In plastic molding, shrinkage is a common phenomenon that occurs during the cooling and solidification of the product. It is caused by volume contraction, which pulls surface material inward in thin-walled areas, resulting in surface depressions.
Injection Molding Shrinkage not only leads to dimensional deviations but may also affect surface quality and introduce internal stress, thereby compromising the strength and appearance of the product.
This article will delve into the causes of injection molding shrinkage, its impact on molded parts, and propose corresponding solutions to optimize the molding process and enhance product quality.
What Is Injection Molding Shrinkage?
Injection molding shrinkage, also known as sink marks or shrinkage dents, refers to surface depressions on plastic molded parts, typically appearing as dimples or grooves.
It is one of the common injection molding defects .
This defect primarily occurs due to uneven shrinkage of the plastic during the molding process or insufficient material compensation during the packing and holding phase.
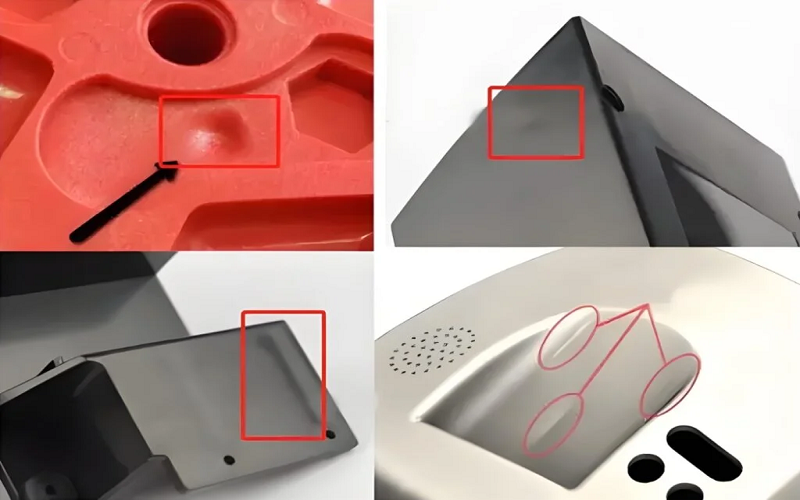
Why Injection Molding Shrinkage Occurs?
The occurrence of injection molding shrinkage is primarily due to the inherent property of plastics to shrink in volume during cooling and solidification.
This phenomenon is closely related to the following key factors:
1.Plastic Materials
- Thermal Expansion and Contraction: Plastics naturally shrink in volume as they cool and transition from a molten to a solid state. Crystalline plastics (e.g., PP, PE) have higher shrinkage rates compared to amorphous plastics (e.g., ABS, PMMA) because the crystallization process significantly reduces material volume.
- Effect of Additives: The use of additives or color masterbatches in plastics affects material density and flow characteristics, thereby influencing the degree of shrinkage.
2.Injection Molding Parameters
- Injection Temperature: Inadequate temperature control of the injection molding machine can lead to excessively high or low product temperatures, affecting the thermal expansion and contraction of the material and resulting in shrinkage.
- Injection Rate: A fast injection rate can cause excessive shear force on the material as it enters the mold, leading to excessive thermal deformation, while a slow rate can result in rapid cooling of the plastic, compromising dimensional stability.
- Injection Pressure: Excessive injection pressure can destabilize plastic flow, causing shrinkage and warping. Conversely, insufficient pressure may lead to air bubbles and blemishes in the product, negatively impacting its appearance and mechanical properties.
3.Part and Mold Design
- Uneven Wall Thickness: Non-uniform wall thickness can generate internal stresses during cooling, leading to shrinkage.
- Mold Surface Adhesion: A rough or burr-filled mold surface can cause issues such as squeezing or tearing of the plastic as it enters the mold, impacting dimensional stability.
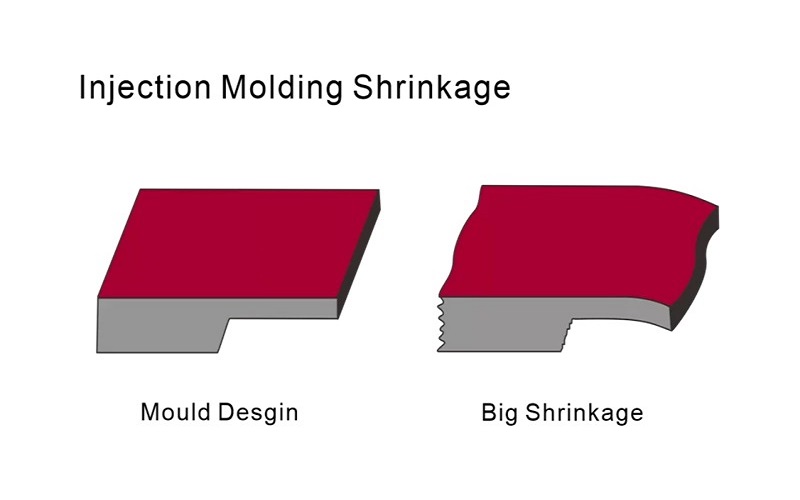
The Impact Of Injection Molding Shrinkage
Appearance
Shrinkage defects manifest as pit-like depressions on the surface of molded parts, typically in areas with greater material thickness.
During the cooling process, volumetric shrinkage generates inward pulling forces toward the center.
When the outer layer is insufficiently solidified, this pulling force can cause surface indentations.
Dimensional Accuracy
Shrinkage reduces the final dimensions of the molded product compared to the design specifications, potentially compromising assembly precision and functional performance.
Internal Structure
During cooling, the outer layer of the molded part solidifies first as it adheres to the mold wall, while the core continues to shrink.
This uneven cooling creates internal stresses, which, if excessive, can deform the outer layer, exacerbating shrinkage.
Mechanical Properties
Shrinkage can weaken the mechanical strength of the product. The resulting porous internal structure reduces the material’s ability to withstand external forces, thereby lowering its durability.
Injection molding shrinkage not only affects the appearance and structural integrity of the product but also impairs its functionality and user experience.
As a result, addressing shrinkage is a critical focus in ensuring the quality and performance of injection molded parts.
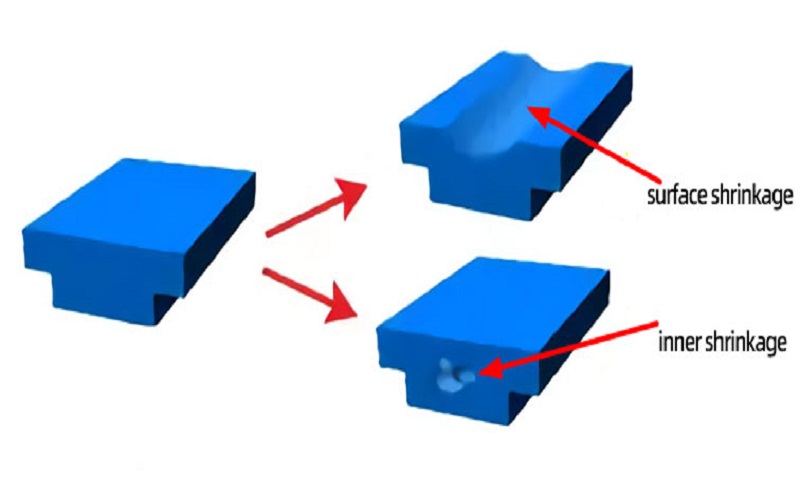
How To Calculate Shrinkage Rate In Injection Molding?
Shrinkage rate is calculated by comparing the difference between the actual dimensions of the injection molded product and the mold dimensions.
The formula is:
Shrinkage rate = (Mold dimensions – Injection product dimensions) ÷ Mold dimensions × 100%
For injection molded products with varying wall thicknesses, the shrinkage rate should be calculated separately for different wall thickness areas, and then a weighted average should be computed.
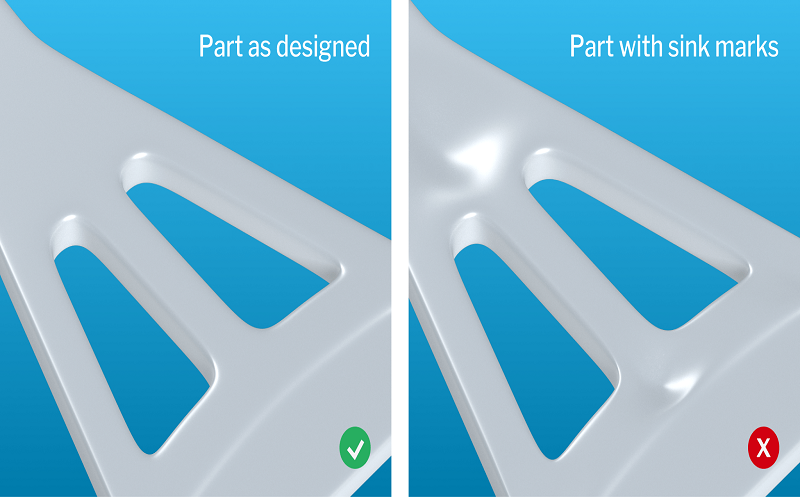
Effective Ways to Solve Injection Molding Shrinkage
To effectively solve the shrinkage problem in the injection molding process, the following approaches can be taken:
1.Improve Structural Design
Adjust the thickness of the molding material to ensure uniform cooling and avoid localized sink marks.
2.Select Appropriate Materials
Choose plastics with an appropriate shrinkage rate and optimize the material formulation.
3.Optimize Injection Molding Process
Lower barrel temperature, increase cooling time, raise injection pressure, extend injection and holding times, etc., to reduce shrinkage.
4.Enhance Mold Design
Ensure uniform wall thickness and smooth gating systems, and increase the cooling water channels to ensure high-precision manufacturing.
5.Control Environmental Factors
Maintain constant temperature and humidity to reduce the impact of the environment on the shrinkage of plastic parts.
6.Other Technical Measures
- Increase gate and runner size: This ensures pressure is effectively applied to the thicker areas of the molded part, reducing shrinkage.
- Use anti-shrinkage agents: Adding anti-shrinkage agents to the plastic can reduce shrinkage and prevent dimensional issues.
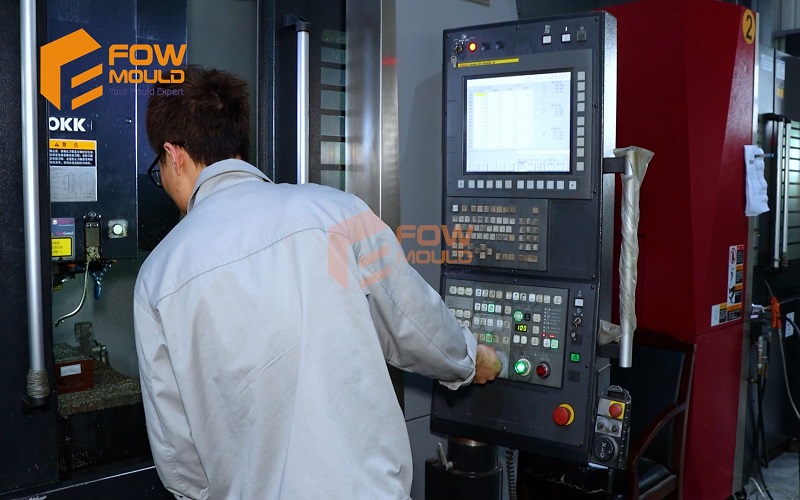
Conclusion
Although defects arising during the injection molding process cannot be completely predicted or eliminated, a thorough understanding of the causes of injection molding shrinkage and its solutions can significantly minimize its impact on the final product.
If you would like to learn more about injection molding, you can visit our official website. FOWMOULD will provide regular updates on injection molding news.