In today’s Industry 4.0 landscape, there’s a mounting demand for enhanced technological resource efficiency. Stepping up to meet this challenge, magnet injection molding emerges as a trailblazing approach, melding the worlds of cutting-edge materials science and meticulous injection molding.
By amalgamating minute magnetic granules with polymer binders and harnessing the power of heat and pressure, this method crafts intricate permanent magnets, opening doors to myriad applications across diverse sectors.
In the ensuing sections, we will unpack the mechanics of magnet injection molding and its transformative impact on contemporary manufacturing.
What is Magnet Injection Molding?
Departing from traditional manufacturing processes, magnet injection molding is a complex manufacturing process in which powdered magnet material is mixed with a polymer binder, heated to a semi-fluid state and injected into a mold where it cools and solidifies to create a permanent magnet.
Notably, the design and manufacture of permanent magnets is at the heart of magnet injection molding technology, minimizing material waste while meeting the need to customize complex magnets. This technological innovation offers unlimited potential to revolutionize the electronics, automotive, and medical industries, rewriting the landscape of modern manufacturing.
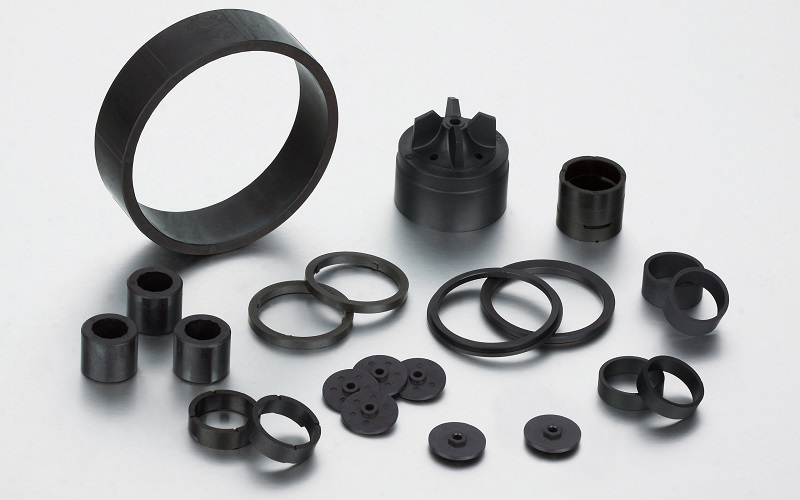
How Magnet Injection Molding Works?
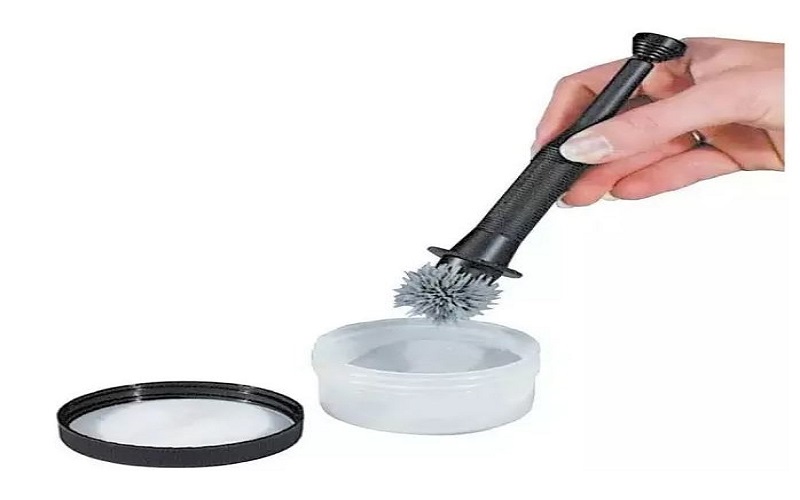
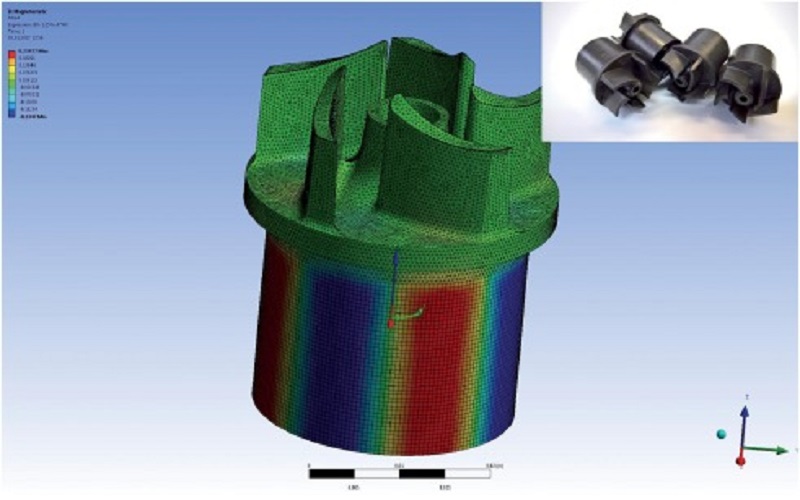
Magnet Injection Molding represents a groundbreaking advancement in the realm of magnetic parts manufacturing. Ingeniously marrying the precision of injection molding with the production of magnetic materials, it deftly bridges the gap between intricate design possibilities and the tangible creation of magnetic components.
The process commences with a blend of fine magnetic powders and polymer binders, creating a composite mixture. This concoction is heated until it reaches a semi-fluid state.
Within specialized machinery, this molten mix is then injected into meticulously designed molds. As the mixture fills these molds, it begins to cool, solidifying the magnetic material into the intended shape.
Post-molding, the procedure transitions to a pivotal debinding phase. Here, the polymer binder is systematically eliminated, leaving only the magnetic material. This is followed by sintering, wherein the magnetic particles fuse together, amplifying their inherent magnetic properties. To meet stringent product standards, post-sintering may see some components undergo additional refining or treatments.
Precautions For The Magnet Injection Molding Process
The complexity of magnet molding requires strict control of details at every step. Thus, it is necessary to have a comprehensive understanding of what needs to be paid attention to in the injection molding process to provide a guarantee for the perfect production of magnets.
Temperature Control
To attain the perfect semi-fluid state, the heating temperature must be strictly regulated. Overheating can compromise the magnetic properties of the powder, leading to defects in the final product. The maximum tolerable temperature is determined by the functions of the magnetic alloy powder and the binder. For instance, ferrite powder in nylon 6 or PPS is suitable for the injection molding process at around 180 °C.
Debinding Treatment
Following the molding, the post-molding phase, especially the debinding process, demands utmost precision. Any remnants of the binder can adversely impact the structural and magnetic performance of the finished item. Moreover, the sintering phase needs meticulous monitoring, with factors like temperature, pressure, and duration playing a pivotal role in establishing the final magnetic characteristics.
Anti-Oxidation Measures
Given the sensitivity of magnetic materials, protection against oxidation stands as a key concern. Exposure to oxygen in the air can substantially weaken their magnetic strength. Hence, the molding environment and sintering processes must be calibrated to minimize exposure to oxygen.
Safety Protocols
Lastly, and most importantly, safety is paramount during the injection molding process. Owing to the potential hazards of magnetic materials, which can have serious consequences if inadvertently consumed, it’s essential to equip workers with appropriate protective gear. Furthermore, comprehensive quality inspections of the final products ensure their reliability and efficacy.
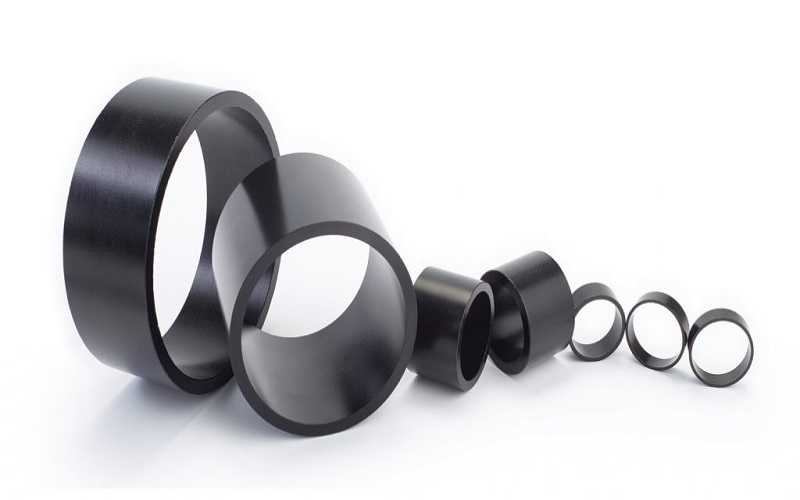
The Power of Magnet Injection Molding
Among the plethora of manufacturing technologies, magnet injection molding stands out, solving intricate magnetic design challenges, epitomizing the pinnacle of process innovation and precision in products.
At the heart of magnet injection molding lies the creation of high-quality permanent magnets. Traditional magnet fabrication often leans on mechanical machining or stamping, leading to constraints in design and manufacturing. However, by blending magnetic powders with polymer binders and meticulously managing the parameters during the injection process, injection molding plastic magnet captures the intended design while preserving magnetic strength, shattering the constraints of old methodologies.
Magnets produced this way, often referred to as “injection-molded magnets” boast strength and durability on par with their traditionally manufactured counterparts. In many scenarios, especially when intricate geometric designs are required without sacrificing the magnet’s inherent attributes, they exhibit remarkable advantages over conventionally made magnets.
Furthermore, the adaptability of magnet injection molding has garnered widespread appreciation across industries. From electronics to automotive, wherever there’s a demand for permanent magnets, its imprint can be found, rising to many challenging occasions.
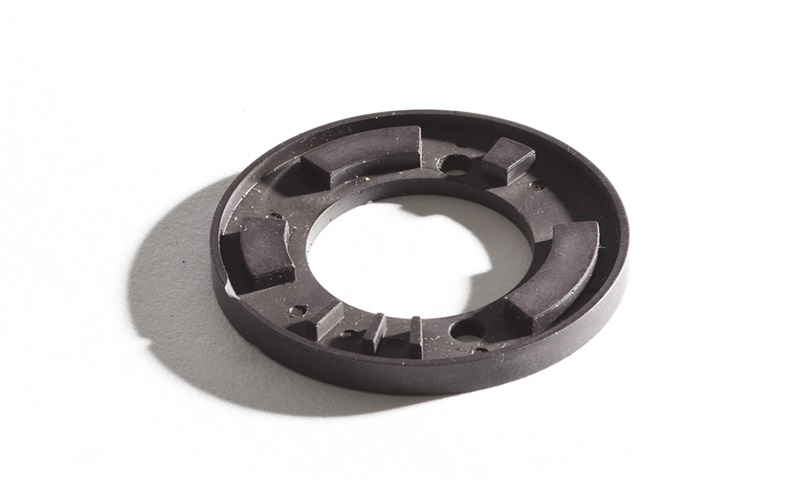
Application of Magnet Injection Molding
As a fusion technology of advanced material science and high-precision manufacturing processes, magnet injection molding has left a magnetic footprint in a wide range of industries.
Automotive Components
As the demand for precision manufactured parts has increased dramatically, the introduction of magnetic injection molding technology in the automotive industry has created specialized magnetic parts for sensors, hybrids, and advanced driver assistance systems (ADAS).
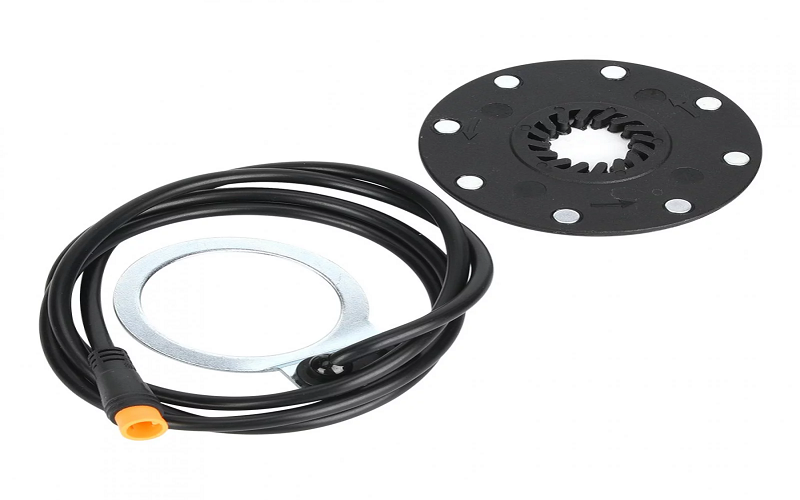
Medical Devices
In the medical industry, especially in the manufacturing of medical devices, the magnet injection molding technique is paramount. The high-precision magnetic components produced by this method meet the essential accuracy and quality requirements perfectly suited for critical applications. This is particularly evident in devices used for imaging and diagnostics, such as MRI machines.
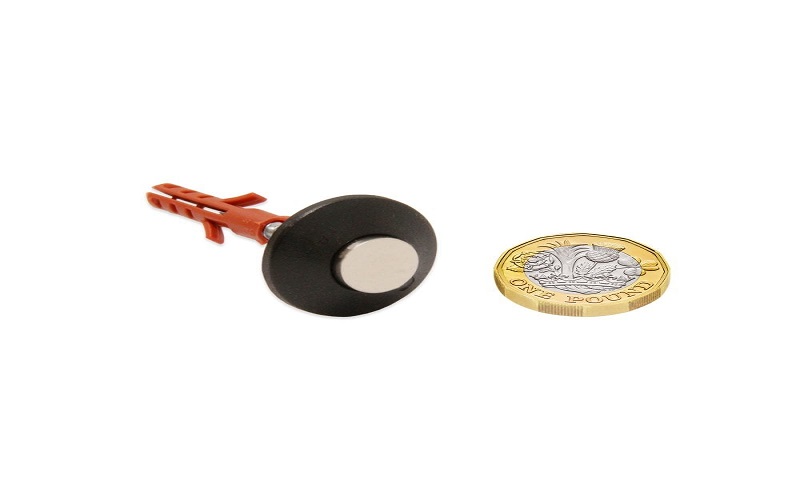
Electronics Product
As the technology behind magnet injection molding matures, it has become the preferred method for manufacturing the essential micro-magnetic components found in electronic products. This advancement has propelled the miniaturization trend seen in devices such as smartphones, tablets, and wearable gadgets.
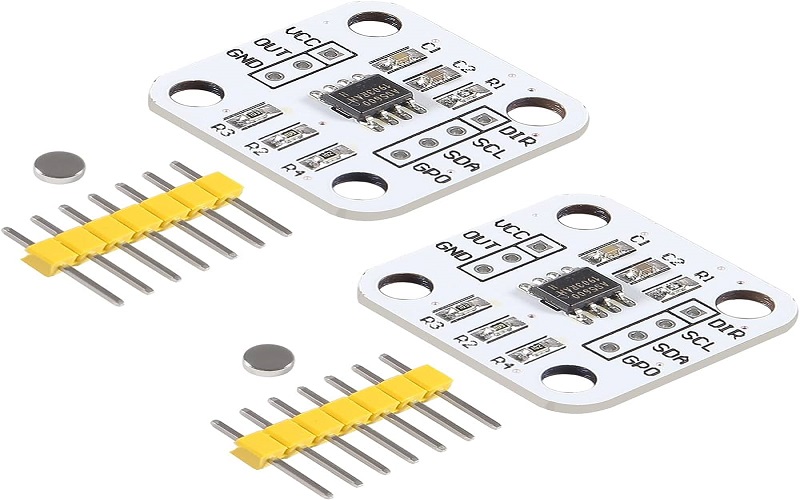
Aerospace
In the aerospace domain, the utilization of magnet injection molding has significantly elevated the sophistication of navigation, communication, and propulsion systems. This technological breakthrough ensures consistent reliability under demanding flight scenarios, contributing to the overarching safety and efficacy of both aerial and space expeditions.
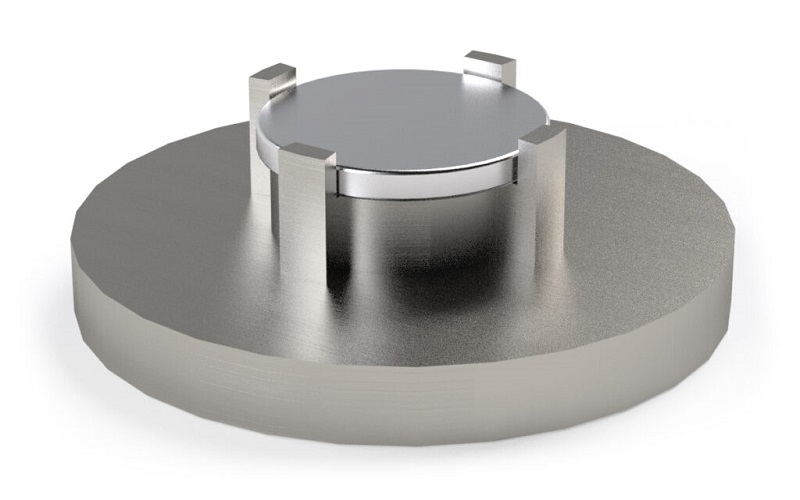
FOWMould-Professional Magnet Injection Molding Service Provider
With countless injection molding companies in China, FOWMould stands out as the premier service provider for magnet injection molding.
Utilizing state-of-the-art technology and deep industry expertise, FOWMould has carved out a niche for itself in the production of high-quality, precision-engineered magnetic components.
For a wide range of sectors, from electronics to aerospace, FOWMould understands the complex needs of modern industry and provides customized solutions.
FOWMould’s unwavering commitment to excellence and innovation ensures that every project is executed with precision, timeliness and quality.
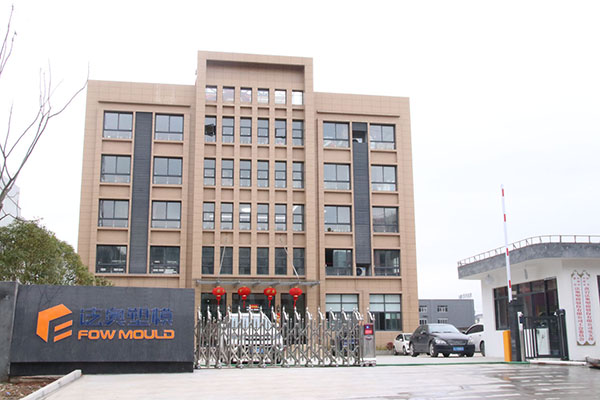
Conclusion
In summary, magnet injection molding is the perfect fusion of precision engineering and material science, completely transforming the production of intricate magnetic components.
Across various domains, magnet molding has established itself as an indispensable process. Experience a craft beyond your imagination—let FOWMould assist you in crafting your unique plastic magnets!