The injection molding wall thickness is a critical factor that directly impacts the product’s mechanical performance, production cost, and molding cycle.
Therefore, maintaining uniform wall thickness is a fundamental principle for the success of an injection molding project.
So, what should the specific wall thickness be? How should it be scientifically designed?
In the following content, we will delve into the intricacies of wall thickness design in injection molding, uncovering its design principles and optimization methods.
What Is Wall Thickness In Injection Molding?
Injection molding wall thickness refers to the thickness between the outer and inner surfaces of a plastic product, and is one of the primary factors to consider in product design.
Generally, the wall thickness for injection molding ranges from 1.5 mm to 4.5 mm.
The specific thickness should be determined based on the product’s size, shape, and usage requirements.
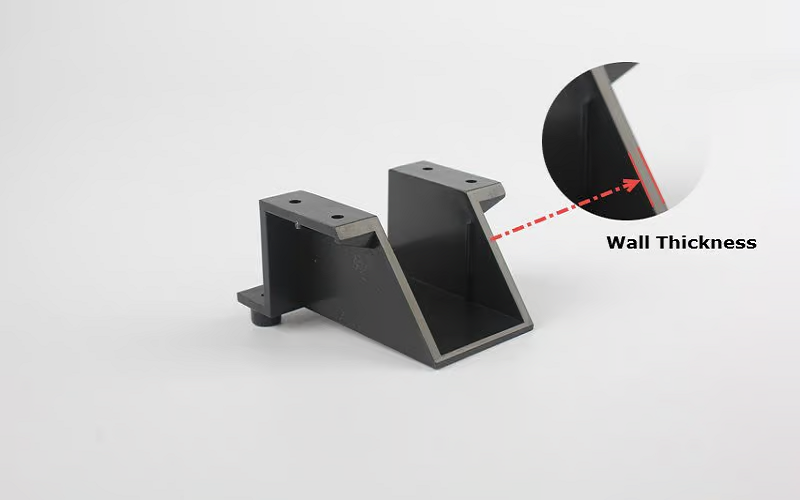
Why Is Uniform Wall Thickness Important In Injection Molding?
The design of wall thickness in injection molding is crucial for the performance, cost, production efficiency, and overall quality of plastic products.
Overly thick walls can lead to material wastage and increased costs, while also adding unnecessary weight and extending production cycles.
Conversely, walls that are too thin may result in deformation, cracking, and other issues that can compromise the product’s durability and performance.
For example, during the injection molding process, areas with varying wall thicknesses cool at different rates, leading to uneven shrinkage.
This can cause surface defects like sink marks or internal issues like voids.
Additionally, inconsistent wall thickness can result in warping, deformation, and internal stresses, which negatively impact the product’s mechanical properties and aesthetic quality.
In summary, achieving uniform wall thickness is essential for ensuring the structural integrity, functionality, and visual appeal of injection-molded products, while also optimizing production costs and efficiency.
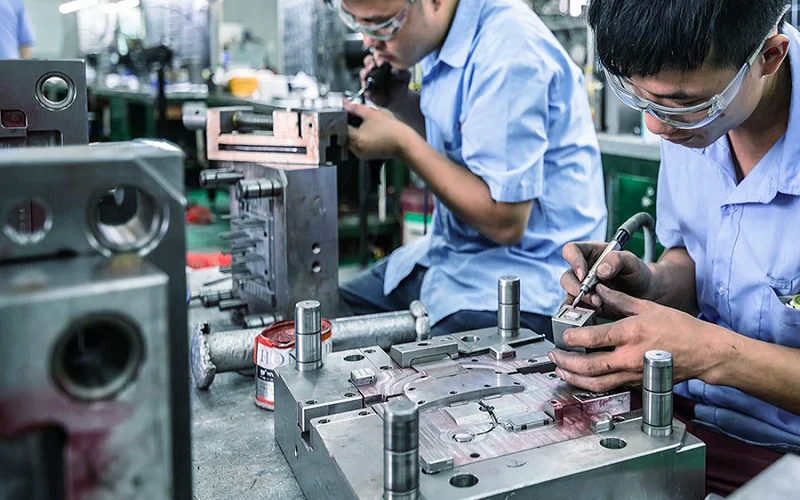
How To Design For Uniform Wall Thicknesses?
Uniform wall thickness doesn’t mean every part of the product must have exactly the same thickness.
Instead, it means creating a design that ensures even material flow and consistent cooling.
When changes in wall thickness are necessary, design smooth transition areas to prevent stress concentration and uneven material shrinkage.
Avoid sharp corners in the design, as they can lead to stress points and reduce the impact strength of the plastic part.
Instead, use rounded corners with a radius that is 25% to 50% of the wall thickness, with 50% being the recommended value.
For areas requiring additional strength or stiffness, incorporate ribs or gussets.
These reinforcing structures should follow the guideline of having a thickness that is 40% to 60% of the primary wall thickness to ensure both strength and overall uniformity.
To achieve the best results, use mold flow analysis software. This tool can simulate material flow, cooling, and shrinkage behaviors, allowing you to optimize wall thickness design and ensure that the final product meets the desired specifications.
By following these principles, you can design injection-molded parts with uniform wall thicknesses that enhance performance, reduce defects, and improve production efficiency.
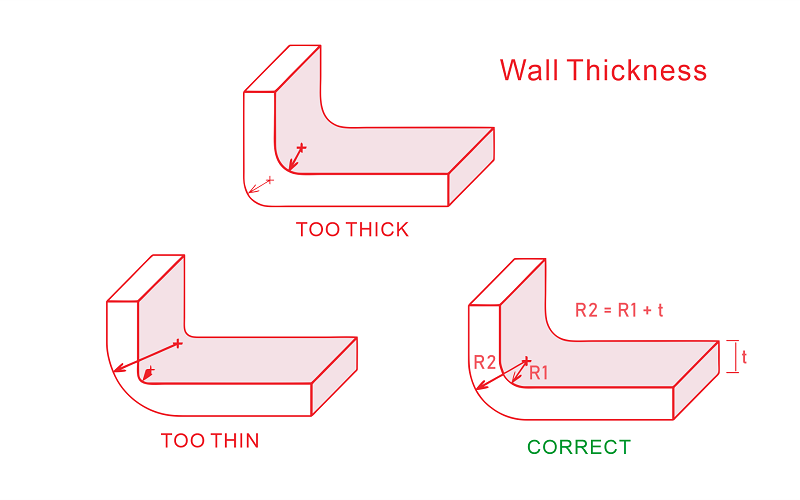
What is the Minimum Injection Molding Wall Thickness?
For injection-molded products, the minimum wall thickness should not be less than 0.6mm to avoid issues like sticking or ejection difficulties.
Too thin walls increase flow resistance, making it hard for large, complex parts to fill the cavity properly, affecting quality.
The wall thickness design must also consider the product’s strength, stiffness, and ability to withstand demolding impacts and assembly forces.
Factors such as material type, properties, and color also influence the minimum wall thickness.
Below is a reference formula for calculating the minimum wall thickness for injection molding:
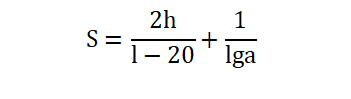
- S=minimum wall thickness of the plastic part (mm)
- h=anticipated wall height of the plastic part (mm)
- l=flow length of the plastic (mm)
- a=specific impact toughness of the plastic (kJ/m2)
The applicable range of this formula: wall height of the injection-molded part is 160-200mm, flow length is 30-200mm, and the specific impact toughness of the plastic is 2.5-100 kJ/m².
What Is The Maximum Injection Molding Wall Thickness?
The maximum injection molding wall thickness refers to the thickest possible design of a plastic part that can be achieved during the injection molding process without compromising the product’s molding quality and performance.
Generally, larger products require thicker walls to ensure their strength and stability.
For example, products with dimensions greater than 200mm typically have a wall thickness of over 2mm.
As the product size increases, the wall thickness also needs to be increased accordingly.
When designing injection-molded parts, it is essential to consider the process complexity and material limitations. Excessive wall thickness can lead to molding difficulties, increased costs, and the inability of some materials to fill the mold properly.
For instance, for certain materials like ABS, designing parts with wall thicknesses exceeding 6mm may result in filling problems.
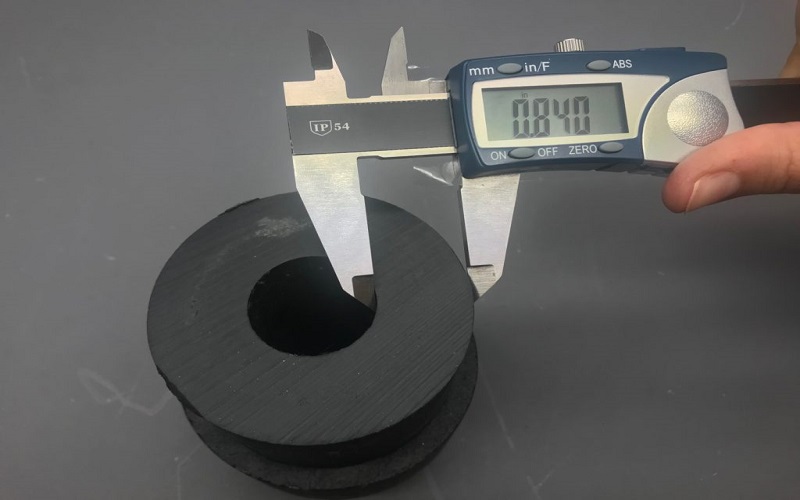
Injection Molding Wall Thickness For Various Materials
Different materials have unique physical and chemical properties that determine the optimal wall thickness range.
For thermoplastic injection-molded products, the wall thickness is generally selected within the range of 1-4mm.
The minimum wall thickness typically should not be less than 0.6-0.9mm, while for large products, the wall thickness can be increased to 6mm or even thicker.
Table 1 presents the wall thickness parameters for several commonly used thermoplastic materials under molding conditions:
Table 1 Wall Thickness Of Common Thermoplastics (mm)
Material Name | Common Wall Thickness | Maximum Wall Thickness | Minimum Wall Thickness |
ABS | 2.3 | 3.18 | 0.76 |
PP | 2.0 | 4.53 | 0.64 |
PC | 2.36 | 9.35 | 0.60 |
PA | 1.57 | 3.18 | 0.38 |
PS | 1.57 | 6.35 | 0.76 |
POM | 1.57 | 3.18 | 0.38 |
HDPE | 1.57 | 6.35 | 0.9 |
LDPE | 1.57 | 5.35 | 0.5 |
Thin Wall Injection Molding vs Thick Wall Injection Molding
Thin-wall injection molding is a relative concept, which can be defined in the following three scenarios:
- The ratio of flow length (L) to thickness (T) is L/T > 150;
- The thickness of the molded part is less than 1 mm, and the projected area of the part is more than 50 cm²;
- The wall thickness of the molded part is less than 1 mm (or 1.5 mm), or the ratio of thickness (T) to diameter (d) (for disc-shaped parts) is less than 0.05.
Thin-wall injection molding is widely used in food packaging due to its advantages of low part weight, small production scale, reduced material costs, and short molding cycles.
Thin-wall injection molds require highly precise design and manufacturing to ensure that products maintain good strength and toughness under thin-wall conditions.
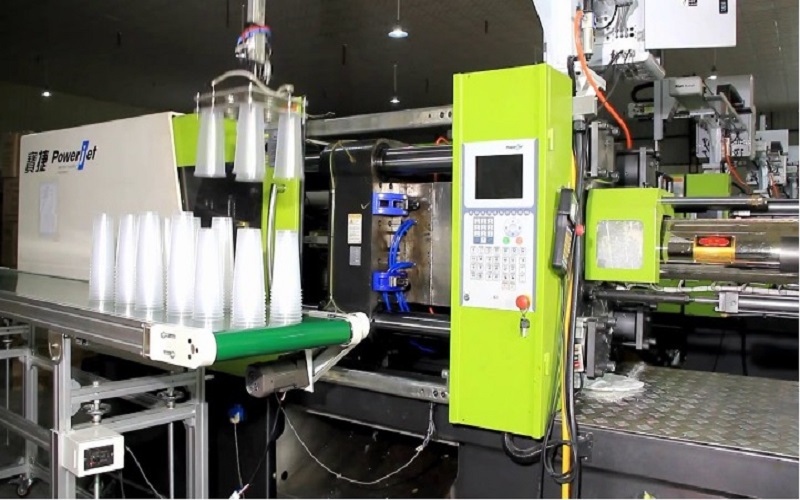
In contrast, thick-wall injection molding is mainly used to produce plastic products with larger wall thicknesses, which are widely applied in industrial components, automotive parts, large containers, and structural parts.
A “revolver” style thick-wall injection molding technique uses a vertical injection molding machine with a large turntable and multiple molds to transfer the cooling process outside the production line, reducing the production cycle and machine count.
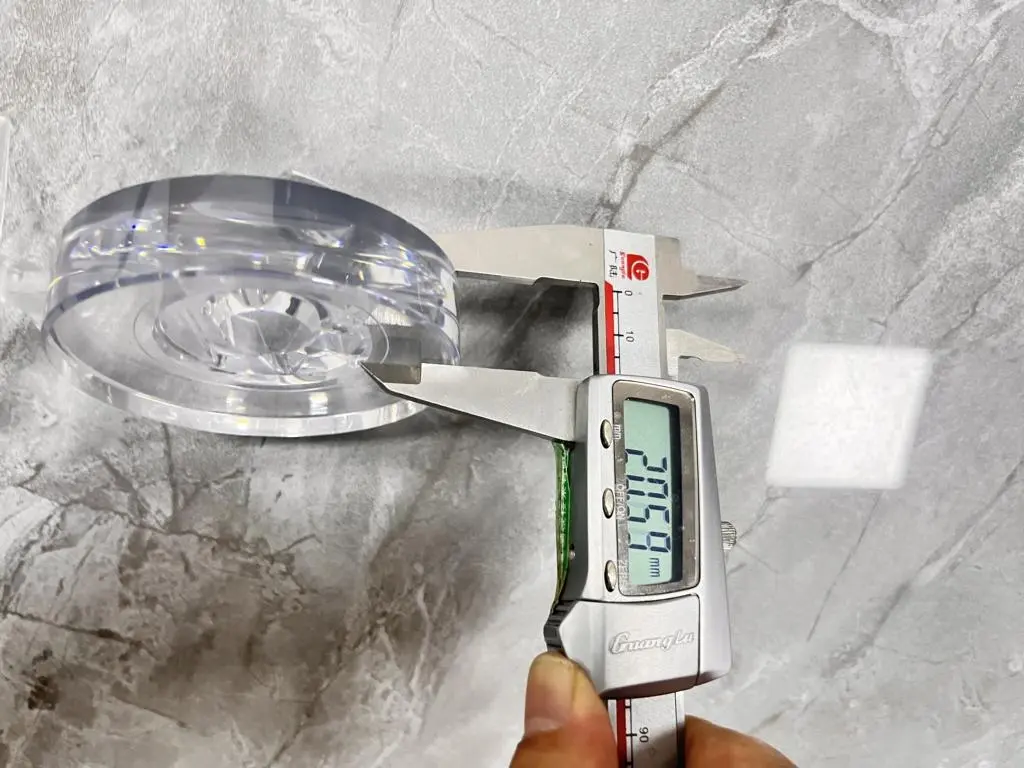
Whether it is thin wall or thick wall injection molding, wall thickness design is a critical factor.
Proper wall thickness design and mold manufacturing can significantly improve product quality and production efficiency, providing reliable solutions for various applications.
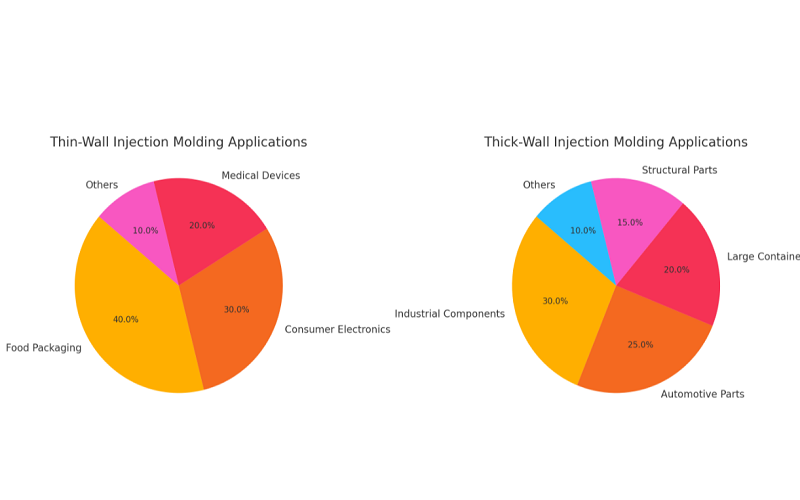
Conclusion
In summary, the optimal injection molding wall thickness should adhere to principles of uniformity, rationality, minimization, and design flexibility to optimize product quality, cost, and production efficiency.
If you need consultation for an injection molding project, FOWMOULD will provide you with a free quote and professional advice, creating injection molding solutions tailored to your needs!