Injection molding tools are crucial for creating high-quality plastic parts. But what are the key tools you need to optimize production efficiency?
In this article, we break down the top five injection molding tools that can significantly improve your manufacturing process.
Key Takeaways
- Injection molding tools are essential for shaping molten plastics, with proper design directly impacting production quality and efficiency.
Different mold types—single-cavity, multi-cavity, and family molds—cater to varying production needs, from low-volume prototyping to high-volume manufacturing.
Material selection for molds is critical; tool steel, aluminum, and copper alloys offer different benefits, affecting mold durability and production effectiveness.
What Are Injection Molding Tools
Injection molding tools, or injection molds, are the backbone of the plastic injection molding industry.
These tools are meticulously designed and engineered to shape molten plastic materials into the desired parts, ensuring precision and consistency throughout the injection molding process.
Injection mold tooling directly influences the quality, accuracy, and efficiency of the production process.
Proper mold design is paramount in the injection molding process.
The tools must be designed to withstand high temperatures and pressures, maintain dimensional stability, and ensure the final product meets the required specifications. Scientific qualification of tools and optimized production steps lead to cost-effective, high-quality outcomes for manufacturers.
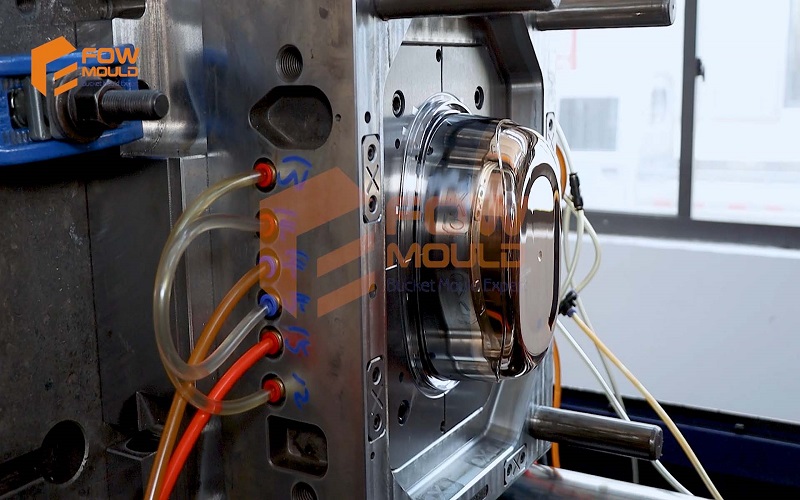
Types of Injection Molding Tools
Understanding the different types of injection molding tools is essential. This knowledge helps in selecting the most suitable option for a project. Each type of mold is tailored to specific production requirements, whether it’s low-volume prototyping or high-volume manufacturing.
The main types include single-cavity molds, multi-cavity molds, and family molds, each serving unique purposes in the injection molding process.
Single-Cavity Molds
Single-cavity molds feature one cavity and produce a single component per cycle. These molds are ideal for low-volume production and prototyping due to their simplicity and cost-effectiveness.
Single-cavity molds are particularly useful for testing new designs and making adjustments before scaling up to higher volumes.
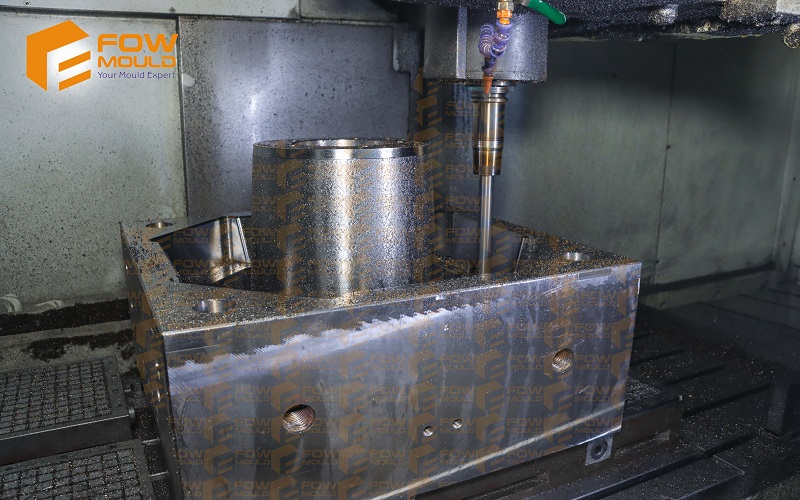
Multi-Cavity Molds
Multi-cavity molds can produce several identical parts in a single cycle. This design greatly boosts production efficiency. These molds are commonly used in high-volume production settings, such as the automotive and electronics industries, where the demand for identical parts is high.
The durability and performance of multi-cavity molds make them essential for mass production.
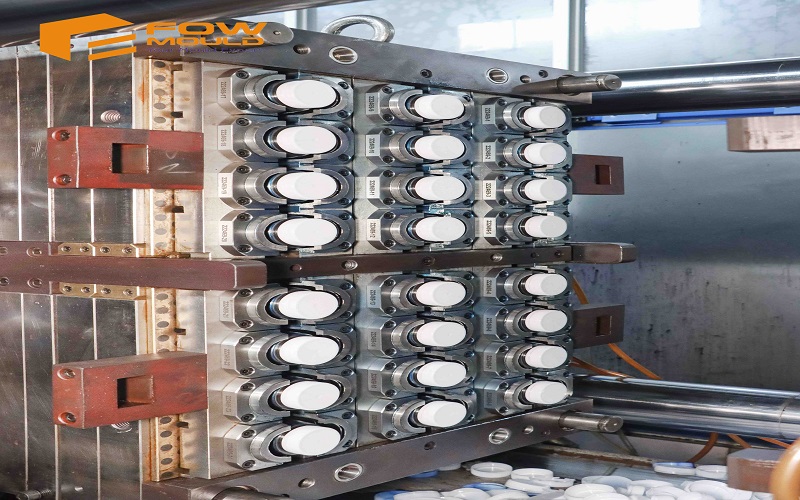
Family Molds
Family molds are unique in that they can produce different parts or variations simultaneously within a single mold. This capability allows manufacturers to consolidate production, reducing costs and improving efficiency.
However, designing family molds can be complex due to the need to accommodate varying geometries and functionalities of different parts.
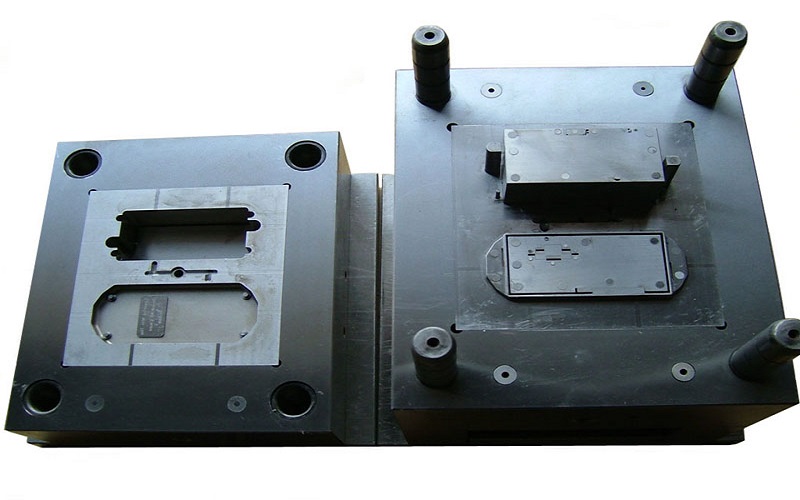
Materials for Injection Molding Tools
Selecting appropriate materials for injection molding tools affects durability, performance, and the quality of molded parts. Different materials, such as tool steel, aluminum, and copper alloys, offer various benefits and are chosen based on specific production requirements.
Choosing the right materials ensures molds withstand high temperatures, pressures, and mechanical stresses while maintaining dimensional stability and surface finish.
Tool Steel
Tool steel is a popular choice for injection molding tools due to its exceptional hardness, toughness, and wear resistance. Hard tooling made from tool steel can endure millions of cycles, making it a cost-effective option for mass production.
Although the initial investment is higher, the long-term benefits of reduced per-part costs make tool steel an economical choice for high-volume manufacturing.
Aluminum
Aluminum is favored for its lightweight, cost-effectiveness, and excellent thermal conductivity, making it suitable for prototyping and low-volume production. Aluminum molds offer quicker production times and lower costs compared to other materials.
However, their wear resistance is limited, making them less suitable for high-volume or abrasive applications.
Copper Alloys
Copper alloys are valued for their excellent thermal conductivity and corrosion resistance, which enhance the efficiency and longevity of injection molds. These properties make copper alloys ideal for specialized applications requiring precision and durability.
Their ability to facilitate rapid heat transfer ensures efficient cooling and improved cycle times during production.
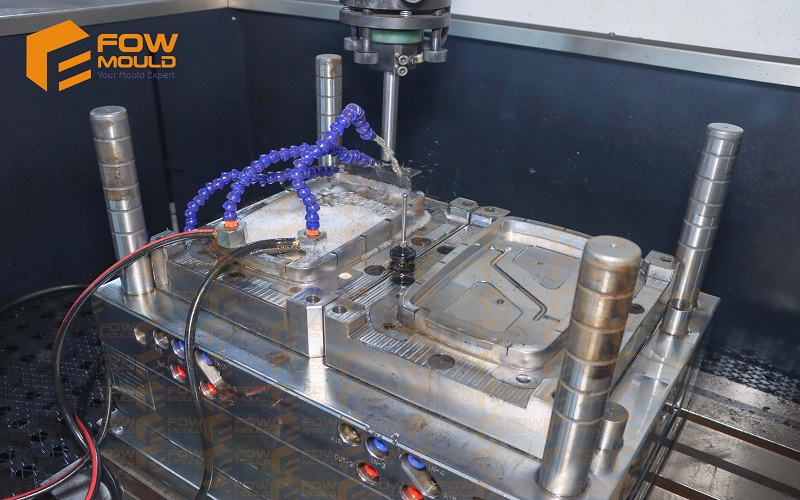
Key Components of Injection Molding Tools
Injection molding tools consist of several key components that work together to shape the final product. These include the injection mold cavity, ejector system, and cooling system, each playing a crucial role in the molding process.
Knowing these components and their functions is key to high-quality, efficient production.
Mold Cavity
The mold cavity is the part of the mold that shapes the molten plastic into the final part. Its design heavily influences the quality and precision of the molded part.
The runner system guides the molten plastic to the mold cavities, ensuring proper filling and shaping of the part.
Ejector System
The ejector system is responsible for removing the solidified part from the mold. It ensures that the part is ejected precisely and without damage, maintaining the integrity of the molded part.
Efficient production and high-quality parts depend on the ejector system’s proper functioning.
Cooling System
The cooling system regulates the temperature of the mold and the solidifying plastic, ensuring efficient production cycles and high-quality parts. Maintaining proper mold temperature and preventing defects hinge on effective cooling.
The efficiency of the cooling system directly impacts cycle time and overall production efficiency.
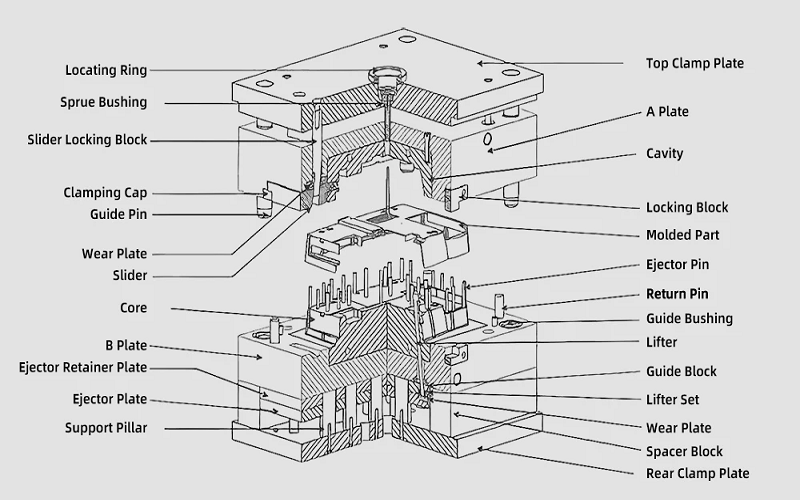
Design Considerations for Injection Molding Tools
Several key considerations in designing injection molding tools ensure optimal production efficiency and part quality. Factors such as part geometry, material selection, and production volume play a crucial role in the tool design process.
These considerations help manufacturers create efficient, high-quality molds.
Part Geometry and Complexity
The geometry and complexity of the part significantly influence the mold design. Complex shapes require intricate molds with advanced features to ensure proper functionality and ease of manufacturing.
Advanced mold designs lead to higher quality parts and improved production efficiency.
Material Selection
Selecting the right materials for both the molds and the parts is crucial for achieving the desired quality and functionality. Material properties affect aspects such as tool durability and overall production quality.
Compatibility between mold material and plastic material resin is crucial for successful production.
Production Volume
Production volume is a critical factor in choosing the appropriate injection molding tools. Low-volume production often utilizes simpler molds, while high-volume production demands more robust and efficient designs.
Operational success hinges on balancing cost-effective tooling for low-volume runs with durable molds for high-volume production.
Injection Molding Tooling Process
The injection molding tooling process involves several molding processes to ensure the quality, reliability, and efficiency of the molds. Each step is vital for efficiently producing high-quality plastic parts, including:
Initial design
Material selection
Prototyping
Tool fabrication
Mold testing
Design Phase
The design phase translates product specifications into detailed mold designs using CAD and CAM software. This phase involves creating 3D digital representations of the mold, allowing for better planning and visualization before fabrication.
Part geometry complexity requires more complex geometries with moving components or special features.
Material Selection for the Mold
Choosing the appropriate materials for the mold is based on production needs and factors like durability, thermal conductivity, and cost. Hardened steel is often selected for high-volume production, while aluminum is suitable for prototypes or low-volume runs.
Balancing performance and budget is the goal.
Prototyping and Testing
Prototyping and testing are crucial in the injection molding tooling process. Techniques such as 3D printing and CNC machining enable rapid prototyping, allowing designers to test and refine mold designs effectively. Early prototyping reduces the risk of costly errors and ensures the final mold meets production requirements.
Tool Fabrication
Tool fabrication involves methods like CNC machining and electrical discharge machining (EDM) to create precise mold components. Aluminum tooling allows for quicker machining compared to steel, resulting in reduced lead times.
Precision in tool fabrication is key to high-quality parts and efficient production, especially when working with tight tolerances.
Mold Testing and Validation
Mold testing and validation ensure the mold produces parts that meet specifications. The process involves installing the mold in an injection molding machine, running initial trials with the selected plastic resin, and inspecting the parts for defects.
Adjustments to mold parameters or refinements may be needed to achieve consistent production with a validated mold.
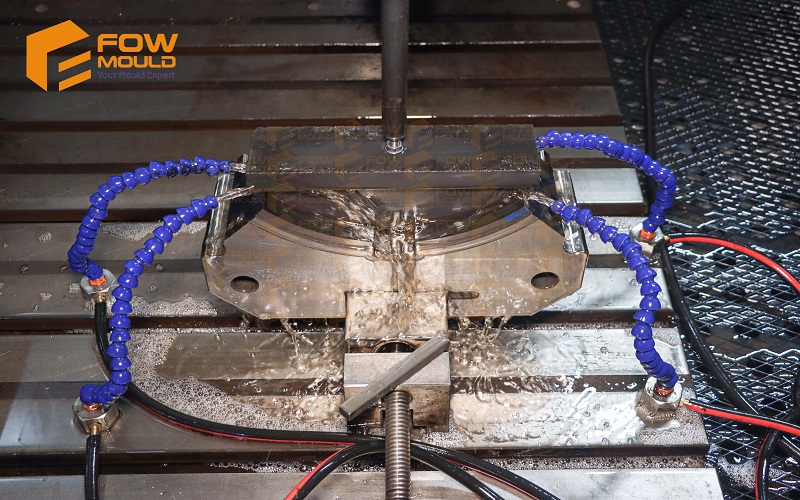
Advantages and Disadvantages of Soft vs. Hard Tooling
Choosing between soft and hard tooling depends on production needs, volume, budget, and tooling design. Soft tooling is generally used for prototyping and low-volume production, while hard tooling is suited for high-volume, long-term production.
Knowing the advantages and disadvantages of each helps manufacturers make informed decisions.
Soft Tooling
Soft tooling, with its rapid production and lower costs, is ideal for prototyping and testing new products. Benefits include cost-effectiveness, quick production times, and the ability to conduct testing before mass production using soft tooling molds.
However, the shorter lifespan of components and limitations with abrasive materials are significant drawbacks.
Hard Tooling
Hard tooling, primarily made from steel, offers greater durability and is suitable for larger batch productions. The longer lifespan, ability to be refurbished, and support for tighter tolerances make hard tooling a valuable investment for high-volume production.
However, higher upfront costs and longer lead times are significant drawbacks.
Innovations in Injection Molding Tooling
Innovations in injection molding tooling have transformed the manufacturing industry.
Advances in micro injection molding, 3D printing integration, and nanocomposites have significantly boosted production efficiency and quality.
These innovations enable the creation of complex parts with greater precision and reduced production times.
Common Issues and Troubleshooting in Injection Molding Tooling
Startup problems and quality control concerns are common issues in injection molding tooling. Startup issues typically arise during the initiation of new tooling or machinery, while quality control problems occur when previously produced items fail to meet specifications.
Troubleshooting involves addressing process conditions, material supply, and maintenance status to resolve defects and ensure consistent production.
Summary
In summary, understanding the different types of injection molding tools, selecting the right materials, and considering key design factors are essential for optimizing production efficiency. The tooling process, from design to validation, ensures high-quality outcomes.
Embracing innovations and addressing common issues will pave the way for continued success in injection molding.
The future is bright for injection molding tooling, with advancements promising even greater efficiency and precision.
Keep exploring, innovating, and pushing the boundaries of what’s possible in manufacturing.
Frequently Asked Questions
What are injection molding tools?
Injection molding tools are essential devices that shape molten plastic into precise and consistent parts during the injection molding process. Their design and functionality are crucial for achieving high-quality production results.
What are the main types of injection molds?
The main types of injection molds are single-cavity molds, multi-cavity molds, and family molds, each tailored to specific production needs. Understanding these types will help you select the most suitable mold for your project.
What materials are commonly used for injection molding tools?
Injection molding tools are typically made from tool steel, aluminum, and copper alloys, each selected based on specific production requirements to optimize performance and durability.
What are the advantages of soft tooling?
Soft tooling provides rapid production and cost-effectiveness, making it particularly advantageous for prototyping and low-volume production. Despite its shorter lifespan than hard tooling, its benefits are significant for specific applications.
How has innovation impacted injection molding tooling?
Innovation has greatly improved injection molding tooling by enhancing efficiency and quality through advancements like micro injection molding, 3D printing integration, and the use of nanocomposites. These developments allow for more precise and cost-effective manufacturing processes.