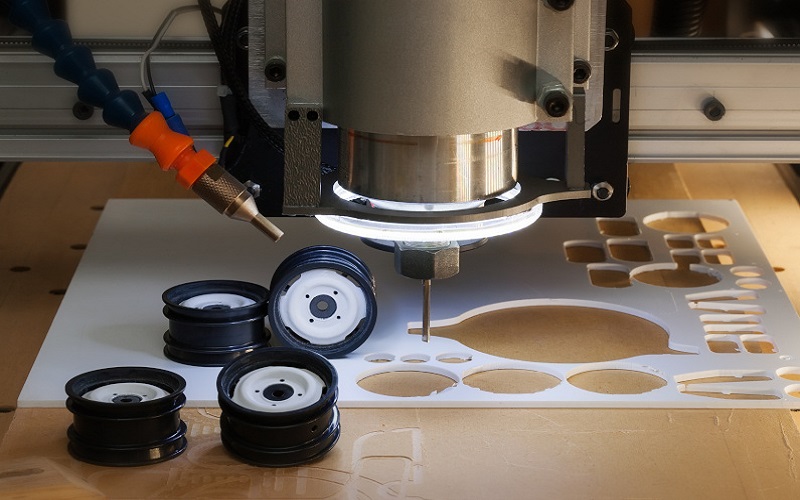
Share :
Share :
There are several costs associated with the injection molding process. You may be reading this article out of curiosity, or as part of your research, either way, you all have the same question in mind. How much does injection molding cost? To start with, the injection molding process is responsible for the production of items such as auto molds. This means that it does demand attention to detail – a skill you should have while reading through this article.
The aim is to give you a better understanding of the costs incurred while conducting the injection molding process. We do hope that by the end you will be in a better place. Do enjoy!
Source: Pinterest
Plastic mold making technology is the procedure for making plastic items that involve injecting melted material into a mold. There are various steps to the procedure. First, the part is meticulously designed, with accurate dimensions and other structural requirements. The part is then prototyped to create a more tangible sample.
The purpose is to inspect and test the construction for stability, functionality, and beauty. The prototype would be reconfigured and printed for a second review if there were any problems or changes that needed to be made to the design. This is repeated until the design is complete. Mold-making can then proceed after the part design is finalized and approved.
There are similarities to the custom plastic molding costs associated with mold making in China, Totaling parts of the world. To make this easier, we can classify the issue into two parts;
Source: Unsplash
China injection molding costs will run between $1000 for small-scale production and $12000 for larger-scale production, depending on the quality/quantity of work. However, as the reputation goes, outsourcing large-scale processing would lower the custom injection molding cost in China as compared to any other way.
A cost breakdown can look something similar to the following;
Source: Unsplash
This is similar to the above in that the cost breakdown in percentage would contain the same considerations. A proper percentage breakdown would have machining taking up the larger share, all the way down to designing costs. This could look like this:
However, in other parts of the world, outsourcing these services might cost you more than it would in China.
Source: Pinterest
Many factors can influence the cost of creating a mold and conducting a molding operation. These may include:
Materials: The type of plastic molding material you choose will have an impact on both tooling and piece pricing, which varies depending on the material.
Mould Design: Designers and product engineers will overlook part color because they presume that piece cost for all hues is the same. If your part is white or transparent, however, the molding cost will be more than for other colors. Molding factories incur additional costs as a result of cleaner molding conditions.
Molding costs are heavily influenced by complexity. It necessitates more work and processes in the mold making process. The main reasons include tolerance requirements, exquisite detailing, or the number of undercuts. The best way to reduce your molding costs is to redesign your part as a simplified version.
Mold life has a significant impact on tooling costs. Regular steels are used in prototype molds. However, hardened steel would be necessary for high-volume production molds.
Mirror polishing raises the cost of injection molding since it necessitates the use of hardened steels in the molds and a healthier injection molding environment. Another factor for cost increases is a higher texturing need.
On produced parts, everyone wants to save money. Increased part quantity is one of the simplest ways to lower price-per-piece cost in injection molding. This is because the upfront cost of designing and machining the mold is amortized over a larger number of pieces.
While injection molding may appear to be more expensive than methods such as CNC machining and 3D printing, its ability to scale and produce thousands of pieces makes it a cost-effective large-scale production alternative.
Some of the methods used in reducing these costs may include;
Source: Pinterest
Undercut characteristics make part ejection more difficult and, in some situations, impossible. If you can, get rid of them. These save tooling costs by obviating the need for additional mold components, which raise production prices.
Source: Pinterest
Textured surfaces, molded component numbers, and business logos are all attractive but expect to pay a premium for these and other non-essential features. Permanent component numbers, on the other hand, are required in many aerospace and military applications. Choose a mill-friendly font and maintain the font size above 20 pt., and go no deeper than 0.010 to 0.015 inches. Also, if the component ejection is a worry, be ready to increase the draft.
Source: Pinterest
If you require housing for electronic products or a comparable box-shaped component, you may either sink the cavity deep into the molding floor or process the aluminum material all around the core and mold the part surrounding it using long and thin tools to make the ribs. The latter process, described as core cavity molding, is significantly more cost-effective for molding high walls and textured surfaces.
Source: Pinterest
Maybe for certain medical components or two mobile radio interlocking halves, you’ll build a snap case. Why construct two components if one can be made? Refine the snaps to fit halves on either side so that a so-called ‘universal’ part is built. Only one mold is necessary, which saves production costs in advance. Now, instead of half the amount of two, you may shape twice as many of one part.
Source: Unsplash
A design for manufacturing feasibility (DFM) analysis should accompany each quote for an injection-molded component. This indicates possible issues or design improvement possibilities. Lack of draft angles, ‘unusable’ features, unworkable geometric features—these are only a few instances of the parts to fix before you accept services.
Source: Unsplash
Take portion extent into consideration always. In the molding language, this implies how large the component is and it is comfortable in the mold and allows the mold to work sprues, runners, ejector pins, and all the others.
Source: Pinterest
Then explore an option to overmold. This may cost you earlier, depending on the part, but may save you money afterward. For example, there might be an extra expense to over form a gasket on a part upfront, but then you will be able to save money by manually installing a gasket.
Source: Unsplash
Aesthetic parts require beads blasting, EDM, or high-mold polishing frequently to get a high aesthetic look. This increases the cost of tools. Anything larger than PM-F0 (as machined) needs to do some handwork, with the use of a grade 2 diamond buff, up to an SPI-A2 mirror termination. Avoid such precise finishing unless they are needed for the work.
Custom plastic molding costs can vary in different parts of the world. China molding injection molding costs, for example, are relatively cheaper compared to those in other parts of the world, due to the manufacturing conditions specific to the country. However, it is important that your focus on the core plastic injection molding production before adding optional parts, to reduce the cost overrun associated. We do recommend that you pay attention to detail in the above-mentioned factors before starting. If you need any help, please contact us to get professional plastic injection molding service.
Please contact us using the form below or emailing (harry@fowmould.com)