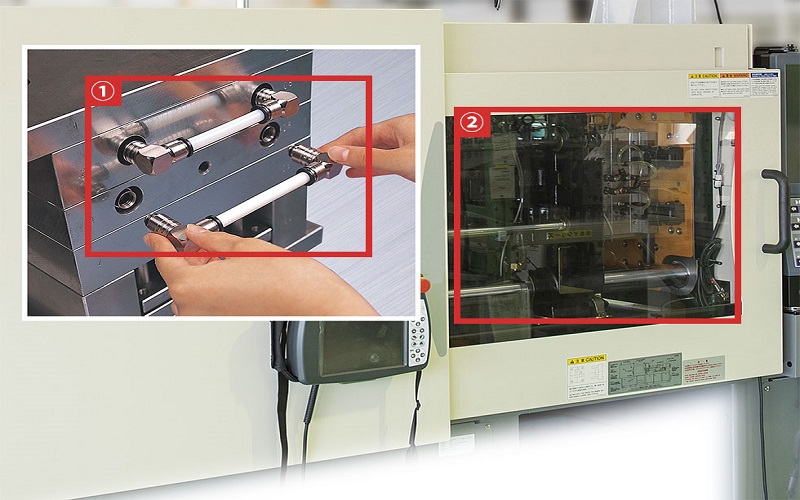
Summary
Mastering injection molding temperature is a multifaceted challenge that demands a deep understanding of material behavior, precise control mechanisms, and advanced simulation tools.
From defining what injection molding temperature is to exploring its impact on product quality, production efficiency, and material performance, this guide has covered the essential aspects of temperature control in injection molding.
By following the recommended molding temperatures for common plastics and adhering to the principles of temperature control, manufacturers can achieve high-quality products with optimal performance.
Regular monitoring, real-time adjustments, and the use of simulation tools further enhance the precision and efficiency of the injection molding process. With the knowledge and strategies shared in this guide, you are well-equipped to tackle the complexities of injection molding temperature control and achieve excellence in your manufacturing endeavors.