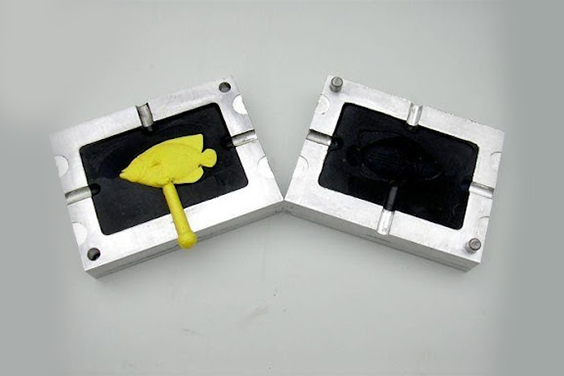
Share :
Share :
The injection molding process is one of the most intensive manufacturing processes that anyone could come across today. Over the years, it has developed into a reliable form of mass production, and it has many different parts that come together to ensure that everything works according to plan.
Among the many parts that make it possible is the lifter. We are going to explore what an injection molding lifter design is, how it affects the entire process, the benefits it brings, and the limitations associated with it. If you are thinking of getting into mold making technology and would like to know what a lifter is, then you are in the right place.
An injection molding lifter is an important component that is part of the injection molding mechanism that travels with the ejection stroke, moving on an angle to slide and pull the cavity steel away from the undercuts in the die.
The average lifter is mainly used to create the internal undercuts of a molded part of a plastic while at the same time offering a mode of ejection once the formation of the end product such as plastic molded chairs or auto plastic parts is complete. This mechanism is made of a very simple structure with some form of rigidity that allows it to travel a very short distance.
The injection molding lifter is made up of two main parts that consist of the body and the forming parts. Based on this, injection molding lifters can be classified either as integral or non-integral. These two distinctions are determined by the body and the forming parts that are part of the construction. An integral lifter is much more compact, with the strength to resist damage. This is why it is used in injection molding that deals with larger parts.
Another advantage of an integral lifter is that the design makes it easy for a combined form to be used, and this is good for replacements to be added as well as the maintenance and repairs to be conducted without affecting the other parts of the injection molding machine.
A lifter is placed at an angle in the hole inside a locating block. Once the lifter is given a push from the bottom, it moves for a certain short distance in the direction the lifter inclines. As the ejection process begins, the product is usually moving in a vertical motion since that’s the direction that has the space on top that allows for the end product to be removed. At the same time, the lifter is able to move in the opposite direction to the mold, away from the undercut, to make the release more easily.
Without a lifter, there’s very little that the injection molding machine can do as far as the ejection process is concerned. For manufacturers who provide plastic injection molding service, lifter is one of the most crucial factors. Depending on the material used, the lifter should be able to handle any kind of work.
For an injection molding lifter to work as designed, there are some certain standards and requirements that have to be met. They include the following.
When it comes to injection molding lifter design, there are some certain material considerations that have to be adhered to in order for the component to work as intended. The one thing that you have to keep in mind is that the movement of the lifter is very important to the entire operation.
The lifter has specific movements that include going in and out of the locking block, and this exerts a lot of pressure on the item being molded. To ensure that nothing is destroyed in the process, the lifter has to be constructed using an abrasion-resistant material that will be able to withstand the huge pressure throughout the entire process.
One of the most common materials that are used to make them includes hardened steel 4507 that has a hardness value of about HRC 50-52, which in layman terms means that it is very hard. The base of the lifter can be made using steel 738, while the other block is usually made using bronze. All these different parts are used for specific reasons, and they all combine to work seamlessly with each other to ensure the ejection process takes palace with as minimal damage as possible.
As efficient as it is, using a lifter of this kind means that there’s an added cost to using the complex design. On the upside, efficiency is boosted many times over, and this is ultimately good for the production in the long run.
There are some injection molding systems that don’t use lifters in any way or form. Depending on the preferences of the mold engineers, there are several alternatives that injection molding manufacturers can turn to and still attain the same results in the end. So far, the most common ones are two sliders and inserts.
Sliders work almost the same as lifters, but they employ a different mechanism. Inserts, on the other hand, make use of a much simpler mold ejection mechanism that force ejects the product alongside the inserts.
Injection molding continues to improve over the years, and more parts are being added, and the existing ones get refined to make the process better and more reliable. Injection molding lifters are just the tip of the iceberg, and they are here to stay and extend well into the future. For more information on injection molding, mould design and lifters, check out our website and have any questions that you may have answered by our team of experts.
Please contact us using the form below or emailing (harry@fowmould.com)