Micro injection molding is a specialized injection molding technique designed for producing extremely small components, capable of manufacturing complex plastic parts at the micron or even nanometer scale.
As modern industry demands increasingly precise and miniature components, this technology demonstrates immense application potential in fields such as medical devices, electronics, and micro-electromechanical systems (MEMS).
This article will explore the process characteristics, application scenarios, and differences between micro injection molding and traditional injection molding, providing readers with a comprehensive understanding of this manufacturing technique.
What Is Micro Injection Molding?
Micro injection molding was first proposed in 1985 and is generally defined as a process used to manufacture the following three types of products or components:
- Products weighing from a few micrograms to fractions of a gram, with dimensions possibly in the micron (mm) range, such as micro gears and micro levers.
- Conventionally sized injection-molded products with microstructured areas or functional zones, for example: optical discs with data pits, lenses with micro-surface features, or thin sheets used to fabricate micro gears.
- High-precision products with arbitrary dimensions but micron-level tolerances, such as connectors used in fiber optic technologies.
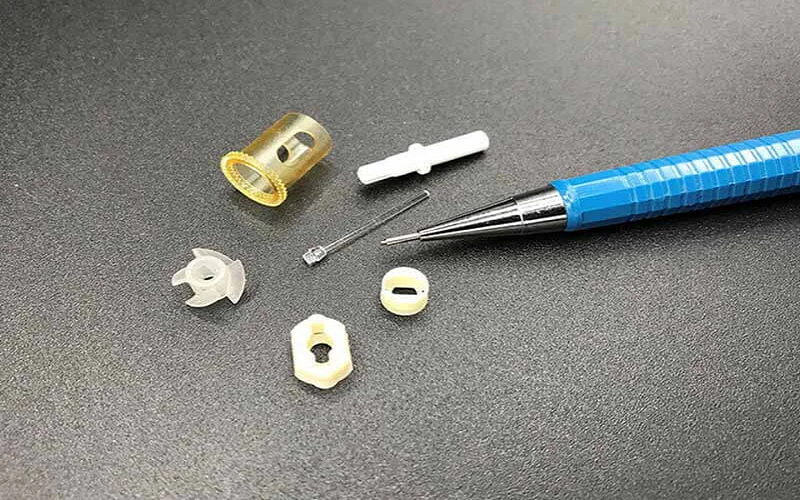
How Micro Molding Differs From Conventional Injection Molding?
Micro injection molding and traditional injection molding both fall under plastic molding technologies but differ significantly in terms of equipment, production capacity, and application areas.
Equipment Differences
Micro injection molding machines are compact and lightweight, with tonnage typically ranging from a few tons to several dozen tons, making them ideal for producing small, lightweight plastic parts.
In contrast, traditional injection molding machines are larger and heavier, requiring more space and suitable for large-scale production.
Production Capacity
Micro injection molding machines are designed for small-batch, customized production, and prototype manufacturing.
They can process high-precision, complex parts weighing less than 1 gram with cross-sectional dimensions under 1 mm.
Traditional injection molding machines, on the other hand, offer higher production capacity, capable of handling larger molds and complex structures for mass production.
Application Areas
Micro injection molding is commonly used for manufacturing medical devices, electronic components, and precision industrial parts, making it ideal for small businesses and R&D teams.
Traditional injection molding machines are widely applied in industries such as automotive, home appliances, and consumer goods, capable of producing large plastic products and intricate structures.
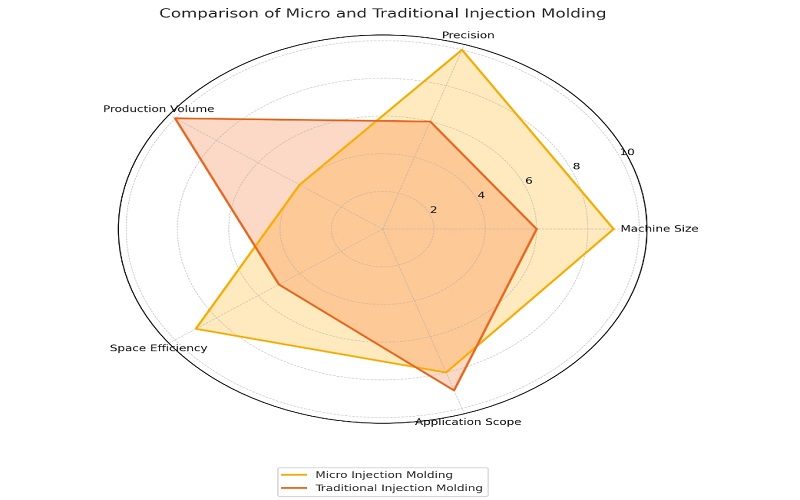
Benefits of Micro Injection Molding
Micro molding technology demonstrates unique advantages in precision, efficiency, and cost-effectiveness:
High Precision
Micro injection molding machines utilize digital control systems to achieve high precision at every stage of production, including injection, holding pressure, and demolding. This ensures enhanced product accuracy and consistency.
Fast Speed
Due to their compact size, micro injection molding machines operate at relatively higher speeds. By optimizing the machine structure and production process, faster production cycles can be achieved.
Wide Applicability
Micro injection molding machines are suitable for producing various small components, molds, electronics, optical products, and more.
Their small size also makes installation and setup quick and convenient.
Cost-Effectiveness
Using appropriate micro injection molding machines ensures high product quality while significantly optimizing production costs, reducing energy consumption, and minimizing material waste.
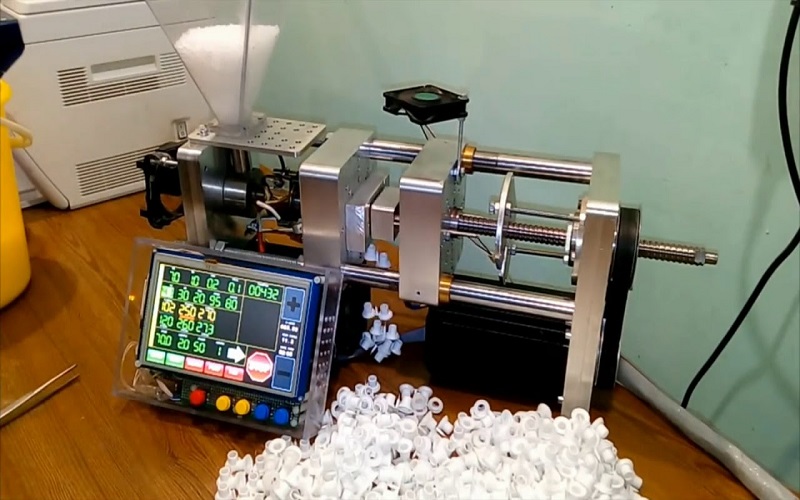
Requirements For Micro Injection Molding Process
Micro injection molding products typically range in size from a few microns to several centimeters, with aspect ratios generally between 1 and 100.
Certain regions of these products often require specific properties such as high strength, superior surface finish, or excellent transparency.
To ensure these features are reproduced with high fidelity, the micro injection molding process and equipment must meet several specialized requirements:
Equipment Requirements
Micro Injection Machines equipped with screws of 12–18 mm in diameter and relatively short lengths, with an L/D ratio of approximately 15.
They should also feature separate systems for material metering and injection, utilizing both plunger and screw mechanisms.
Process Requirements
- High Injection Speed and Pressure: Extremely high injection speed and pressure, typically ranging from hundreds to thousands of kg/cm², are essential to ensure complete mold filling.
- Elevated Melt and Mold Temperatures: The melt temperature should be maximized within the allowable range, and mold wall temperatures should be maintained at the higher end to enhance mold filling and replication accuracy.
- Large Flow Channels and Gates: These designs enable effective control and switching of polymer flow, preventing material degradation during the molding process.
Mold Requirements
- Dynamic Temperature Control: Molds must include separate heating and cooling systems to dynamically adjust mold temperatures. High temperatures are required during the filling phase, while rapid cooling is essential during the solidification phase. This is typically achieved using dual oil circuits for temperature regulation.
- High Precision and Automation: Molds should integrate high-precision guidance systems, advanced sensors, and automation technologies, such as robotic arms for product removal, automated gate cutting systems, and integrated runner collectors.
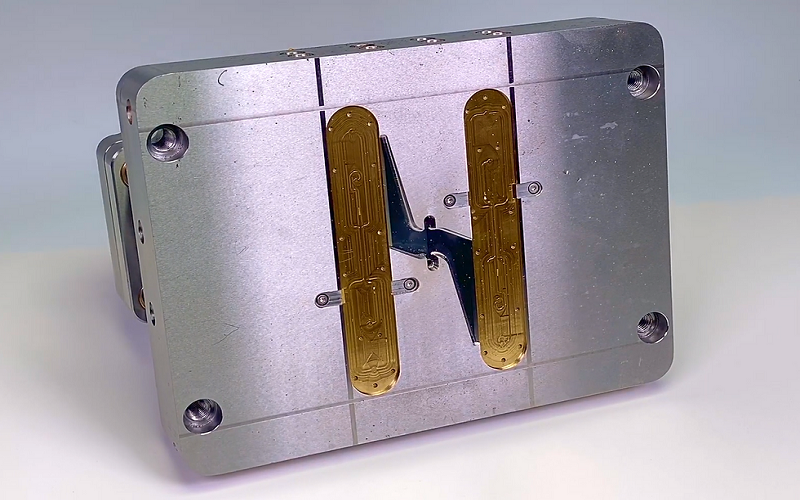
Applications of Micro Injection Molded Products
Micro injection molding is characterized by high precision, low production volume, and space efficiency, making it ideal for manufacturing complex, high-precision components. It is primarily applied in the following industries:
Medical Industry
Used for producing high-precision, high-sterility medical devices and accessories, including syringes, infusion sets, blood collection devices, microcatheters, and sensors. It also enables the production of biodegradable medical screws and microfluidic devices for biomedical research and clinical diagnostics.
Electronics Industry
Ideal for manufacturing small electronic product components such as housings and circuit board encapsulations for devices like smartphones, digital cameras, headphones, and power tools.
Precision Industrial Components
Micro injection molding is well-suited for creating small, high-precision, and complex parts required in precision industrial applications, offering flexibility for products demanding advanced manufacturing techniques.
Automotive Industry
Applied in the production of lightweight interior and exterior components, dashboards, lighting, and bumpers, micro injection molding supports fuel efficiency and integrates complex shapes and functionalities.
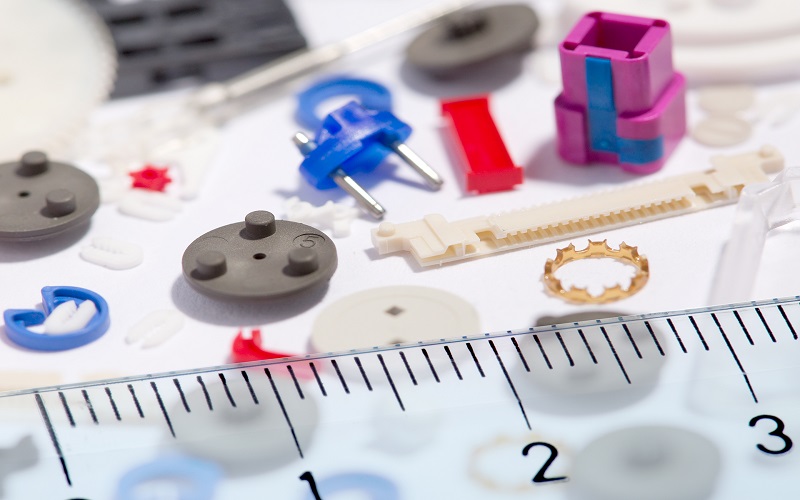
Challenges And Opportunities Of Micro Injection Molding
Micro injection molding faces significant challenges, particularly in mold design, which requires extreme precision to replicate intricate micro-component geometries.
Material selection is equally critical, as variations in flow properties, shrinkage, and physical performance directly affect product quality.
Additionally, precise control of temperature, pressure, and timing is essential, demanding advanced equipment and expertise to ensure stability and repeatability.
Despite these challenges, the field is advancing rapidly. Innovations in smart manufacturing and automation have improved precision, efficiency, and cost-effectiveness.
Advanced materials like liquid crystal polymers (LCP) and polyether ether ketone (PEEK) offer superior mechanical and thermal properties, expanding design possibilities and applications in high-performance industries such as electronics, healthcare, and aerospace.
As technology and materials evolve, micro injection molding continues to overcome its challenges, unlocking new potential for producing complex, high-precision components.
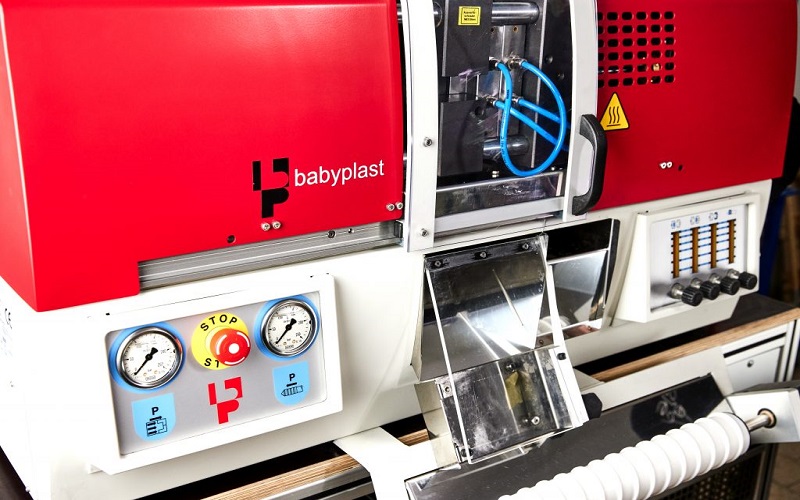
Conclusion
In conclusion, micro injection molding, as a specialized branch of injection molding, is advancing toward higher dimensional accuracy, enhanced functionality, and superior aesthetic standards.
Meeting market demands requires rigorous control over molds, equipment, materials, and processes, along with continuous technological advancements.
As one of China’s leading injection molding manufacturers, FOWMOULD is equipped with state-of-the-art facilities to provide customized micro injection molding solutions. If you are interested, please feel free to contact us today!