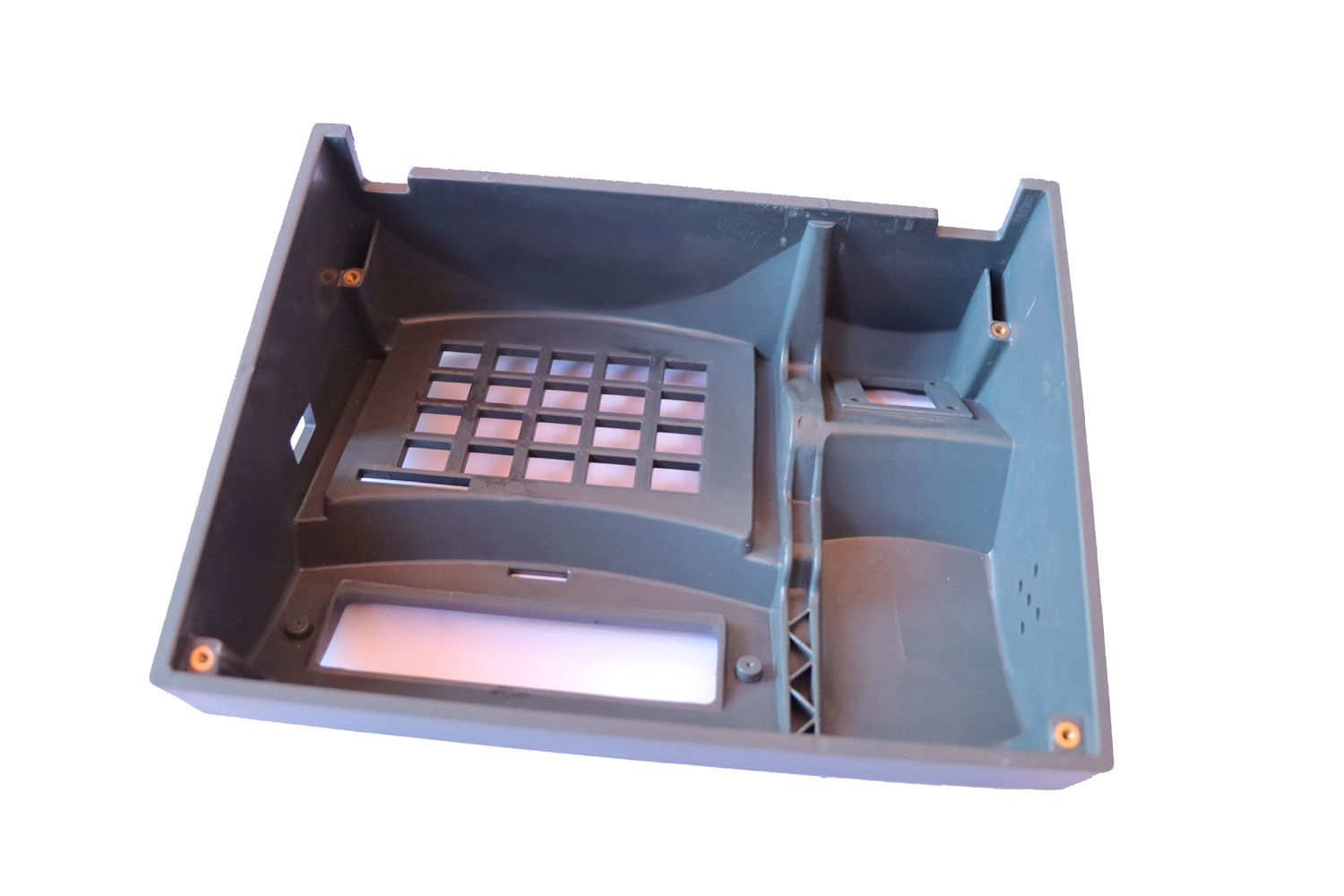
Share :
Share :
Nylon (PA) or Nylon Polyamide is a synthetic thermoplastic used for its chemical compatibility, high melting point, and chemical strength. The plastic can be melted into fibers that are applicable for use in textiles, into filaments used in advanced prototype molding, into sheet stock which finds use in cnc machine for mold making, and into films that are used in packaging of various types. Nylon typically occurs in an off-white color and is mostly found in black and white variants. But the plastic can be dyed into any color, which is why many toys are made of nylon. Injection molding with nylon plastic is a process that often includes the infusion of glass fibers to increase the tensile strength and durability of the molds.
In scientific terms, nylon is a thermoplastic linear polyamide. Nylon was created in 1935 by Wallace Carothers, an American chemist. The first type of nylon ever produced was Nylon 66, which still remains one of the commonly used variants of nylon plastic. The invention of nylon came in handy during the second world war when naturally occurring materials were in limited supply, and man-made products were needed.
Nylon has many applications that range from its use in clothing to its inclusion in car tires. Nylon ropes, injection insert molding, and mechanical equipment are in high demand. Nylon is very resistant to naturally occurring deterrents which makes it a popularly used plastic. Nylon is a strong material, resistant to moisture and chemicals, is easy to clean, and is also very elastic. A clever substitute for materials that are not as strong as nylon, this material is also used in the engines of automobiles as it stays durable when exposed to high temperatures and is chemically strong.
Nylon plastic is used in mold design for injections and in many other ways because of its numerous advantages. Nylon’s advantages are as follows:
Even though nylon is extensively used in molding and manufacturing, there are some properties of the material that can be counted as its disadvantages. Some of these disadvantages are mentioned below:
Some other issues that can come up during injection molding with nylon plastic should also be taken into account. These are:
Nylon finds use in many industries and in various forms. A versatile material, nylon is used in the textile industry and has industrial and mechanical uses as well. Because of its low coefficient of friction, nylon finds use in gears, bearings, and bushings. The high melting temperature also makes it manufacturers’ favorite for a variety of purposes that include cookware and parts of the engine. Other frequent uses of nylon are in food packaging, toothbrush manufacturing, plastic fasteners, and fiber ropes.
If we go into more detail, nylon has certain specialized uses across industries. These comprise the following:
Some of the notable properties of nylon eventually relate to its strength. From its high melting temperature to its high tensile strength, all of these properties ensure that the plastic is durable and suitable for purposes such as injection molding. With its resistance to abrasion and chemicals, nylon also finds use in many industries. In high-temperature environments like the engine of an automobile, nylon is used instead of any other plastic. The low coefficient of friction does not cause heating up in the material and enables nylon to be used in gears and bearings.
Because of its resistance to fire, nylon melts rather than burning which allows for manufacturers to recycle and remold the thermoplastic for continued use. Nylon also bonds well with other materials to improve its properties. To increase the already commendable tensile strength of the material, nylon is filled with glass fibers. This helps with strengthening the material and also makes the material less flexible and brittle. For injection molding and overmolding as well, some manufacturers infuse glass fibers into nylon plastic.
The hardness level of nylon (Rockwell) is R115, whereas the flexural modulus of the material amounts to about 16,000 psi. The impact strength of the material is 0.6 fit-lb/in notched Izod. The tensile strength of nylon is measured to be approximately 11,000 psi.
Name | Nylon (PA), or Nylon Polyamide |
Chemical Formula | (C12H22N2O2)n |
Melting Point (°C) | ~220°C |
Melt Temperature | 220 °C (248 °F) |
Typical Injection Molding Temperature | 59 – 93 °C (130 – 200 °F) |
Heat Deflection Temperature (HDT) | At 0.46 MPa (66 PSI), HDT is 160 °C (320 °F) |
Nylon plastic is used while molding to harness the advantages of its strength, heat resistance, and durability. Since nylon is more affordable than rubber, silk, latex, or other naturally occurring materials, it finds varied use across manufacturing industries. Some of the most prominent uses of nylon include injection molding. During mold making, more often than not, manufacturers insert glass fibers into nylon to increase strength and reduce the elasticity nylon typically has.
The nylon injection mold or any other product that has a glass fiber filling is named 30% GF Nylon. Here, GF stands for glass fiberfill, and the percentage informs of the infusion of glass fibers.
Please contact us using the form below or emailing (harry@fowmould.com)