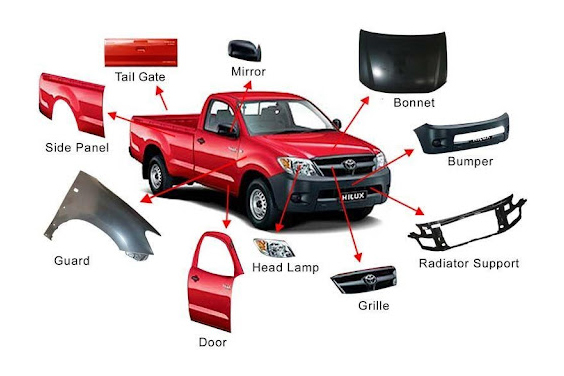
In the manufacturing industry, there are different processes employed to help ensure that all products being produced are of high quality. This is especially true when it comes to the manufacture of plastic products applicable in different sections, such as auto molds, bucket mould, and furniture molding. As a business, working towards getting your plastic products manufactured using the right processes is essential. Some of the main processes that you can expect to be working with include injection molding and compression molding. These two manufacturing processes will feature the use of different techniques and be used for various products. With this in mind learning more about these methods is a great idea given that it will give you the perfect opportunity to decide which process works for your needs.
For further guidance, working with a mold manufacturer is a great step. They will be in a better position to ensure that you invest in the right systems. Here is everything you should know when comparing injection molding vs compression molding.
Source: www.machinedesign.com
When it comes to the manufacture of different products, injection molding is the process you’ll hear most companies talking about. This is mainly because it features additional advantages that are quite appealing to a lot of businesses. This process features the use of injection molding machines and involves different aspects when it relates to the production process. Some of the aspects to consider include:
Source: teampti.com
The first step when it comes to injection molding is the product design. The customer is required to work with an established designer who will give a clear demonstration of the product’s outcome. This is essential to ensure that all the products that will be produced will meet your customer’s requirements and expectations. The designers will use software that will allow them to come up with a clear demonstration to facilitate further production processes. To make this process more efficient there may feature the need to produce a working prototype to ensure that the product design appeals to the customer.
After the product has been designed, the same designers will then work on the mold design to ensure that it works accurately. The mold design should feature the specific details featured in the product design. The mold is to be used as the basis when it comes to manufacturing any products. Designers need to ensure that the mold design is accurate and that it will translate to the exact design of the products.
Source: www.sachimolds.com
Source: www.boucherie.com
After the mold design, the process is then handed over to the engineers who are tasked with the mold-making process. Here, the engineers will be working with the mold design created earlier to ensure that they get the mold right. The engineers will determine the best material to use on the mold to ensure that it provides the perfect molded products. This process is important to ensure that the products feature the exact detail worked on in the product design stage.
After all the foundation work is done, the injection molding then begins to get the final product that you can easily work with. In this process, the first step is the clamping of the molds to ensure that they are secure. Once this is done, the molten plastic material to be used in this process is introduced into the mold using the injection tool. This tool comes in a cylinder-like shape and is designed to withstand the high temperatures that come with molten plastic products. After that, the molten material in the mold then solidifies by cooling to take the shape of the mold being used. Once it is cooled, the mold then opens and ejects the final products to be used in its designed application.
Source: www.creativemechanisms.com
Source: www.essentracomponents.com
Different companies will prefer the injection molding process because of the advantages it comes with. They include:
Ability to manufacture more products
When it comes to injection molding, if you are looking to have a bulk order, this is the best manufacturing option. It is designed to feature the use of multi-cavity molds that allow for simultaneous productions in one cycle.
Lower costs incurred
The ability for this process to achieve different products in one cycle translates to fewer costs incurred when in the manufacturing process.
Enhances versatility
With this method, the possibility of working on complicated products with creative shapes and sizes is made possible. This process is versatile and will allow you to feature the right designs for your specific product.
It is an efficient and reliable process
The injection molding is a reliable process provided the product design and mold making is done right, you’ll have what you envisioned.
Source: www.3erp.com
Like any other process, injection molding will feature a few disadvantages you should keep in mind. They include:
High tooling cost
When getting into the injection molding process, it may cost a pretty penny when it comes to creating the designs and the mold. However, once that is done, you can easily re-use the mold for other product needs.
A small number of productions is costly
Injection molding is best used in the production of bulk orders mainly because small orders tend to be more expensive due to the work involved.
Source: www.open.edu
Compression molding involves the use of both heat and high pressures to ensure that the end product meets the required specifications. It is a three-dimensional manufacturing process that features an upper compression part and a lower compression part. The compression molding process starts with the heating of the plastic polymers to be used in the process.
The molten plastic polymers are then introduced into the cavity of a mold. Once this is done, the top of the mold is then covered using a plug that helps add on pressure. When the pressure builds up, the molten material expands to fill the mold being used. After expanding, it is then allowed to cool taking the shape of the mold before being released.
It is however important to note that when working with the plastic polymer it needs to be heated to the right temperature. If the polymer is not heated enough, the compression process will fail while if it is overheated, the cooling process will take longer. This is however a great and effective process to consider when working on the manufacture of your plastic products.
Source: www.towajapan.co.jp
The compression molding process is a great manufacturing process that comes with its set of advantages. Some of them include:
Low initial investment and tooling costs.
Mold is easy to maintain.
Stress has a lower lingering effect.
Mechanical and electrical properties are preserved.
Like any other manufacturing process, compression molding also features some disadvantages you should be aware of. Some of them include:
Making a limited quantity of goods is not cost-effective
After compression molding, secondary machining (trimming, machining) of the product may be needed
May exhibit odd parting lines
Molding depth is reduced
Source: www.wuxipd.com
Source: www.open.edu
When it comes to compression vs injection molding, you find that there will feature a few similarities and also differences. The table below will help illustrate the two.
Similarities Between Injection and Compression Molding | Differences Between Injection and Compression Molding |
---|---|
They both feature the use of mold cavities | Injection molding works best with smaller products while compression molding can be used for larger products. |
They both rely on molten plastic polymers | The time taken to manufacture products using the injection molding process is lower compared to compression molding. |
The two processes feature the use of heat | Injection molding features greater production quantities compared to the compression molding process. |
Injection molding results in
stronger products with higher qualities compared to compression molding. |
Injection molding and compression molding are great manufacturing options for businesses to consider. They will result in accurate products with great turnaround time. Work with a mold manufacturer who will help you through this process and advise you on what is best for you. Take your time to ensure that the process you go with will actually deliver the results you are looking for.
Please contact us using the form below or emailing (harry@fowmould.com)